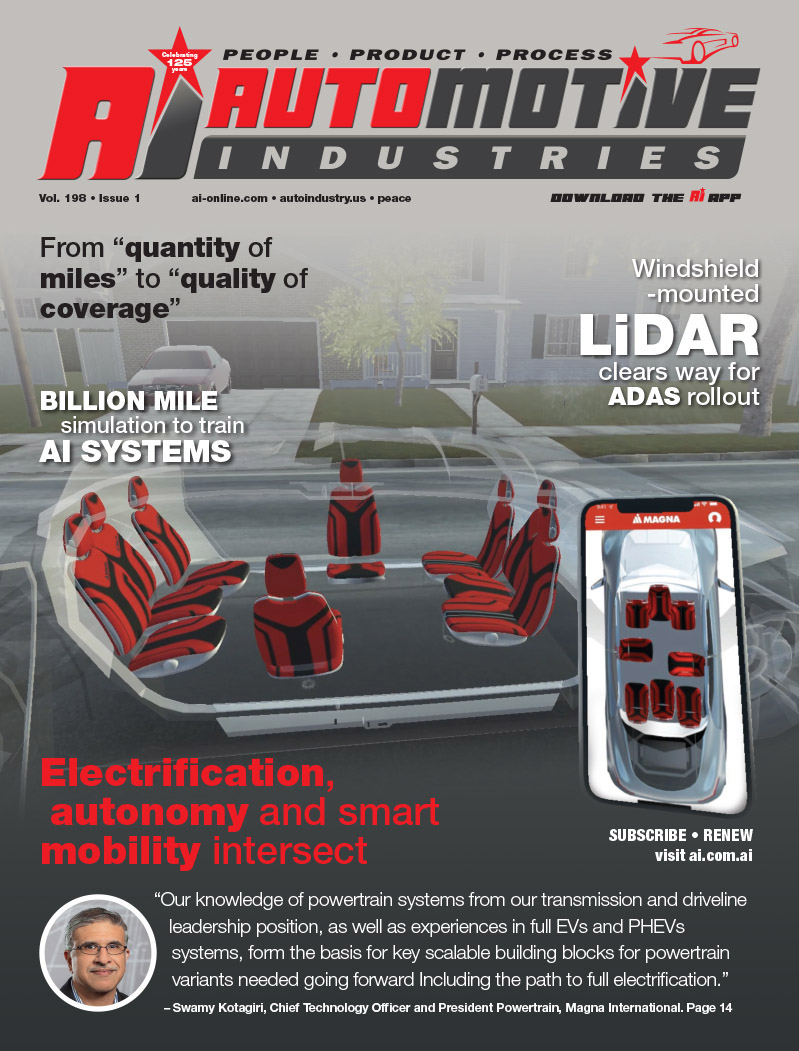
The Austrian Frauenthal Holding AG is a group of industrial companies with three different business divisions. The automotive components division is represented by Styria Federn, Linnemann-Schnetzer, Ceram and Pol-Necks. Each company is market leader in its specific sector of Heavy Duty Vehicles: Styria Federn for springs and stabilizers, Linnemann-Schnetzer as specialist for air reservoirs used in brake systems and Pol-Necks being the European leader in the manufacture of U-bolts to fix the springs. The whole Frauenthal Group has 9 manufacturing facilities in six European countries as well as service & sales companies in the US and South Korea.
Ceram, Porzellanfabrik Frauenthal, as one of the leading manufacturers of catalytic and ceramic honeycombs plays worldwide a double role: On the one hand in the area of automotive emission control, SCR-catalysts for nitrogen oxide reduction and ammonia slip catalysts are its expertise. On the other hand as leading producer of SCR catalysts for stationary applications such as thermal power stations, waste incinerators and other large combustion plants. Porzellanfabrik Frauenthal was founded long ago in 1921 and is a specialist in shaping by extrusion of honeycomb ceramics. Initially, the company manufactured high voltage insulators made of hard porcelain. In 1985 Frauenthal started its first product for environmental protection, SCR catalysts. At that time Frauenthal was the first producer in Europe.
In 2005 the SCR diesel catalyst, developed for commercial vehicles, successfully entered into series production. Diesel catalysts yield a nitric oxide reduction of up to 90 per cent in exhaust gases of today’s diesel engines. The various forms of usage range from low-temperature reduction of nitric oxides up to full load operation in motor vehicles. This SCR-system requires the admix of an additional reducing agent, e.g. a 32.5 per cent urea solution marketed under the trade name AdBlue. “The advantage of SCR-systems for automotive applications lies in the considerable reduction of fuel consumption up to 7%, as it is possible to efficiently optimize diesel engines,†says the company.
In 2007 the automotive product division from Porzellanfabrik Frauenthal GmbH became CERAM Catalysts GmbH in Frauental/Austria and a separate production plant for these specialised products has been started up including new offices and R&D labs.
However, the unexpected developments affecting the automotive manufacturing industry, which began at the end of 2008, together with the simultaneous boom in the market for power plant catalysts, led to consolidation respectively merger of the two production facilities in Frauental in the course of last year, bringing them back under one roof of Porzellanfabrik Frauenthal GmbH in order to maximize the anticipated synergies.Â
SCR-catalysts as homogeneous extruded honeycombs containing titania, tungsten and vanadia are the worldwide leading technology for nitrogen oxide reduction in stationary applications from Japan to the US and the market is still growing. This year, the company is optimistic to start selling its SCR catalysts for mobile diesel exhaust after-treatment in the US in addition to significant deliveries of stationary catalyst since more than a decade.
Automotive Industries spoke to Karl Fuehrer, Managing Director of the Porzellanfabrik Frauenthal GmbH.
AI: Porzellanfabrik Frauenthal earmarked 5 million Euros for expansion – what kind of increased capacities is the company working towards?
Production capacity had to answer to the booming market and a considerable amount had to be invested in the new metal processing center, where we manufacture the key shaping tools for extrusion: the die plates.Â
Additionally the stationary SCR catalysts are “canned†at our site since decades. The capacity for these “modules†urgently had to be increased. Of course all these processes needed support by more research and development resources.
AI: Tell us about the catalyst technology that gave rise to the Frauenthal diesel catalyst.Â
The chemical composition of the SCR catalysts was already well proven for NO-reduction and durability – stationary as well as mobile. The SCR technology is successfully installed worldwide since more than a quarter of a century in power plants. The real challenge for vehicles was the development of a new geometry, an extreme increase of cell density to accommodate a reasonable catalyst volume in the limited space of a vehicle. Pioneer’s work was done in manufacturing the new tools with ten thousands of high precision cells instead of a few hundred for stationary operations. All this R&D had to be accompanied by adjusting the necessary processing parameters of the catalytic mass.
AI: What are some of the latest innovations in the Ceram catalysts?
We are preparing serial start up of a very challenging geometry of mobile SCR catalyst for USA.
AI: What kind of opportunities do you expect for your company’s SCR catalysts in the US market?
Off Highway and Non Road Vehicles predominantly use diesel engines because of their high performance, reliability and durability. The new emission limits are already decided. SCR is the preferred emission control technique due to the favorable fuel savings.
AI: What are some of the new technologies your company plans for launch in 2010?.
For the real tough conditions such as very hot regeneration temperatures behind particle traps we develop a stabilized new catalyst type.
Additionally we fully investigate the limits of our traditional series catalysts as they are well proven in all conditions – below a certain temperature one has to admit.
There is a lot of public discussion about the possible loss of vanadia in the environment if catalysts are installed into mufflers of vehicles. We take our responsibility serious and have comprehensive projects running at well known and specialized external organisations. Toxicological behaviour of the catalyst as a whole as well as biologic influence of the separate ingredients are investigated. To name some results already in advance: Our homogeneous, vanadia containing catalysts did no damage to aquatic organisms or cause cancer in approved test series.Â
But this is not really surprising as life on earth is well adopted to intake and removing of vanadia: Vanadia is nearly everywhere in our natural environment as it is part of plants where it plays a vital role for enzymes in photosynthesis. That is why we eat and breathe daily small quantities of vanadia. But it does not accumulate; our body keeps the vanadia level constant between 20 mg and 100 mg. A daily dose of up to 1 mg vanadia is even recommended as trace element in our food. This is the typical amount in 200 g of nuts or 100 g of green beans or approximately 500 g of fruits and vegetables.
Be aware of different types of automotive exhaust catalysts on the market, namely oxidation catalysts and SCR-catalysts. Their composition is different: In the long ago introduced oxidation catalysts for oxidation of hydrocarbons and carbon monoxide relatively high concentrations of vanadia oxides exist that have only weak interaction with the usual alumina supportÂ
In marked contrast the homogeneous SCR-catalysts consist of mainly titanium oxides (80 wt.%) and contain a maximum of 2% vanadium oxide loading.Â
The vanadium is evenly distributed over the very high surface of titanium oxide in the form of isolated monomeric atoms due a very strong interaction with titania.
And titania itself is in all the wall paints around us, in tooth paste, sun protection creams, the white powder around salamis – to name a few more applications. Even if our catalyst would not poison you – we recommend staying with tastier food.
More Stories
Dürr and GROB concept battery factory uses 50% less production space
DuPont materials science advances next generation of EV batteries at The Battery Show
How Modern Power Management Enhances Connected Fleet Tech