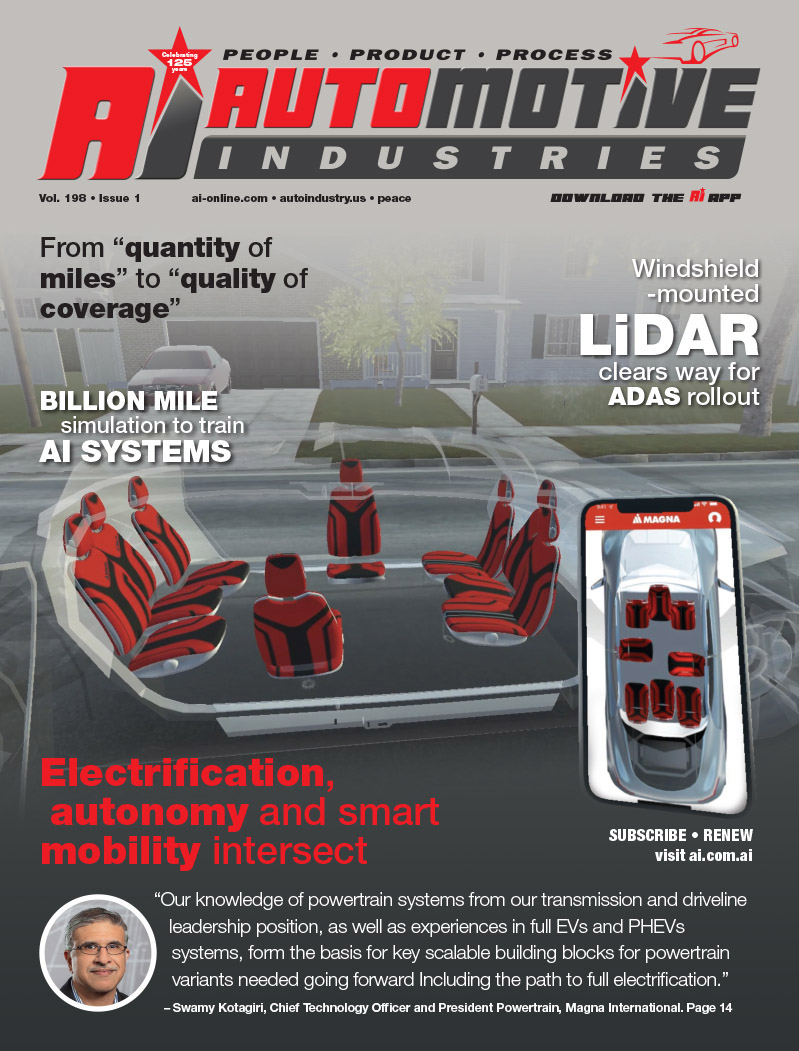
The Italian software company, ESTECO, a world leader in the field of Process Integration and Design Optimization (PIDO) tools, recently announced the release of the latest version of its flagship product, modeFRONTIERâ„¢. The foremost multi-objective optimization and design environment for process integration, modeFRONTIERâ„¢ provides the user with a set of building blocks to enable the creation of sophisticated workflows to integrate all the software components of a design process, as well as a set of state-of-the-art algorithms (for either single or multi-objective optimization) and extensive post-processing and decision support capabilities. modeFRONTIERâ„¢ was born in a European Union project, funded partly by industrial collaborators (such as British Aerospace and Daimler Chrysler Aerospace) and partly by the EU government. The project, headed by Professor Carlo Poloni, now CEO of ESTECO, addressed the need, primarily in the aerospace industry, for a process integration platform which was also capable of providing true multi-objective optimization and extensive decision-making capabilities. In this respect, modeFRONTIERâ„¢, which became a commercial PIDO software in 1999, was at the forefront of the field. Other tools available at the time were solving multi-objective optimization problems by reducing all objectives to a single objective function to be solved using mono-objective algorithms. modeFRONTIERâ„¢ has played a ground-breaking role in spreading the industrial use of multi-objective algorithms, such as genetic and evolutionary methods, and Game Theory.
The use of PIDO tools is gaining in popularity as a way to automate and drive simulation-based design processes. Most companies involved in product development already rely heavily on computer aided engineering (CAE) software, such as tools for design (CAD), Finite Element Analysis (FEA), Computational Fluid Dynamics (CFD), and even proprietary software written within companies to address their particular needs. Frequently, however, these analyses are run separately from each other; even in the case where the result of one simulation is to be fed to another (an example would be running a CFD analysis to provide thermal boundary conditions for an FEA analysis) there is often a manual process of extracting the data of interest, and passing the file to the user who will perform the next step of the process. Companies are now recognizing that such procedures should be automated in a way which allows all CAE tools to be run without human intervention, and provides for the transfer of the necessary data files between the components. This is not always a trivial task: in today’s environment, product development is often a global activity, distributed among research and development centers in different countries, and even on different continents. It is not uncommon to have CAE tools installed in multiple locations as well; hence process integration in such cases must involve seamless file transfers, using protocols already in place, but avoiding the need for manual entering of passwords, for example. Automating such design processes can be achieved using the process integration part of modeFRONTIERâ„¢; the initial set-up of a workflow will take time, as every component has to be tested rigorously to ensure robust performance, but the benefits are immense, since the process can then be run in batch hundreds or even thousands of times for different sets of inputs. The inclusion of a host of direct integration nodes in modeFRONTIER allow the user to easily couple in many of the most widely used CAD and CAE tools.
Once the chain of simulations has been automated, it does not take much extra effort to convert it into an optimization process. The user, having specified which design inputs are to be the variables, will also define certain goals, or objectives; for example, to maximize efficiency and minimize cost. Often in real life applications the goals may be conflicting, which brings us to the concept of trade-off: by keeping the objectives separate, multi-objective optimization frequently gives rise to a Pareto Frontier of designs, all of which can be considered to be candidates for the optimum. In fact, the software got its name from the Pareto Frontier; this is to emphasize the fact that we are dealing with true multi-objective optimization. The fact that modeFRONTIERâ„¢ can be used in virtually any field of product development has led ESTECO to forge relationships with a variety of other software suppliers to the automotive industry.
Automotive Industries spoke to Carlo Poloni, CEO of ESTECO
AI: Please help us understand how modeFRONTIERâ„¢ helps companies looking for advanced engineering design solutions.
CP: Using the many direct integration nodes, or by employing ASCII files to link other software, the user can easily create a workflow which combines all components of a design process. Once objectives have been defined (e.g. minimize weight, maximize efficiency, etc), and an optimization algorithm selected, modeFRONTIERâ„¢ will take over, searching for configurations which provide the best compromise between goals which may well be in conflict. By combining ease-of-use with powerful, state-of-the-art optimization algorithms and process integration techniques, modeFRONTIERâ„¢ provides the user with an invaluable aid for product design and development.
AI: How has your affiliation with other software vendors helped ESTECO?
CP: We have both technical and commercial collaborations with 3rd party software vendors; the former involves the creation of direct integrations between their products and ours, while the latter allows those companies also to sell the bundled product (their software together with modeFRONTIER™). As modeFRONTIER™ is a very “horizontal†product, it is not easy for us to be present in all the markets where it could be used; these relationships give us access to new markets which we might otherwise not penetrate.
AI: How have these partnerships helped modeFRONTIER be more useful to the automotive industry?
CP: Our industrial users, many of whom are in the automotive industry, now have a platform to integrate all their CAE tools; moreover, the ability to directly couple many of the most widely used CAE tools in industry makes the creation of the process workflow significantly easier. It should be remembered that modeFRONTIERâ„¢ is, in effect, a robot driving a black box (the analysis programs) which converts inputs (the design variables) into outputs (the metrics by which the system performance can be quantified). For modeFRONTIERâ„¢ it is irrelevant whether the programs being driven are Excel, FEA, in-house programs, financial analysis, or a combination of all of these. The easy-to-use and intuitive GUI is the interface to a powerful environment in which to automate design processes, the optimization “driverâ€, and an extensive toolkit of statistical post-processing and decision-making tools.
AI: Please tell us a little more about the new version of modeFRONTIER.
CP: modeFRONTIERâ„¢ version 4 is a major release with which we are preparing for the future of simulation. Computer hardware is getting increasingly powerful, and already we see that tremendous computing resources are available for all types of simulation, including co-simulation, as part of the product development process. modeFRONTIERâ„¢ 4 is able to harness large quantities of data, and brings sophisticated data mining technology to the desk of designers. This version allows not only optimization but also what we can call “knowledge discoveryâ€; it adds significant new functionality without sacrificing any of the user-friendliness of the previous version.
AI: How popular do you think Version 4 will be to automotive designers? And why?
CP: modeFRONTIERâ„¢ 3 was already very popular among both specialist and non-specialist users; I think version 4 will increase even more the acceptance of PIDO tools within the ranks of optimisation experts, CAE users, and upper level decision makers. Managers will be able to exploit detailed information coming from specialists through the integrated design process. For example, a control engineer will be able to exchange information with a mechanical engineer through high-fidelity models integrated in modeFRONTIERâ„¢, while the decision maker will be able to add financial considerations to best exploit all the data available.
More Stories
Professional vs. DIY Tinting: What You Should Know
New updated edition of “PXIMate” reference guide for T&M engineers available from Pickering Interfaces
5 Mistakes That Can Ruin Your Car Accident Claim