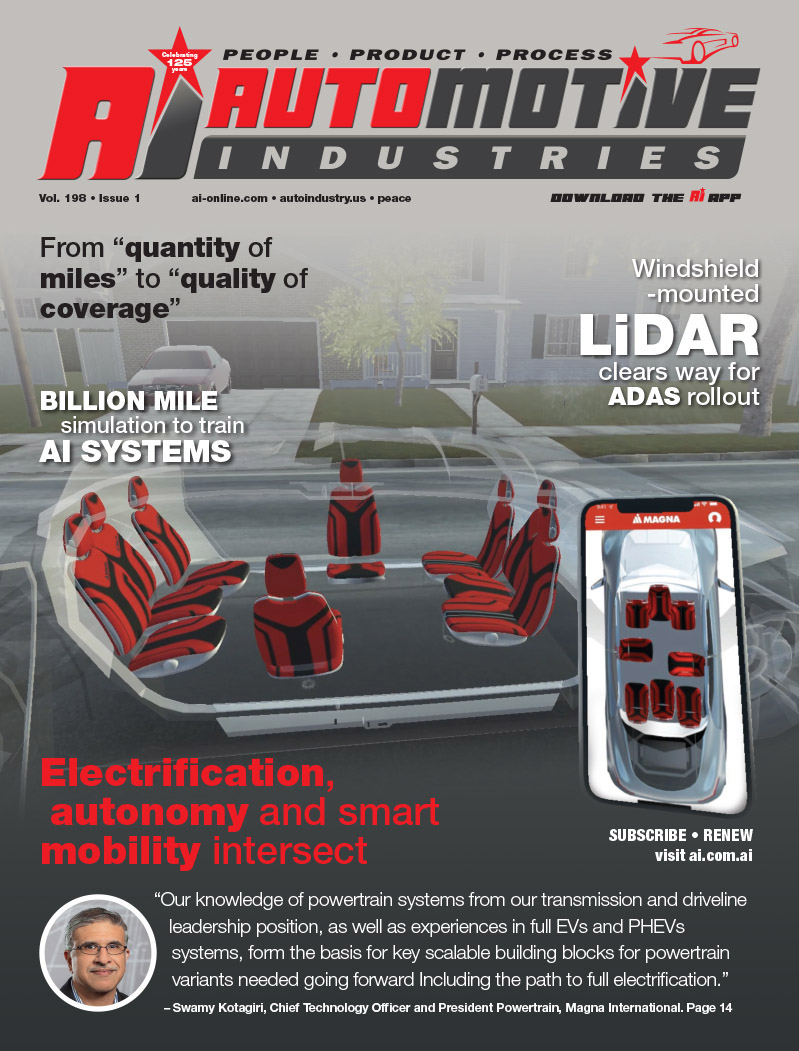
Ford’s fuel cell fleet takes shape.
Traditionally, ultra-low volume vehicles costing hundreds of thousands of dollars are the preserve of Italian or German exotic sports car manufacturers. But a series of 30 cars being completed in a nondescript Detroit warehouse this month defies that notion.
![]() |
A Focus FCV comes together at MSX’s Detroit facility (above). Components for the other 29 copies wait patiently in the warehouse (below). |
![]() |
At the MSX facility in east Detroit, which previously assembled the electric Ranger for Ford, the Focus FCVs are coming together in a station build process, surrounded by a warehouse of specialty components. The process starts with a body delivered from Ford’s Wayne assembly plant. Heavily modified, to accommodate the underbody mounted 85kW fuel cell stack and system module, the Focus body features high strength steel to meet crash requirements, as well as aluminum outer panels and a carbon fiber decklid.
The extensive use of lightweight components, which also includes titanium springs (a feature shared with Ferrari) and forged aluminum suspension arms, is all in the cause of offsetting the extra mass of the fuel cell powertrain. Even with the lighter parts, the 3,527 lb. Focus FCV still comes in 882 lb. heavier than a production Focus.
The FCV program, led by chief engineer Mark Mehall, worked closely with Wayne assembly to simplify the process wherever possible. “Wayne helped us to get all the new technology through their plant, using their framing fixtures,” says Mehall. “For example, it is the first time they put stainless steel panels through the stamping plant. We used novel approaches to make aluminum parts off production tools, so it’s been a joint effort with manufacturing and engineering to bring this project home.” The choice of the Focus for the FCV project was driven in part by the fact that the platform was being developed as a pure electric car.
![]() |
The FCV uses exotic lightweight materials like a carbon fiber decklid. |
As it happens, the Focus FCV does use a battery, although a much smaller one than that in a pure electric vehicle. The car is designed as a hybrid and utilizes a Sanyo-supplied battery pack that provides extra boost when taking off from the rest or accelerating. The battery pack and associated regenerative braking system (supplied by Continental Teves) are derived from Ford’s Hybrid Escape production sport utility vehicle. However, while the Escape is a full hybrid, the Focus FCV is designed as a mild hybrid, meaning that the battery pack cannot drive the vehicle by itself.
On the MSX “assembly” line the Sanyo battery pack is installed behind the rear seat near to the end of the process. Prior to that, many of the 400 unique components (about one quarter of the total parts count of a Focus) are fitted, including the front and rear cradles, electric motor, suspension, cooling loops, electrical pumps and fans, radiators, DC/DC converters, controllers and wiring. Most of the critical plumbing and high voltage wiring is colored orange to warn rescue crews in case of an accident. The trunk space is largely taken up with a Dynatech 5,000 psi tank, which holds 4 kg of compressed hydrogen.
![]() |
Subassembled axles wait their turn in a hold area. |
Among the final assembly procedures for the MSX workforce, which numbers 30 in all, is the insertion of the Ballard 902 stack and system module unit. This large rectangular module is loaded from underneath the vehicle and its wiring and plumbing fixtures are connected to the car. Although the stack itself is free of moving parts, an examination of the mechanicals of a near-complete Focus FCV reveals a very complex machine. And this complexity is part of the challenge facing not just Ford, argues Mehall, but all the auto makers engaged in fuel cell vehicle development.
“We are looking downstream,” says Mehall. “We’re going to get cost out by simplifying the system, by making it more robust and making it run in a stable way. These are all new technologies. We’re trying to accomplish in three or four years what took 100 years to refine with today’s vehicles.
“It’s not too different from the technology we had to develop for exhaust emissions; initially these were very rich in platinum but we learned how to use palladium and we learned how to use multi-stage catalysts. That type of evolution has not really been accomplished with fuel cell technology yet.”
![]() |
Engineers install the power module. |
Aside from cooling, the main challenges include reducing system complexity, hydrogen storage methods and establishing a fuelling infrastructure. “Our target is to achieve parity with today’s internal combustion engine,” says Mehall. “Because that’s the only way the public will accept this technology.”
Ford continues to work on fuel cell technologies in parallel with DaimlerChrysler, its partner in Ballard Power Systems. A recent realignment of that partnership, which involved $110 million investment by Ford, will result in Ballard focusing more tightly on the fuel cell stack development, its core competency, and leaving the system integration to Ford and DaimlerChrysler. “We have a single set of parameters with DaimlerChrysler for Ballard, but beyond that the vehicles we develop are our own responsibility,” says Mehall. “However, we have helped DaimlerChrysler with some of our hybrid knowledge as needed and we may work together on hydrogen storage as we both use Dynatech.”
![]() |
The fuel cell stack is bolted to the front subframe and connected to the front axles. |
Meanwhile, Ford’s Focus FCVs should soon be making their way into fleet use. The program involves BP, which is establishing a network of hydrogen fueling stations to support the fleet. For both Ford and BP, the motivation for the program came from the U.S. Department of Energy’s Controlled Hydrogen Fleet and Infrastructure Demonstration and Validation Project.
BP says its network of stations will demonstrate the latest hydrogen fueling technologies. Some stations will evaluate technologies that have near-term commercial feasibility, such as reformation of natural gas, while others will explore more long-term technology options and assess the potential to produce renewable-based hydrogen that achieve U.S. DOE hydrogen fuel cost targets. Ford’s plans for its California Focus fleet include three organizations in Sacramento. Service and maintenance of the vehicles will be provided at the existing California Fuel Cell Partnership facility. The California Air Resources Board, California Energy Commission and Department of General Services are working together to operate the FCVs to gain fuel cell operating experience and to promote hydrogen-powered vehicles through education and outreach activities.
![]() |
Chief Engineer Mark Mehall points to the underside of the Focus unibody which has been greatly modified to accept the power module. |
In Florida up to 10 FCVs will be deployed in the Orlando area across three fleets. BP is examining several sites in the north Orlando area to locate a fueling site central to the three proposed fleet users. BP is also examining several hydrogen production methods for the Orlando location. The Progress Energy Longwood facility, located in Longwood, Fla., will be used for service and maintenance of that state’s FCV fleet.
In Michigan Ford plans to place up to 10 FCVs with the city of Taylor and with the University of Michigan. BP is considering several sites for refueling infrastructure, including the Wayne County Metropolitan Airport and the EPA vehicle test laboratory in Ann Arbor. The vehicles in southeast Michigan will be serviced at Ford’s existing fuel cell development facility (its Sustainable Mobility Transportation Lab).
The University of Michigan plans to use the vehicles to support administrative services on campus. In addition, the Colleges of Engineering, Natural Sciences and the Business School are all planning to integrate the vehicles into their advanced courses.
“By testing fuel cell vehicles in everyday conditions and applications, Ford is moving the industry toward commercialization,” says Mary Ann Wright, director of Sustainable Mobility Technologies and Hybrid Programs, the group at Ford responsible for research and development of fuel cell products. “Projects like these will provide the data we need to engineer improved performance, reliability and durability of fuel cell vehicles, and prepare the market for wide spread commercialization.”
More Stories
Best Wheel Size for Off-Road Adventures: What People Get Wrong
Trusted Auto Collision Repair That Restores Both Performance and Peace of Mind
What You Need to Know About Tire Pressure in Winter vs Summer