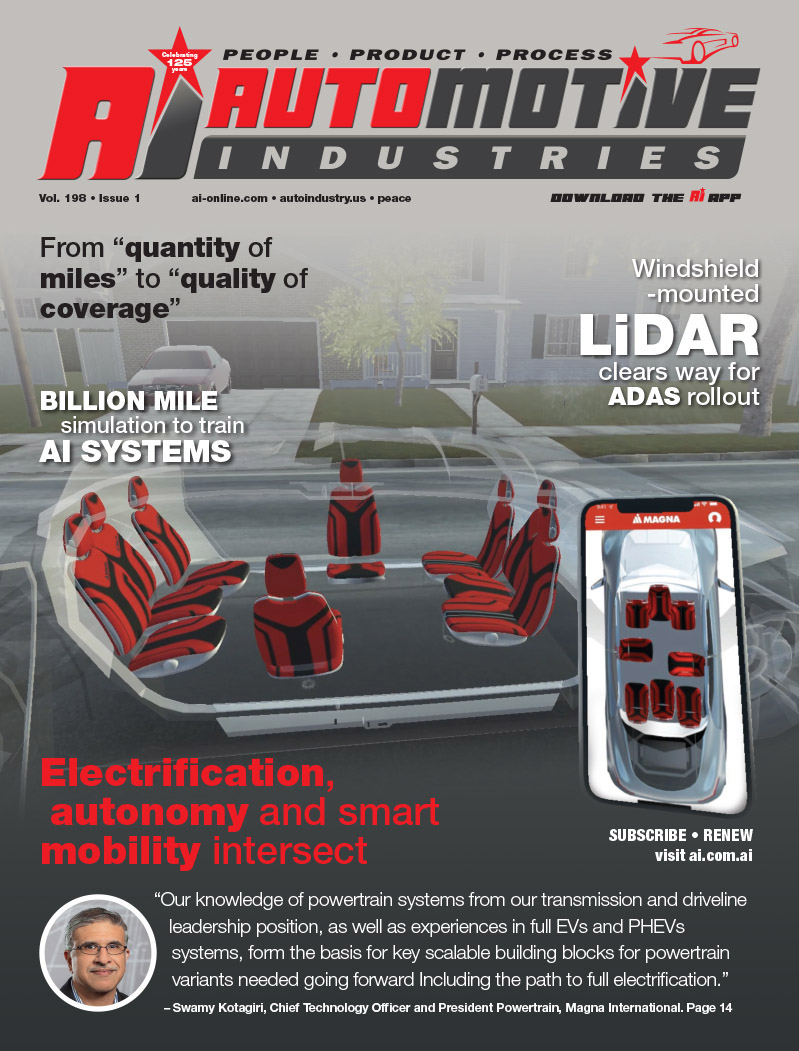
High strength steel lays claim to GM “H” body rear bumper in a costcutting shootout.
![]() |
The 2004 Pontiac Bonneville is one of GM’s “H” body cars to get a high-strength steel bumper that replaces an aluminum bumper. |
The changeover date was February 6, but the exploratory talk started just one year ago between GM and the Cosma International Division of Magna.
We visited with Stuart Brown, GM’s technical integration engineer for bumper systems, Dan Scherle, general manager, Marada Industries, DeWayne Egle, senior account manager energy management for Cosma, Gene Schilling, marketing manager for Cosma, and Jay Mellis, director of product engineering for Marada Industries, a manufacturing unit of Cosma International, to learn more about the program.
![]() |
Cosma International, a division of Magna, made a steel bumper that weighs just 0.8 kg more than the aluminum version. |
“There was one more important element and that was timing,” says GM’s Brown. “How fast can you get the program done?” Speed was important because the “H” body models are scheduled for replacement in eighteen months and that meant amortizing the tooling costs was a major consideration in making the deal pay off.
GM was also interested in making a changeover to the “H” body front end bumper beam as well, but revalidation of the front end for crash worthiness would simply take too much time. Rear bumpers simply weren’t as daunting to revalidate from the timing perspective.
“GM gave the program the green light to proceed in July and it was a done deal by December,” Jay Mellis told us. “We came in only 0.8 kg over existing weight and achieved an average savings per vehicle of $8. The program met all objectives.”
Cosma had to push the envelope for metal forming to get there and can now claim that it is forming the highest strength steel grade ever used for an automotive bumper beam. The material is MartINsite M220, with a minimum tensile strength of 1500 MPa (220,000 psi), a product from Ispat Inland.
Ispat Inland’s family of ultra high-strength martensite steels run from 900 MPa to 1500 MPa, so the M220 is the top grade for strength. The microstructure of the product consists of 100 percent martensite, the strongest steel phase. Not the most formable steel, the MartINsite grades offer much higher strength-to-weight ratios than conventional cold rolled steel and the mechanical properties are uniform in the longitudinal and transverse directions and thus minimize material waste.

And Cosma has produced side intrusion beams from M220, but the geometry is less challenging than the bumper beams. The beams are gradually roll formed through 18 stands (sets of rollers) from flat coil into a “U” section with an inward return on each leg of the “U.” Gradual shaping the steel through so many stands overcomes the high spring back properties found in such a high-strength steel. Mellis says that proper lubrication during forming is a key to success and also to minimizing the wear on tooling.
In two final stations the bumper is bowed into what Mellis refers to as a 38 sweep. (The higher the number, the smaller the radius of the sweep or bow and the Explorer bumper has a 50 sweep.) Integral with the process, beam sections are cut off hydraulically. Small bulkhead members are welded into the “U” section throughout its length as stiffeners and reinforcements, and at each end of the beam there is a bracket assembly with a mounting plate. These components are all attached by conventional welding.
The mounting brackets vary in length, depending on which “H” body model happens to be the destination. Brackets are fabricated in an 80,000 psi yield strength steel and the mounting plates in 50,000 psi steel.
Because the ultra high-strength is inherent in the M220 material as delivered, no subsequent heat treating is required. The Maranda Industries plant in Westminster, Md., produces this complete assembly and E coats it before shipment.
According to Mellis, the M190 was their early pick for the job, but through modeling and prototyping it just seemed impossible to meet the structural integrity and weight objectives established for the program. Thus Cosma chose to down gage the beam section, but step up in yield strength to the M220.
As a handy comparison, consider that the Explorer front bumper material is 1.8 mm in thickness. The final “H” body bumper material is 1.55 mm in thickness. What seems so small (0.25 mm), actually results in a 14 percent savings in weight inch for inch.
So where do we go from here? Nothing is certain, but Cosma is at least aboard the current “H” body replacement development programs as one of the options for both the front and rear bumpers. The timing issue doesn’t loom as large as an obstacle since the development schedule is more normal and that puts the front bumper squarely in play.
Low- and high-speed computer modeling is currently being conducted to validate crash performance. The M220 experience with the “H” body bumper changeover program is an important new arrow in Cosma’s quiver. Cosma also has the opportunity to keep cost down for the replacement programs if the geometry of the new bumpers allows them to reuse tooling from the current program. As much as 80 percent of tooling costs could carry forward, the company estimates.
It’s been a battle royal in materials substitution for the last 25 years and the tempo increases with the march of time. In this encounter, steel demonstrates again that it can strap it on and move to yet another higher level of application performance. Steel wants its bumpers back!
More Stories
What You Need to Know About Tire Pressure in Winter vs Summer
Essential Features to Look for in ADAS Calibration Systems
Your Guide to Filing a Car Accident Claim