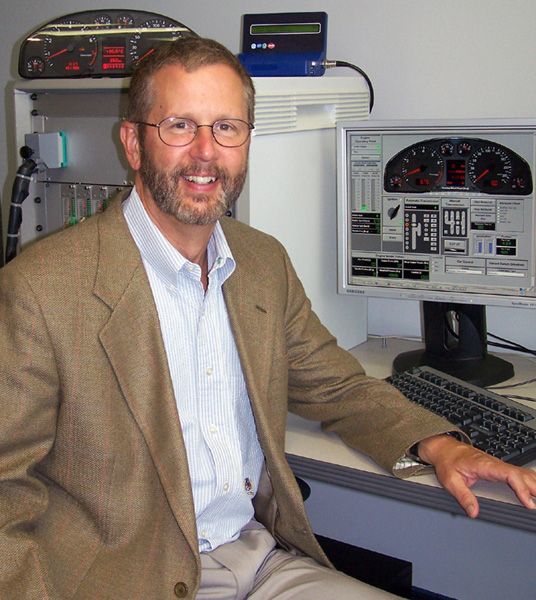
“In most of our product lines, we lead the industry in feature-rich products.”
Automotive Industries spoke to Kevin Kott, president of dSPACE Inc, and asked him how the company’s products have helped change the design of automobiles
dSPACE Inc, is the Michigan-based subsidiary of the German dSPACE, which is a leading manufacturer of engineering tools for embedded controller development and testing. The company provides integrated hardware and software for prototyping control algorithms, automatic generation of production code, controller testing and calibration and engineering support services.
In 2005. dSPACE introduced its RapidPro System, which helps improve integration of automotive sensors and actuators, which is a key requirement in rapid control prototyping or RCP, for electronic control unit functions. DaimlerChrysler, used RapidPro along with dSPACE’s MicroAutoBox, for Active Body Control.
The RapidPro System can be used together with the dSPACE prototyping platforms (MicroAutoBox and AutoBox) to develop control applications for engine, transmission, vehicle dynamics, body electronics, drives and others. The company’s PC software called ConfigurationDesk provides fast, intuitive configuration of all RapidPro’s hardware parameters, as well as diagnostics.
The RapidPro Power Unit enables the adaptation of many different types of actuators (for example, drives, injectors, valves, relays, etc.) to specific prototyping systems. The RapidPro SC (Signal Conditioning) Unit in conjunction with standard SC modules or customer-specific modules, lets customers adapt to almost any type of sensor (for example, temperature, pressure, and crankshaft and camshaft sensors). Two other new signal conditioning modules, an exhaust gas oxygen sensor and a knock detection sensor, provide a whole range of extra prototyping features for engine management applications.
dSPACE automotive customers include: GM, Ford, DCX, Delphi, Visteon, Honda, ISUZU, Hyundai, Renault, BorgWarner, Bosch, Continental, Volkswagen, AFT, HINO Motors, Ricardo and BMW.
Automotive Industries spoke to Kevin Kott, president of dSPACE, and asked him how the company’s products have helped change the design of automobiles.
AI: What are some of the major benefits for automotive companies in using dSPACE’s products in terms of design and development?
Kott: Our products are used to develop, verify and calibrate ECU software and systems. Our customers benefit by producing systems faster and ultimately with higher quality than if they used more traditional development methods. Automotive features are becoming more and more software dependent, and as a result, exceptionally complex. Without the tools and simulation systems, these tasks would be much more difficult.
AI: How popular are your products in North America? And in the rest of the world?
Kott: dSPACE technology was used more extensively first in Germany, where automotive ECU network complexity developed earlier than in the USA. However, use in the USA has grown and our Rapid Control Prototyping systems and Hardware-in-the-Loop simulators are now the de-facto standard among auto OEMs in the USA and around the world.
AI: Please give us an example of how RapidPro has been put to use by an auto company.
Kott: DaimlerChrysler used dSPACE’s RapidPro system to develop its Active Body Control (ABC) controller function. Specifically, RapidPro was used to condition the transverse acceleration, pressure, body acceleration and level sensors, as well as to compute the actuator signals for electro-hydraulic spring struts. The modular design of the RapidPro system enabled DaimlerChrysler to make requirements changes with minimum effort. This feature also made it possible for DaimlerChrysler to reuse components in vehicle tests for other development projects. Additionally, DaimlerChrysler was able to execute its complex I/O tasks with the use of an external microcontroller (the RapidPro Control Unit), freeing up the system’s main processor.
AI: What are some of the new products we can expect from dSPACE over the next few years?
Kott: We take pride in introducing products that are well tested, robust, error free, and leading-edge in terms of technology and customer usability. In most of our product lines, we lead the industry in feature-rich products. Therefore, we do not announce new products until shortly before introduction. I can say that if you look at each of our existing product lines, you will see customer desirable features being added on a regular and continuous basis.
AI: What kind of presence does dSPACE have in developing markets such as Asia, and what are your plans for growth in these markets?
Kott: We are already well established in Asia with one of our largest, wholly-owned subsidiaries in Japan. Additionally, we have long-established distributors in India, China, Korea, and Taiwan. As Automotive OEMs and suppliers add ECU development activities in these countries, we are there to support them.
GM drives dSPACE
Keith Lang, General Motors Powertrain, Advanced Power Transfer Group USA
General Motors is employing XCP on CAN for software development and CalDesk, the universal measurement and calibration tool, to parameterize the electronic control unit (ECU) for advanced transmission projects. Using CalDesk has numerous advantages compared to working with a combination of different tools: For example, measurements on ECUs and prototyping platforms can be run according to a common time base, with simultaneous parameter adjustments.
Accessing ECUs in the Transmission
ECUs in the transmission area are becoming more compact, and increasingly being installed in inacces¬sible places. This makes it all but impossible to connect additional interface hardware in or on the ECU for software development purposes as is the case with General Motors’ new six-speed transmission, where the ECU is located inside the actual transmission.
General Motors Advanced Transmission Group is using CCP for calibration and measurement, while bypass com¬munication between the ECU and the prototyping hardware (MicroAutoBox in this case) is established via XCP on CAN.
Employing an integrated experiment environment featuring calibration and measurement access to both the ECU and the dSPACE prototyping hard¬ware was a crucial requirement for GM in this project. CalDesk has been chosen for this. CalDesk allows vehicle ECUs and their busses, and rapid control prototyping platforms, to be accessed simultaneously. It is capable of handling any number of devices in a single experiment.
Active Seat Suspension
A joint project between DaimlerChrysler Research and Technology and the company’s advanced engineering truck group developed a mechatronic truck seat system. The system aims to reduce the annoying vibration that truck drivers are subjected to while driving. A dSPACE prototyping system based on a DS1005 PPC Board provided fast results for developing and verifying a prototype of the controller. And since the seat system is modular in design, the basic seat model can be reused in multiple ways, which cuts down on the number of different parts.
Mechatronic Concept
Truck drivers’ performance and condition behind the wheel greatly depend on their being in good physical and mental shape. The seat they sit on has a lot to do with this. Conventional, passive seat suspension systems for commercial vehicles use springs and dampers to iso¬late vibration. Since there is virtually no more room for improvement in these, the team developed an active seat suspension for commercial vehicles that uses actuators in addition to the spring-damper elements. Passive support of the seat is provided by an air spring integrated into the seat frame. The air spring compensates for vibra¬tion and is also used for seat height adjustment. This is supplemented by a compact electrical linear direct drive for active vibration isolation, which acts as an actuator and is supplied by the vehicle’s electrical system.
Good vibration isolation was one essential criterion, modular design was another. The seat’s basic frame had to accommodate two seat suspension systems: the conventional passive one and the new active one. The modular seat system also had to be installed in various truck series with dif¬ferent floor structures and wheel arches.
Fast Results with dSPACE
The controller structure was designed graphically using MATLAB®/Simulink and first simulated offline using the model of the controlled system. Next the controller structure was replaced by dSPACE hardware.
The DS1005 PPC Board supplied the computing power for our real-time system and was also the interface to the I/O board.
The DS2201 Multi-I/O Board measured the required input and output signals, and provided the output value for the actuator signal. Finally, relative motion given by the electrical actuator was captured via the DS3002 Incremental Encoder Interface Board.
Validating the Controller Design
To initially test for compliance with the design specifi¬cations without using a real vehicle environment, the design results were validated online on DaimlerChrysler’s vibration comfort test bench in Sindelfingen, which included a real driver’s seat, sensors, and actuators. Measurements made on the test bench and in later test drives proved that the active seat suspension consider¬ably reduces physical stress for the truck driver. However, the improved vibration isolation also results in greater relative motion between the seat and the cab floor. This takes some getting used to and as a first impression impairs the subjective comfort level.
Involved in the project are:
Prof. Dr. Jürgen Maas: (formerly DaimlerChrysler Research and Technology) Fachhochschule Lippe und Höxter, University of Applied Science
Simon Kern: (formerly DaimlerChrysler Research and Technology) Darmstadt University of Technology
Prof. Dr. Hans-Christian Pflug: DaimlerChrysler, Advanced engineering truck group
Helmut Porod: DaimlerChrysler, Advanced engineering truck group Germany
More Stories
Cybord warns of dangers of the stability illusion
Automotive Industries interviews Bahar Sadeghi, Technical Director, Car Connectivity Consortium (CCC)
Hexagon’s MAESTRO reinvents CMM systems through digitization