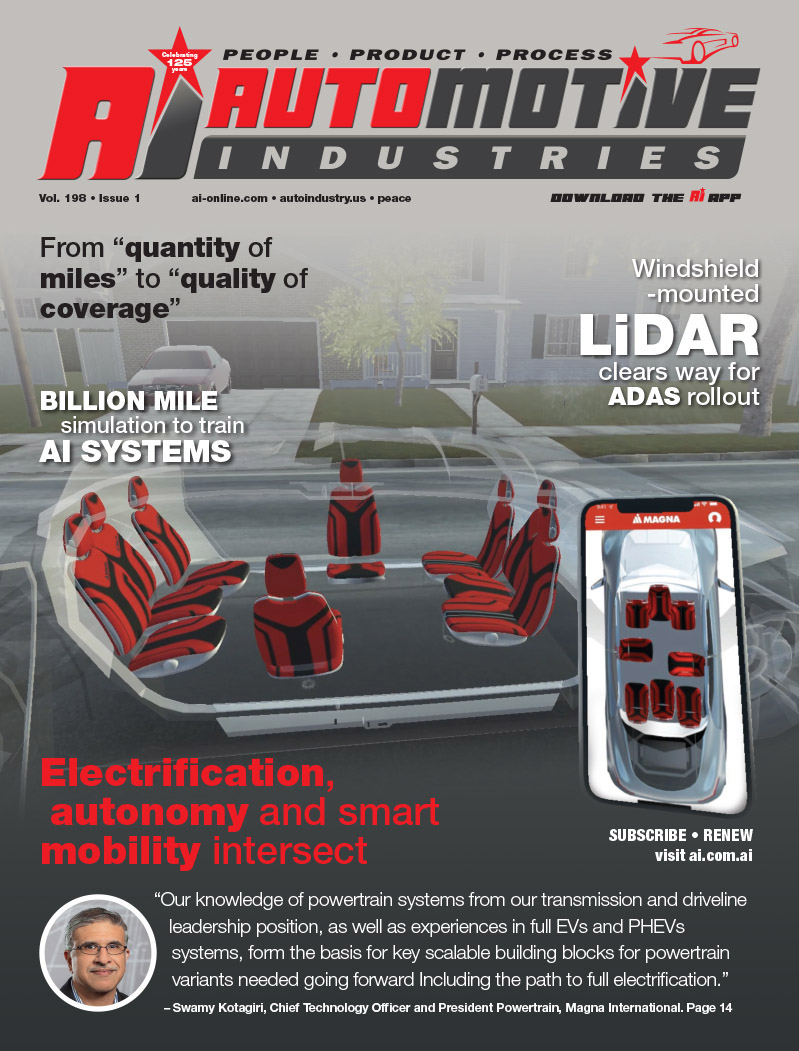
Quasar International offers a new approach in non-destructive testing of automotive castings.
The purpose of non-destructive testing (NDT) is to identify and reject defective parts, parts that would fail prematurely in service. Most of today’s methods for NDT depend on visual inspection. X-ray, magnetic analysis, ultrasonic and flux leakage are a sampling of NDT commonly used in the automotive industry.
![]() |
Quasar NDT system with robotic parts handling. |
“Most of today’s NDT methods depend on some type of indication,” says Robert Nath, chairman of the Albuquerque, N.M.-based company.
“Indication is a very big word in non-destructive testing — an indication of a void, an indication of porosity an indication of a crack, an indication of something. Our method on the other hand is a measurement of the structural characteristics of that part.”
According to Nath, Quasar identifies patterns that discriminate between acceptable and unacceptable variations in these characteristics. An unacceptable pattern indicates the presence of a defect and the RI computer rejects the part. “The resonant frequency varies with the stiffness and mass,” says Nath. “Changes in stiffness and mass change resonant frequencies.”
According to Jim Schwarz, president of Quasar International, the resonances are based on the material properties, “the dimensions, the density, the stiffness,” of the part. “So a defect, when you think about it, is a change in the stiffness because it is cracked, or the dimensions because the part is too big or too small, or the density because perhaps the part was made with the wrong material,” says Schwarz.
Parts made by a controlled process have a similar pattern of resonances determined by the part’s dimensions and material properties.
“A resonance is a perfect way to measure for structural defects, and people have been trying to use it for the past 50 years,” says Schwarz. “But the problem is that acceptable process variations cause greater frequency variations than all except the most severe defects. So, without some method of compensation for the process variation, resonant testing is limited to only very gross defects. What we realized was that if the reason the resonances are moving is because of the process variation, the information about the process variation must be contained in those resonances. So if I measure several of them, I ought to be able to extract that information.”
Quasar’s NDT system measures several resonances and calculates a compensation factor.
“Any part has an infinite number of resonances all determined by slightly different things,” says Schwarz. “The trick is picking which resonances to use. In a typical Sorting Module, we use five resonances. Four are used to predict where the fifth one should be. If it is there, it is a good part. If it is not, it’s a bad part.” Quasar calls its method PCRI — Process Compensated Resonant Inspection.
The fact that PCRI is based on measurable physical properties means that results are quantifiable and repeatable. Parts are rejected because of their structural properties, with no human judgment about the severity of a defect.
“The customer sets up the pass/fail standards based on the application of the product,” says Nath. “They can measure as many parameters as they feel necessary. This is all set up beforehand, so the person at the end of the line isn’t setting standards; he’s only pulling parts that have been failed based on the standards set up by management.”
The Quasar resonant inspection system involves three computers. A transceiver generates and analyzes the signals. All of the calculations are done by a standard PC, which is mounted into an industrial cabinet. And an Allen Bradley PLC measures the part temperature and controls loading and unloading the part.
![]() |
A cast-aluminum master cylinder undergoes non-destructive resonant inspection testing on one of Quasar’s fixtures. Jim Schwarz, president of Quasar, says that the industry needs to be convinced that NDT rejects defective parts, not parts with defective indications. |
The key to Quasar’s PCRI is the Sorting Module, which is the set of patterns that describes the characteristics of an acceptable part to the computer. The Quasar RI system is used to measure the resonances of a training set of parts (both good and defective). Quasar recommends that the training parts be destructively tested to establish an objective set of failure standards. The results are input to VIPR, Quasar’s pattern recognition program, which generates the Sorting Module and translates it into instructions for the RI system. In production, each part is vibrated and the Sorting Module accepts or rejects it based on its deviation from the accepted standard. When design or process changes occur, VIPR’s maintenance mode is used to update the Sorting Module.
Quasar currently has systems installed in North America, Brazil, China, India, Europe, Japan and Korea, testing castings, forgings, powder metal and ceramic parts. According to Schwarz, one of the biggest obstacles the company faces when visiting potential new customers is that most companies, unless they are forced to, don’t test.
“Companies are under tremendous pressure for cost reduction and price reduction. The only time they think about NDT is if they have to, either the customer has it specified in their contract or they are in containment. People have to get over this idea that their eye is smarter than the material property measurement. There are some parts that to the eye look like good parts, but they aren’t, and vice versa. Our experience is that the majority of parts rejected by conventional NDT will not fail in use. This is a big waste.
“Our goal is to revolutionize the impact of NDT on the manufacturing system. That means we want to enhance safety and reduce risks for the OEM and the person riding in the car.
“We need to convince the community that the purpose of NDT is rejecting defective parts,” Schwarz says, “not rejecting parts with defective indications. And that is exactly what our method does.”
More Stories
Your Guide to Filing a Car Accident Claim
Steps to Take Immediately After a Car Accident
What Makes SUV Cars More Prone to Accidents?