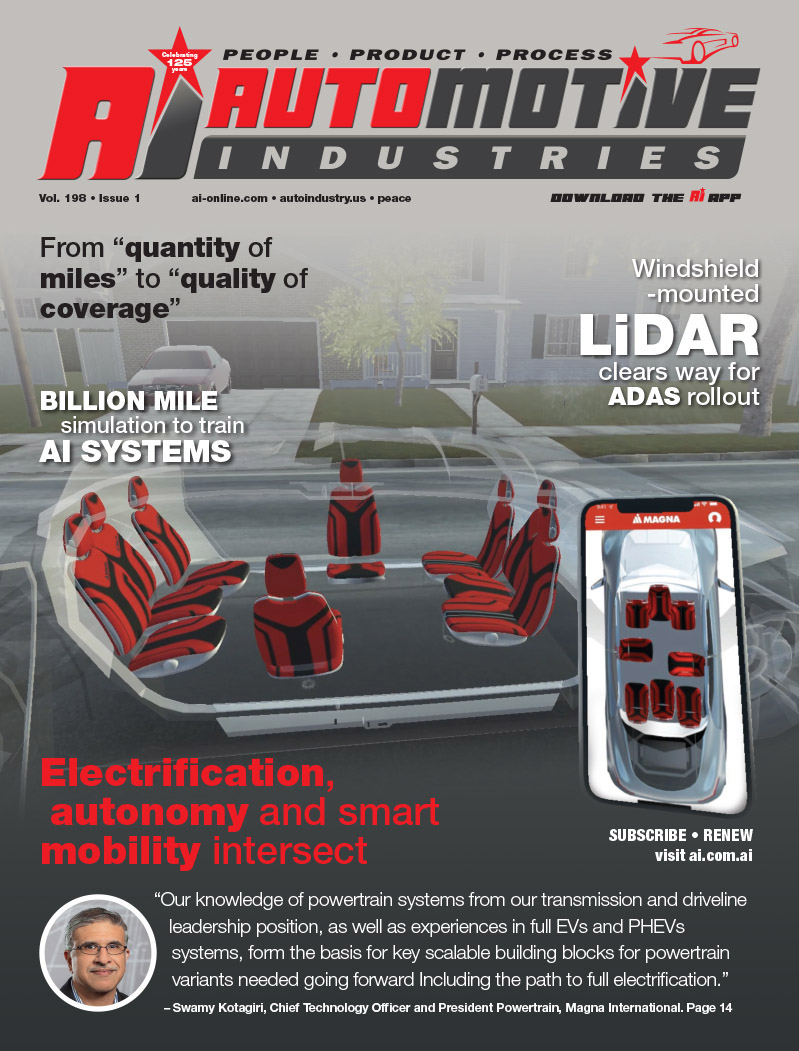
In the mid-’90s automakers and suppliers were looking at Russia like they are now looking at China.
Virtually every automaker had some sort of production plan for the world’s largest country and suppliers seemed willing to follow their customers to supply high quality, high-technology components. The market was large and growing and while customers were craving the latest vehicles local automakers were supplying lowquality cars straight out of the ’70s.
It seemed like the automotive promise land.
But economic crisis hit in 1998, the ruble fell and automakers had to deal with problems in their home markets. Russian plans fell to the side. Five years later the spotlight is again starting to brighten on Russia. It’s slower than before but automakers are more cautious than before.
During the last year the world’s two largest automakers opened production facilities while others have reconfirmed their intentions to build vehicles in the market. Oil companies are setting up partnerships in Russia, while local automakers and suppliers find the money to invest in their aging operations. Most importantly, the government has detailed a plan for the industry, including curbing the import of used vehicles. While experts agree the market is still volatile and at times dangerous, there are ways to succeed in Russia.
When you are in business you have to take a risk, says John Mylonas, managing director of the GM-AvtoVAZ JV plant. “If you are timid in life for everything you will never get out of bed,” he says. “You have to do a plan, evaluate a risk and go for it.”
According to GM data, the new car market in Russia currently totals about 1.1 million units. By 2006, that number should touch 1.5 million cars. Former head of GM Russian operations David Herman says Russia is one of the largest markets in the world and will grow faster than others.
“Russia will grow in importance,” he says. Ford estimates the market for new Russian car sales at almost 1.3 million units while new foreign vehicle sales will touch 108,000. Used foreign vehicles — a growing and very important segment — will equal 505,000 units.
More importantly, the market is turning into a global low-cost source for cars and components due to low labor, material and energy costs, which are 1/6 of those in Europe and will remain substantially lower, says Herman.
![]() |
SHAAZ uses copper strip and brass tubes to build radiator cores via CuproBraze technology. |
![]() |
GM assembles Chevy Nivas using VAZ-stamped body panels at the GM-AvtoVAZ joint venture. |
Ford and GM race to market
Seeing Russia as a local production location and export powerhouse, both Ford and GM opened new production facilities in Russia last year. But their strategies could not be further apart.
GM turned to Russia’s largest automaker AvtoVAZ to build an existing Russian vehicle, while Ford essentially went it alone to build a European/American vehicle. Both plans seem to have been successful.
GM-AvtoVAZ was born after years of negotiations between GM and AvtoVAZ. The two, with help from the European Bank for Reconstruction and Development (EBRD), formed the joint venture to build the Chevy Niva. The Niva was already in small-scale production by VAZ, who sold the rights to the vehicle to the joint venture.
“We in GM did a good decision,” say Mylonas. “It wasn’t an easy one.”
The SUV is built in a new facility located on the grounds of the AvtoVAZ plant in Togliatti — Russia’s Motor City. GM essentially assembles the vehicle using bodies stamped nearby by VAZ. The joint venture, until very recently, also used VAZ’s paint shop.
Most of the assembly work is then done by hand with the only robot in the plant spraying on window adhesive. When the new paint shop is up and running it will be fully robotized. Production started in September with the vehicle selling out into the summer. GM will meet the robust demand by adding shifts at the plant. It will also start exporting to other Russian countries and, more importantly, to Western Europe.
In the beginning, Mylonas admits quality was questionable but GM worked on it and continues to work on it.
Ford took the opposite approach. It entered the market by itself with only a bank as a partner. It also located in Vsevolozhsk, near St. Petersburg, but far from other automakers. And while GM essentially assembles the Niva, Ford presses, welds and paints the Focus, which it builds at the plant three different body styles with four different engine options.
It is a complete manufacturing plant, says Henrik Nenzen, head of Ford’s operations in Russia, at a seminar about the Russian auto industry.
Ford set up shop in what it calls a greenfield location even though the walls were already standing. A start-up decision was made in June 2000 with production starting July 2002.
According to Nenzen, the automaker decided to make the $160 million investment because the basic strategic resources are in Russia. Labor costs are low, the government stable and trade is possible. Couple that with the low vehicle ownership and the venture is highly viable, he says.
Besides selling locally, like GM, Ford hopes use its Russian operations as a global export location. But unlike GM, Ford would also like to export components and its European operations have already expressed interest in parts. “High growth potential was the reason for going to Russia,” Nenzen says.
The company can build five different models the facility. It is currently building 25,000 vehicles a year but can increase that to 35,000 if needed and eventually will be able build up to 100,000 units.
It has an agreement with the government use 50 percent local parts and is ramping to that amount. It currently uses about 20 percent local components.
Public reaction to the Focus has been good, says Nenzen. Some 3,600 vehicles were sold in 2002, with that number set to jump to 14,000 this year, 18,000 in 2004 and 22,000 by 2005.
“We are sold out through July already,” he says. “We are trying to ramp up production as quickly as we can.”
Ford says its quality from the start was at European levels even though it drastically reworked the car for the market. Nenzen also says the facility is 1.5 years ahead in its profit forecast.
Even with their limited time in the market, Nenzen and Mylonas offer advice for other companies looking to locate in Russia. Know the business and know the customer, says Ford’s Nenzen. “I would say to anyone coming in they have to have a good guide,” Mylonas says, “a good lawyer and a good accountant.”
Use the available resources, he says. The Russian people are innovative. “Over the last 70 years they exercised their brains because no one could tax it,” he says.
Mylonas’ most trusted Russian employees regularly argue with him.
“I always know that people who say no to me will do the good job,” he says. “If they argue they understand the details if they just say yes they don’t understand.”
While the Ford and GM plants are up and running. Renault SA recently reconfirmed its plans to build vehicles in Moscow at Avtoframos — a company owned 62 percent by Renault and 38 percent by the city of Moscow. The company will invest about $320 million to build the X90 — called the Symbol in Russia — at a rate of 60,000 units per year starting in mid-2005. The inexpensive vehicle is built on the company’s B platform at the old Moskvich car plant.
The facility will eventually increase production to 120,000 units each year. That is expected to happen after 2007.
Renault hopes to have an eight to 10 percent market share in Russian within five years, says Georges Douin, Renault’s executive vice president, product and strategic planning and international operations.
Local manufacturers still in the game
Even with global automakers making inroads into Russia, local automakers will most likely continue to supply the majority of vehicles to Russian consumers.
When communism fell, these automakers emerged with little technology and completely outdated vehicles. Fighting to stay alive, some of these companies continued to build the same vehicles while others emerged from privatization with plans to fill new segments cropping up in the marketplace.
The largest, AvtoVAZ, has introduced only a few new vehicles and continues to build the Lada variants that crowd Russian streets. The company is overstaffed and builds more vehicles than demand warrants.
Izmash-Avto is the No. 2 automaker. It built 68,000 vehicles in 2002 and plans to dramatically increase production this year to 120,000.
GAZ, which is one of the few automakers to see success in the last decade, builds the age-old Volga. But it has developed and launched two new lines. The GAZelle van and Sobal minibus/light commercial vehicle have found success among Russians looking for an alternative to the sedan or SUV.
GAZ expects to see an increase in sales this year, says the company’s head of marketing, but segments will be redistributed with Volga sales dropping to 58,500 units and GAZelle and Sobol sales increasing to 123,000.
The increase should total about 2.5 percent, says Fanis Hasanov, GAZ deputy director, purchase director.
The company is also planning several investments this year including modernization of the Volga plant and adding a diesel engine from Iveco in its GAZelle and Sobol ranges. Total investment is expected to touch $24 million.
Italy’s troubled Fiat SpA had negotiated a joint venture with GAZ to build a vehicle on its Stilo platform. GAZ now says the venture will not happen and its activities with the company’s Iveco division have taken the place of the planned joint venture.
Room for suppliers
Nenzen, Mylonas, Herman and others would agree that a huge part of the future of the auto industry in Russia is parts suppliers. While some foreign suppliers have located in Russia more are needed.
“We are trying to create an industrial park for suppliers to locate,” say Herman. GM especially needs European suppliers as it considers building an Opel vehicle in Russia. Ford, meanwhile, would also like to see global suppliers make the investment in Russia.
“We are looking for suppliers,” he says. “We are looking for suppliers who want to grow.” But what happens to existing Russian suppliers? In some cases they are bought out by global suppliers in other cases they slowly die. In the rare instance, they make a huge investment and bring their facilities up to Western standards.
While this is relatively rare, it recently happened in Western Siberia. SHAAZ, a radiator company located in Shadrinsk, recently invested about $12 million in a new CuproBraze heat exchanger facility.
The company, owned by the Ural Mining and Metallurgical Co. (UMMC), had been supplying virtually all of Russia’s truckmakers and automakers with traditional aluminum radiators. Seeing an opportunity to grow its business inside and outside of the Russia auto industry, it signed on with the International Copper Assn. (ICA) to become a licensed builder of the ICA’s CuproBraze technology.
CuproBraze allows the production of charge air coolers that are able to withstand higher temperatures than existing technology. By replacing temperature challenged aluminum charge air coolers with copper-brass counterparts, automakers can cut emissions and increase fuel efficiency. Seeing a need for the technology, SHAAZ significantly reconstructed a plant on its manufacturing complex and installed all new machinery that will turn out 450,000 radiators, including 250,000 charge air coolers per year, by 2005.
![]() |
GM-AvtoVAZ has only one robot (above) on its assembly line. It sprays on window adhesive. |
Instead of turning to Russian companies for machinery, SHAAZ turned to American and European companies for the newest technology. Seco/Warwick Limited supplied the continuous belt furnace from its facility in Poland. Germany’s Schoeler GmbH supplied the automated spray and slurry machines and the semiautomated core assembly machine. Outokumpu supplies the copper from Sweden with BrazeTec supplying the brazing material.
What results is a radiator with five to 10 percent better performance. It may also fill a need automakers and truckmakers may see develop in the next five years. Experts say that beginning in 2008 aluminum will no longer be used in the production of charge coolers because of high temperatures. Some companies have said they will use a pre-cooler but this will take up space under the hood and require companies to rearrange the engine compartment.
The CuproBraze radiator is the solution, says Gert Lundmark, managing director of Outokumpu. The copper radiators have a cost, size and performance advantage, he says. With the only drawback being that the CuproBraze products do have a penalty on weight vs. aluminum.
With this discovery, SHAAZ may also have a chance at becoming a worldwide exporter. It is one of less than a handful of companies using the CuproBraze technology. The company says it is ready and willing to ship around the world if needed.
“While we will continue to be a key supplier to the Russian auto and truck industry, our goal is to export 50 percent of our production capacity,” says Vladimir Kolotushkin, general director of SHAAZs, “Our global competitiveness will be a key measure of our success and CuproBraze technology will be a key ingredient in that success.” Government policy to help industry Automakers and suppliers alike have asked for help for the Russian government. And the Russian government has responded with a plan to help integrate the Russian automotive industry into the global arena, says an Ernst and Young study. It made public its plan The Government Concept of Automotive Industry Development up to 2010 — in July 2002.
Major goals include:
- Improvement of domestic technical standards to meet international norms.
- Implementation of advanced technologies new assembly lines.
- Production of automotive components, basing new technological levels on international standards.
- Production of modern automotive components and materials.
- Optimization of customs tariffs and tax regulations.
- Expansion of Russian production into international markets.
- By 2010, increase the supply of cars to the Russian population by 1.7 times.
“The decreasing scale of tariffs (on imported components) which are 35 percent now would be down to zero hopefully by 2012,” he says.
On a local level, change will come slowly as people get used to working with foreign companies. GM’s Mylonas says customs policies must change and bank policies must eventually evolve.
For example when GM sent $25 million to Russian bank Mylonas signed the paperwork — with a black pen — and thought he was done. But the paperwork was sent back with a note that it has to be signed in blue. This was the first time they had to do this,” Mylonas says.“They have to learn.”
Most Performing Automotive Sector Over the Next Five Years
Domestic Production by Multinational Producers = 79%
Automotive Components = 43%
Import of Used Cars = 11%
Import of New Cars = 11%
Domestic Production by Traditional Russian Producers = 7%
Source: Ernst & Young
Foreign automaker activity in Russia
BMW/Kia
Since 1999, Kalingrad’s Avtotor has collaborated with BMW in SKD assembly. It also assembles Kia’s Sportage SUV.
Fiat
Fiat planned to build a Stilo-based vehicle in Nizhny Novgorod with GAZ. Those plans have been put on hold.
General Motors
GM is building the Chevy Niva SUV with AvtoVAZ at a new plant in Togliatti. The venture plans to assemble models from GM and Opel as well as Opel engines in the near future.
Ford
Ford launched a production plant in Vsevolozhsk in July 2002. The venture currently produces three versions of the Focus. Due to the high demand for its products, the company is planning to boost production by adding a second shift at the plant. The factory is designed to produce virtually any Ford model car or light commercial vehicle.
Hyundai/Citroen
Hyundai vehicles have been assembled at TagAZ in Taganrog since July 2001 with production concentrated on the Accent. The company is considering switching from SKD to CKD this year. TagAZ also assembles the Citroen Berlingo.
Renault
Renault currently assembles the Symbol at Avtoframos. Full scale production is set to start in 2005.
Scania
Scania started bus production in July 2002 at a plant near St. Petersburg.
Volvo
Volvo recently started truck and towing vehicle production in Zelenograd with local partner Sistema.
Source: Ernst & Young
More Stories
Essential Features to Look for in ADAS Calibration Systems
Your Guide to Filing a Car Accident Claim
Steps to Take Immediately After a Car Accident