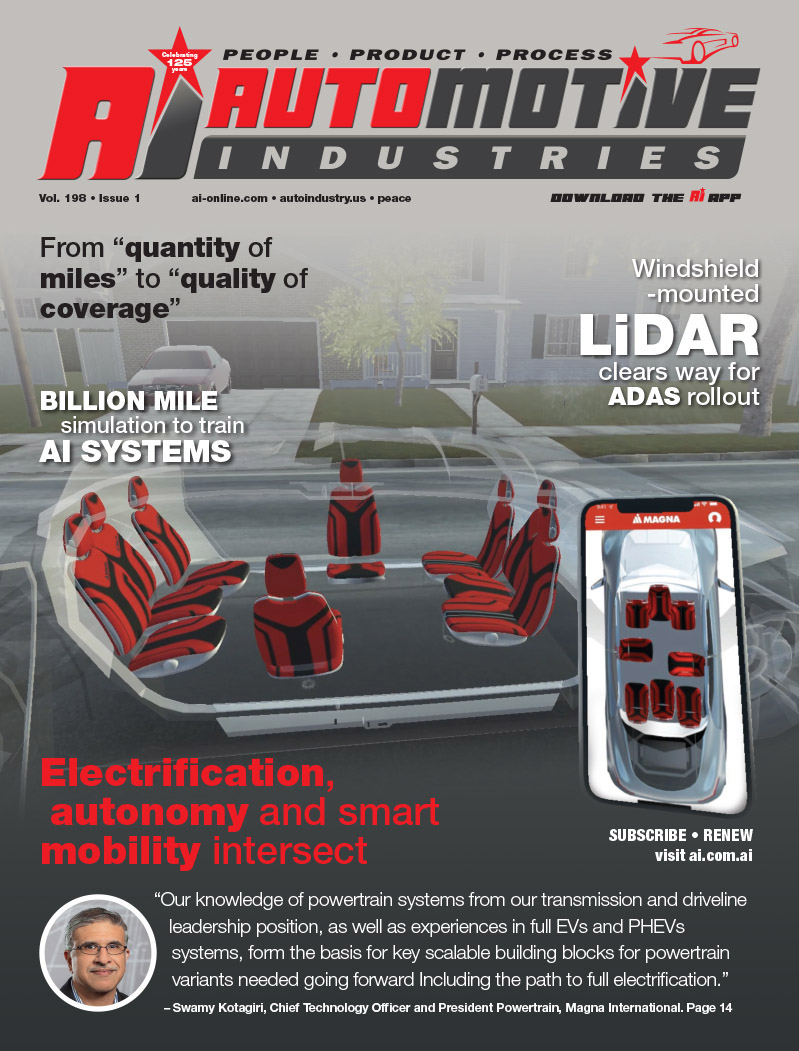
Globalization of the auto industry means that a US company is able to provide automated desktop programming solutions to a major Japanese-based multinational automotive supplier for its Eastern European production plants making electro-mechanical switching and audio car electronics.
“The FLX500 was selected after a careful study of device programming alternatives and was chosen for its excellent fit with the mix and volume needs of our customer. The flexibility of this desktop system, ease of use, and cost-effectiveness over outsourcing and on-board programming were major factors in the selection. This important win further strengthens our growing family of leading automotive customers,” says Harald Weigelt, vice president of worldwide sales and support at Data I/O, which has its headquarters in Redmond and offices in Germany and China.
The company launched its Automotive Performance Programming System (APPS) in 2007. Based on the PS Series platform, it is tailored for automotive original equipment manufacturers as well as Tier 1 and 2 automotive electronics systems companies. Key features of Data I/O’s APPS include a PS FlashCORE Remote Monitoring application that provides managers or clients responsible for production processing residing in remote locations a real-time direct link to the programming activities on the factory floor. Customers can view up to five networked programming systems and monitor the current production activity and yield statistics.
The APPS is Data I/O’s complete automotive industry solution for off-line programming. Whereas other products are targeted at specific needs, the APPS brings them all together in one solution. Individual features of the APPS, such as SPC job logging, remote monitoring, and serial number labeling, were developed at the request of automotive customers and their programming centers, to meet industry requirements for quality, traceability, and version control, says Data I/O.
Automotive Industries caught up with Hume, and asked him to share some of the current challenges facing the in-vehicle electronics market today and what Data I/O’s strategy is in dealing with these problems?
Hume: Industry experts predict that by 2010 nearly ninety percent of automotive innovations will be software driven with the number of programmable microcontrollers and Flash memories per vehicle growing rapidly. The automobile is becoming a very complex electronic system on a grand scale. Every piece of this software must be developed, deployed, and maintained at a very high quality level otherwise the cost of warranty failures makes the business unprofitable. A product recall could destroy a company. As a result we see many changes in the way electronic systems are designed and specified.
For example, DVD players have for a number of years been used to provide the navigation system database. These players, being optical/mechanical systems have difficulty surviving the hostile environments encountered by some vehicles. Most manufacturers have plans to switch to solid state players that use portable memory such as SD or MMC cards to contain the database. Data I/O’s new Flash Media Duplication system provides a solution for duplicating these memory cards for the navigation system manufacturers.
AI: What’s new for Data I/O at this year’s SAE show?
Hume: Data I/O is displaying the ProLINE-RoadRunner solution designed to just-in-time programming. The Roadrunner attaches to pick-and-place machine to program devices at virtually the last possible stage of manufacturing – at the point of placement on a circuit board. This solution eliminates the inventory associated with pre-programmed Microcontroller and Flash Memory devices. It reduces process steps, eliminates the risk that firmware changes will make the pre-programmed devices unusable, and prevents interruptions in the flow of devices.
Our FLX500 automated desktop programming system is for moderate volumes and where minimum changeover time is important due to a moderately high product mix. The FLX500 provides the same high quality programming environment as our larger automated systems at a much lower price point, making it an alternative to error-prone manual programming operations.
AI: Is your company’s approach different when dealing with international customers?
Hume: Our international customers are looking for solutions that are easy-to-learn, easy-to-use and that require a minimum of process integration to adopt. For the FLX500, Data I/O created a language independent graphical user interface that minimizes training time and reduces the cost of adoption.
AI: Last year, the APSS was a big draw, what are some of the new products and innovations that we can expect this year from Data I/O?
Hume: New for 2008 is the FlashCORE II programming engine with Flash boost technology. The FlashCORE II programmer is designed to support the most advanced microcontroller and memory (NAND and NOR) devices and is available in all of our automated programming solutions including the RoadRunner, the PS family, and the FLX500. As automotive electronic systems become more sophisticated, the file sizes grow. This increases programming time and can impact the takt time of the production line. FlashCORE II’s boost technology provides a dramatic improvement in programming speed. For example, using ProLINE-RoadRunner a Samsung K9F2G08UOM-P (2Gbit) device without boost technology takes 151.3 seconds to program/verify four devices. With boost technology the program/verify time is just 32.1 seconds, an improvement of 470%.
PS-Automotive Performance Pak
Data I/O is also introducing its Automotive Performance Pak for the PS-series of automated offline programming systems. It includes application specific software tools to help automotive suppliers trace, monitor, and control the flow of programmable devices from inventory through production. This capability is vital to the prevention of programming errors that could lead to a product recall. If a product recall becomes necessary because of a software bug at some revision level, the software tools allow the user to identify only those products by serial number that are specifically affected.
The Remote Monitor software provides production manages with a direct link to programming activities. Production managers can monitor PS systems remotely and view current job status including devices passed, failed and yield percentages.
Enhanced Statistical Process Control (SPC) tracks the motion of each programmable device and together with system status is recorded in a delimited-text file. This file can be exported to an Access/Excel database or to proprietary SPC tools for process analysis and quality improvements.
Label Generator enables the design and printing of labels for reels of preprogrammed devices. Managers can track programmed components with a barcode ID, to facilitate item tracking in inventory through production. Users customize their own label type with job details including Checksum, Job name, Date, Time, Device name and the actual quantity on the reel.
Confirm Device Input validates that a new reel of devices provided to the programming system match the selected job since many programming jobs contain multiple vendors/versions of the same device as a second source. It’s critical to eliminate any possibly of error during an input reel changeover since each device has its own unique algorithm used for programming. Machine operators are prompted to validate that the correct device is being provided to the programming system. The user scans the new reel to confirm match of new devices defined in the job.
More Stories
MESSRING completes new crash test facility for Mahindra in India
ROHM Develops an Ultra-Compact MOSFET Featuring Industry-Leading* Low ON-Resistance Ideal for Fast Charging Applications
More than 30 of the top 50 global suppliers have production facilities in Turkey