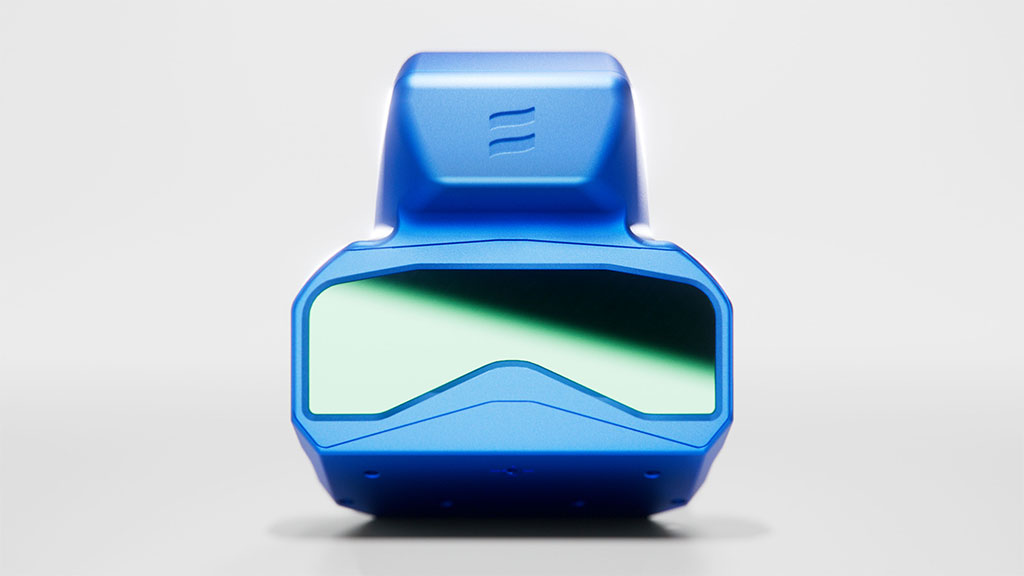
Baraja, creator of the breakthrough Spectrum- ScanTM LiDAR technology for autonomous vehicles, has signed an agreement with Tier 1 automotive supplier Veoneer to industrialize Spectrum-ScanTM LiDAR technology for the next market wave of L2+ through L4 autonomous vehicle applications.
Under the agreement, Veoneer will develop, market, and integrate a scalable Spectrum-ScanTM platform from Baraja to serve the automotive market.
Veoneer chose to partner with Baraja after extensive testing, as Baraja offers robust technology and a roadmap that lends itself to be among the smallest-size LiDARs to enable vehicle integration.
Baraja’s Spectrum-ScanTM LiDAR connects a wavelength-tunable laser to prism-like optics, deflecting the light in different directions to achieve scanning with higher reliability and lower cost. Baraja’s random-modulated continuous wave (RMCW) technology enables industry-leading interference rejection and the ability to measure instantaneous velocity which distinguishes it from traditional Time of Flight (ToF) approaches.
“Veoneer is a natural partner for us. We built our Spectrum-ScanTM technology to enable autonomous driving that is safer, more accessible and ready today for the next generation of vehicles. By combining our technology with Veoneer’s vast experience in automotive design and platform integration, this partnership helps ensure the world’s leading automotive brands can bring that autonomous reality to more people,” said Federico Collarte, Founder & CEO of Baraja.
Spectrum-ScanTM enables Level 4 autonomy Baraja Spectrum-ScanTM LiDAR completely rethinks the way autonomous vehicles see the world around them. Instead of relying on fragile moving parts and oscillating mirrors, it uses dispersive optics to scan the environment, significantly improving reliability and robustness compared to traditional FMCW or spinning LiDAR. Baraja has tested its LiDAR in the harshest conditions, from the outback to arctic tundra, to ensure it works in any condition.
Baraja Spectrum-ScanTM LiDAR creates high-resolution pointclouds to accurately detect objects at more than 250 metres away at speed, while remaining immune to interference from other sensors or light sources. The technology is also more tolerant to factors that have hindered traditional LiDAR systems such as heat, shock and vibration.
Veoneer and Baraja bring world-class expertise closer together
The technology will be complemented with Veoneer’s decades-long industry experience in developing automotive grade sensing solutions for driver assistance and autonomy applications to create a new generation of LiDAR systems enabling automakers to detect and classify objects faster and with more precision.
“Veoneer is committed to offering safe, robust, high-quality sensor solutions to vehicle manufacturers globally. We have performed extensive research among 70 LiDAR technology companies globally, and have come to the conclusion that by partnering with Baraja, Veoneer will be able to offer and integrate scalable automotive-grade LiDAR-sensors in future cars, at competitive prices,” said Jan Carlson, Chairman, President and CEO of Veoneer.
About Baraja
Baraja is building the future of LiDAR to enable the autonomous future. With its revolutionary Spectrum-ScanTM LiDAR technology, Baraja gives leading automotive companies a solid state system in the fast axis that sets a new benchmark in precision and reliability.
Baraja was founded in 2016 by telecommunications engineers Federico Collarte and Cibby Pulikkaseril, who discovered a way to use the industry’s proven optical fiber + photonics technology to solve the problems faced by legacy LiDAR. Baraja is backed by Sequoia, Blackbird Ventures, Hitachi Construction Machinery and Main Sequence Ventures.
About Veoneer, Inc.
Veoneer, Inc. is a worldwide leader in automotive technology. Our purpose is to create trust in mobility. We design, develop, and manufacture state-of-the-art software, hardware and systems for occupant protection, advanced driving assistance systems, and collaborative and automated driving to OEMs globally. Headquartered in Stockholm, Sweden, Veoneer has 7,500 employees in 11 countries. In 2020, sales amounted to $1.37 billion. The Company is building on a heritage of close to 70 years of automotive safety development. In 2018, Veoneer became an independent, publicly traded company listed on the New York Stock Exchange (NYSE: VNE) and on the Nasdaq Stockholm (SSE: VNE SDB).
About Baraja Spectrum-ScanTM
Baraja’s revolutionary Spectrum-ScanTM LiDAR completely rethinks the way autonomous vehicles see the world around them.
Built on proven optical and photonics technologies from the telecommunications industry, Spectrum-ScanTM precisely steers infrared lasers through prism-like optics in the sensor, rapidly switching the laser’s wavelength to send each color of light in a different direction — the same way optic fiber technology works. The resulting pointclouds are extremely high-resolution and immune to interference from other light sources and LiDAR systems.
Because it is solid state in the fast axis, Spectrum-ScanTM sensors have fewer moving parts and are more tolerant to factors that have hindered traditional LiDAR systems such as heat, shock and vibration. It delivers high resolution to detect objects at distance, and speed, and is immune to interference from other sensors and light sources.
Baraja Spectrum-ScanTM operates on the 1550 nm infrared spectrum, making it safe for human eyes, and creates crystal-clear pointclouds with a high-resolution 2000-channel vertical axis and responsive focus to effectively detect objects at ranges of more 250 metres.
Baraja Spectrum-ScanTM is built for maximum reliability in real-world environments. Tested on the dirt roads of mines and arctic tundra, Spectrum-ScanTM has higher tolerance to heat, shock and vibration than other systems so it can brave the toughest environments, from city streets to the outback.
The technical advantage of Baraja Spectrum-ScanTM include:
2000 Channel Vertical Axis
Object detection at range and speed with 10 times the standard vertical resolution.
Working with the highest resolution pointcloud data is the foundation of more accurate perception. Historically, LiDAR resolution has been limited by how precisely a rotating mirror or laser can be moved. But Spectrum-ScanTM technology is a unique solution that uses refraction to completely scan in one axis with no moving parts. Through our approach, we’ve achieved a substantial increase in resolution which is only possible by moving away from mechanical scanning.
Foveation
Ability to detect and focus on objects in the field of view and dynamically change point density on the fly.
The Spectrum-ScanTM platform can dynamically increase pointcloud resolution around key objects, providing enhanced detail to make classification decisions. Points can be foveated to provide the maximum density on areas of interest, such as tracking a target as it moves further away from the sensor. Fully customisable, the perception stack can trigger instant changes to resolution and scan pattern without affecting reliability.
Per-point Doppler Velocity
Ability to measure the instantaneous velocity of each point in the field of view to significantly help segmentation and object detection.
By measuring the Doppler shift of returning light for each point in the pointcloud we can detect whether an object is in motion and calculate its speed. This data can be used to detect movement at a distance, such as a pedestrian stepping out of stationary crowd into the road. And while other LiDAR relies on software processing to infer this information, our measurement is built into hardware.
Better Effective Range
A LiDAR that looks at sensitivity, resolution, beam divergence, accuracy and precision to reliably and confidently detect small objects out at range.
Long range perception is paramount to safe driving, but range alone is a misleading metric if the data doesn’t lead to accurate detection – what we call ‘effective range’. While many LiDAR makers tout impressive specs for their maximum range, flawed pointcloud data can make those numbers useless. Our Spectrum-ScanTM system combines improvements in resolution, beam divergence, accuracy and precision with long-range sensitivity to give you a better ‘effective range’ that ensure partners can classify even small objects at up to 250m away.
Interference Immunity
Accurate sensor data that depicts the real world around the car and is immune to interference from both the environment and other LiDAR.
Traditional LiDAR systems are vulnerable to interference from external light sources, in particular other LiDAR sensors – a major obstacle to safely putting autonomous vehicles on the road.
But the Spectrum-ScanTM platform is the first LiDAR with a unique built-in immunity to all interference. A signal would have to match the exact timing, angle, wavelength and encoding to interfere with our system. This multi-layered protection means no more blind spots in perception and enhanced safety that’s ready for tomorrow’s sensor-filled world.
Blur-free Pointcloud
A solution that allows high-quality point cloud at long ranges without the blur caused by non-solid state scanning in the fast axis.
Blurring is inherent to conventional LiDAR systems due to the rapid movement of mirrors or lasers as they scan in the fast axis – much like how shaking a camera leads to a blurry photograph. At 200m away, pointcloud blur can cause objects to become undetectable.
Spectrum-ScanTM technology uses tunable wavelengths to scan in the fast axis, with no cumbersome moving parts, resulting in a blur-free pointcloud and more reliable information – unlike traditional systems that are stuck with blurring and imperfect data.
Speckle-free Pointcloud
A solution that allows high-quality point cloud data with increased probability of detection at all ranges.
Speckle degradation is a common issue with next- generation homodyne LiDAR sensors, returning false negatives that drastically lower the probability of accurate classification. Through a proprietary receiver photonics chip, we’ve eliminated speckle – ensuring we have a best-in- class effective range that’s ready for highway driving.
Solid state
An elegant system that is completely solid state in the fast axis to mitigate key failure modes.
To create the Spectrum-ScanTM sensor we went back to the drawing board and built our system around optical physics – refracting light through a prism to scan in the fast axis at more than a million times per second with no mechanical parts. This allowed us to remove the most expensive, bulky and failure-prone components of any LiDAR system – the scanner.
This fundamental shift in scanning has allowed us to create a platform with unmatched reliability and longevity.
Automotive durability
Able to be produced at automotive scale and cost while meeting strict reliability requirements for life-time maintenance.
Our core innovation of solid state scanning in the fast axis, using only a laser and a prism, means we’re a generation ahead in terms of performance and reliability.
By removing the mechanical components most prone to failure, our sensors easily exceed the stringent automotive requirements for shock resistance and longevity – lasting over 20 times the standard 10,000 hour lifespan. With the Spectrum-ScanTM platform, we’ve designed a robust and reliable system that requires less maintenance and is ready for commercial manufacturing at scale.
End-game LiDAR
A credible roadmap that will allow for production planning for SOP.
By taking a radically different approach to scanning we’ve achieved breakthroughs in performance and precision. To overcome the inherent flaws of other methods and meet our benchmarks, other LiDAR makers will have to completely rethink their solutions.
Because we’ve solved the fundamental challenges of LiDAR scanning our core technology won’t need to change. So we have a clear roadmap to fit our sensor onto a single chip, unlock the benefits of semiconductor manufacturing, miniaturize our product and lower the overall cost to meet automotive requirements.
More Stories
Towing Services Explained: 6 Key Facts You Need to Know
Environmental Factors That Influence Ceramic Coating Choices
Professional vs. DIY Tinting: What You Should Know