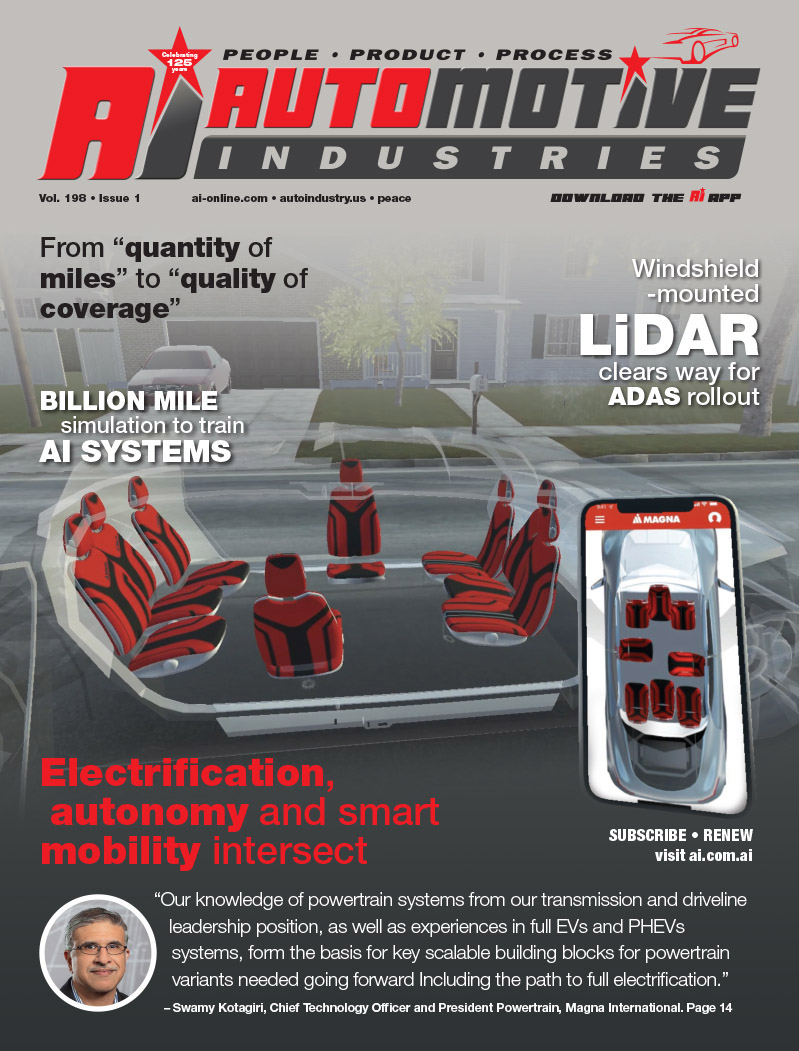
As of March 25, 2011
Scenario analysis released by IHS Automotive underscores that the non-Japan production impact will worsen substantially before it improves. In a positive scenario, 15% of global output could still be affected at the eight-week point—fully 30% of global output in a negative scenario could be affected at the same point.
Global light-vehicle output is expected to be affected by approximately 600,000 units to the end of March. The total Japan output effect could reach 530,000 light-vehicle units by the end of March—rising at a rate of 37,000 units per day if all volume is influenced in the country.
Several OEMs have started component production in Japan to ready for vehicle build later this week (as well as supplying international operations); the ability to commence is still variable and may be short-lived.
Component shortages have begun to affect locations outside Japan at both Japanese and non-Japanese OEMs. All OEMs and suppliers in the Tier-1 and -2 sectors are analyzing their exposure to components emanating from the quake/radiation zones.
It could take approximately seven weeks of full production with overtime at a facility to compensate for one week of lost production volume.
Readiness of the Supply Base to Reengage Is Critical
The state of several OEM production facilities in the affected zone has been roughly established, with varying states of production readiness. Most component/material facilities have little or no damage that would inhibit the resumption of output once stable component/system supply resumes.
Once the state of readiness of the facilities is established, issues with the electric, water, natural gas, communications, and transport infrastructure need to be evaluated. Ample incremental capacity to compensate for challenged Tier-1, -2, and -3 capabilities in the northeastern Japan region is difficult to launch quickly and, quite possibly, nonexistent. Some components are single-sourced—immediate shifting of supply is not possible.
Key Component Supply Issues to Overcome
Electrical/electronic components: The capability to produce integrated circuits, semi-conductors, LCD displays/films, and sensors is still in question. This is possibly most important to global OEMs—the downstream effects are beginning to influence volume outside Japan. The loss of this output, already in tight supply, is now being felt globally with varying effects. Impact varies from immediate to 4-6 weeks downstream.
The state of the production capability for petro-chemical feedstocks (specialty resins, pigments, butylenes, etc.) is also becoming clear. Four petroleum “crackers” are not operational currently, slowing the process to refill low petro-chemical feedstocks.
Powertrain components: The quake zone is the home of gear manufacturing, seal systems, clutch components, specialty bearings, and other capital-intensive, application-specific components, for which alternate supply sources are difficult to find.
Specialty materials shortages: Automotive float glass, specific metals, and silicon output. Effects vary depending on sourcing, inventory, and availability of alternative supply.
Impact on Light-Vehicle Production in Japan
Toyota output is officially idled through this weekend except for two facilities manufacturing hybrid offerings. Given the state of the manufacturing infrastructure, it is expected Toyota will need to keep most of its facilities fallow until the condition of downstream supply becomes clearer. Downtime is expected to extend into next week.
Nissan’s situation is similar to that of Toyota, in that the vast majority of its facilities are not producing vehicles. The Iwate engine plant (V6 engines) will need to depend upon its US sister facility as a temporary backup, as it may not be operational until mid-April at the earliest.
(Fuji Heavy) Subaru has closed its facilities through this weekend. Similar to Honda, it has several just-in-time (JIT) suppliers in the quake zone that need to establish production readiness.
Honda has idled its core Sayama and Suzuki facilities through this weekend but likely beyond. Many of its core JIT suppliers were not only in the quake zone but in the less accessible radiation zone. Quite possibly, Honda’s core supplier base could be most affected by the disaster.
Suzuki has closed all its plants in Japan through this weekend, after which the company will assess the situation. Mazda has reported that although none of its facilities have been affected by the disaster, as its plants are primarily located in southern Japan, well away from the quake-affected areas, it will idle production nonetheless through this weekend.
Mitsubishi ran some half-shifts this week, although part supply has again been drawn down. Output is cancelled through this weekend.
Impact on Output Outside Japan
North America
Output of Japanese OEMs in North America is expected to be affected (outside the cancelled overtime) by early April. Effects will be rolling and variable, although real. Of greater variability is the impact on non-Japan OEMs, especially the Detroit Three. Both GM and Ford have been affected through downtime or mix shifts, although more acute effects are expected for the mid-to-late-April timeframe.
Europe
Electronics supply is a more focused issue with European OEMs. Mass air flow sensors, LCD screens, and other electronic components are key here. PSA and GM have been affected thus far, although others are expected to be by mid-month.
China
Whereas China is building many of the same vehicles as Western Europe, Japan, and North America, the strikes of 2010 drove many OEMs to keep a safety stock. Western OEMs will be affected first, although possibly not until mid-April—the Japanese OEM joint ventures may be first.
India & ASEAN
Japanese OEMs are core to both regions. Thailand output is heavily focused on Japanese OEMs, and thus, the supply impact could be faster than in other emerging markets. Thailand has nominal electronic-component production for automotive applications—well coordinated with Japanese supply. There is a safety stock, although this may only last into mid-April before issues emerge. India is in slightly better condition, in that supply lines are longer and thus in-route inventory is stronger. Supply issues of specialty components may be apparent by late April.
Scenario Analysis
The accompanying scenario slides outline possible positive and negative scenarios over the four-, six-, eight-, and twelve-week time periods from March 11. These underscore the possible effects to Japanese output and output outside Japan by both Japanese and non-Japanese OEMs. Additionally, a replacement rate or “compensation time” is integrated. This measures the amount of time to replace volume on overtime if full supply is regained.
The situation is highly fluid. Scenarios were introduced to underscore the seriousness, possible longevity, and downstream interconnectedness of the supply base interruptions on final vehicle output.
How to read the scenarios: For instance, in the Week 8 scenario, if substantive production disruptions were to continue through this period, between 20% and 40% of global output could be affected, taking up to 12 months to recover. If the disruption lasts 12 weeks (three months), a lower portion of global volume for both cases (with the expectation of some relief and supply remediation) would lower this to between 15% and 30%, still taking over 12 months to remedy.
IHS Automotive is continuing to evaluate the situation as it progresses, with teams inside and outside Japan examining the impact of the disaster locally and on the global automotive community.
More Stories
Sonatus – The industry is shifting gears to software
Cybord warns of dangers of the stability illusion
HERE building trust in ADAS systems