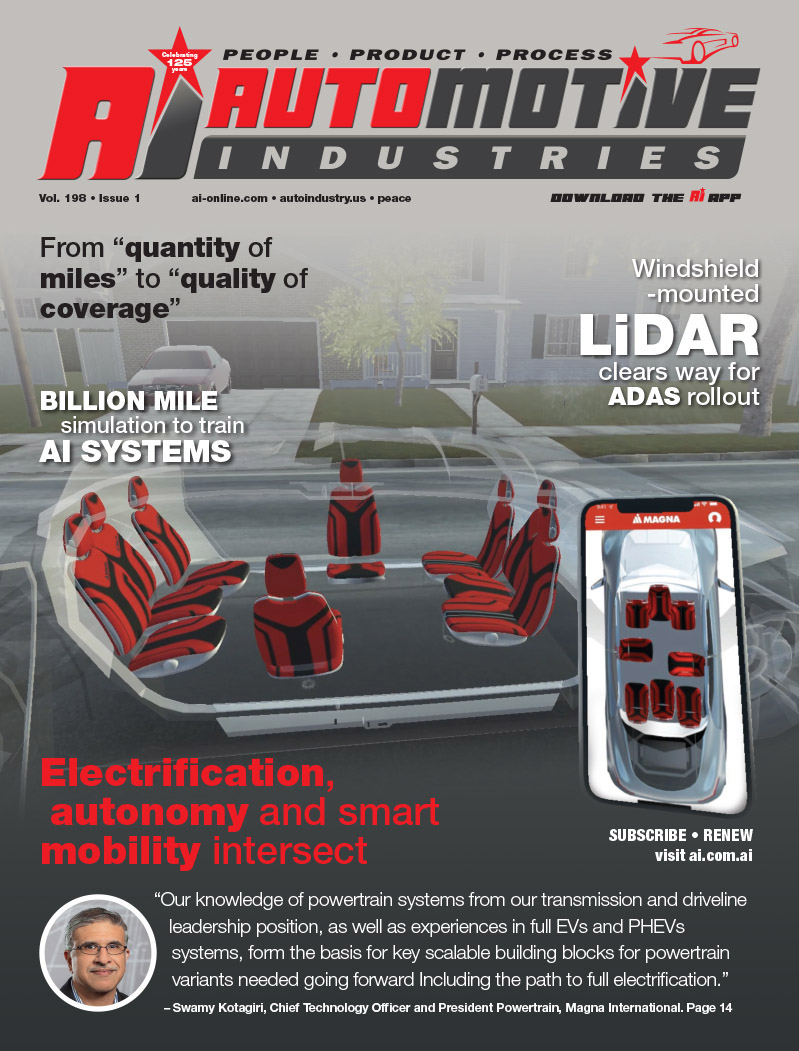
Serious efforts appear to be paying off
![]() |
Ford Quality vice president, Louise Goeser has made sure that quality really is job one. |
On the other hand, Ford’s vehicle quality and customer satisfaction have not declined by any measure over the past five years. In fact, they have improved. But they have not improved as fast as the competition’s.
“Between 1998 and 2003,” says Brian Walters, director of Quality Research at J.D. Power and Associates, “Ford has improved about 18 percent in initial quality.” To put that performance in context, however, industry IQS (Initial Quality Survey) results improved nearly 25 percent in the same period. Competitors General Motors Corp. and DaimlerChrysler AG each improved about 28 percent, while Toyota Motor Sales improved about 26 percent.
“What’s interesting,” Walters continues, “is that between 1998 and 2001, Ford’s IQS stayed flat — there was relatively no change. Meanwhile, the industry was improving at a rate of about 6.7 percent a year, so they were losing competitive ground.”
In other word’s, Ford’s 18 percent improvement over five years really occurred in the last two years. “In those two years,” Walters says, “their IQS has improved more rapidly than the industry’s has — which they have to do to close the competitive gap that was opened between ’98 and ’01. They’re in a catch-up mode.”
Of course, there is a lot more to QRD (quality, reliability, durability), than J.D. Power’s IQS ratings, which are derived from surveys of new-vehicle owners after their first three months of ownership. Two other well-known J.D. Power measures are VDI (Vehicle Dependability Index) and SSI (Sales Satisfaction Index); and there are many more — some scientific, others not — from a variety of other research firms and publications.
Most concur, however, that Ford (including Mazda and PAG brands Volvo, Jaguar and Land Rover) lost ground in QRD by improving too slowly or not at all between 1998 and 2001, then gained some back in ’02 and ‘03. The individual whose critically important responsibility is to build on those recent gains is Ford Quality Vice President, Louise Goeser.
Goeser, who joined Ford March 1, 1999, after five years at Whirlpool and 20 years at Westinghouse Electric, has much to celebrate in recent survey results, including Power’s recently released 2003 IQS. Although still slightly below the industry average of 133 reported “problems” per 100 vehicles (PP100), Ford’s score of 136 PP100 surpassed DC’s 139 and gained ground on leader Toyota at 115, 4th-place Honda at 126 and 5thplace GM at 134.
Among individual Ford brands, Mercury placed a healthy sixth of 36 in IQS (behind premium marques Lexus, Cadillac, Infiniti, Acura and Buick), Jaguar was 10th and Volvo 12th, all above industry average. Slightly below average but still respectable (and, surprisingly, ahead of all Japanese brands except Lexus, Toyota and Honda) were Ford at 18th and Lincoln, tied with Nissan at 20th. And the differences are very small, with 17 PP100 separating Jaguar at 122 and Lincoln at 139, vs. the industry average of 133. Also, five Ford-family vehicles — Mercury Sable, Ford Crown Victoria, Mazda Miata, Mazda BSeries and Ford F-Series pickups — won their individual segments against stiff competition.
What specifically has been done in the past four years to boost Ford’s QRD and customer satisfaction? “The basic things we focused on,” Goeser says, “were: first, how do we measure quality the way our customers do? Second, how do we make sure quality is a key priority for everyone in the company? And third, how do we improve our skills in quality?”
She points out that Ford is the only “major” maker to improve in the latest J. D. Power IQS, while the rest of the industry stayed flat, and the only maker to improve in each of the last six years in Power’s VDI, which (until recent changes) surveyed owners following four to five years of ownership. “When we measure ourselves,” she says, “the key measures we look at are not just initial quality but also highmileage and long-term durability.
“We focused on reliability and robustness principles in the design process and engaged all of our engineering organization globally in looking at the most prominent high-mileage issues, putting teams together and training them on how to do high-mileage improvements. When I started here, we had done maybe 10 or 15 projects like that. In the first year, we expanded that to over 100, and in the next year we included our 100 top suppliers. We now have a reliability ‘statement of work’ in purchase orders that requires suppliers to go through the same process we use internally for robustness and reliability.
“So we expanded the techniques, we have a lot more engagement, and we tied the results to our overall corporate metrics and bonuses. Quality objectives are included in bonus calculations, based on the measures of low time-in-service, high time-in-service and sales and service satisfaction.” As quality vice president at Whirlpool, Goeser initiated the data-driven global statistical problem-solving process called Six-Sigma, which she implemented at Ford beginning in 2000. Since its implementation, 6-Sigma is credited with saving about $1 billion worldwide in waste elimination, cutting product “Things Gone Wrong” (TGW) in half and helping to reduce recalls from 28 in 2001 to 16 in 2002.
Goeser calls Ford’s customer-driven 6-Sigma the “third leg of the stool,” the other two being people and processes. The company has completed some 6,000 6-Sigma projects worldwide and trained 2,000 socalled Black Belt experts, who facilitate the process, and 40,000 Green Belts, who help support it. “The results,” she says, “are vehicle quality, sales and service satisfaction and eliminating waste in our processes.”
One recent example is a “squeak and rattle” problem identified from customer feedback in Explorer Sport and Sport Trac vehicles. A 6-Sigma Black Belt, assisted by a team of Green Belts, conducted a series of tests at the assembly plant, diagnosed the problem as a loose running board sealer and quickly eliminated it, reducing TGW by three points and ongoing cost by nearly $2 million.
On the process side are Quality Operating Systems (QOS), “standards, methods and processes,” Goeser says, “to assure the quality of the design process, the product development process, the manufacturing process, the sales and service process and supplier processes. That’s a major undertaking. And every year we go through a check process that says, ‘OK, here’s our standard this year; how do we upgrade that? What worked and how do we upgrade it again next year?’” A major part of QOS is the Q1 process (Ford’s version of QS9000), which requires suppliers to re-certify each year. “Q1 means you have achieved the standards of Quality Operating Systems as described,” Goeser explains. “It’s not a ‘gimme.’ We actually visit and audit a huge number of suppliers to validate that they continue to be Q1. And you can think of Q1 as extending througout Ford, through product development, manufacturing, and so on.”
On the people side, as part of the process of “engaging all employees” — from top leadership to salaried and hourly people at all levels — are Quality Leadership Initiatives (QLIs). “We work very well with our union partners in engaging all employees in quality improvement,” Goeser says, “to bring it to each person… their responsibilities, their engagement.”
Among Ford’s QLI principles are: “Help us help suppliers succeed,” “Relentless daily focus on quality” and “Ensure people have the necessary skills and tools.”
Following relatively smooth 2002 launches of 10 redesigned or substantially updated products — including Ford Expedition, Lincoln Navigator, Ford Crown Victoria, Mercury Grand Marquis and Lincoln Town Car — what specific steps have been taken to ensure a trouble-free launch of the critically important all-new F-150 pickups?
“We’ve done a lot,” Goeser says, “that makes me confident we’ll see a wonderful vehicle. To begin with, the design is fantastic; it’s going to set a new standard. Beyond that, we brought manufacturing into the product creation process much earlier, we’ve increased the number of vehicles being driven for durability proof-out, we’ve increased our process audit capability at the assembly plant and — this is an important one — we’ve conducted regular onsite reviews of production processes at our top 50 suppliers as they accelerate to run rate.
“We’ve done a whole lot of detail work around this launch, including keeping the launch team there until the external indicators show we’ve met our targets, so I’m feeling very confident.” Beyond all that, she adds, the Norfolk, VA, lead plant is one of Ford’s and the industry’s best facilities, and the current F- 150 led its class this year in J. D. Power IQS.
Summing up Ford’s progress in recent years, Goeser asserts, “If we look at all the different measures, we’re at the best-ever level in low-mileage vehicles, high-mileage vehicles, sales and service, warranty and recalls. So when we look at our scoreboard, we’re moving in the right direction. We’re seeing progress on all fronts, and we’re at best-ever levels. Of course, our goal is not just to be at best-ever levels but to be at best-of-industry levels.”
Adds J. D. Power’s Walter’s: “This is for the most part an industry that is built on continuous improvement. With the exception of this year, the industry has historically improved five to six percentage points per year. If you as a manufacturer are not keeping up with this industry rate of improvement, you’re losing competitive ground.
“Ford appears to have turned the corner on that, based on its improvements in 2002 and 2003. They have picked up their focus on continuous improvement and appear to be beating the average rate of industry improvement and beating the rate of improvement of some of its their competitors. If they are able to continue this — which they need to do — they will begin to close that gap.”
No easy task, as every automaker worldwide continues working extra hard on QRD — but one that Ford has proven capable of doing, given its recent strong improvement.
More Stories
Your Guide to Filing a Car Accident Claim
Steps to Take Immediately After a Car Accident
What Makes SUV Cars More Prone to Accidents?