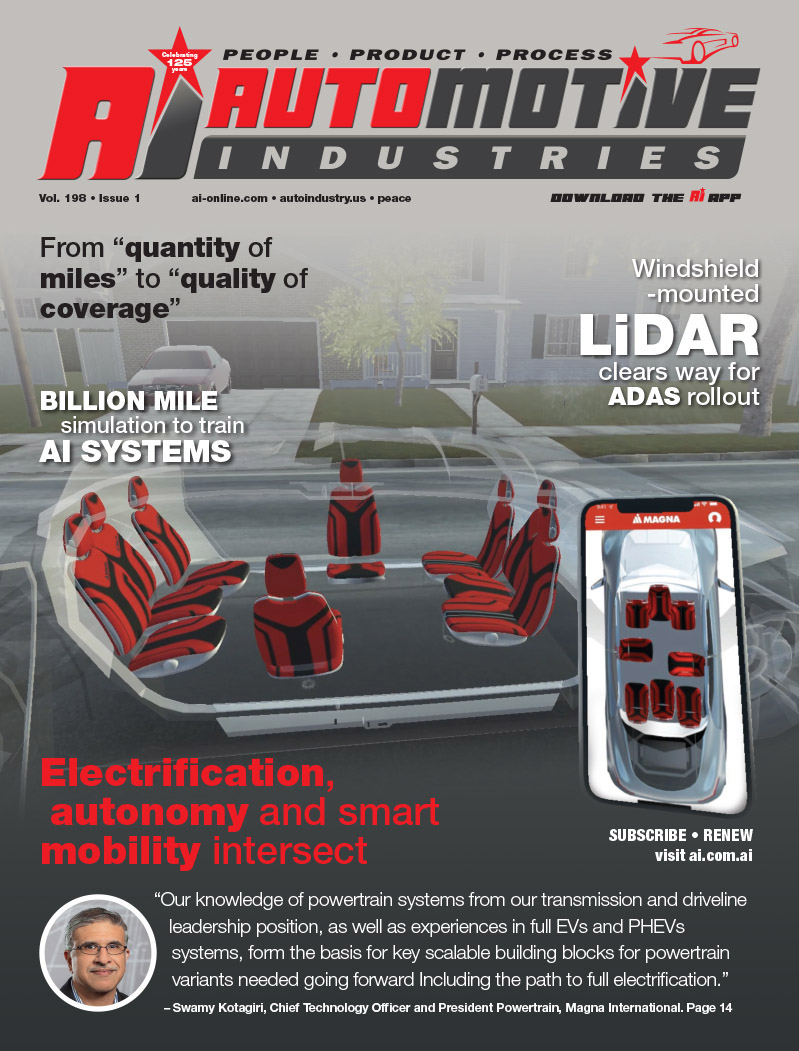
The Center for Advanced Vehicular Systems (CAVS) at Mississippi State University (MSU) is an interdisciplinary center that provides engineering research and development teams focused on complex technical problems.
It aims to provide short-term solutions relevant to manufacturers, while the research builds longer-term knowledge needed for sustained economic development. CAVS operates research facilities on campus, in the adjacent Thad Cochran Research and Technology Park, and in Canton, MS, near Nissan’s manufacturing facility. Annual expenditures are passing $20 million with 225 students, staff, and faculty involved in the program. The vehicle testing capabilities are evident by the rather unique collection of tools, including a four-wheel drive dynamometer, engine dynamometers, materials testing laboratories, and a collection of tension, fatigue, corrosion, and high strain rate test stands.
The computational manufacturing and design effort at CAVS couples multidisciplinary research of solid mechanics, materials, physics, and applied mathematics in three synergistic areas: theoretical modeling, experimentation, and large scale parallel simulations.
Currently, CAVS’ design and computational manufacturing partners involve most of the major auto firms, several software vendors, regional manufacturers, and a variety of other sponsors such as Alcoa, Instron, Viking Range, Allegheny Technologies, Northrop Grumman, and the Center for Powder Metallurgy Technologies.
CAVS’ projects also include the development of vehicle system power electronics that use the latest advancements in silicon carbide semiconductors. A critical technology in the use of SiC was developed at MSU. Newly developed hardware is being integrated into military vehicles such as the popular High Mobility, Multi-Wheeled Vehicle or Humvee. CAVS supports spin-off companies, such as SemiSouth, also located within the research park where the main research facilities are housed.
Work on Alternative Power Systems (APS) includes developing new technologies to achieve higher fuel efficiency and cut pollution, by using advanced controls and renewable energy. This is accomplished through modeling and simulations of power train and bio-diesel hybrid technologies, including electric motor propulsion, power electronic switching, and electronic control systems. This research is currently funded by the Air Force Research Laboratories and the United States Army Space and Missile Defense Command. This hot topic has recently attracted additional funding from the Propane Education and Research Council, Office of Naval Research, and the U.S. Army TARDEC.
A major focus is on Hybrid Vehicle Design, exemplified by participation in the Challenge X Project. This project is sponsored by the U.S. Department of Energy, General Motors Corporation, and other major automotive related companies. The competition gives selected engineering schools an opportunity for students to participate in hands-on research and development with leading-edge automotive propulsion, fuels, materials, and emissions-control technologies. MSU is one of 17 teams taking part in this four-year competition. The MSU team is compiled of students from various disciplines in the James Bagley College of Engineering and the College of Business and Industry at Mississippi State.
“We strive to be a recognized leader in virtual manufacturing and design. We are synergizing our education and research efforts toward a broad range of industries – automotive, materials, aerospace, electronics, and manufacturing. An early partner in this effort is Oak Ridge National Laboratory. Our research niche is based upon a multi-scale methodology that couples theory, simulation, and experiments, from the large structural scale down to the nanoscale. This multi-scale methodology captures the ‘cradle-to-grave’ cycle of engineering systems. We are working very hard to keep our research relevant to industry,†states Bob Kirkland, Business Development Officer for CAVS.
Automotive Industries interviewed Rand German, CAVS’ Director and Chaired Professor of Mechanical Engineering.
AI: How do CAVS solutions for Challenge X compare to the other 16 teams?
German: Under the leadership of graduate student David Oglesby and faculty advisor Marshall Molen, the MSU team has made great achievements in our first-time competition. The competition allows us to focus a multi-disciplinary team of students on the task of redesigning a 2005 Chevrolet Equinox into a cleaner, more efficient vehicle without compromising performance or consumer acceptability. After two years, we are ranked third overall and our vehicle placed first in performance at GM’s proving ground in Mesa, Arizona. We are using Challenge X as a means to train a cadre of students in project work beyond classroom learning. This is probably more important to us compared to some of the schools with multiple competitions under their belt. We have proven to be one of the leaders in this competition.
AI: Have any of CAVS technologies been incorporated into automobiles? If so, which ones?
German: For a newer R&D center, CAVS already has some notable successes. Our USCAR structural cast magnesium development project worked on a Corvette front engine cradle. The redesign involved finding solutions to many issues prior to entering production in 2006. However, many of our contributions are nearly invisible, such as silicon carbide electronic modules in hybrid motor controls, vehicle design optimization for crashworthiness, improved occupant restraint, interior control concepts to better handle fogging, new driver control systems, lightweight materials and designs, and even some “black box †technologies. With respect to military vehicles, we made significant contributions associated with field repair (laser sintering), 10 kW on-board power generation, and prognostication and field readiness.
AI: What are some of the cutting edge automotive technologies CAVS is working with and on?
German: One of our surprising early successes was in advanced learning technologies, helping train manufacturers, repair technicians, and disaster response personnel. One of our newer activities relates to training police forces using our advanced simulators and research in human factors. We also have leading-edge efforts based on diverse fields such as friction spot welding. Our largest projects deal with automotive applications for lightweight materials based on composites or alloys of titanium, magnesium, and aluminum. For example, we are designing new magnesium alloys from basic atomic scale simulations and developing parallel to each other, forming technologies and subsequent optimized designs with these new materials. All of this leads to new courses that range from six-sigma quality to welding. Power electronics based on silicon carbide is progressing rapidly, but with this success comes some real research challenges in heat dissipation that leads to a need for design and low-cost composition innovations.
AI: Will CAVS be partnering with automotive companies in the future and if so, which ones?
German: Since many of the principles at CAVS were very successful prior to joining Mississippi State University, they brought along well-established relations with the automotive industry. Yes, we are partnering with many companies and our relations are pervasive. For example, I personally was supported by GM, Ford, Cummins, Daimler Chrysler, John Deere, and others prior to my move here in 2005. Such relations persist because of the talent and track record of our principles. Although CAVS is relatively new, our relations are long-established.
For more information, visit www.cavs.msstate.edu.
Toyota chooses Mississippi
In February 27th, the State of Mississippi and Toyota announced that Toyota had selected the Wellspring Megasite near Blue Springs, MS (northwest of Tupelo, MS) for its new $829 million manufacturing plant for the Highlander SUVs. The Toyota facility would open in 2009 and have a production capacity of 150,000 vehicles and about 2,000 workers.
Automotive suppliers could provide an additional 2,000 spinoff jobs.
CAVS support
CAVS employs specialist research teams in the following areas:
Advanced Learning Technologies – In a technologically advanced society, the team recognizes the human component as critical in product design and manufacturing. It researches and develops advanced learning systems based on this fact.
Alternative Power Systems – The goal of this team is to achieve higher fuel efficiency and reduce pollution using advanced controls and renewable energy. This is accomplished through the modeling and simulation of power train and bio-diesel hybrid technologies.
Computational Manufacturing & Design – This team uses a multidisciplinary approach in the following three synergistic areas: theoretical modeling, experimentation, and large scale parallel computational simulation. It aims to provide solutions to the automotive industry from the manufacturing process to supplying aftermarket information.
Cooperative Computing – The long term goal of the team is to provide support for system-level science. System-Level Science is the broad understanding of how complex, multiphenomena physical systems behave and how their constituent components interact and interrelate.
Extension & Outreach Service – This team focuses on providing advanced technical expertise to Mississippi’s emerging automotive industry, other OEM’s and small to medium size manufacturers. It specializes in the areas of product and process improvement, professional development education and training, and technology transfer.
Human and Systems Engineering – This team also recognizes the importance of the human component in product and process design. It uses a multidisciplinary approach as well as traditional engineering methods to research ergonomics, cognitive science, learning and training systems, human-machine interfaces, telematics, and advanced computing technologies.
Materials Processing – This team is based on partnerships between universities, industry, government agencies and professional and trade associations. It aims to develop cutting-edge technology for the processing of engineering materials.
More Stories
Towing Services Explained: 6 Key Facts You Need to Know
Environmental Factors That Influence Ceramic Coating Choices
Professional vs. DIY Tinting: What You Should Know