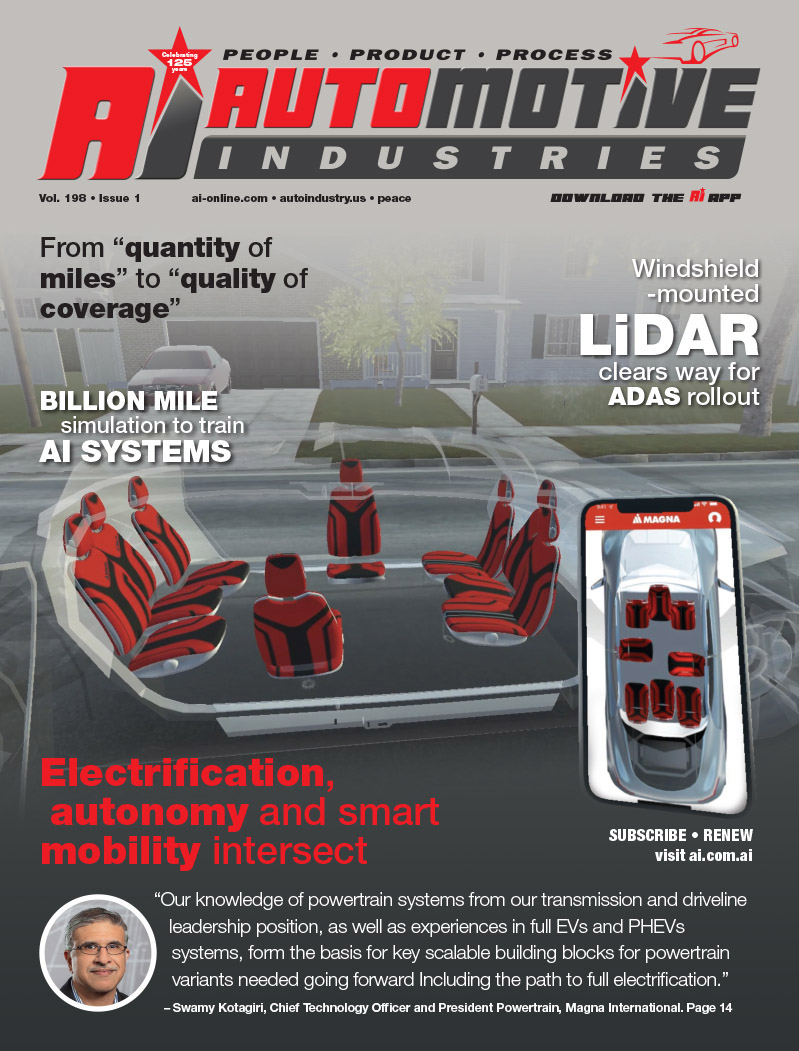
Pierburg targets higher specific output in both diesel and petrol car engines.
![]() |
In KS Kolbenschmidt’s latest diesel pistons a variable-section coolant passage is positioned as near as possible to the first groove and the bowl lip. Improved cooling of up to 50 degrees F at the lip and up to 59 degrees F at the groove is attained, as is improved stress distribution. |
In preparation for further projected rises in component loading, two divisions of German component specialist Kolbenschmidt Pierburg GmbH have recently released details of products targeting the effects higher specific output in both diesel and petrol car engines.
KS Gleitlager GmbH, the division of Kolbenschmidt Pierburg specializing in plain bearings, is responding to the rise in component loading with sputter bearing technology, while piston specialist KS Kolbenschmidt GmbH has developed pistons with a variablesection cooling gallery.
Hitherto reserved by reason of high cost to large high- and medium-speed diesels, increasing loads on main and big end bearings now make sputter technology viable in car diesels, KS Gleitlager reports. Currently cylinder pressures are as high as 2610 psi and 2900 psi is in prospect, imposing extreme loads on bearing material. In the period 1990 to 2005, the loads imposed on diesel engine connecting rod bearings will have risen by 37 percent, and by 33 percent in the case of the crankshaft bearings, KS Gleitlager estimates.
To respond, the St. Leon-Rot-based division has introduced the sputter production process at its Plain Bearings Competence Centre in Papenburg, Germany. In the complex Physical Vapour Deposition (PVD) process, in highvacuum clean-room conditions argon ions are accelerated to extract atoms from a target (coating material) and deposit them on a bearing shell. The ultrafine dispersion of the coating material gives rise to a plain bearing sliding surface with enormous load-bearing capability but only a few thousandths of a millimeter thick, KS Gleitlager reports.
It is absolutely essential that the surfaces to be coated are extremely clean since the slightest contamination can ruin the end result. Thus the plain bearing shell blanks are subjected to a series of cleaning processes: they pass through a normal cleaner; onto a clean room for plasma cleaning; final cleaning in the deposition plant where a number of atom layers are stripped from the shells. The outcome is a metallic surface of extreme cleanliness with high load bearing capacity and excellent tribological properties.
![]() |
Sputter bearing production KS Gleitlager’s Plain Bearings Competence Centre in Papenburg uses the Physical Vapour Deposition process to create sliding surface with high load-bearing capability but only a few thousandths of a millimeter thick. |
Specific outputs of diesel engines are already as high as 67 to 80 hp/L and likely to rise to 80 to 94 hp over the coming years. Temperatures of around 752 degrees F can occur at the lip of the combustion chamber recess and the top ring groove reaches temperatures of over 572 degrees F, with the possibility of the top ring being unable to function effectively due to coke deposits at the groove.
The KS Kolbenschmidt answer is a variable section cooling passage which gives enhanced cooling effect at the bowl lip and the top groove via improved material distribution compared with conventional cooling galleries.
For this purpose, the cooling gallery has been positioned as near as possible to the first groove and the bowl lip. Besides an improved cooling effect of up to 50 degrees F at the lip and up to 59 degrees F at the first groove, this type of cooling gallery also offers a further improvement in stress distribution due to its variable cross-section, the company notes. The outcome is that piston loads remain controllable despite the larger cooling cavities. Moreover, oil flow is accelerated and made more efficient.
Dr. Hartmut Kamp, KS Kolbenschmidt’s head of R&D, Europe, notes that since most engines use inclined cooling nozzles, the point at which the oil spray hits the inside of the piston depends on the stroke position and hence angle of the crankshaft.
“In order to improve the oil flow required for cooling purposes,” he tells us, “ the entry orifice is now elongated, with a deflector placed at the base of the cooling passage so that the oil flow is diverted to achieve a consistent, controlled volume in circumferential direction.
“A particular advantage is that if the oil spray no longer hits the entry orifice due to increasing stroke, it then cools the inside of the piston, directing oil at the piston pin, pin bore, and connecting rod small end. We have thus succeeded in further lowering the temperature in the region of the piston crown.”
More Stories
Essential Features to Look for in ADAS Calibration Systems
Your Guide to Filing a Car Accident Claim
Steps to Take Immediately After a Car Accident