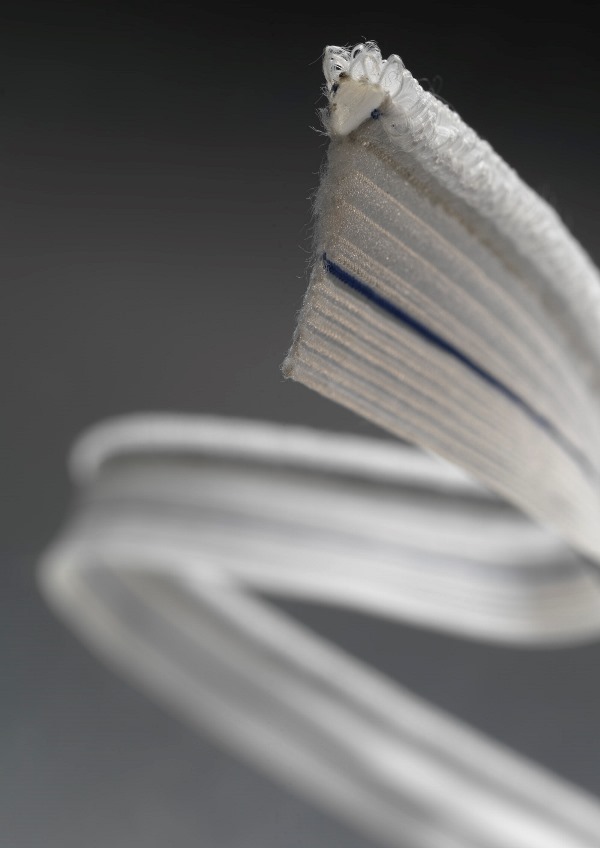
Digital transformation of the factory floor and integration with the rest of the company’s operations is proving to be a lifeline for medium-sized manufacturing operations as it allows them to remain competitive.
Being able to generate data is only the first step in the transformation. Management systems are required to collate, analyze and share the information. There is a direct link between connecting the entire supply chain and increased profitability, according to the developers of FactoryEye, which integrates information flow from order to delivery.
Automotive Industries (AI) asked Terri Ghio, President of FactoryEye North America, what makes the system different from other enterprising software solutions.
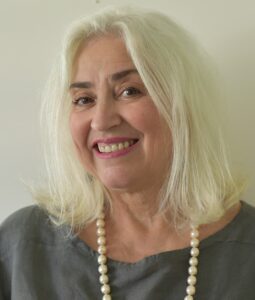
Ghio: There are several unique differentiators. One of the biggest is that many of these companies only have one piece of the solution, they only have an MES (manufacturing execution system) or analytics system. We can offer either or both. In other words, our solution can either “layer over” what you have or provide additional functionality, depending on your requirements. We have a holistic view of their operation and focus on the pain points.
Another is our ability to connect and communicate with existing systems with minimal disruption. We enhance what is already in place including adding sensors that allow aging equipment to be monitored while producing actionable data to enhance future processes. Many automotive manufacturers have complicated production processes that include a combination of injection molding, metal processing, different types of assembly processes and more.
Our solution is flexible enough to support automated and semi-automated processes. For example, in ultrasonic welding the process is semi-automated, so the operator has to set the base of the machine. In those cases, there is still sensitivity in material management and traceability to manage OEE and reduce downtime, but the manual element has to be considered in data.
Our approach to implementation also makes us unique from other 4.0 software solutions in the marketplace. We want to show return on investment for our customers as soon as possible so we implement in what we call “sprints” in 90-120 days to show results and then move on to the next sprint (which is generally paid for by the first sprint).
AI: Is the Automotive Industry strategically important for FactoryEye over the next 5 – 10 years?
Ghio: Yes, we see automotive as critical to our growth path. We have recently signed two very well-known and entrenched business partners with over 30 years’ experience in the automotive market. Our solution is what they have been looking for to stay competitive. The Automotive market is embracing Industry 4.0 and we bring an affordable solution to the mid-market.
For automotive manufacturers, the main concerns that FactoryEye can help alleviate are quality and lead times. In general, quality of service improves the customers’ service experience. Creating a consistent flow of quality products is important for car manufacturers since they need a timely flow of parts to keep their production line moving. Many large manufacturers look for local suppliers to reduce uncertainty related to offshore suppliers.
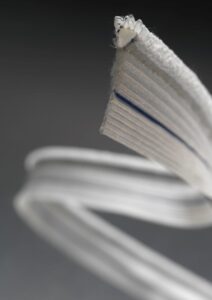
AI: What advantages does Digital 4.0 automated business reengineering bring to the manufacturing process?
Ghio: The most important advantages are speed and accuracy. The ability to make changes in a timely manner and to understand immediately when there is a quality issue. Industry 4.0 also helps with recruiting new talent who are comfortable with and embrace the use of technology. Technology can help automotive manufacturers maintain critical information that could be lost with aging experts who are leaving the company.
AI: How significant are the R.O.I. of a company’ overall production management cycles i.e. ERP, PLM, QMS …etc. using Digital 4.0?
Ghio: Digital 4.0 is needed for management to fully understand the needs on the production floor. FactoryEye is one of the leading drivers of integration in the industry and this is a strength we bring to all our customers. Siloed information throughout the production process makes it difficult to pinpoint the areas that will benefit the most from Industry 4.0.
AI: What size enterprise was FactoryEye developed for?
Ghio: FactoryEye was developed specifically for the mid-sized market. We saw the need for an affordable solution that could be implemented with minimal disruption to operations.
AI: How important is the machine learning component in your solutions for achieving the expected process efficiencies and ROI?
Ghio: It is the difference between looking in the rear-view mirror and looking forward. Predictive analytics with real actionable data are what makes a difference for manufacturers! Knowing in advance when to schedule maintenance or what will likely go wrong gives you control and the ability to make rational decisions instead of just putting out fires. We call it “Actionable Intelligence”.
Our quality procedures are extremely strict. FactoryEye helps to reduce product waste by utilizing online quality equipment that monitors product quality, collects the data, and provides feedback to the operators to improve machine performance. We have one auto parts manufacturing customer in the U.S. that increased productivity by over 100%.
AI: Are your solutions a one size fits all, plug and play software?
Ghio: Our solutions are a “one size adapts to all”. We deliver best business practices in a scalable solution while making it “plug and play’ to minimize disruption. Working with our Automotive Industry experts we can implement a series of problem-solving sprints which pinpoint the most immediate need for change while utilizing our continuous improvement model to produce accurate results.
AI: How does FactoryEye tech fit around differentiated customer needs, environments and manufacturing requirements?
Ghio: It is a scalable and configurable solution which is only as good as the expertise driving it. We have both. Our easy implementation process consists of three parts: integration with ERP systems (such as JDE, Microsoft Dynamics, Infor and many others), a phased-in implementation of the new MES system and the implementation of the FactoryEye Smart Analytics system. This way we can help automotive manufacturers quickly start their 90-day sprints to produce accurate, actionable data as quickly as possible.
One simple example is a customer needed to improve productivity for its injection molding machine to produce car dashboard parts. This customer was struggling with a long set-up time and excessive rejects due to a variety of reasons. Using our installed sensors, we sent automatic messages to managers when the rejects surpassed a percentage threshold so they could act. Then, they could fix the process in real-time to stop producing rejects.
AI: How can mid-size manufacturers trust FactoryEye technologies to deliver the best optimized solutions for their processes?
Ghio: The technology follows the lead of the industry experts not vice versa. Once you realize we understand your needs and the solution is there to support changes and give accurate information then it is a no brainer.
More Stories
What You Need to Know About Tire Pressure in Winter vs Summer
Auto Repair Services: Keeping Your Vehicle Road-Ready
Unleashing Creativity with Vidnoz: The Best Free AI Video Generator in 2025