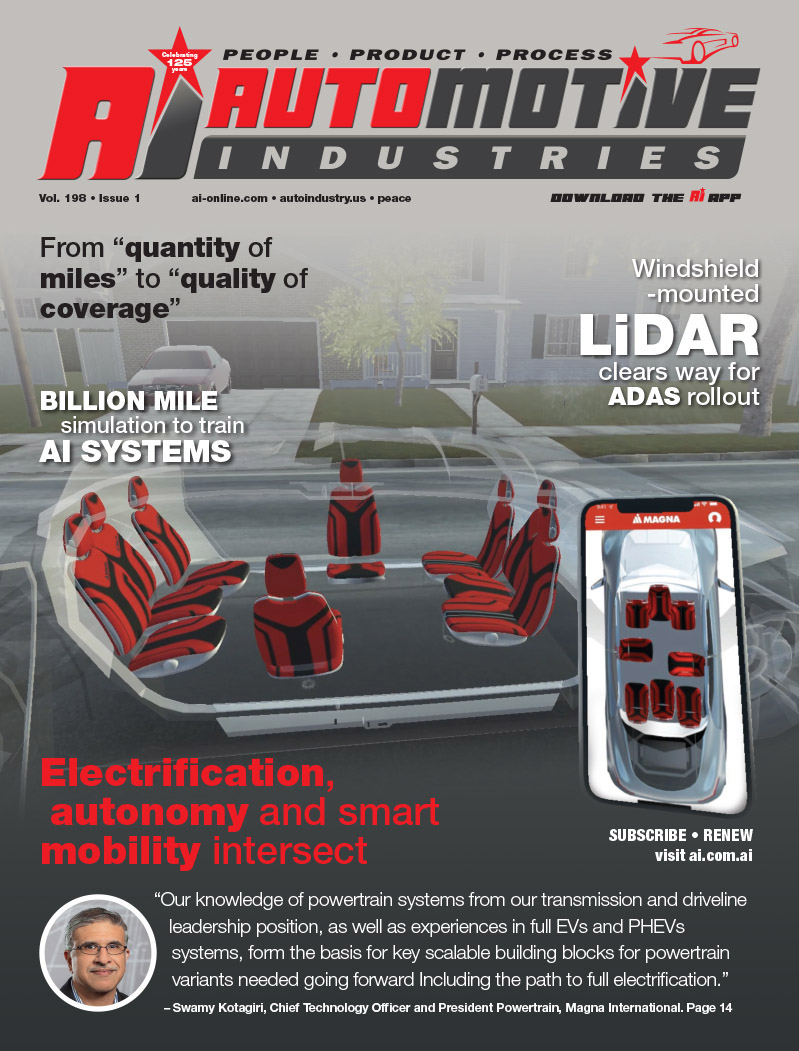
CVRD Inco Special Products of Canada has developed a uniform, porous metal alloy foam that is designed for deep bed diesel exhaust treatment systems. The patented powder metallurgical process transforms nickel foam into a true homogeneous alloy foam substrate.
CVRD Inco Limited, formerly Inco Limited, is a subsidiary of Companhia Vale do Rio Doce (CVRD) of Brazil.
Automotive Industries (AI) spoke to Dirk Naumann, Director of New Technology at CVRD Inco Special Products, and asked him about recent innovations in nickel technology.
Naumann: These include traditional areas of expertise, such as energy storage, where we have developed materials which significantly increase rechargeable battery capacity, and powder metallurgy, where we have developed specialty nickel powders to enhance their blending characteristics, resulting in improved strength and consistency of alloys used in near net shape part production. Most exciting of all are the advances we have made in alloy foams. These porous metallic structures can be formulated to provide high temperature and corrosion resistance in material formulations optimized for many different applications. Initially these foams will change the way in which diesel exhaust emissions are treated, but will progress to be used in industrial catalyst, heat and mass transfer applications, amongst others.
AI: What research are you doing into rechargeable batteries and fuel cells?
Naumann: CVRD Inco has research programs to improve the storage capacity, useful life and cost effectiveness of its energy materials. We work closely with the major battery makers in collaborative programs where our technologies and expertise complement one another.
AI: What is your involvement in hybrid engine technology and emission control?
Naumann: A critical technology behind hybrid systems is the performance of the power storage device in terms of their capacity and charge/discharge rates. CVRD Inco has a strong commitment to hybrid engine technologies and is working with specialized battery and car makers to improve performance and build on an increasing environmentally conscious consumer base.
Hybrids combine internal combustion and electrical drive systems. In addition to its contribution to the electrical development, CVRD Inco is cleaning up the engine exhaust. CVRD Inco’s new alloy foam offers the potential for smaller and more effective NOx reduction components, meeting environmental and cost concerns.
AI: Now that CVRD and Inco have merged, have your automotive capabilities been ramped up and how?
Naumann: CVRD Inco has built its automotive capabilities over many years and, within certain applications areas, has developed an expert knowledge. The use of groundbreaking emission control materials in the growing diesel exhaust treatment segment has required a focusing of established materials technology platforms and the development of new skills in emission controls. We have worked hard to identify and recruit innovative and open minded automotive engineers and managers. We continue to build our relationships with key partners in the supply chain.
AI: What are some of CVRD Inco’s future focus areas?
Naumann: Regarding emissions control, CVRD Inco’s future focus is on DeNOx applications where the high surface area and good mass transfer properties of the foam can bring volume and system cost reduction benefits to selective catalytic reduction (SCR) and NOx adsorption technologies. With appropriate modification to the alloy composition to suit the different operating conditions, gasoline 3-way catalyst substrates also offer potential for the future.
More Stories
MESSRING completes new crash test facility for Mahindra in India
ROHM Develops an Ultra-Compact MOSFET Featuring Industry-Leading* Low ON-Resistance Ideal for Fast Charging Applications
More than 30 of the top 50 global suppliers have production facilities in Turkey