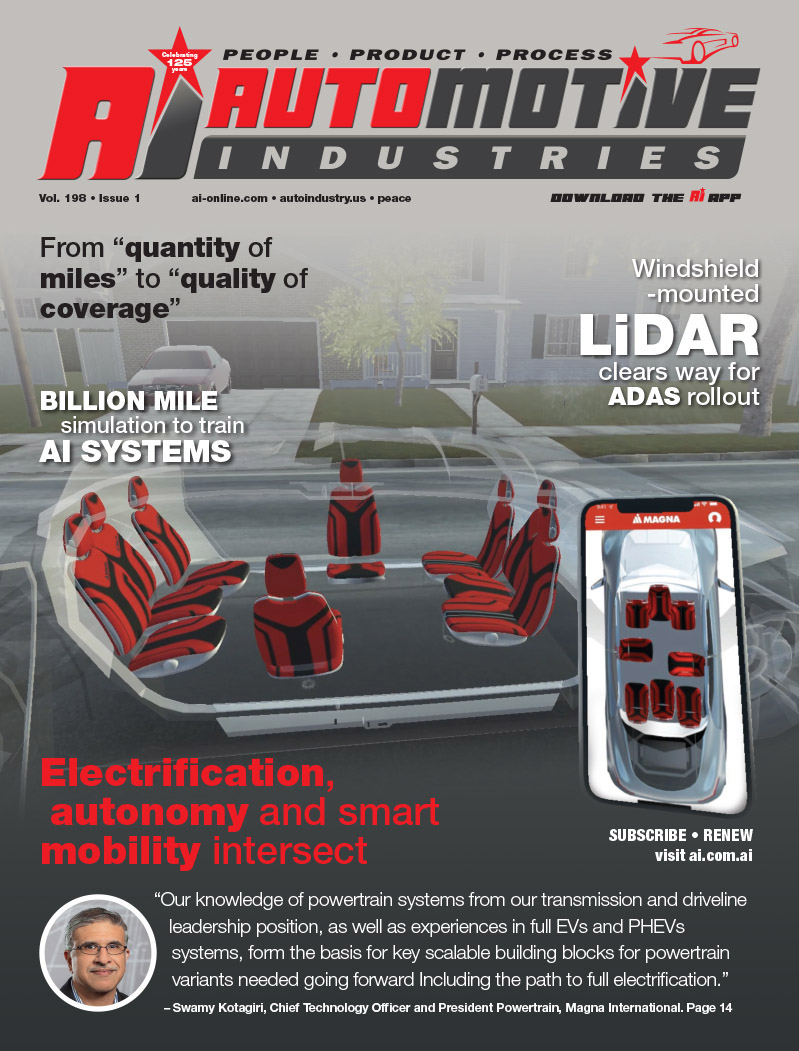
Originally penned in 1999, and then rewritten in 2002, TS 16949 has really started to pick up steam. The new standard takes a more holistic look at a company’s business to assess the quality system. While the actual product quality is part of the equation, TS 16949 also analyzes the management processes, shipping, customer satisfaction and a number of other metrics for continual improvement.
“The development of a quality management system that provides for continual improvement, emphasizing defect prevention and the reducing of variation and waste in the supply chain. This technical specification in conjunction with applicable customer specific requirements for quality systems defines the fundamental quality management system for those subscribing to this document,” this is the published goal for the new standard from the TS guide.
To further get to the essence of this new standard we talked to a certifier and companies that had undergone audits to see what they thought.
The Certifier
Bob Kozak, Technical Specialist/Lead Auditor for DNV, spent some time explaining the history of the new standard as well as outlining what it entails.
This second edition of ISO/TS 16949 replaces ISO/TS 16949:1999. The first edition contained ISO 9001:1994 in its entirety, while the second edition of TS 16949 contains ISO 9001:2000 which promotes the adoption of a process approach when developing, implementing and improving the effectiveness of a quality system, to enhance customer satisfaction by meeting customer requirements. This approach emphasizes understanding and meeting requirements, the need to consider processes in terms of value, obtaining results of process performance and continual improvement of processes based on objective measurement.
Some of the framers responsible for the contents of the standard were the International Automotive Taskforce and the Japan Automobile Manufactures Inc. with support from the ISO/TC (technical committee) 176. “One of the big challenges in the automotive industry in North America is low cost. It’s also a challenge to all manufacturers to not only stay profitable but to maintain their quality levels, ramping up quality, meeting consumer expectations to do well in J. D. Power surveys and so forth — All the while trying to cut cost. And that’s where the continual improvement cycle comes in. Companies will need to master improvement not just in the quality of the product but rather all the processes in the company to add the entire value stream of the company,” Kozak explained.
“If you want to do business in the automotive industry, as a supplier, TS 16949 is a requirement that GM, Ford and Chrysler have deadlines requiring compliance. Chrysler has the tightest deadline on TS 16949, which is July of 2004 for its 1st tier suppliers.”
With the deadlines on the horizon, companies have already begun the process and in some cases received the accreditation. Steps included in the process are as follows:
1. Readiness Review — Customer score cards are analyzed. High enough scores allow companies to start the process. In the case of the customer score cards being substandard they cannot even qualify to undergo the audit. In addition to customer score cards, a complete cycle of internal audit management reviews, a list of trained auditors, a list of customers, customer specific requirements, a list of corrective actions taken in the case of customer complaints and operational performance trends for the past 12 months must be submitted.
2. Quality Manual review — makes sure that companies adhere to all the requirements set forth in ISO TS 16949 that they have designed for themselves (including a process model of the quality system).
3. Audit plan — the lead auditor and experts from that industry segment with product commodity experience identify all the processes within the company and make sure that each process is analyzed. Risk to customer is analyzed, including customer satisfaction performance metrics to guide the on-site audit focus. High PPM’s, late delivery trends, spills, recalls, and safety related parts all constitute “risk” to the customer. The auditors are meant to represent the customers (OEMs) and consumers in all quality systems audits.
4. Test the control on each process — Whether it’s manufacturing or shipping, the checks and balances for each process are tested.
After giving the background info on TS 16949, Kozak also went on to illustrate a few things he felt were important about the new standard, “A big part of this TS 16949 is the inclusion and focus on the customer specific quality system requirements.”
He also pointed out that the International Automotive Oversight Bureau (IAOB), which police (accredits) the certification bodies, has reduced the number of certifiers from over 100 down to approximately 50 worldwide.
Something else brought to light about the very nature of the new standard is the trickledown effect. Within the TS also comes the inherent mandate that 1st tier suppliers are essentially passing along directives from TS 16949 to their sub suppliers.
Supplier quality system development requires third party registration to ISO 9001:2000 by an accredited third party certification body and a goal of conformity with ISO/TS 16949. ISO/TS 16949 certification isn’t necessarily needed but the idea is that the 2nd/3rd tier suppliers are being made to follow suit and do business in a similar fashion.
The new standard is aimed at a process approach geared directly at specific companies’ processes rather than changing a business to suit a guideline that may not make sense for the specifics of that business. It also, by its nature, should help reduce the need for multiple audits.
The Auditor Gets Audited
While all the new mandates and directives within the TS 16949 can be daunting to some companies, there’s no substitute for experience. In the case of Dupont, possessing experience in this realm came through in spades.
Dupont’s point man for TS 16949 accreditation was Joseph Debiaso. Joe is a certified Registrar Accreditation Board Quality Management Systems Lead Auditor (RAB QMS LA QO4446) certified since March 9, 1995. Furthermore, he’s a certified Registrar Accreditation Board International Auditor and Training Certification Association Senior Auditor (RAB IATCA QMS Senior Auditor QIO-4446), certified since February 15, 1999 and a certified trainer and coach for Plexus ISO- 9001: 2000 and ISO/TS-16949: 2002 courses.
His litany of experience in TS/ISO/QS auditing greatly helped Dupont prepare for its audit. He did a pre-assessment before the 3rd party auditors came in to actually allow for the certification. The certifiers employed by Dupont were LRQA and Underwriters Laboratory.
“Before the auditors get there they review a whole bunch of documents. When they show up they do a complete analysis of your processes and all of the parts of your quality systems. I think the 3rd party audits are much more intense and in depth than certifications past. “The more difficult parts involve getting the whole organization used to this whole process approach, giving them an idea of what’s going to take place during these audits and realizing that they may have different findings than in audits past,” explained Debiaso.
“When we looked at the differences between the two standards we identified certain hot spots that might be problematic in regard to the new metrics for quality. The differences seem subtle but I think they are fairly significant. You have to make sure you have a well defined plan and that you’ve looked at all the areas of your business.”
Dupont passed a multi-sight registration and is now operating with TS 16949.
The New Guys
Nearly the polar opposite of the Dupont story was that of Lubrication Technology’s (LTI) experience with TS 16949. Unlike Dupont it didn’t have a certified registrar in house nor did it have a former ISO/QS accreditation on its wall.
“A big automotive customer asked that we get QS certification. When we saw that TS 16949 was going to be the next big thing we decided to go that way. We then called in a consulting firm to get our initial documentation in place to help get us ready,” Shane Nunley told us. Shane Nunley is the Supply Chain Manager at LTI and also became the management representative for quality systems by virtue of TS 16949 decree.
So it began.
“It’s difficult but with any new system you’re going to find that. I believe it’s been very useful in helping companies, like ours, in looking deeper into our processes and approaching all our processes with the standard in mind. It forces your to look at your process.
“The only problem I see with the process itself is that it seems to be written for parts. We make batches of grease so the FEMA and parts per million numbers are harder to apply. Most automotive suppliers are providing a part and what we make goes into those parts which complicated things,” says Nunley.
LTI contracted BSI as its certifier and underwent a two day audit because LTI is also designresponsible so the design facet of its business was also analyzed.
LTI didn’t receive TS 16949, on a technicality. It didn’t have the 12 months of data required, but passed on the other segments of the audit. It is currently operating under a letter of compliance which states that it has meet all the standards of TS 16949 with the exception of the required data dating back one year. A registration audit for LTI is scheduled for September of this year, at which time it expects to receive full accreditation.
The Holistic Approach
As the old standards no longer make as much sense as they once did and the new ones come in — TS 16949 distinguishes itself not only by being a newer standard but one with a different outlook on accreditation. By taking a look at how each process feeds the next in a company it is, as Shane Nunley says, forced to look more deeply at all its own processes.
So not only does the company undergoing a registration audit have the upside of having a shiny new quality standard to show its customers and use to lure new ones — but it also has a vested reason to take a second look at how it has planned its business.
While time and then ever-changing automotive industry will surely give way to new directives and quality control obbligatos, this current incarnation is latent with common sense and like the all important J. D. Power surveys has quality at heart.
More Stories
Essential Features to Look for in ADAS Calibration Systems
Your Guide to Filing a Car Accident Claim
Steps to Take Immediately After a Car Accident