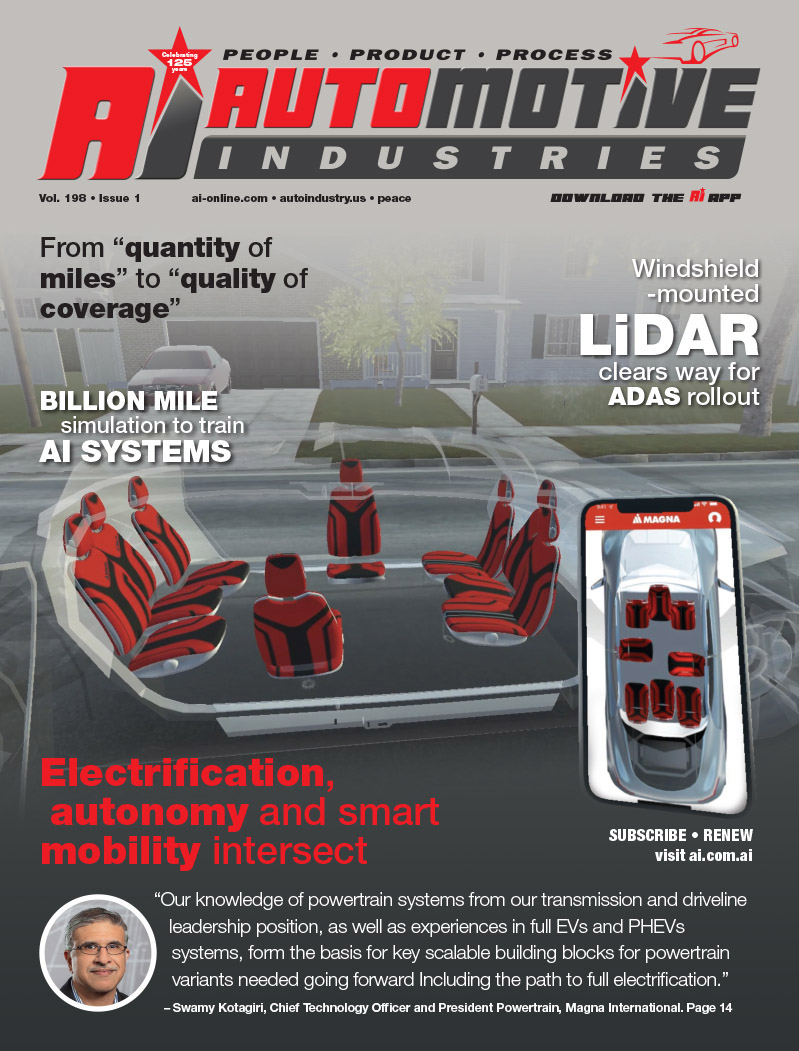
Once the preserve of luxury car powerplants, variable valve timing is now spreading to more mainstream engines. Case in point: the arrival of General Motors’ new ‘high feature’ global V-6 engine family, the first engine from GM to feature VVT on both intake and exhaust camshafts.
The first of this V-6 family, a 3.6L will make its debut in Cadillac’s 2004 CTS, replacing its existing, U.K.-sourced 3.2L V-6. The new 255 hp CTS motor is one of several versions of the modular V-6, which will also come in 2.8L and 3.2L displacements, to be used in major markets worldwide. Engine size can be expanded to 3.8L, or as large as 4.0L when the cylinder liners are eliminated in favor of bore coatings.
Versions of the engine will be both naturally aspirated and turbocharged and applications will include front-, rear- and all-wheeldrive, as well as hybrid vehicles.
One key to the new engine family’s success, maintains GM, is that it will be competitive with the best in the V-6 class, such as the Honda/Acura 3.2L and Toyota/Lexus 3.0L units, yet be built at a lower cost. All GM’s V-6s will share the following features: aluminum construction, dual overhead camshafts, fourvalve- per-cylinder valvetrain, roller-finger followers, continuously variable cam phasing, electronic throttle control, forged-steel crankshaft, piston-cooling oil jets, coolant-loss protection software, GM’s oil-life system, 32 bit microprocessor and coil-on-plug ignition.
![]() |
A valve in the dualstage manifold closes to boost cylinder charging in the low- to midspeed range. It opens at higher speeds to feed all cylinders from a common larger plenum. |
![]() |
Work on the new V-6 family started in 1999, and was completed in record time, says Tim Cyrus global V-6 chief engineer.
“The goals for the engine were industry leading reliability, flexibility, package size, pleasibility, efficiency and value,” Cyrus says. The engine can be easily integrated into most platforms, has industry leading NVH and performance with three discrete combustion systems MPFI, SIDI and turbo.”
Importantly, the V-6 engine architecture was designed to incorporate different options, in order to create a broad range of configurations. As well as normally aspirated/ sequential port fuel injection ‘foundation’ architecture, there are two potential major variants. One is a spark-ignition direct-injection (SIDI) V-6 of either 2.8L or 3.2L displacement. To account for differing market regulations and conditions, particularly in Europe, the engine design can accommodate both stratified-charge (lean-burn) and stoichiometric- charge SIDI architectures. Also in the pipeline are turbocharged 2.8L or 3.2L variants, with a variety of power and torque outputs depending on specific content.
As well as its adaptability, the key feature of GM’s V-6 family is its use of variable valve timing. Moving to full VVT eliminates the traditional compromise in engine design between power and torque outputs, and also improves fuel economy and lowers emissions. In the case of the 3.6L engine, the improvement in torque output is notable: 90 percent of the 252 lbs-ft. peak torque is available across a broad operating range, from 1,600 to 5,800 rpm.
Compared to an existing GM double overhead cam V-6, the 3.6L develops 20 percent more peak power, a 13 percent increase in peak torque — and a 24 percent increase in torque-integral, or the amount of torque available at most points throughout the rpm range.
“Flexibility was very important,” says Bob Jacques, base engine design system engineer. “We insisted on going after high performance and high refinement at the same time.”
![]() |
A 32-bit micro-hybrid engine control unit embeds all of the necessary electronic circuitry on a four layer substrate that reduces the size of the unit. The new design can be engine mounted, freeing up valuable engine compartment space. |
An added benefit of the VVT system is that it allowed for the elimination of the exhaust gas recirculation system, thus reducing weight and complexity.
The V-6’s intake system includes a dualstage variable manifold. A valve in the manifold changes the plenum volume available for resonance tuning of the inlet flow path. When the valve is shut, the cylinders feed from two separate plenums. In this mode the system boosts cylinder charging in the low- to midspeed range. At higher engine speeds, the valve opens and the cylinders all feed from a common larger plenum.
Another significant technical advance is the V-6’s 32-bit micro-hybrid engine control unit, which GM claims is the most powerful currently used in the industry. The ECU design embeds all of the necessary electronic circuitry on a four-layer ‘sandwich’ substrate that reduces the size of the control unit. More robust and resistant to vibration than previous ECUs, the new design can be engine mounted. This move frees valuable space in the engine bay and eliminates attachment problems at the assembly plant.
![]() |
The four-cam continuously variable cam phasing system is electronically controlled and hydraulically actuated. The phasers allow intake cam adjustment through 50 degrees of crankshaft rotation and 50 degrees for exhaust-cam adjustment. |
In terms of detail refinements, Jacques says the target was to be class leading. “We went after all the benchmarks,” he says. “You name it — if there is a good V-6 out there, we found out how and why it was good.”
Refinement measures include specially isolated cam covers, which incorporate an isolated gasket around the cover perimeter and radial lip seals at the tubes through which each spark plug is inserted. These components decouple the cam cover from vibration created by the combustion process.
The structural aluminum oil pan is attached by a full-circle mounting that enhances bending stiffness. Specially contrived curves on the major panel surfaces and the sidewalls mitigate ‘drumming’ from the oil pan.
The engine front cover has internal damping plates that quell vibrations caused by the engine. The steel plates, made in two different thicknesses ‘tune’ at differing frequency from the aluminum front cover; the frequency separation dampens noise output.

GM plans to assemble its new V-6 engine family for all global applications at plants in St. Catharines, Ontario, Canada and Port Melbourne, Victoria, Australia.
Beyond the Cadillac CTS, initial North American market applications for the 3.6L V- 6 include Cadillac’s forthcoming mid-sized Rendezvous.
Engine specifications: 2004 3.6L Global V-6 Engine (LY7) | |
Configuration | 3.6L 60-degree DOHC V-6 |
Peak Power (SAE net) | Estimated 255 hp @ 6,500 rpm |
Peak Torque | 250 lb.-ft./339 Nm @ 2,800 rpm; (90% of peak produced from 1,600 rpm to 5,800 rpm) |
Displacement (cc) | 3,564 |
Bore x Stroke | 94 mm x 85.6 mm |
Valvetrain | Dual overhead camshaft 4-valve-per-cylinder Roller-finger followers valvetrain Hydraulic lash adjusters Four-cam continuously variable cam phasing Two-stage roller-chain camshaft drive |
Variable Cam Timing | Intake: 132 degrees ATDC initial timing 50 crankshaft degrees advance authority |
Exhaust | 111 degrees BTDC initial timing 50 crankshaft degrees retard authority |
Compression Ratio | 10.2:1 |
Bore Centers | 103 mm |
Firing Order | 1-2-3-4-5-6 |
Fuel Shutoff | 6,700 rpm |
Engine Idle Speed | 600 rpm |
Fuel System | Sequential port fuel injection (returnless) |
Engine Management | Torque-based; Bosch Motronic ME 9 32-bit micro-hybrid controller |
Intake Manifold | Dual-plenum, equal-length with 2-position variable volume control (resonance tuned) |
Throttle | 68-mm single bore; electronic control (ETC) |
Ignition | Individual coil-on-plug; individual cylinder knock control |
Fuel Requirement | Premium fuel recommended |
Emissions Controls | Dual close-coupled catalytic converters (1.15L ultra-thinwall ceramic) Positive crankcase ventilation (PCV) Intake- and exhaust-cam phasers (EGR) Evaporative emissions system |
Assembly Site | St. Catharines, Ontario, Canada Port Melbourne, Victoria, Australia |
Material Applications Block Material | Aluminum, precision sand-cast 319 with cast-in-place iron liners |
Cylinder Head Material | Aluminum, semi-permanent mold 319 |
Intake Manifold: Upper | Aluminum, sand-cast 319 |
Lower | Aluminum, 356-T6 |
Exhaust Manifold | High-silicon moly cast iron |
Camshaft Covers | Injection compression thermoset composite; vibration isolated |
Front Cover | Diecast 380 aluminum; internal multilayer damping panels |
Crankshaft | Forged steel |
Connecting Rods | Sinterforged steel |
Pistons | Aluminum, polymer-coated skirts, full-floating wristpins |
Main Bearing Caps | 6 bolt caps, copper-infiltrated sintered steel |
Oil Pan | Structural diecast aluminum, steel windage and baffle plates |
Additional features: Pressure-actuated piston-cooling oil jets Extended-life sparkplugs, coolant, accessory belts Cartridge-style, top-access oil filter Oil-level sensor Wide-range oxygen sensors |
More Stories
Buying Car Insurance in Toronto? Don’t Make These Rookie Mistakes
Extend Your Range, Maximize Your Storage with FRDM’s 45 Gallon Combo
How to Install a Ford Bumper Yourself (Step-by-Step Guide)