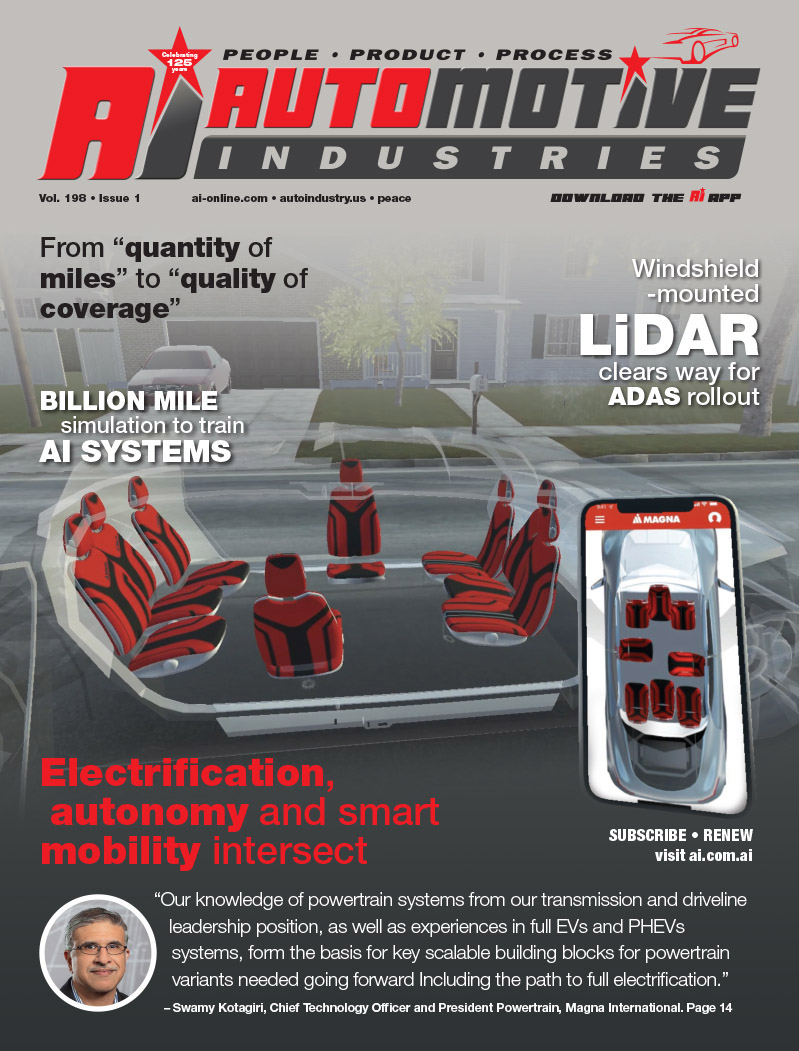
In the old Frank Sinatra song “High Hopes,” various animals look to perform seemingly impossible tasks, such as the “little ol’ ant” moving a rubber tree plant. While no one gives them much chance of succeeding, through sheer will and perseverance they are able to prevail against the odds and do what they set out to do.
A new stereolithography resin introduced in 2006 by DSM Somos® is helping investment casting foundries move their own version of the rubber tree plant. Antimony-free ProtocastT AF 19120 combined with the QuickCast® method of building patterns allows the low volume production of parts in virtually any alloy without the concern of degraded material properties. In addition, the removal of antimony automatically eliminates much of the ash created during burnout of patterns, simplifying clean-up and helping get the mold ready for production faster. In short, it removes many of the limitations that have restricted engineers in the past, ushering in a whole new era of metal part design possibilities.
Why Antimony Is Used
Traditionally, stereolithography (SL) resins used for direct casting have always contained antimony. Antimony is used as the photo-initiator that converts the liquid resin to a solid when exposed to ultraviolet light during the SL process. In today’s rapid prototyping industry, however, many direct cast patterns are created using the QuickCast process. This process creates a lightweight shell with a honeycomb infrastructure that provides ample strength for mold creation, yet allows the pattern to collapse inward on itself during burnout in order to prevent damage to the ceramic mold. When the pattern is burned out, it leaves a residue of ash or oxide – most of which is made up of antimony.
Having an antimony-free resin simplifies the post-mold creation clean-up process by removing as much as 80 percent of the ash normally left behind. This greatly reduces the chance of blemishes appearing on the cast part, assuring it will require less reworking to finished form. In short, engineers can now take advantage of the benefits of the QuickCast process without concerning themselves as to whether there is antimony left over. It can’t be left over if it wasn’t there in the first place.
ProtoCastT AF 19120 Advantages
Low ash content of burned out patterns allows engineers the ability to take advantage of the direct casting process for a wider variety of alloys, from Aluminum to Titanium. This provides time and cost savings over machining molds. An investment cast part made using ProtoCast AF and the direct casting method can be produced in as little as four weeks, even on the most complex geometries. Compare that to the 20 to 30 weeks required for a similarly complex part with a machined mold.
This faster, less expensive process yields several benefits for industries such as luxury automotive, aerospace, motor sports and medical, including:
Shorter product development times:
1. Spend less time removing fewer blemishes.
2. Create and test several design variations at once, rather than using the one-at-a-time, iterative process that is currently the norm on high-performance parts.
3. Generate short production runs in order to gain a first move advantage in the market while a more permanent traditional mold is being created
Cost-effective customization:
1. Customize castings to particular customer requirements rather than needing a high minimum volume to meet cost projections.
2. Create single, customer-specific castings efficiently. In the medical field, for example, a doctor performing a knee replacement can conceivably take an X-ray of the current knee and have a titanium replacement created that matches it exactly, rather than being limited to a choice of 15 generic knee designs that then have to be adjusted to the patient.
Using a QuickCast pattern also means designs can have more complex features (such as undercuts) that cannot be incorporated into a traditional, two-piece machined mold. There are virtually no limitations on the design of the part, allowing engineers to optimize the casting for the job instead of the mold-making process. All of this is made possible by removing the antimony from the resin, thus widening the range of alloys that can be investment cast using direct cast patterns.
Unbridled Optimism
While every design process begins with “high hopes,”, the realities of the real world often bring those hopes crashing down. The introduction of antimony-free resins such as Somos ProtoCastT AF 19120 will now allow design engineers to do things with investment casting they never would have considered before, opening their eyes to all kinds of new possibilities. A comprehensive investment casting guide describing the time saving benefits of direct casting with ProtoCast AF 19120 has been written and is available either through DSM Somos or Express Pattern.
More Stories
Professional vs. DIY Tinting: What You Should Know
New updated edition of “PXIMate” reference guide for T&M engineers available from Pickering Interfaces
5 Mistakes That Can Ruin Your Car Accident Claim