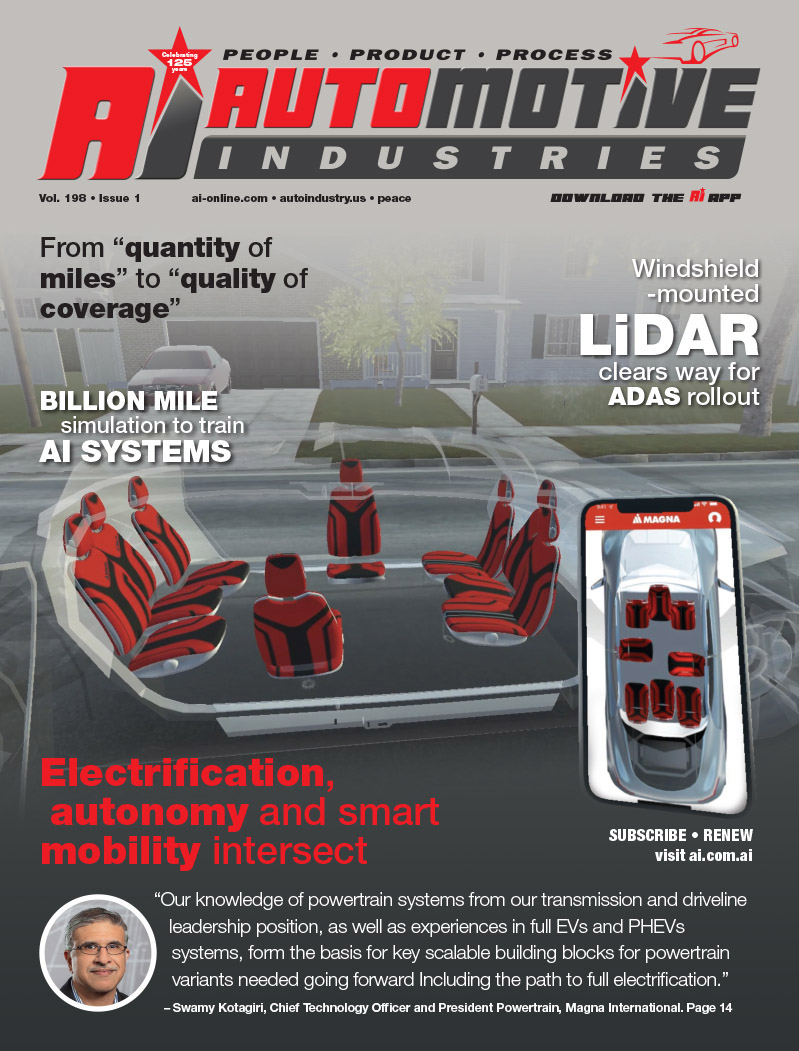
IBS has successfully implemented its new Tool Assistance System (TAS) at BMW’s production plant in Regensburg, Germany. The TAS is based on the Location Identification System (LIS), which, as the name suggests, is a system for locating and identifying industrial goods. LIS/TAS was developed as a joint software product by general contractor IBS and Ubisense. The development of the LIS/TAS system is based on integration of the Ubisense real-time location system with the IBS quality management software system. The IBS software mediates between the Ubisense location system and the other existing IT systems in use at BMW.
The Tool Assistance System, successfully implemented in Regensburg, is designed to enable the automatic identification of vehicles in the assembly process, and the automatic assignment of each vehicle to computer-assisted process equipment (screwdriving/inspection devices). The entire manual scanning process will be replaced, eliminating non value-added activities and error prone manual allocations. LIS/TAS will first and foremost support BMW in the production line area of vehicle assembly. The allocation of process equipment and devices to each vehicle is based on an analysis of the real-time spatial relationship between the vehicle and the equipment. The allocation relies on the vehicle entering a predefined zone or — in the case of moving equipment — the allocation is carried out as the equipment approaches the vehicle.
The LIS/TAS application has been embedded in BMW’s IT landscape with IBS communication software supporting all necessary interfaces with the other systems being used. In this particular case, it is designed to manage and administer tools and transmit allocation events to the automated screwdriver device control center. Following allocation of the tool to the vehicle, LIS/TAS triggers the respective vehicle-specific assembly order and the corresponding assembly programs. The assembly order for the vehicle is loaded onto the corresponding tool or equipment in real-time. In this context, tools and equipment involve such things as automated screwdrivers, riveting tools and filling equipment.
The new system has already been put into production at the Regensburg plant covering approximately 1,000 vehicles a day and 120 automated screwdrivers in the assembly area. The location of each vehicle is determined in three-dimensions using a tag attached to each vehicle. These tags are miniature transponders, which transmit information on their position to fixed-mounted sensors, using ultra wide band radio technology. Approximately 400 sensors are mounted along a 1.2 km section of the assembly line at the Regensburg plant. The location and identification data produced is then received, processed and directly transferred to the BMW IT infrastructure. The ultra wide band radio technology locates vehicles and equipment precisely thanks to the transmission of very short pulses with an extremely low output (less than 0.1 milliwatt per m2). This low output means there is no impact on other systems or employee health.
All project goals were achieved within the planned timeframe and on budget. In terms of added value, BMW regards the project as a complete success.
Hans Dieter Strack, Key Account Manager Automotive at IBS is delighted with the successful realization of the project: “With the LIS/TAS solution, IBS — along with its partner Ubisense — is the only software provider to meet all of BMW’s requirements and in doing so has put BMW in possession of a unique tool. This product represents a unique selling point and we are delighted by the positive response from BMW.”
The follow-up project and expansion of the LIS/TAS project is called LIS/IDENT. Various technologies (scanning, active and passive RFID, WiFi, UWB) are currently involved in the identification and location of vehicles and resources at BMW. The omission of individual working steps or operations (e.g. manual scanning) and the standardization and reduction in the number of systems are anticipated to enable considerable cost-saving. LIS uses standard technology that enables continuous vehicle location and identification (e.g. precise parking bay location, automatic vehicle identification) throughout the entire assembly process.
IBS is one of the world’s leading suppliers of cross-company software systems and consulting services for industrial quality, production and compliance management. In keeping with its corporate philosophy, “The Productivity Advantage,” IBS has set the goal of developing and implementing QMS, MES, LIMS and compliance management solutions that help to optimize its customers’ business processes and increase their productivity.
Founded in 1982, the Company today employs approximately 200 people in Europe and the USA. The Company is listed in the Prime Standard of the German Stock Exchange in Frankfurt/Main (ISIN 622840) and is also member of the GEX-German Entrepreneurial Index.
IBS software installations number over 4,000 worldwide and including at companies such as Airbus, Audi, BOSCH, Daimler, Evonik, FCI, Goodyear, KEIPER, Siemens, ThyssenKrupp and Tyco Electronics. IBS has been certified for its mySAP Business Suite interface software and the IBS Group has also been awarded the “Advanced Industry Optimized” status in the IBM PartnerWorld Industry Network for the automotive industry.
More Stories
Towing Services Explained: 6 Key Facts You Need to Know
Environmental Factors That Influence Ceramic Coating Choices
Professional vs. DIY Tinting: What You Should Know