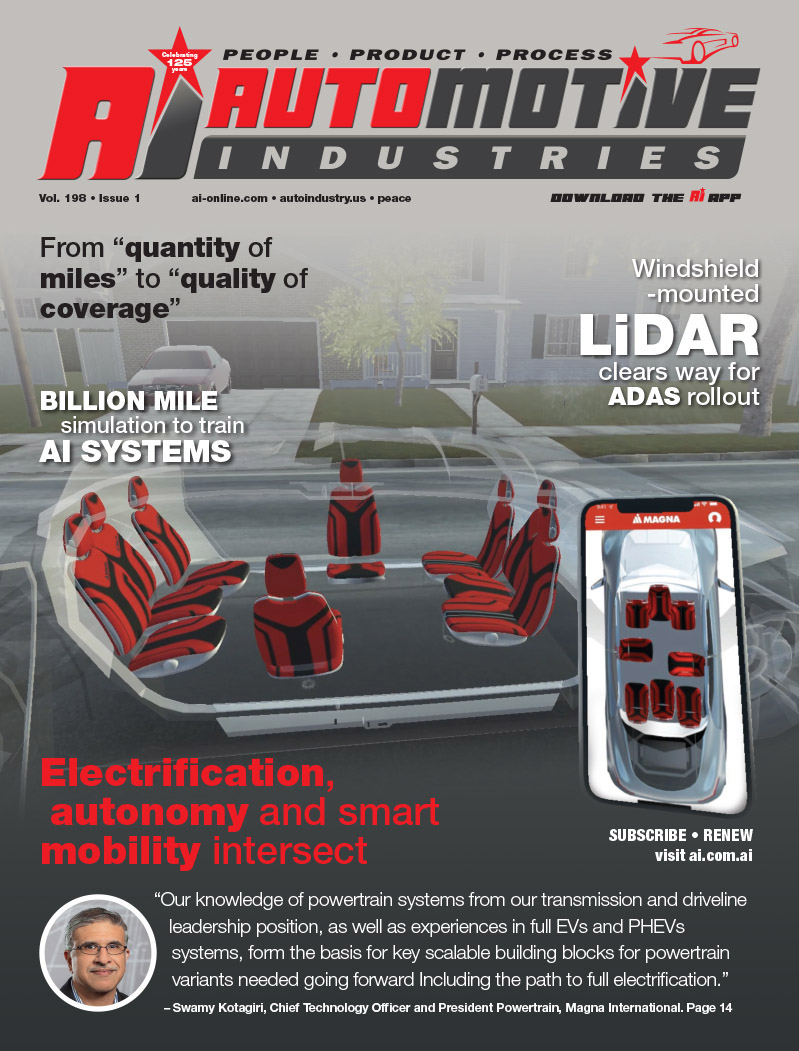
Kolbenschmidt Pierburg, a member of the Rheinmetall Group, is winning orders for its newly developed Pierburg cooled exhaust gas recirculation (EGR) module. Pierburg currently has orders on hand from three renowned European carmakers, representing a total contract volume of around $400 million.
The industry is moving toward increased use of EGR technology as a viable solution to meeting stricter exhaust gas regulations for diesel and turbo-charged gas engines. For passenger car and commercial vehicle diesel engines, the technology is proving to be increasingly effective in the reduction of nitrogen oxides (NOx).
The new EGR module from Pierburg comprises a newly developed cooler made from die-cast aluminum that provides improved heat conductivity. Aluminum also is a low-cost and weight-saving alternative to today’s commonly used stainless steel coolers. An additional inherent advantage of aluminum is that it does not corrode.
In lowering exhaust gas temperatures by over 600 °C, depending on the operating mode, the Pierburg exhaust gas cooler helps reduce combustion temperatures and, as well, nitrogen oxide emissions, while also minimizing heat generation from other engine components.
Pierburg’s longstanding expertise in emissions reduction enabled its engineering team to develop this aluminum EGR cooler. Its innovative design features specially shaped fins that efficiently and effectively re-circulate the exhaust gas. The new cooler concept is suitable for both low- and high-pressure systems and can be integrated into the intake manifold of engines with matching design features.
Coolers have traditionally consisted of welded stainless steel sheet metal with relatively high production costs. Aluminum, however, provides much higher heat conductivity versus steel and makes it possible to achieve very high exhaust cooling even in a relatively small space.
Moreover, the patented discontinuous fin construction is ideal, since the turbulent mixing of the exhaust gas flow is enhanced by the unique fin design. It counteracts direct fouling, promotes convective heat exchange and permits an exchange of substances, pressure and heat transverse to the mainstream direction, and also provides the advantages of self-cleaning.
This fin creates what is termed Kelvin-Helmholtz instabilities that are exploited where a swirl occurs at the shear layer of two parallel-flow layers with varying flow velocities. The result is a more efficient cooling process.
In order for the engine to reach its operating temperature as quickly as possible, the new Pierburg exhaust gas cooler has a bypass valve that is actuated either electrically or pneumatically, depending on the application.
The exhaust gases are routed through this valve as well as a bypass channel, until the required engine operating temperature is reached.
With the engine at its peak operating temperature, the bypass is closed so that the cooler can reduce the temperature of the recirculated exhaust gases. The effective lowering of the combustion temperature achieved through this process, combined with corresponding oxygen abatement, reduces nitrogen oxide emissions to a maximum degree.
Another important advantage of the new EGR cooler is that it is an integrated assembly in which the individual components are integrated into one EGR module. The components include an EGR cooler with its coolant flow, a bypass valve alternating on-demand between the cooler and bypass operation, and an EGR valve for controlling the EGR rate. Moreover, aluminum makes it possible to combine the EGR module and intake manifold into one individual component. The result is an integrated intake manifold module with an exhaust gas recirculation and cooling system.
By fine-tuning a new welding technique developed for die-cast aluminum parts, Pierburg is now welding together all the internal interfaces of the module rather than using the type of temperature-resistant seals and supplementary fasteners employed in previous systems.
More Stories
DuPont materials science advances next generation of EV batteries at The Battery Show
How Modern Power Management Enhances Connected Fleet Tech
Automotive Industries interviews Bahar Sadeghi, Technical Director, Car Connectivity Consortium (CCC)