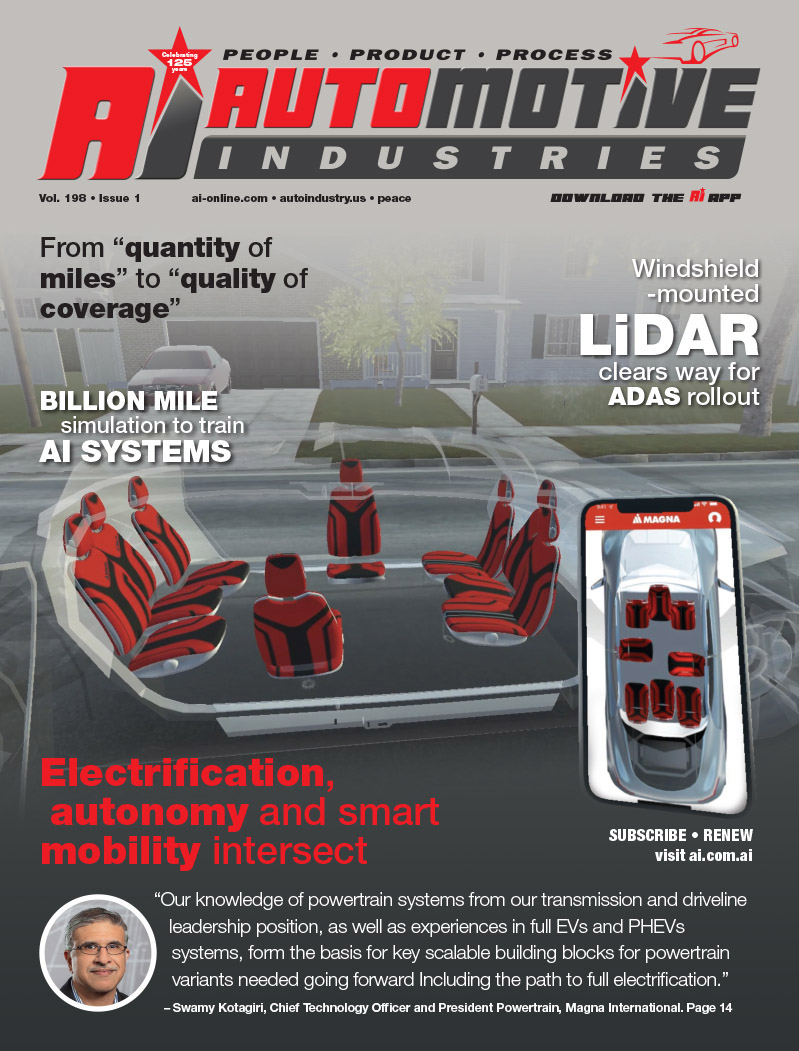
Propulsion technology development is being affected by a combination of converging and diverging trends. There is convergence through the hybridization of electric and internal combustion engine powertrains, and continued divergence as engineers continue refining a variety of different types of combustion engine pretty much in isolation from electric motor development.
ueling the unprecedented diversification of power trains is a rich mix of increasingly stringent global emission regulations, the development of autonomous driving, car sharing and connected cars.
Automotive Industries (AI) asked Volker Heinz, Director Engineering, BorgWarner Drivetrain Engineering, what solutions the company is offering OEMs to sustainably reduce their carbon footprints. Heinz: We already have a very broad portfolio, including all the key technologies necessary for clean and energy-efficient electrified mobility. To give you one example: the integrated drive module (iDM) combines specially developed power electronics with an advanced transmission system and industry-leading electric motor technology in a compact package. In addition, the company already offers P2 modules, which facilitate cost-efficient hybridization by enabling pure electric driving as well as hybrid functionalities such as stop/start, regenerative braking and supplementary electric propulsion.
AI: Will electric vehicles ever completely replace vehicles propelled by internal combustion engines? Heinz: The IHS Light Vehicle Forecast predicts a 41 % increase in the CAGR (compound annual growth rate) for HEVs, and a 36 % increase in the CAGR for EVs from 2017 to 2023. At the same time, a 3 % decline in the CAGR for combustion vehicles is to be expected from 2017 to 2023. This outlook from June 2018 shows that combustion engines will still hold the largest market share in 2023. Keeping this in mind, BorgWarner is in a unique position as a company that has evolved and struck a balance between all three types of propulsion: combustion, hybrid and electric.
AI: Sustainability is about much more than just carbon emissions. Do you include recycling in the design of your systems? Heinz: Sustainability is a key part of who we are and what we do. At BorgWarner, sustainability starts with the advanced propulsion system technologies we produce and continues with our manufacturing operations, where our employees are constantly looking for ways to recycle and reuse resources efficiently. BorgWarner’s remanufacturing program (REMAN) is a good example here. For the past 27 years the company has been remanufacturing turbochargers in multiple plants on different continents. In this period, 14,300 tons of cast iron and 3,700 tons of aluminum have been saved by reusing 4.7 million turbine, bearing and compressor housings. We pursue our goal of a cleaner world inside our facilities too – we have already built a few buildings certified according to LEED (Leadership in Energy and Environmental Design), for example in Rzeszów, Poland.
AI: What will the next generation of drivetrains look like? Heinz: The change towards clean and environmentally friendly mobility is set to continue. As we have already said, we expect a 41 % increase in the CAGR for HEVs and a 36 % increase in the CAGR for EVs from 2017 to 2023, whereas the figures for combustion vehicles will decline over the next couple of years. However, regardless of what the next generation of drivetrains will look like, one thing is clear: a highly efficient propulsion system will be needed to get vehicles from A to B. This is where BorgWarner as a product leader in clean and efficient propulsion solutions comes in. We will continue to broaden our product portfolio and optimize existing technologies in order to always provide our customers with the right solutions at the right time. We move things and we will continue to do so in the future.
AI then asked Carlos Castano, Vice President Engineering, BorgWarner Emissions and Thermal Systems, what the main risks are for automotive manufacturers brought about by the growing focus on sustainability and environmental awareness. Castano: There are few challenges as important today as creating solutions that support a cleaner, more energy-efficient world. This requires a commitment to constantly improve the transportation of people and things. At BorgWarner, we made that commitment decades ago and have since been creating technologies to improve efficiency, emissions and performance for all types of vehicles. It is important to keep an eye on the development of all kinds of propulsion systems. For this reason, BorgWarner has a balanced propulsion strategy allowing it to always deliver the right solution at the right time.
AI: Where are the opportunities? Castano: Vehicle manufacturers are searching for ways to make their engines cleaner and more efficient. Hybrid and electric propulsion systems are an important factor in achieving this goal. We at BorgWarner see electrification as an opportunity to strengthen our business. We already have a very broad portfolio covering all kinds of electric vehicles. The pace of change and the ideas being developed provide exciting opportunities. For example, being one of the leading suppliers of 48V mild hybrid technologies, BorgWarner has an expanding lineup of products. Advanced technologies such as P2 hybrid modules can be integrated into existing drivetrains and allow engine and transmission to be decoupled to enable switching between combustion mode and pure electric driving mode.
AI: How important is the thermal management of drivetrains? Castano: As trends like electrification, hybridization and the awareness of sustainability issues grow and emissions regulations become stricter than ever, topics such as efficiency and the question as to how to expand the driving range of these vehicles are now being widely discussed by suppliers and OEMs. The heat management of modern passenger cars is increasingly being decoupled from the internal combustion engine, and assistance from auxiliary heating systems is required. For pure electric driving, solutions that compensate for the lack of heating performance are necessary. These have to work without usable exhaust heat – temporarily in hybrid cars and permanently in electric cars – and have to be energy-efficient so as not to have a negative effect on consumption, range and acceleration. With its battery and cabin heater families, BorgWarner provides a broad product portfolio of thermal management solutions.
AI: What solutions do you offer? Castano: We already have a very broad portfolio with regard to electric vehicles, including all necessary key technologies. As far as future-proof heating concepts are concerned, BorgWarner offers a few groundbreaking heating solutions: the high voltage coolant heater as part of the company’s battery and cabin heater families and the high voltage PTC cabin heater, which is a part of the company’s cabin heater family. BorgWarner’s high voltage PTC Cabin Heater provides industryfirst dual-zone functions and operates independently of waste heat. Comfort is maximized due to rapid, silent warming of the cabin, quick defrosting of the windshield and the delivery of a smooth air stream. The high voltage coolant heater allows comfortable cabin temperatures and offers a high thermal power density and a fast response as a result of its low thermal mass. In addition, the innovation supplies a power range of between 3 and 10 kW and can be applied to a broad range of vehicles. This flexible solution is also available as a single plate and dual plate HV coolant heater.
AI: Which technology are you currently working on? Castano: While the forerunner – the electric drive module (eDM) – has already entered serial production, the fully integrated drive module (iDM) featuring specially developed power electronics is expected to follow as the next logical step. This solution combines highly efficient power electronics with advanced transmission and electric motor technology. Another of our latest innovations is the Onboard Battery Charger, which converts alternating current (AC) taken from the power grid to direct current (DC) in order to charge the batteries. This advanced technology uses pioneering silicon carbide technology and provides best-in-class power density, safety compliance and power conversion efficiency.
More Stories
Towing Services Explained: 6 Key Facts You Need to Know
Environmental Factors That Influence Ceramic Coating Choices
Professional vs. DIY Tinting: What You Should Know