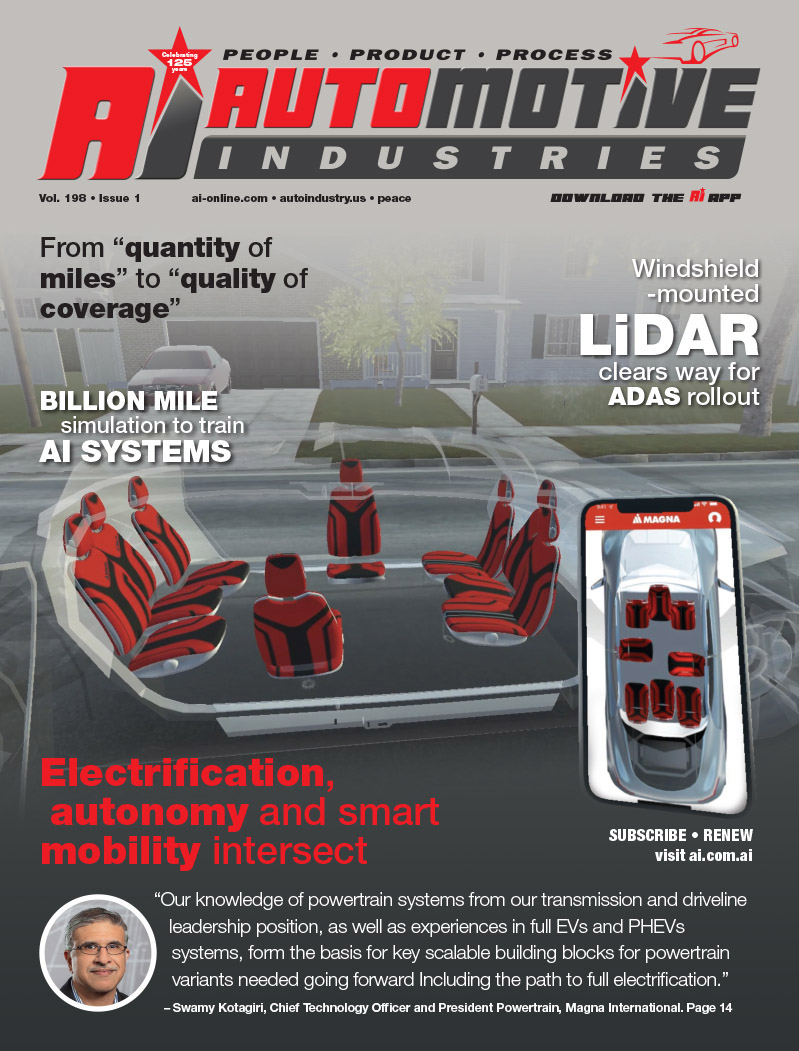
Fueled by the consumer’s love affair with crash test ratings, the auto industry’s on-going, fervent development of safety technologies is a sure thing.In 1947, scattered about the desert sands of Roswell, New Mexico, the U.S. Air Force claimed it had discovered the crushed remains of a flying saucer and the bodies of alien beings.
Practically overnight, every major newspaper west of Chicago carried a cover story detailing the five-foot tall human-like creatures with large heads, big hollow eye sockets, no ears, a small nose, a slit for a mouth and four fingers on each hand. The episode entered UFO folklore as “The Roswell Incident.”
Fifty years later, in 1997, the U.S. military released a report entitled, “Roswell Incident: Case Closed,” which determined — or admitted, depending on how you want to look at it — that the Roswell “aliens” were really anthropomorphic dummies who were simply doing their job: ejecting out of airplanes at high speeds to help a maverick air force colonel named John Paul Stapp determine the maximum speed that pilots could eject from their planes safely. It seems the assumption that the dummies found in the desert were aliens was nothing more than a strange recipe of Cold War paranoia and secret scientific experiments coming to a boil.
Throughout the late 1940s and early 1950s, Stapp had personally volunteered for 26 potentially lethal experiments in his quest for learning how the human body responded to crashes at different speeds and angles. Stapp survived the experiments, but admitted that he had pushed human testing to the limit. If he was to continue his work on improving pilot safety, he needed a substitute.
Stapp teamed up with a man who made artificial limbs for injured soldiers returning from war. The early dummies were very crude, but the air force had a wealth of anthropomorphic data and before long, the dummies were replacing people in Stapp’s myriad of experiments.
The dummies were ejected from planes at high altitudes and parachuted down to earth. One such experiment run amok resulted in a couple of dummies landing in a Roswell drive-in movie theatre — the first of the “alien invasions.” While studying accidents and injuries sustained by air force pilots, Stapp discovered that pilots were hurt more often and more severely in the drive to and from the base than they were hurt in the air. And, of course, the problem wasn’t unique to pilots. All over the United States, more and more motorists were dying on the road. It wasn’t long before Stapp left the desert for the metropolis of Detroit.
Stapp become obsessed with automotive safety. By 1966, Congress passed a series of laws making car crash testing mandatory. Colonel Stapp quietly took his place as the father of automotive safety, and his dummy became the patron saint of the motorist.
It’s a Hard Knock Life
Today’s typical dummy contains 300 engineered parts and can cost up to $300,000 each. “It’s a labor-intensive, low volume business,” says Tom Gutwald, president of the leading dummy manufacturer, First Technology Safety Systems (FTSS) in Plymouth, Mich. FTSS manufactures about 20 to 30 dummies per month, plus a “ton of spare parts.”
The current product line contains a whole family of dummies representing men, women and children of different sizes. THOR-FT is a sophisticated crash test dummy for the 21st century, a complicated representation of the human body and its various flexions, including a multi-directional neck, internal components that mimic the body’s internal organs and even a leg and ankle limb that reflect the load path of the Achilles tendon.
On the flip side, FTSS also offers full mathematical computer simulation versions of most crash tests. These computer simulations allow OEMs to perform simulated crash tests with an accuracy of five percent or better, a full 18 months before the OEM does any hardware development.
“A big, full-crash simulation can take anywhere from 12 to 24 hours to run on the computer,” says Gutwald, “but these simulations save the industry a tremendous amount of money.”
These days, the dummy’s lead role is on the stage of side-impact testing. With the National Highway Transportation Safety Administration (NHTSA) poised to announce an upgrade to its side-impact standard next month, OEMs are aggressively funding dummy research that can yield more refined crash-test data.
According to NHTSA, side-impact collisions kill 10,000 people a year in the U.S. “Side impact is definitely our top priority,” concurs Rae Tyson, NHTSA’s spokesperson. “The new generation of crash test dummies has helped us understand better what’s happening to the human body in a side-impact crash. Over the last several years, the change in our fleet regarding the ratio of light trucks and SUVs to passenger cars has necessitated an improved side-impact standard.”
Tyson says once it’s released, NHTSA’s proposed upgrade will stay out for public comment for 120 days; U.S. automakers will respond and suggest modifications during that time. After that, the new rule will be published within 12 months, while the actual phase-in of the regulation will take several years.
“We never tell auto manufacturers which technology to use,” says Tyson. “We simply give them the performance goal that they must meet. We have to give the OEMs time to figure out how to meet the standard — whether that is through strengthening their structural components, or through airbags, curtains or other safety technologies.”
The good news is that safety suppliers are offering up a smorgasbord of technological options for OEMs to choose from to get the job done.
Side Impact Takes Center Stage
![]() |
The industry has seen an increase in side-impact crash testing in response to an upgraded side impact standard coming from NHTSA. |
![]() |
Autoliv’s Patrick Jarboe feels that as more consumers understand the relation of side impact crashes to head injuries, they’ll demand side curtain airbags. |
“Unfortunately, OEMs tend to only put safety equipment on that helps their vehicles’ ratings, but NHTSA’s five-star crash ratings — the benchmark most well-known to the consumer — only rates chest and pelvic injuries. Head ratings don’t even factor in, let alone injuries to knees, feet and ankles.”
TRW Automotive’s Alain Charlois, director of product planning for occupant safety systems, agrees. “No matter how exciting the technology, you have to pay attention to the economics,” he says. “Sometimes a technology performs and tests beautifully, but is not as cost-effective as it could be and you have to keep working on it.”
Even so, Jarboe believes increasing consumer awareness over the next four to five years will drive greater production vehicle offerings in head protection. In fact, Autoliv is already partnering with the Brain Injury Association of America on a series of public service announcements to bring the issue to the forefront. Jarboe believes it won’t be long before consumers understand that side-impact crashes cause about half of all life-threatening head injuries to drivers and that head injuries are as common in far-side impacts as in near-side impacts.
“Today, a typical consumer asks, ‘Does it have side-impact bags?’ and the salesman will answer, ‘Sure does.’ But in the not too distant future, the educated consumer will ask, ‘Does it have sideimpact with head protection?’ and consumers will expect the answer to be yes,” Jarboe predicts.
Jarboe says the addition of these types of airbag systems into production vehicles will result in an 80 to 90 percent reduction in head injuries. In addition, Autoliv has also developed a companion technology called the 3+2 point seatbelt, which consists of a standard 3- point belt and a supplementary 2-point belt.
According to Jarboe, this advanced seatbelt system is 30 percent more efficient in front crashes than the traditional 3-point belt and virtually eliminates severe side-impact injuries. Autoliv’s testing also shows that a combination of the new seatbelt systems and a side-support airbag system could considerably cut the number of fatalities and severe injuries in far-side impact collisions and roll-overs, because the test dummies remained firmly in the seat with an adequate distance to the vehicle’s side in side-impact crash testing. Typically in such crashes, there is a risk that the occupant’s torso will slip out of a 3-point belt and the head violently hits the inside of the car.
Jarboe says the new seat belt is attached to the top of the seat and crosses the regular 3-point belt. It can only be buckled after the regular belt is buckled. “The biggest challenge to selling this concept to OEMs is that because the belts are attached to the seats, the seat design has to dramatically change,” he explains. “The system requires a much more rigid seat, and such a redesign is very costly to OEMs. We’re working to alert automakers to the tremendous benefit this seatbelt system could provide society.”
Not So Common Sensors
![]() |
TRW’s interior vision system can accurately sense occupant size and position and deliver real-time information for added passenger protection. The Active Control Retractor belts use braking and stability control sensors to pull the passenger into an upright position prior to an impact. |
“For example, the vision system is designed to ‘see’ a rear-facing infant seat on the passenger side and will automatically prevent deployment of the bag,” explains Charlois. “It can also determine if the passenger is a child under six or a smallstature female and prevent or adjust the severity of airbag deployment according to the situation.”
The system uses a tiny, highly accurate stereo camera system mounted in the overhead console facing back into the vehicle cockpit. The lens circumference is roughly the size of a dime and the camera about 1 in. long. A stereo video mode was chosen, because it allows data to be triangulated to pinpoint the position of the occupant. This information determines if the occupant is considered in the “keep out” zone where airbag deployment is prevented.
Charlois says the system is cost-effective, because it does not rely on a proliferation of electronic weight sensors, belt tension sensors and seat position indicators. The camera and complex classification and recognition algorithms are the primary means of occupant sensing and data gathering, and he says it produces a reliable picture of what is really happening inside the vehicle. “These cameras also have some applications that would be classified more under the heading of convenience than safety,” he adds. “For example, some drivers would love to see what’s going on in their back seats.”
Vision sensing technologies are also popping up (literally) in exterior vehicle applications. Autoliv has a night vision system with a 2006 production vehicle contract (Jarboe was skittish when asked if it’s a North American or European customer).
The night vision system uses an infrared camera that significantly improves the driver’s vision at night. It even gives the driver the possibility to see what happens in the dark area between two meeting cars. The distance that the driver can see in front of the vehicle can be extended from less than 100 m with dipped head beams to more than 500 m in ideal conditions.
The system also improves the driver’s vision in fog. The camera detects heat from objects and is calibrated to be especially sensitive to the temperature of humans and animals. The view from the infrared camera is projected on a pop-up display screen in front of the driver, just as in modern jet fighters. The camera is so small that it can be installed under the rear edge of the hood. When in use, it is raised and “looks” above the hood just as a periscope — without interfering with the driver’s vision.
Another Autoliv product employs a nearzone radar sensor that is capable of identifying the relative speed toward an object and the estimated time of impact in just a few tenths of a second before a crash. The regular crash sensor is then put in alert mode.
“For example, the radar sensor could be mounted on the front end of a light truck,” says Jarboe, “and if a crash is imminent, it sends a signal that opens two air release valves on the air suspension system. By venting some air out of the front suspension system, we can lower the front of a truck 4 to 6 in. in about one second, thereby reducing penetration of the front of the truck into a passenger car because the truck would now hit below the passenger car’s sill. If you don’t lower the structure, then the truck or SUV will just blow through half of the vehicle.”
Sensing technologies from the vehicle’s active safety systems are also being used with new seat belt technologies. TRW has introduced an active seat belt system that employs sensors in the Mercedes S-Class as part of the manufacturer’s “Pre-Safe” system. By bringing together active and passive safety system features, TRW’s Active Control Retractor (ACR) belts use braking sensor and stability control sensor information to react to potentially hazardous driving situations in split seconds. If the sensors detect a potential event, the ACR works with a control algorithm that reads the sensor information and controls the retractor.
When the algorithm detects potentially hazardous driving conditions, the ACR immediately reduces the seat belt slack, urging the occupant rearward into a more upright position. In case of a subsequent crash, prepositioning reduces the probability of an “out-of-position” occupant.
What Would They Say?
One would have to guess that if the dummies could talk, they’d say that the automotive industry has grown pretty smart when it comes to safety. The technologies are exciting and the possibilities endless. True, the economics are sometimes scary, but even more frightening would be a world where industry turns a blind eye to the value of saving even one more human life.
“Being part of the automotive safety sector is a feel-good job,” says FTSS’ Gutwald. “We may complain about each other sometimes, but in the end, the suppliers, the OEMs and the government regulators find common ground and get the job done.”
Autoliv Pedestrian Protection System Sees Production in 2006

A sensor system placed in the vehicle’s front bumper sends a signal to two steel bellows, which lift the rear part of the hood. The sensor is so accurate that it can differentiate between a lamp post and a human leg. In addition, Autoliv has further enhanced the system by adding a pair of energy-absorbing airbags, one at each windshield pillar. Autoliv has two product vehicle contracts in Europe for this system.
TRW says it has a similar pedestrian protection hood-lifting system under development at its Occupant Safety technical center in Alfdorf, Germany, where the company has made significant investment in a new crash testing center.
More Stories
Essential Features to Look for in ADAS Calibration Systems
Your Guide to Filing a Car Accident Claim
Steps to Take Immediately After a Car Accident