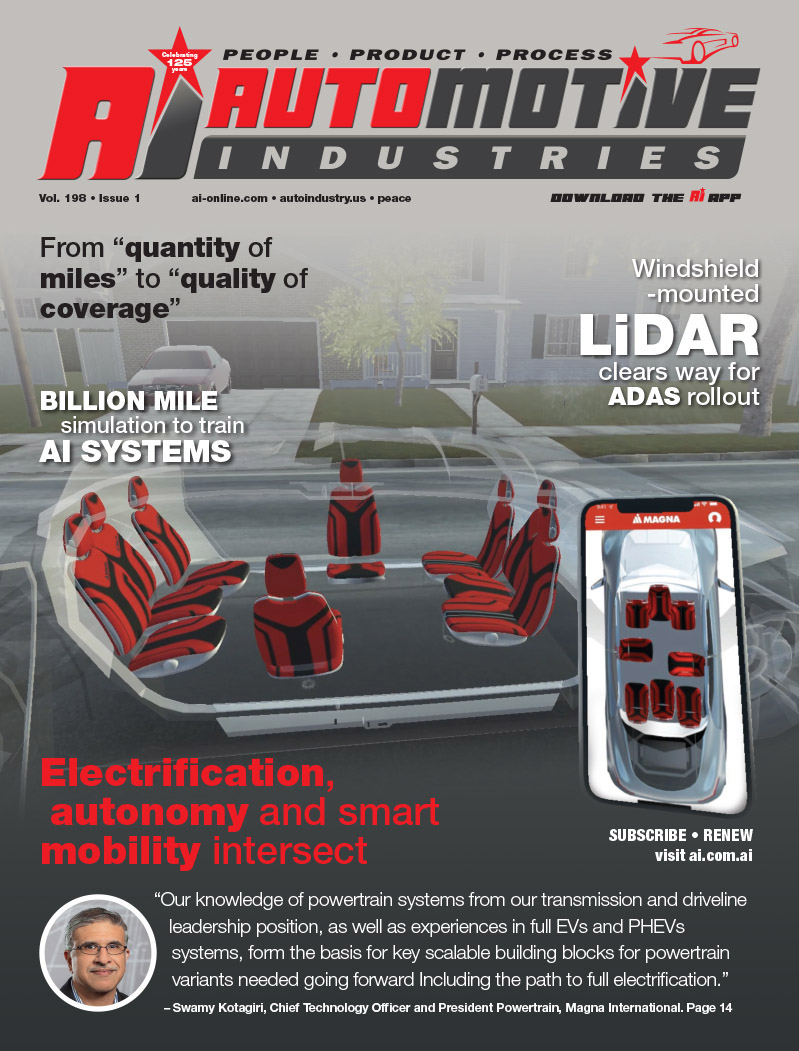
The reality of the violent and often fatal side impact collision is anything but a new topic for automotive safety professionals. Safety technologies to help lessen the effects of these horrific crashes have been evolving for years.
“Either your head hits the oncoming tree or pole, or your head hits the hood of the oncoming vehicle, that’s the typical mode of death on a side impact. These are not the only ones, but certainly the most predominant,” says Doug Campbell of TRW.
New proposed additions to NHTSA’s 214 standard (the one governing side impact) have reinvigorated the safety collective consciousness at OEMs, supplier companies, and NHTSA itself. Auotmotive Industries sat down with a number of these professionals and let them shed some light on the issues and technologies that will come into play to lower fatality rates.
Airbags
Bob Yakushi, director of product safety for Nissan North America, walks us through Nissan/Infiniti’s history with supplemental restraint systems designed for side-impact.
“We had side airbags, seat-deployed thorax/ head combination bags, around 1998 on the G20 models. That’s when we introduced our first thorax/head air bag. The shape is an upside down L. Prior to that, we had offered thorax (only) bags. We did some research in the mid ’90s that showed that if you could offer head protection you could mitigate head injuries by 80-90 percent. This research led us to phase out the thorax (only) bags and introduce the head/thorax bag. We now offer some type of side airbag on all our models.
“We’ve been going towards curtain airbags applications as we have new models. It’s not as simple as just adding a curtain to the vehicle — for instance the Sentra is still equipped with the head/thorax combination bag.”
One of the big advantages to the side curtain airbag over the head/thorax bags, according to Yakushi, is the ability to provide rear seat coverage. Yakushi went on to say that every Nissan offers side impact coverage to each passenger row in the vehicle.
“For example, on the Armada and Quest we cover three rows and to do that there’s one airbag (side curtain) to cover the first two rows and then a second bag to cover the third row,” he says.
![]() |
Safety experts say that the industry will migrate to side curtain airbags as NHTSA rewrites side impact requirements. |
“As safety technology evolves, we then look at applying those safety technologies as they become feasible and as they meet our internal criteria,” Yakushi says. “There’s governmental criteria, voluntary criteria and Nissan, of course, has its own internal criteria. As systems are developed that meet our criteria for performance, then we will start to apply those to our vehicles.
“The evolution from the seat mounted airbags into curtain airbags is the evolution of the vehicle platform. In order to apply a curtain airbag system you have to have the vehicle structure and a system developed specifically for that vehicle platform.”
Airbag manufacturer Autoliv explains that head/thorax bags have a higher propensity for inducing an injury based on the deployment strategy: The side curtain down airbag is not a concern as far as inducing injury. Also, the head/throrax bag isn’t going to be useful for keeping the occupant inside the vehicle. The side curtain bag does offer a chance to keep extremities inside the vehicle as well as provide some protection against rollover.
The evolution of the technology was one of the factors that lead to the availability of side curtains with the biggest change in the bag itself. “These bags look like an air mattress that you’d lay on and you have extremely high pressures to deal with. It was important that the bag be woven because then each strand of nylon could be controlled by computer,” says Patrick Jarboe, director of communications for Autoliv. “When air bags are sewn, that can change the structural integrity.”
Doug Campbell, vice president, engineering/ occupant safety systems and Ayad Nayef, manager, systems performance, side impact and rollover systems from TRW detailed some of TRW’s airbag inflation technologies.
“They originated (side airbags) in Europe at our design center. Our customer base was asking for them and we’ve been in production for the last five to six years, in Europe, on side curtains and seat deployed bags. We’ve been going in this direction for a number of years. The current marketplace competition has more such options coming to American and Japanese vehicles and then, of course, Ford came out with a rollover bag, an extension of the other technologies, requiring different bag design and inflator technology,” Campbell says.
TRW sights Mercedes door-deployed side impact bag as one of the earliest types of side impact systems. The company moved away from the technology due to positioning concerns. Ayad Nayef broke down the deployment technologies: “We have three technologies we use dependant upon the need of the vehicle. The speed and length (temporally speaking) of the bag pressure holding, are a big factor.
“We have a fully pyrotechnic inflator used on some smaller bags, namely the seatdeployed bags, that is very quick. Then we have the hybrid design which uses stored gas and a small pyrotechnic charge that augments it by adding heat. This system is used on curtains and side bags.
“Third, we have the cold gas (high-pressure helium) inflator system which is what we use for our rollover curtains and some side impacts. It provides a longer duration of inflation. The absence of heat in this inflator system protects the bag from retarding.
“The seat mounted airbags typically deploy in fewer than 5 milliseconds and full extension for the thorax is achieved in 8 to 10 milliseconds, while head/thorax bag full extension in about 20 milliseconds. The curtain airbags escape from the trim/headliner in about 5 milliseconds and reach full extension to the top of the door in about 25 milliseconds.”
Body Structures/Materials
Cosma International’s energy management experience came from its work with bumper systems and door beams. Cosma has global facilities offering a number of manufacturing/ material solutions to its customers. Current materials used at Cosma include Ispat Inland’s MartINsite and ThyssenKrupp’s MSW1200. The company has also been working with dual-phase and TRIP steels. Cosma also offers several manufacturing solutions such as hot stamping, roll forming and cold stamping to meet specific customer needs.
“Basically, all North American door beams are roll formed,” says Jay Mellis, director of engineering for Energy Management. “We roll form from the flat sheet. From a weight side of things, some sort of martensitic product makes the most sense for weight/performance in side impact. That doesn’t mean there’s nothing else. There’s also 120 ksi, an ultra high-strength steel that’s not martensitic, that has been speced out and worked with. But we typically go forward with something in martensite because it gives us the lowest weight solutions.”
Mellis describes the company’s North American hot stamping operations.
“We get the material in a boron grade. That (boron) seems to be the key to allowing it to be transformed into martensite with relative ease during the stamping process. We take the material and we heat it up — it’s stamped while hot and then cooled in the press.
“Once pressed, we keep the press closed, which keeps the formation constant. It allows us to cool it, essentially, in a holding fixture.
This process makes your parts very dimensionally stable and allows them to cool at a rate that assists the transformation to martensite.” Cosma’s European operation makes use of cold stamping with a slightly more formable martensite MSW1200, made in Europe, that ThyssenKrupp supplies. Typically, beams are formed into single hat or double hat configurations, 30 to 35 millimeters in depth.
Swamy Kotagiri, Cosma’s Director of R&D, explains how material/manufacturing choices affect body structure/strategies and how the new pole contingency of Proposition 214 impacts thinking.
![]() |
The Cadillac CTS features rockers made of Ispat’s M130 and M190 steel. |
“The B-pillar becomes increasingly important in taking the loads in a side-impact. There is some discussion about what part of the Bpillar actually takes the force. Do you need the whole pillar to be of equal strength or can you have one more for stiffness and the other for taking the load? We’re looking at several ideas that take into account the complete vehicle system, but of course want to solve this without putting too much cost into it.”
Nassos Lazaridis, staff consultant, product applications R&D, with Ispat Inland, reviews his company’s involvement in providing materials for door reinforcement beams.
Ispat Inland provides steel in the form of flat sheets to companies such as Shape, Trim Trends, Magna and Iroquois. From there the material is usually roll-formed into a tube, single or double head configuration or hat configurations. The most commonly provided steel choices for such applications are MartINsite M190, M220, or Di- Form TM980 (dual phase), also referred to as Di- Form140T (140 is the tensile strength in ksi).
However, Lazaridis also stresses that there are other steel structures in the vehicles that are radically important and were essential to enduring a side-impact. Namely the B-pillars, roof rails, rockers/rocker reinforcements, as well as cross-car beams. He cites the Cadillac CTS’s use of the M130 and M190 steel in the rockers.
Lazaridis says, “The trend appears to have more carmakers moving towards M130, M190 or Di-Form140T for the crosscar beams and dual phase or TRIP steels for the B-pillars.” He also notes that as a strategy, the side structures are best made of material with highyield strengths. This property helps keep structures from collapsing.
“You want to transfer the energy from one side to the other — you don’t want to absorb it,” he notes.
Front/Side Compatibility
With the proliferation of SUVs on the road, a lot of thought is given to the issue of a larger/higher aggressor vehicle colliding with a sub-compact (smaller/lower) vehicle and the inherently dangers there-in. The industry is working on several different concepts to solve these issues.
![]() |
Volvo conducted its own compatibility test by crashing an XC90 SUV into the side of the smaller S40 sedan. |
Volvo has tested the compatibility of its XC90 SUV in side impact crashes with the smaller S40 sedan.
“In our SUV, we have an under-bumper structure that, in the case of a collision, is meant to hit the other vehicle at a normal bumper height,” says Daniel Johnston, product communications, for Volvo Cars of North America. “So rather than us overriding the other car, if the car is set at the standard height, set by NHTSA, we should impact that car right at that bumper.”
According to Yakushi, Nissan’s contention is that in cases where some effort has been given to front/side compatibility, especially in newer product launches, you would still have instances where vehicles of greatly varied sizes would collide. In those cases, the smaller vehicle being struck by one of considerable larger size would benefit greatly from the presence of a side curtain airbag system.
Proposed additions to 214
“The incompatibility issue is all about head injuries,” says NHTSA’s Rae Tyson. “We feel that this pole test (an addition to 214) is going to speak to that point.”
NHTSA is also upgrading the side impact requirements by adding an additional test and a new fifth-percentile adult (4 ft. 11-in. dummy) to the requirement. The current barrier test will continue but the vehicles will also have to pass the pole test, which is a much more aggressive test.
“What we are particularly interested in is increased head protection,” Tyson says. “The pole test will force the manufacturers to improve head protection.”
Tyson says that NHTSA doesn’t usually specify a technology but sets a performance goal.
“We don’t tell OEMs how to get there. It’s up to them to design the cars to do it. In all likelihood they will select side curtain airbags to meet the standard. This is a reasonably typical sort of crash that does occur in the real world. It is also one of the most severe side impact crashes you can have,” says Tyson.
Tyson says that the proposed regulation is put out for public comment. After 150 days, NHTSA reviews the comments and makes whatever changes to the proposal it feels are necessary. The final step is deciding when the new regulations will be enacted.
“We usually give manufacturers one product cycle,” Tyson says.
“We feel that this is one of the few remaining areas where there are significant safety benefits to be derived from government regulation. We’re talking about a significant saving of lives and a significant reduction of injuries once this regulation comes online and the fleet starts to turns over. There isn’t anything we’ve done over the last several years that is going to have the impact on safety that this will.” “Certainly a pole impact is more severe than a flat barrier,” says Yakushi. “I think that type of regulatory test, if it comes to be implemented, will certainly move the industry towards having curtain airbags. But with the voluntary agreement, the industry was going that way anyway.”
The Fundamentals
The painful irony in all these safety mandates and technologies is that they are largely ineffective when a passenger/driver operates sans seatbelt.
“We can offer all kinds of really cool technologies in the car but in the end, if the driver doesn’t put on a seat belt or drive responsibly there’s less and less we can do for them,” says Johnston of Volvo.
Nissan’s Yakushi simply states, “If you don’t have a restrained occupant, all bets are off.” Is there a way to get more Americans to buckle up?
“Education,” says Autoliv’s Patrick Jarboe. “Educating consumers is what it’s all about. Look at the effort that Toyota is making in its dealerships to educate people about the benefits of the side curtain airbags. I’d like to see more of that. It takes a proactive approach.”
What is MartINsite? Ispat Inland created MartINsite, an ultra-high strength steel that consists of fully martensitic microstructures engineered to offer some of the highest strength levels available in the marketplace. According to Ispat, these steels offer much higher strength-to-weight ratios than conventional cold rolled steels and, pound-for-pound, are more cost effective than other metals or plastics. Ispat’s ultra-high strength steels have been designed to provide uniform mechanical properties in both longitudinal and transverse directions to allow more flexibility in both design and manufacturing and increase material utilization. Though limited in the formability, alternate available manufacturing technologies such as roll-forming are used to fully utilize these grades. The high strength-to-weight ratio opens up many weight reduction opportunities. They are designed especially for roll-formed and tubular applications where high strength is critically important. Typical applications for MartINsite grades are: bumper reinforcement beams, door intrusion beams, rocker panel inners and reinforcements, side sill reinforcements, belt line reinforcements, springs and clips, among others. |
More Stories
Best Wheel Size for Off-Road Adventures: What People Get Wrong
Trusted Auto Collision Repair That Restores Both Performance and Peace of Mind
What You Need to Know About Tire Pressure in Winter vs Summer