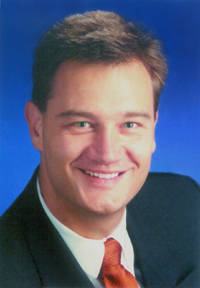
Stankiewitcz supplies acoustic insulation packages for the automotive industry. Automotive Industries talks to Dr Oliver Hafner, Managing Director, Stankiewicz about the company and future trends in acoustics.
Automotive Industries (AI): Dr. Hafner, would you please introduce Stankiewitcz to our readers?
Hafner: Stankiewicz is a German-based automotive supplier which has been working for the automotive industry for the last 50 years. Our main customers are DaimlerChrysler, BMW and General Motors. We are suppliers for the acoustic insulation package, including the carpet for DC for the M Class, G class, R class and C Class and for BMW for the 7, 6, 5, X5, X3 and Z4 series. With 2150 people we are producing sound insulation parts at 9 facilities in Germany, USA, Belgium, the Czech Republic, France and Poland, creating annual sales of 270 million Euro.
AI: What are the main strengths of your company?
Hafner: As a supplier to the premium OEMs we have to offer our customers above average service. Stankiewicz offers its customers the whole variety of products, beginning from standard “me too†products to highly innovative new solutions and new sound absorbing materials. We are able to offer systems solutions for the whole vehicle, from the engine compartment and under body to the interior and trunk. It is the combination of engineering of the acoustic result, developing new production processes and the development of complete new materials. You can not do this with R&D that only works on customer based orders. For this you need a motivated R&D team which develops solutions for tomorrow and is able to lead the way for the customer. (We spend about 5.5% of our sales on R&D)
AI: What were the biggest challenges you encountered with Mercedes-Benz M-, G-, and R- Class?
Hafner: For the M class, G class and R class we deliver the carpet and the complete interior sound insulation packages from our plant in Spartanburg, SC. Being competitive was the biggest challenge for us from the beginning. We have to deliver from our existing plant which is about 400 miles away from Tuscaloosa. This is a distance you cannot ship sequenced parts, therefore it was clear we have to deliver to a sequence centre close to the MBUSI plant. Because we were not willing to have a stock in Tuscaloosa and a second one in Spartanburg we had to come to a very lean production which has no stock for finished parts. In combination with the production forecast from MBUSI we are able to put the produced parts on the next truck, without any stock. After we have erected the new building for the DC production, a lot of new and variations and parts emerged. One challenge was to keep the complexity under control and to produce the additional parts under the restrictions of the existing building. Kaizen methods and a further reduction of work in process materials and raw materials, freed up more space to get the additional parts handled. Another challenge was to develop suppliers which can handle the specifications of the German premium OEMs. This was a long road, but we are now finally able to domestically purchase 99% of our raw materials. This also saved valuable space and made our customers and us more independent from trade restrictions and currency exchange rates.
AI: What are the future trends in acoustics?
Hafner:
• An increasing demand for a higher level of comfort
• A demand for reduction sound emission to the exterior
• Intelligent light weight solutions
• Flexibility
Let’s look at them one at a time…
An increasing demand for higher level of comfort
It will no longer be the power of an engine or the top speed of a car which is important to the final customer. Fuel economy and comfort will rise to the top of the customer’s wish list. People spend more time in their vehicles. They want the means to communicate – they want to listen to music coming out of high-end audio devices and they have to makes their business phone calls. Therefore I clearly expect a shift from power demand to comfort demand and this calls for silent cars. Today’s middle class cars of the premium segment offer the same acoustical comfort as luxury cars did 15 years ago, and this trend will continue. This will be an important way for the premium OEMs to differentiate their products and to generate a brand DNA which meets premium customer’s demand.
Intelligent light-weight solutions
Improving the fuel economy will be one of the top priorities for the OEMs. This will be achieved be more economic engines and by reducing the total weight of a vehicle.
One the one hand engines will be made of light alloy metals that will have a way higher sound emission. In combination with a power train trend going towards Diesel and a change of engine configurations e.g. V8 to V6 or even I6, the demand for improved sound insulation will go up.
One the other hand, due to physical reasons, a higher acoustic dampening has to be achieved by the usage of more weight, for example dampening foil, or heavy layer. But the last thing one wants to do is to increase the weight of one’s sound package in order to eliminate the noise of a lighter engine. Therefore one has to develop sound systems which can do the same job with less weight or a better job with the same weight. The key question there is to find an intelligent distribution of the masses. This could hardly be done with the existing solutions because the distribution of the weight is determined by the production process and not by the acoustic demand of the vehicle. Using new techniques such as sprayable heavy layers will give you the possibility to have tailor made solutions for each vehicle, even adapted to the individual configuration of the engine or gear box type.
At Stankiewicz we can apply sprayable heavy layer on the back side of a carpet where the vehicle needs it, for example adjacent to the gear box or to the exhaust system. We can even produce a dash board sound insulator with spray technique where you can adjust the area weight within the part from 2 kilograms per square metre to 6 kilograms to square metre. All this can be done with the same tool; the only thing you have to adjust is the programme of a robot.
A demand for reduction sound emission to the exterior
Legislation will change and the OEMs have to comply with higher legal demands for exterior sound emissions. This will automatically increase the demand for acoustic solution for the engine compartment and the under body of the car. In this case you are not only talking about a more intelligent distribution of weight but the development of complete new materials. Fibre materials will substitute injection moulded materials.
Flexibility
The car models where one has to build the same number of vehicles from SOP to EOP are gone. New models are popping at a never seen frequency and a car model which is on the market for three years will dramatically go down in numbers. This has two impacts on the suppliers.
Firstly, you need a more flexible production which can handle a higher variety of products and smaller lot sizes. Reduction of change over times and versatile equipment will be decisive for future model lines.
But not only are the models changing but also the equipment of the cars within the live cycle. New engines, gearboxes and transmissions will be implemented during the live cycle to freshen up a model. The change of a power train has a tremendous impact on the acoustics of the vehicles. If a supplier is able to develop variations in a shorter period of time and to produce these variations on existing tools, more varieties can be faster handled at lower cost.
More Stories
MESSRING completes new crash test facility for Mahindra in India
ROHM Develops an Ultra-Compact MOSFET Featuring Industry-Leading* Low ON-Resistance Ideal for Fast Charging Applications
More than 30 of the top 50 global suppliers have production facilities in Turkey