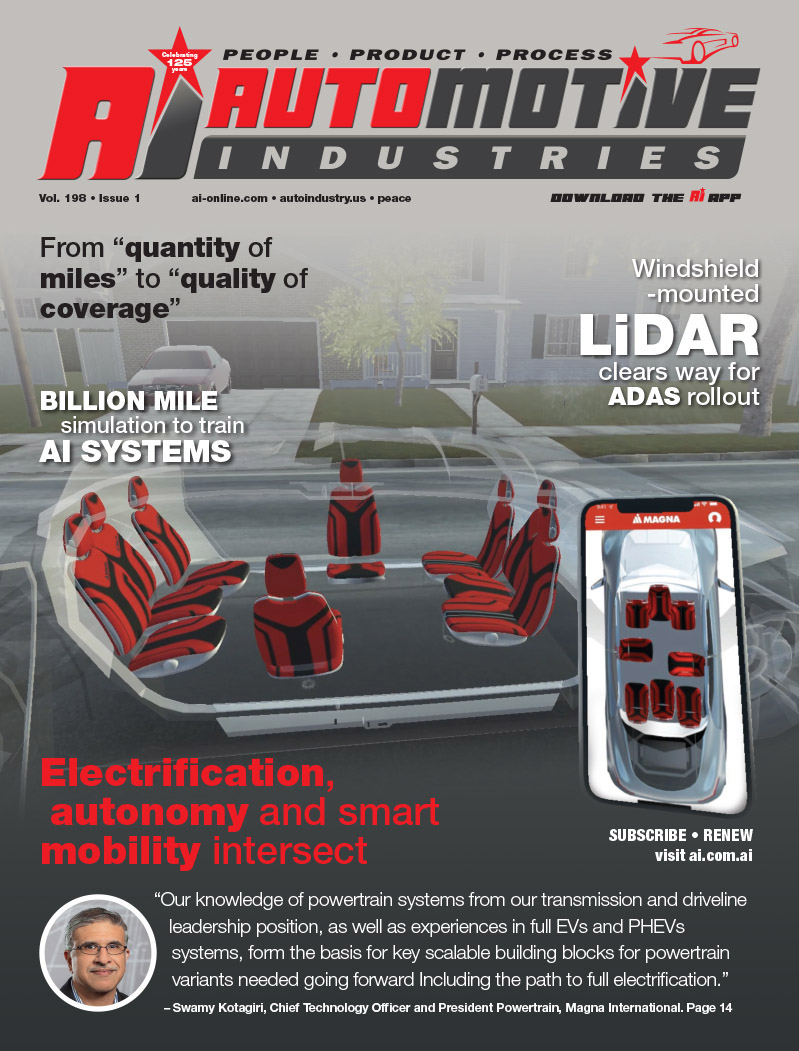
An advanced Resin Transfer Molding system (Advanced RTM) developed by the ATR Group and Huntsman Advanced Materials has been used on an award winning prototype engine air box for the Ferrari F430.
ATR is an Italian consortium comprising nine leading companies involved in the research and production of advanced structural composite parts and components. Using ATR’s advanced RTM technology and a new epoxy resin system – XB 3583/Aradur 3486/ LMB 6432 from Huntsman Advanced Materials – it was possible to build the highly complex prototype of the engine air box. The process won the highly prestigious 2006 China Composites Expo-JEC Innovation Award for the best application for FRP/Composites Production in September 2006.
RTM is a molding process in which a catalyzed resin is transferred into an enclosed mould, lined with reinforced fibrous material. It then may or may not be heated to complete the molding process. The main benefit of RTM is that it combines relatively low cost tooling and equipment costs with the ability to consolidate large structural parts.
ATR’s advanced RTM system, in combination with Huntsman’s resin system XB 3585/ Aradur 3486/ LMB 6432, enables the production of detailed composite parts in a single operation. It also reduces the weight of the part by minimizing the amount of resin used.
With the Ferrari F430 engine air box, the weight of the finished prototype part was virtually halved from the aluminum original – from 4.1kg to just 2.4kg. This was achieved by using a special, flexible silicone membrane rather than the usual metal mould, enabling the resin content to be reduced and the reinforced fiber content to be increased. The complex part was so accurate that even the engine flange drill holes matched up with no further finishing required.
No additional bonding was needed either to add connecting parts such as inserts and internal auxiliary structures as they were formed in the mould during the RTM process. Abramo Levato, R&D Manager at ATR Group said: “With our significant advancement in RTM technology combined with the Huntsman Advanced Materials resin system, it is possible to produce highly complex, yet lightweight composite parts in a single shot. This versatile laminating system makes Advanced RTM an even more time and cost effective manufacturing option for our customers.â€
The striking new IZANA sports coupe is the latest innovative concept car from SIVAX, one of Japan’s leading automotive design and prototype production companies. The four-seater, gull-winged door sports coupe was launched to great acclaim at the Paris Motor Show in October 2006. It goes further in flawless design terms than any of its illustrious predecessors. “Huntsman Advanced Materials BM 5025 boards and the Araldite® LY 5052/Aradur HY5052 laminating system proved ideally matched to meet our very demanding standards,†says Tomohiro Onuma, Manager for Model Production at the SIVAX R&D Centre.
“The boards have excellent mechanical properties – tough and durable, yet lightweight and easy to machine or hand finish to any design refinements with very little waste. “With the laminating resin system, we were also able to achieve an unprecedented level of design and surface quality finish for the IZANA models.â€
“The IZANA is one of our most ambitious creations yet – subtly blending Japanese and Western design cultures,†says Onuma. “Huntsman Advanced Materials has played an important part in the success of this project – not only with the versatility and consistently high quality of the materials they supplied, but with the technical data and support the Huntsman team provided as well.â€
More Stories
Towing Services Explained: 6 Key Facts You Need to Know
Environmental Factors That Influence Ceramic Coating Choices
Professional vs. DIY Tinting: What You Should Know