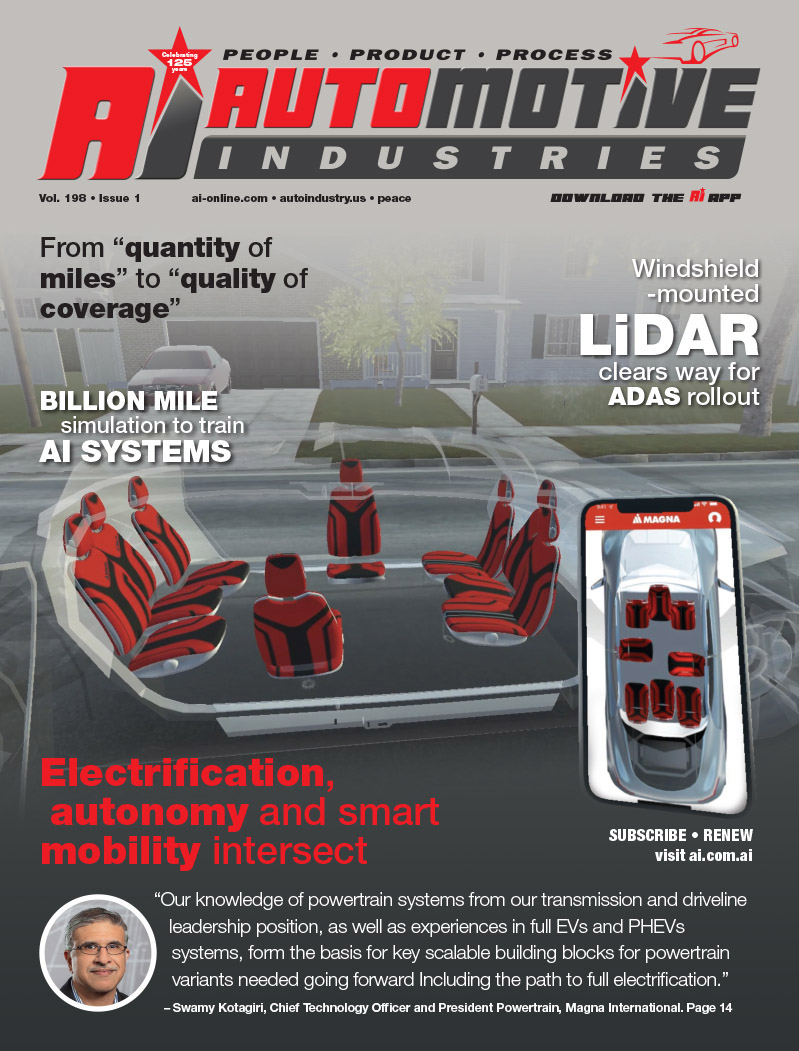
Critical bolted joints often require exacting tightening procedures to establish the optimum clamp load. While tightening by torque wrenching methods is quick and easy, extensive tests have shown that a given torque can produce tensions or clamp forces varying by as much as 5 to 1 depending on bolt plating, lubrication, thread condition, nut and washer material and seventy-one other variables according to a US Air Force study.
A Direct Tension Indicator (DTI) can remove this uncertainty, since it responds only to bolt tension and not to torque.
DTI SmartBoltsâ were invented by Stress Indicators, Inc of Bethesda, MD to set up the proper bolt tension with no need for torque wrenches, strain gages, wires, electronic or ultrasonic equipment. In fact, there is no need to touch or contact the fastener at all in order to verify its clamp load condition. A glance is sufficient. DTI SmartBoltsâ provide an eye-catching visual indication of the tension in the fastener at installation or at any later time, and the degree of bolt tension may be estimated by the indicator color.
The indication is a bright red when loose, and gradually darkens to a deep black as the bolt is tightened. Operation is completely reversible- SmartBolts can be tightened and loosened thousands of times without any degradation or loss of accuracy. A loose fastener is obvious even at a distance or, in some cases, in moving machinery. The standard tension accuracy is specified to be ±10%.
The main limitation of the DTI SmartBolt color-change scheme is that the indicator is not designed to show an over-tension condition. Once design tension is achieved, the indicator will remain black if it is tightened further thus giving no indication of over-tension. Another limitation is that the color change associated with a loss of, say, 10% of tension may be difficult to resolve in real world conditions.
The new HR (High Resolution) SmartBolt was developed to transcend these limitations. The HR SmartBolt is armed with a sensitive optical microindicator element that allows quick-look inspection—Green is Go! The simple yet sophisticated indicator, located in the center of the bolt head, remains yellow as the fastener elongates while being initially tightened. When about 85 percent of the design tension has been achieved, the indicator rapidly turns to a bright green at 100%. When tightened beyond design specifications, the indicator darkens until it is nearly black. More importantly, should the bolt loosen more than 10-15 %, the indicator returns to bright yellow, warning observers of a problem.
The color-coded system is ideal for critical inspections. Once the bolt is installed, the proper tension may be verified without contact or loosening of fasteners. It also means that loosened fasteners in critical situations may be easily identified and corrected, thereby averting catastrophic incidents.
The HR SmartBolt indicates bolt tension through direct measurement of bolt elongation. Accuracy is improved over the DTI SmartBolt because each bolt is calibrated at design tension during assembly. The HR indicator is sensitive to an elongation of 60 millionths of an inch, which corresponds to a tension precision of around 2% when installed in high-strength bolts. If the indicator is “grass green” you can be certain that the bolt is doing its job!
Torque wrenches, on the other hand, respond only to the applied torque, which is only weakly related to tension. A large part of this torque, as much as 80-90%, is required to overcome friction, which can vary significantly in different situations. The result is that a perfectly accurate torque wrench may produce errors in bolt tension as much as 25-50%, according to many engineering studies
In contrast to torque wrenching, SmartBolt’s clamp load is independent of friction and remains reliable and reproducible through countless cycles of tightening and loosening. The process is completely reversible and there are no moving parts to wear out. Twenty-year-old DTI SmartBolts still operate as reliably as when they were new. A life expectancy exceeding 20 years is similarly forecast for the HR bolts, since they use the same inert materials and components.
The HR SmartBolt is a significant upgrade of the flagship DTI SmartBolt. Besides being more accurate, they are easier to read. However, the original DTI SmartBolts are still appropriate for less demanding applications, and remain the choice of companies such as General Electric, Texas Eastman Chemical, Rockwell Collins and the National Weather Service.
In fact, GE Busway, the Electrical Distribution division of General Electric, has used DTI SmartBolts in their Spectra Series Busway systems since 1997. The fasteners are used to join modular electrical conductors that supply power throughout industrial plants.
DTI SmartBolts make inspection of these high-voltage busway joints high in the plant’s overhead easier and safer and provide visual joint integrity assurance.
The potential of the HR SmartBolt has garnered the interest of the U.S. Army, which is now evaluating the fastener technology for possible use on Apache helicopters, as well as other military applications.
SmartBolts have also been critically analyzed in a report by the Electric Power Research Institute (EPRI). This nonprofit group conducts research on key issues facing the electric power industry on behalf of its members and society. The report concluded that SmartBolts products could be a cost-effective means to reduce radiation exposure for nuclear power plant personnel. SmartBolts have survived intensive test radiation exposure, and will soon be installed in nuclear plants for further evaluation.
Customers are enthusiastic that the HR SmartBolt will be ideal for rugged applications that require precise information about fastener tension for critical applications. This includes such industries as aerospace, petroleum, materials processing, power generation, chemical processing, transportation, rail, and off-road and heavy equipment. The HR SmartBolt promises to provide customers in many industries with unprecedented knowledge about fastener tension in critical joints
More Stories
Professional vs. DIY Tinting: What You Should Know
New updated edition of “PXIMate” reference guide for T&M engineers available from Pickering Interfaces
5 Mistakes That Can Ruin Your Car Accident Claim