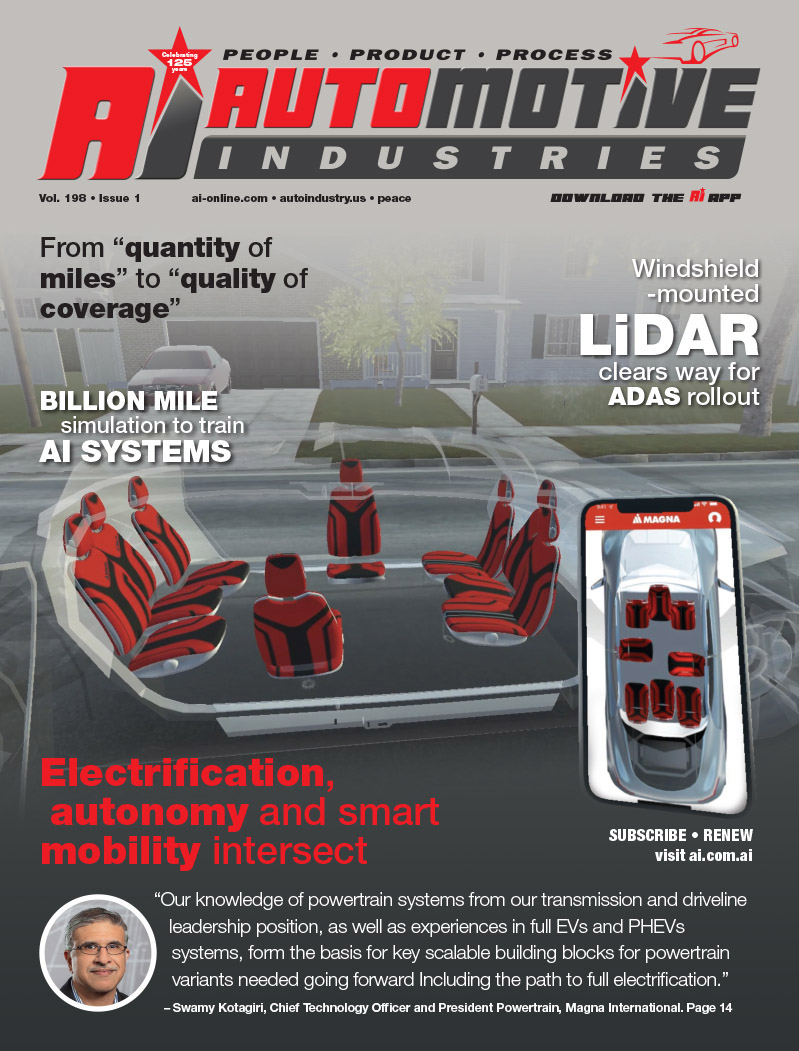
Ford’s supplier park is a model for future supply chain operations in North America.
Ford not only launched the new Freestyle crossover and Ford Five Hundred and Mercury Montego sedans this fall, it also launched the first North American supply park. The four multi-tenant buildings offer 1.5 million sq.ft. of manufacturing and office space and occupy a 155-acre site that sits onehalf mile from the Chicago assembly plant where the Ford Five Hundred and Mercury Montego sedans and Ford Freestyle Crossover are built. Reports are that a Mercury Crossover will join the line-up in 2005.
![]() |
Workers at Lear’s supplier park facility build headliners that will be sequenced into Ford’s Chicago assembly plant and installed in the new Ford Freestyle crossover. and Ford Five Hundred and Mercury Montego sedans. |
Brose North America will supply door systems, window regulators and latches; Decoma International will supply bumpers, front and rearend modules, plastic body panels, roof modules, exterior trim components, sealing and greenhouse systems and lighting components; Facil LLC will provide fasteners; Flex-N-Gate supplies bumpers, engine mounts, grilles, hinges, pedal systems and running boards; Lear Corp. will supply the headliners; Plastech Engineered Products Inc. will supply interior trim, cockpit module assemblies, bolster integrated cooling module assemblies, fuel tank assemblies and climate auxiliary assemblies; Summit Polymers Inc. will supply consoles; S-Y Systems Technologies America LLC, a joint-venture with Siemens and Yazaki, supplies wiring harnesses; TDS Automotive is supplying value-added logistics services; Tower Automotive Inc. is supplying most of the vehicle’s structural underbody stampings including the rear floor pan, engine cradle and front apron and ZF Lemforder Corp. is providing front and rear axle systems.
All in all, the supply park is supplying 60 percent of the value of the vehicle. Roman Krygier, group vice president manufacturing and quality, bases that number on the supplier park and the fact that most of the major sheet metal is coming from Chicago Stamping which is just 25 miles up the road. Even without the stamping facility factored in, the supplier park still supplies about 50 percent of the vehicle,s value.
“We’ve got the suspension systems, the rear floor pan, the IP, the center console, there’s a high value in these parts in relation to the value of the vehicle,” Krygier adds.
While this is the first of its kind in North America, supplier parks aren’t a new concept to Ford. The company currently operates supplier parks at its plants in Genk, Belgium, Saarlouis, France, Valencia, Spain and a new facility in Bahia, Brazil.
![]() |
Brose North America supplies inner door systems for the Ford Freestyle and Five Hundred and Mercury Montego. |
“We think it’s an excellent model,” says Krygier, “but it also depends on where we’re going with product, and what the capability of that surrounding area is. “But, in our judgment, we’re going to build off of this concept.”
As for expansion in Chicago, Krygier says that Ford is going to take advantage of it as time progresses.
“If we have an opportunity to do more just-in-time and interface more suppliers, we will,” Krygier says. “It’s not an issue of space and we’d like to grow that. And we’re going to leverage it as much as possible.”
Krygier says that the business case in Chicago was overwhelming. Previous to the supplier park, the average number of miles traveled by the supply system was 460. The average now is only 120 miles.
“That equals two billion gallons of diesel fuel saved a year because of the supply park across the street,” Krygier says. “Just freight alone saves us about $50 a vehicle.”
But Krygier says that the key is that suppliers are linked together more productively — becoming an integral extension of the plant, responding in broadcast and building in sequence.
“We have very little inventory,” Krygier says. “There’s just enough inventory in our supply park to protect our flow for changeover and we’re building just-in-time.”
![]() |
Plastech employees build center consoles for the Ford Five Hundred, Freestyle and Mercury Montego. |
“Firstly,” he says, “in the communications. This is not a business now where something happens in the supply park and we can wait a few days because there’s a lot of stock in the system. The toughest part is that communication has got to be rigorously tight. The good news is that if the supplier park has an issue or we need them to help us do something to change a process, it comes to us in no time at all — within a day — depending on whether or not it’s in a tool. But we can take things out of the process part of it in a day.”
There will be supplier representatives on the assembly floor and Krygier says that they will be treated as extensions of the management. Suppliers will also meet with Lawson on a daily basis to discuss things like quality and mix changes — things that affect the products they build.
Tower Automotive isn’t new to supplier parks or just-in-time manufacturing. It supplies frames to Nissan’s Canton, Miss., plant from a facility just down the road.
Kathleen Ligocki, president and CEO of Tower says that what makes this deal different is that Ford has decided to outsource a large portion of its body shop. (Tower has a similar arrangement with Ford at its Genk, Belgium, facility). Ligocki also says that being located on a supplier campus not only requires collaboration with Ford, but collaboration among the eleven suppliers who are on the campus.
![]() |
A Tower worker moves a Ford Freestyle rear floorpan to a shipping rack to be moved next door to Ford’s Chicago assembly plant. |
S-Y Systems Technologies America LLC will supply wiring harnesses for the vehicle, both as a Tier 1 to Ford and a Tier 2 to Lear Corp. A company spokesperson says that the company manufactures 300 different harness variations for the three models being built at the plant. The harnesses aren’t manufactured at the supplier park as the process is very labor intensive requiring 400 people to make the harnesses for Ford. Instead, the harnesses will be made in Asia and shipped to Chicago where S-Y Technologies employees will sort and sequence the harnesses to Lear and the assembly plant.
S-Y signed on with Ford in 1999 when the vehicle development program was started. Talk of developing a supplier park in Chicago started in late 2001, early 2002. The company has been on site for about a year. An S-Y spokesperson says that they are currently working with Ford to develop a supplier park for the Hermosillo, Mexico, assembly plant that will produce the Ford Fusion and Mercury Milan mid-size sedans. Interior supplier Collins & Aikman will also be a part of the Hermisillo supply park. A spokesperson for the company says that Hermisillo will mark the first time the company has sequenced things like interior carpeting into the assembly plant.
Lear Corp. employs 70 people in two shifts to make headliners for the Freestyle, Five Hundred and Montego. Plant Manager, Jeff Schropp, says that the headliners for the Taurus (Chicago’s previous model) were made along with the seats at Lear’s Hammond, Ind., plant, which is only eight miles away from Chicago Assembly. Schropp feels that the added seat production to accommodate the Freestyle’s third row gave Lear an incentive to join the supplier park.
“When Ford said that they wanted headliners to be broadcast,” Schropp says, “we decided to pay rent.
More Stories
What You Need to Know About Tire Pressure in Winter vs Summer
Essential Features to Look for in ADAS Calibration Systems
Your Guide to Filing a Car Accident Claim