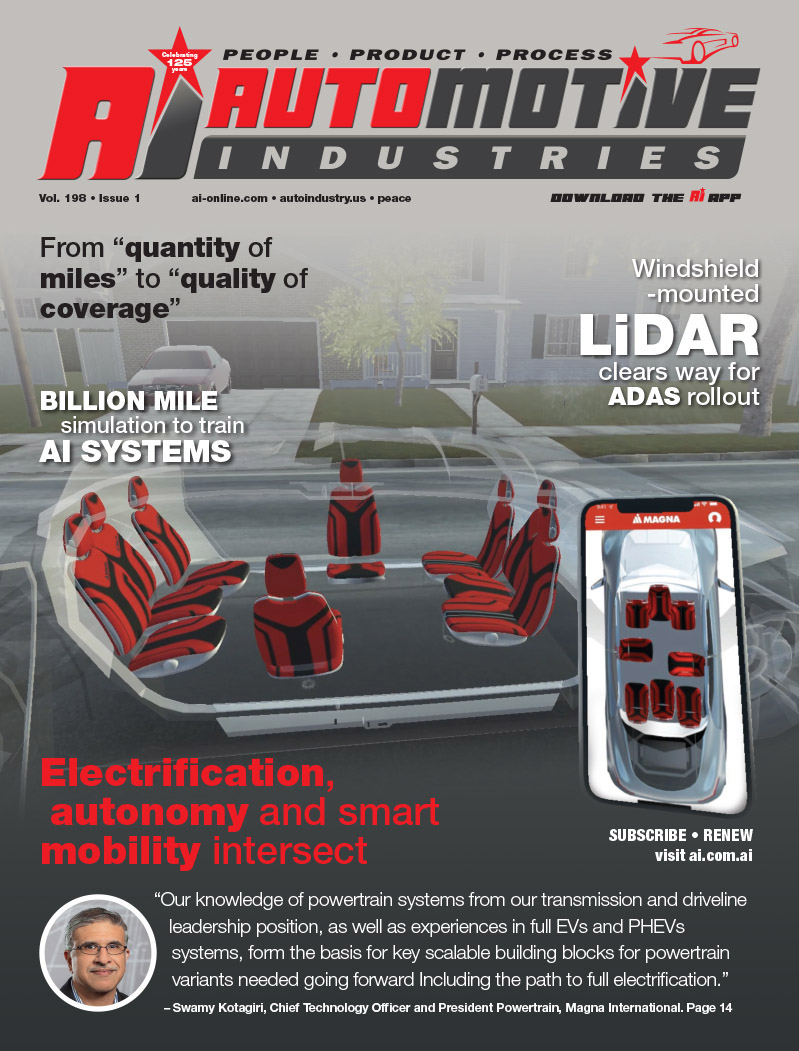
The hottest thing in seating today is functionality. Consumers might buy an SUV or minivan because they want the cargo space, but the truth is, they don’t want it all the time – they just want it, when they want it. The rest of the time, that SUV or minivan needs to be very comfortable (not just the first row seats), very safe and it’s got to look good, too.
Enter the latest buzzword in seating design: reconfigurability. “Reconfigurability is about creating a wide-open environment in the vehicle interior,” says John Gorton, group vice president and general manager, engineering, for the Automotive Group of Johnson Controls (JCI). “We’re leaving behind the concept of removing seats to provide that capability, and instead, developing seats that remain in the vehicle but become unobtrusive when not in the seating position.”
“Vehicle interiors are becoming more flexible to accommodate that spontaneous reconfigurability that consumers are looking for,” says Randy Koenigsknecht, vice president, sales and marketing, Intier Automotive seating division.
“Reconfigurability is on the top of the list with all our customers,” says Don Bernhardt, vice president, engineering, for Lear Corp.’s Seating Systems Division. “The question is, how many ways can we help the consumer reconfigure their vehicle interior to meet their needs?”
Actually, seating manufacturers have been studying the concept of stowing seats for a number of years. “We’ve come up with seats that stow to the ceiling, to the tailgate, to the floor and to the side of the vehicle,” says Koenigsknecht. “We needed an OEM willing to take the steps to meet the challenges in their body structure. Chrysler Group stepped up and was able to do that.” Intier’s fold-in-floor seating, marketed as Stow ’n Go in the 2005 Chrysler and Dodge minivans, feature second- and third-row seats that fold completely into the floor and disappear with an easy, one-hand operation. The second-row seats fold flat and disappear into a well to achieve a flat load floor, made possible by innovative mechanisms used to stow the seats into the floor. The comfort of the second row was maintained using translating armrests and super high-density foam.
The armrests pivot inward for storage and outward when the seats are upright, and the super high-density foam achieves a minimal stack height and allows for thinner, lighter cushions without sacrificing comfort.
In the third row, a 60/40 split bench seat pivots and folds into a storage well via onehand stowing operation that requires no effort greater than 20 pounds, thereby meeting the “5th percentile female” guideline for easy stowing and unstowing of the seats. Each section can be actuated individually to provide maximum versatility for various cargo/passenger arrangements. In total, the complete seating system offers up to 256 different seating configurations. Intier says it was its most challenging seat program to date, moving from award of business to production in 15 months.
JCI’s fold-flat product is called Open Seating. Debuted at the North American International Auto Show in Detroit this year, the product offers the comfort and styling of front-row seats for rear compartments. When stowed away, it has a much smaller footprint, enhancing a vehicle’s cargo capacity. When deployed, the seating product features side bolsters that provide comfort similar to the front row and fold completely flat when the seat is stowed. When stowed, the seat is just 135 millimeters thick. The product is available for integration into 2007 model-year vehicles.
![]() |
The Johnson Controls Leap automotive seat system redefines traditional seat architecture and features in key areas, including an anthropometric pivot for optimized comfort and Steelcase’s Live Back and Natural Glide systems. |
The technology can be included on all vehicle segments, and all rows with folding seat backs. It also enables a vehicle’s styling theme and trim outline to be carried from the front row to the second- and third-row areas.
“The underlying mechanisms that provide this functionality are critical,” says JCI’s Gorton. “The consumer doesn’t see or feel the mechanism, but they experience a seat that is comfortable. It also allows the OEM to keep a consistent theme throughout the vehicle because they don’t have to settle for flat seats, which is the typical trade-off when you try to incorporate some of this functionality.
“All the seating design challenges emerging today require a good, solid foundation in mechanisms,” he says. Intier’s Koenigsknecht says the future will bring what he calls “refined extreme reconfigurability,” which will require even more mechanisms added to seats. “You will see seats that become very thin and low profile as you reconfigure them into a cargo mode, but then ‘bloom’ into a seat that is no longer thin but has bolsters and a comfortable appearance when in the seating mode.”
Of course, all these additional mechanisms and flexibility in seating bring up the question of safety. When the reconfigurable seat is in the seating position, will it stay locked there – even in a collision? “As you have more reconfigurability in seating, the mechanisms are crucial because you want the seats to move smoothly and easily, but you also want them to have a solid perceived, and actual, safety. When the seat is locked in a seating position, the occupants must be confident that the mechanisms don’t move and don’t vibrate,” says Koenigsknecht.
Seats and Safety
Automotive seating has become a big supporter of safety features. “We have airbags deploying out of the seat for side impact protection and increased regulations coming down the pike on head restraints to prevent neck injuries,” says Koenigsknecht. “The question becomes, what complications do new safety requirements bring forward into seating design?”
For one, Koenigsknecht says headrests will become larger, which introduces a visibility issue for the driver. Trying to stay ahead of the game, Intier has developed a head restraint with mesh technology that allows greater visibility in the vehicle but meets all new safety requirements. Another option is to design headrests that disappear when not needed. “New regulations will bring higher headrests and an increase in the number of positions the headrest must move to, for all seats in the vehicle,” says JCI’s Gorton. “Yet, visibility and clear line of sight specifications require us to develop technologies for the headrest to fold away when not needed. It gets back to why seating suppliers continue to make huge investments in mechanisms.”
Gorton says a final ruling on new U.S. headrest regulations is expected in the fall of 2005. The good news is that the regulations are expected to create more harmonization between U.S. and European safety requirements. “Rear impact is a real hot-button issue for us now,” says Gerry Locke, Lear’s director of safety engineering (Central Engineering) for the Seating Systems Division, “and one of the biggest challenges is in perceived comfort. New head restraints are going to be mandated closer to the occupant’s head, and U.S. consumers are likely to find that less comfortable than what they’re used to.”
Locke says Lear is addressing that concern with a new development to its active head restraint system. “The new design provides a little larger gap between the occupant’s head and the headrest and still exceeds the proposed federal requirement,” he says. In addition to meeting the regulation, OEMs can maintain their styling and comfort needs. “We could put this technology into production in a couple of years, but we won’t proceed until the final regulation comes out and we know what we have to meet.”
A more immediate seating safety challenge, says John Nathan, director, electrical, for Lear’s Seating Systems Division, comes from the new federal FMVSS 208 regulation, which mandates “smart sensing” in the passenger seat and helps the airbag know when or if to deploy and at what force, based on the passenger’s size and position at the moment of impact. Nathan says Lear introduced its OccuSense technology at an Asian road show to address these new regulations, which began going into effect June of this year.
Get in There Early
The seating suppliers agree that the key to implementing a truly revolutionary seating system into a program is early involvement. “To achieve optimization of innovations, suppliers have to be involved earlier,” says Intier’s Koenigsknecht. “For example, to achieve optimum load paths and safety with reconfigurable seats, you have to interface closely with the body structure where those loads are going to be transferred.”
Having seating suppliers involved earlier in the vehicle concept process also helps decrease development time. “All the OEMs are focusing on how to get products to market quicker,” says JCI’s Gorton. “Three to five year vehicle development cycles are history – about 15 months is now state-of-the art.
It’s up to the suppliers to be proactive and make sure they are involved earlier.” “We’re pretty aggressive in presenting our innovations to the customer,” says Lear’s Bernhardt. “We have a display area in Southfield that shows our latest ideas and technologies, and we update our customers once a week.”
![]() |
Lear’s Flexible Seat Architecture cuts lead-time by using inproduction parts and technologies. |
LFSA features a modular/flexible seat structure to accommodate various vehicle architecture and comfort needs. The system meets or exceeds all OEM global seat performance requirements and allows OEMs a fast-to-market response with the latest safety technology available. Lead time and investment is reduced because the system uses inproduction components and technology. It also helps simplify the manufacturing process with standard assembly characteristics. “Basically, we’re using common components to meet different customer-specific needs,” Wagner explains. “It’s like a menu of various features to choose from that are already tooled and pre-validated. We can build a custom seat very quickly that way.” LFSA is being incorporated in several seat systems across several OEMs starting in 2005.
JCI’s solution is called its Core Product Portfolio (CPP). “A common, but highly flexible automotive seat structure allows us to provide standardization without losing the functionality that the OEM is looking for,” says Gorton. The seating uses standard metal interface areas that remain constant, while allowing other areas to be modified for different vehicle platforms. Products slated for production in 2004 have been sold to several automakers, he says. “We can also provide carry-over part numbers, and if the functionality doesn’t exist on a carry-over, we have an efficient methodology that uses the standard component’s interfaces to deliver new functionality without the architecture. By creating a master plan design with a standardized architecture, CPP allows add-on features and midcycle enhancements to be integrated throughout a product’s life cycle.”
Fostering Innovation
The honest truth is that many of today’s seating innovations are generated on the supply side. As a result, seating suppliers have specific ways to boost the creativity and innovation at their companies that is so key to winning future OEM business.
“We have a flat organizational structure which allows everyone to bring their ideas to the table,” says Will Harney, chief of Intier’s seating R&D. “Fostering innovation is an ingrained part of our heritage, and the key to our success so far has been the ability to accelerate the process in getting a new idea ready for market.”
Similar opportunities exist at Lear. “The person on the plant floor has avenues to bring innovations to the attention of the people at Lear who could do something with it,” says Lear’s Bernhardt.
Gorton says JCI has been willing to go out on a limb for very unusual ideas, and a good example of that is its Leap automotive seat technology. Based on a collaboration with Steelcase office furniture manufacturer, the technology was borrowed from Steelcase’s Leap high-performance office chair. The Leap system’s Live Back technology changes shape to move the way one’s upper and lower spine want and need to move; while a traditional seat back requires the individual to adjust it, the Live Back system contours to the individual. This is coupled with The Natural Glide system, which allows the individuals to change postures without affecting their reach or visual orientation and allows a more fluid natural motion as the seat bottom glides forward when the seat back reclines. Gorton says the Leap automotive seat has been debuted to customers, but is not in production yet.
In considering the importance of innovation, the suppliers reflected on the climate of today’s seating industry. “Increased functionality is cascading all through the vehicle,” Gorton says. “It’s all about facilitating multi-use of the vehicle’s interior environment and meeting the demand in a very competitive marketplace.”
“Without a doubt, a seating manufacturer’s success will depend on its ability to reconfigure seats combined with a process that delivers craftsmanship and the agility to deliver the product quickly,” agrees Intier’s Koenigsknecht.
“There’s this continuous push to bring functionality to the customer, along with stronger and stronger architectures that lead to a safer environment,” says Lear’s Wagner. “The biggest challenge for a seating supplier is to remain on that curve of continuing change and improvement.”
More Stories
Best Wheel Size for Off-Road Adventures: What People Get Wrong
Trusted Auto Collision Repair That Restores Both Performance and Peace of Mind
What You Need to Know About Tire Pressure in Winter vs Summer