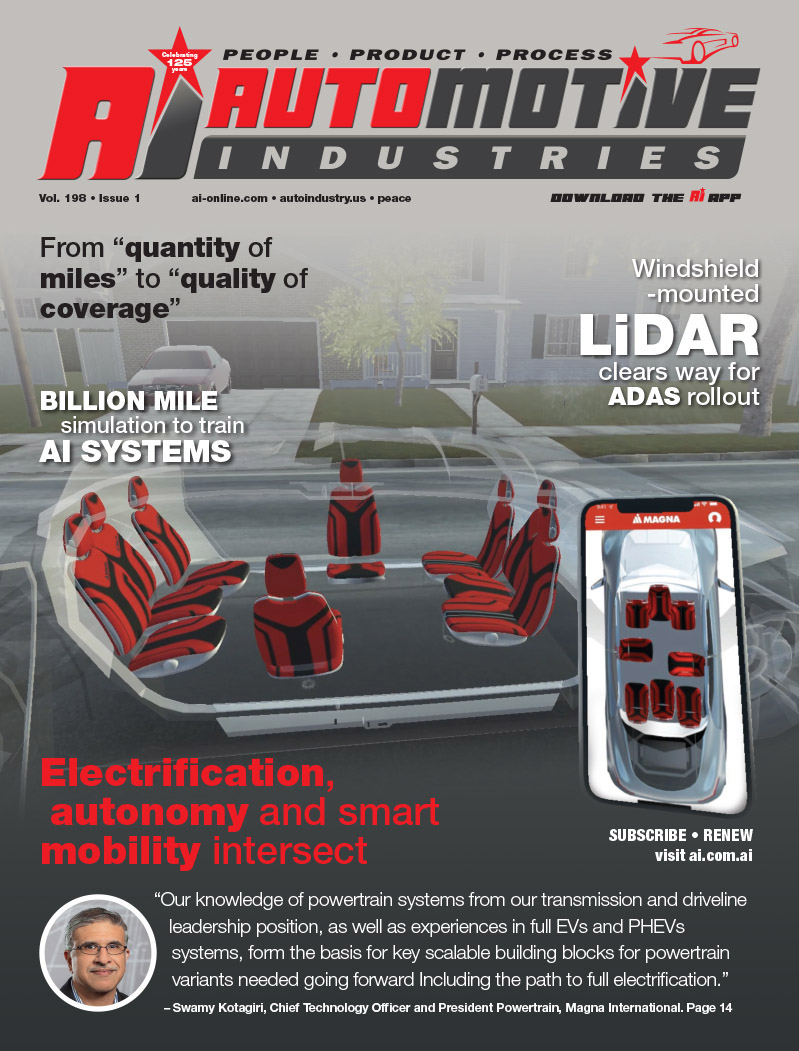
The world aluminium industry reported today that the application of automotive aluminium in passenger cars manufactured in 2006 will lead to potential global savings of approximately 140 million tons of CO2 equivalent greenhouse gas (GHG) emissions and to energy savings equivalent to about 60 billion litres of crude oil over the lifecycle of these vehicles.
“The GHG reductions and fuel savings are the result of weight reduction achieved through the application of aluminium by the world’s automakers,” according to Robert Chase, Secretary General of the International Aluminium Institute (IAI).
These energy savings and emissions reduction numbers were included in a presentation by Marlen Bertram, IAI research associate, at the 2007 China Aluminium & Transportation Conference in Dalian, China, entitled “Improving Sustainability in the Transport Sector Through Weight Reduction and the Application of Aluminium”.
As part of her presentation, she reviewed the results of a study by the Institute for Energy and Environmental Research (IFEU) in Heidelberg, Germany, that concluded lightweighting the world’s transportation fleet – passenger cars, trucks, rail vehicles, air and sea craft – has the potential of reducing GHG emissions by 660 million tons annually, or close to 9% of global, transportation-related GHG emissions.
Ms. Bertram presented several case studies demonstrating aluminium’s capacity to reduce weight in real-world vehicle applications.
“Our results are based on data from the IFEU study and a lifecycle model developed by the aluminium industry. This model accounts for all greenhouse gases emitted during aluminium production, vehicle use and end-of-life processing. It has also been tailored for component-specific applications on passenger vehicles.
“All our analyses are based on publicly-available information concerning weight reduction achieved through the application of aluminium. Our model adheres to the principles of lifecycle assessment per ISO standard 14044,” she added.
The actual IAI study is available on the IAI website: www.world-aluminium.org.
The study also compared aluminium versus high strength steels in two applications: a bumper beam on two similar European-made cars (one using high strength steel the other aluminium) and a hood on a US-made family sedan. In both applications, aluminium achieved significant energy and emissions savings.
The aluminium bumper beam saved 2.6 kilograms (kg) over the high-strength steel beam. Over a 200,000 kilometer (km) driving cycle of these compact vehicles, the aluminium bumper beam will reduce GHG emissions by 15 kg per kilogram of aluminium, or 48 kg for the bumper.
The aluminium hood on the US-manufactured family sedan registered a 42% direct weight reduction over high-strength steel. Over the 200,000 km driving cycle of this vehicle, this hood will reduce CO2 equivalent emissions by 131 kg.
The introduction of a single aluminium bumper beam or a hood offers little or no potential for indirect, or secondary, weight savings, whereas a combination of replacements or an all-aluminium body structure enable secondary weight savings of the order of 50% or more. For instance, when the secondary weight savings of the bumper and hood are included in the model, the CO2 equivalent emissions reductions increase to 61 and 161 kg, respectively.
The aluminium industry’s study also revealed that each ton of the light metal replacing iron in engine blocks has the potential to save the energy equivalent of 8,000 litres of crude oil over its lifecycle. According to a 2006 study by Ducker Worldwide, 45 kg of aluminium were put into each car and light truck in form of engine blocks in 2006, resulting in the energy savings equivalent to 375 liters of crude oil per vehicle for this application alone.
“These data underpin the key role that aluminium can play in reducing GHG emissions form transport. They also further the 15 objectives of the industry’s global sustainability program, Aluminium for Future Generations,” the IAI’s Chase concluded.
The full report also addresses the issue of vehicle size and weight as important elements of sustainable transportation. It presents the results of a previous study done by Dynamic Research Institute (DRI) where size and weight were key variables in 500 “virtual” collisions.
The study concluded that both vehicle weight and size were key elements in producing passenger vehicles that reduce crash energy to save lives. The study demonstrated that maintaining vehicle size while reducing its weight reduces the energy it has to absorb in a crash and making it less damaging to other vehicles in a collision.
The study also shows that if lightweight structural materials, such as aluminium, are used to increase a vehicle’s crush zones, even by several centimeters, significant improvements in safety can be achieved without increasing vehicle weight.
Aluminium is all around us. It is light and strong, corrosion resistant and durable, formable and highly conductive, it has natural shine and is recyclable. Aluminium provides intelligent solutions for present and future generations.
The European Aluminium Association, founded in 1981, represents the European aluminium industry from alumina and primary production to semi- finished and end-use products, through to recycling. The European aluminium industry directly employs about 236,000 people.
The IAI is the global forum of aluminium producers dedicated to the development and wider use of aluminium as a competitive and uniquely valuable material. The IAI in all its activities supports the concept that aluminium is a material that lends itself to improving world living standards and developing a better and sustainable world environment.
The IAI reflects the aluminium industry’s wish to promote wider understanding of its activities and its responsibility of approach on questions of environmental protection, public health and safety in the workplace.
The Aluminum Association, based in Arlington, VA, with offices in Detroit, MI, represents U.S. and foreign based primary producers of aluminum, aluminum recyclers and producers of semi-fabricated products as well as suppliers to the industry. Member companies operate almost 200 plants in North America and many conduct business worldwide.
More Stories
Automotive Industries (AI) Newsletter April 2025
Bangkok International Motor Show 2025 – The Talk of Sensuous Automotive
Earn GHG reduction values through MOL Pure Car Carrier “Book and Claim (B&C)” service