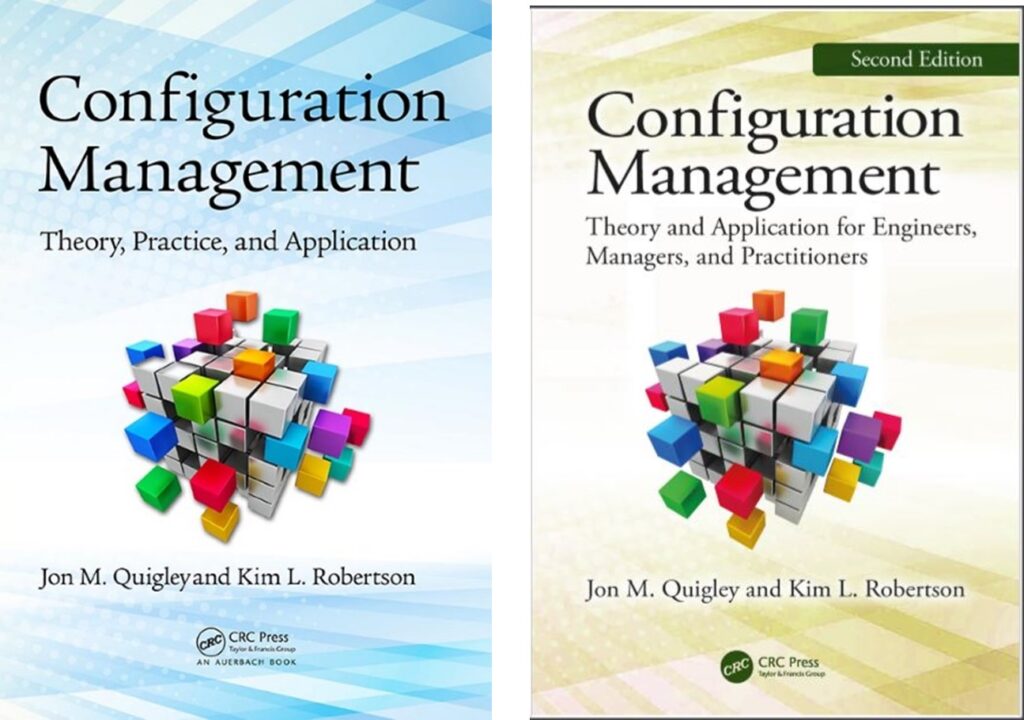
In this article Jon Quigley makes the case for developing common platforms for multiple propulsion systems in order to save costs and provide greater manufacturing flexibility.
Vehicle Development
I do interviews for magazines and businesses on a range of product development and manufacturing topics and especially as it applies to the automotive industry.
Recently in one of those discussions, the interviewer asked me about creating new vehicles. Specifically, do we build vehicles from scratch? This sometimes happens for sure. But many things go into the development and design of vehicle systems. We wrote earlier about electric vehicles tracing back to the beginning of the automobile.
Expensive to develop
To develop and manufacture a vehicle can be a massive expenditure. For example, molds and tools to build the prototype parts, development test equipment, as well as molds and tools to build the production product, jigs, and tools for the manufacturing line, manufacturing equipment for the line, test fixtures, and so forth.
Consider the seat of the vehicle. The material and shape will be different for each vehicle platform, but the mounting tracks and the seat sensing and movement mechanism can be the same. There may be no need to develop these components for a new vehicle.
To start from nothing, creating an entire vehicle is costly indeed, building from iterations, or well-defined subsystems is less costly in time and the development effort. The distributed development effort cost applies to multiple platforms.
Electrification
You may have noticed that even for vehicles powered by internal combustion engines, the vehicle is becoming more electrified.
This electrification essentially creates subsystems that can apply to both internal combustion and electric vehicles. A way to minimize the vehicle costs, and to maximize the quality of the product, is to create common subsystems that apply for multiple propulsion systems.
An article in SAE’s April 2021 issue of Automotive Engineering, Optimizing hybrids, for Cost and Efficiency, describes the variety of propulsion systems that are projected to be available, a specific propulsion system depending upon the application. For example, stop-and-go driving demands are different from continuous driving, and the best propulsion system for these two may not be the same.
Systems for vehicles
Developing components sub-systems, or systems for vehicles, we take an approach that will allow application on more than one vehicle. We may choose to introduce on one specific platform, and to reduce risk we will likely introduce one model series, extending to other model series on the same platform as we learn about the product and customer reaction.
From experience, this is how we introduce new features and to vehicles. Developing the product to some standard set of interfaces allows it to ultimately be used on multiple platforms or model series. This benefit will apply throughout product development and manufacturing cycle.
The same tools are used for installation on multiple platforms and models.
One way to ensure a cost-effective solution for the customer is to manage the developed components in a way that maximizes the volume (material cost savings) and minimizes the impact on the manufacturing line due to product variation.
By defining the interfaces for the various vehicle subsystems, we can create parts that apply to multiple vehicle platforms, achieving some measure of independence from the propulsion system.
These defined interfaces can be physical such as mounting points, or connectors and pinouts, as well as software components such as algorithms, communications, and message handling, or other electrical interfaces such as drivers and analog inputs or outputs.
Fixing these variables provides for ease of interchangeability or more particularly use on multiple platforms. Creating these common interfaces reduces the manufacturing burden, as well as the cost as the components, use on multiple platforms, present a volume purchasing possibility and the aforementioned manufacturing tools and processes.
To accomplish this, we will need to define and control the interfaces.
Configuration management
We start by describing configuration management. This product management collection of processes will be the mechanism by which we will control these interfaces.
This is not a configuration management primer, though we will say we have written a bit on this topic. These books were written by Kim Robertson and myself. If you seek a larger discussion on the topic, one of these books may be interesting. Configuration Management consists of a collection of processes that plan, identify, control, and verify changes to these key product interfaces.
- Management and Planning
- Configuration Identification
- Configuration Control
- Configuration Status Accounting
- Configuration Verification Identification
We will control these identified product and system attributes. We will ask questions about changes to these interfaces with the objective of understanding does the proposed change impact, form, fit, or function. We want no accidental changes or changes with unintended consequences, on the system to which the product or subsystem fits.
For example, physical interfaces, such as attachment points are controlled. A change in the mounting points or envelope of the component, must not impact fit or mounting. If it is, the product may not fit if it or attach as expected.
This will mean the product will not fit in the myriad of vehicle platforms. Think of a double-DIN (DIN 75490) which is 150mm tall and 100mm tall. This same thing applies to electrical connections, shapes, and communications.
Summary
Standard products and interfaces are ways of reducing product and manufacturing costs.
This helps whether the vehicle is largely mechanical or electrical, or when there are changes to the propulsion system.
Standards and configuration management are tools, processes, and techniques to address these changing combinations while not severely impacting the system or the manufacturing of that system.
Development of the propulsion systems and interfacing subsystems can be done in such a way as to allow changing out the propulsion system without impacting the vehicle physicals and the subsystem.
Ideally, we will not have to change these subsystems because we have changed the propulsion system. This is where systems engineering and creative thinking can save development costs and product quality.
More Stories
DuPont materials science advances next generation of EV batteries at The Battery Show
How a Truck Driver Can Avoid Mistakes That Lead to Truck Accidents
Car Crash Types Explained: From Rear-End to Head-On Collisions