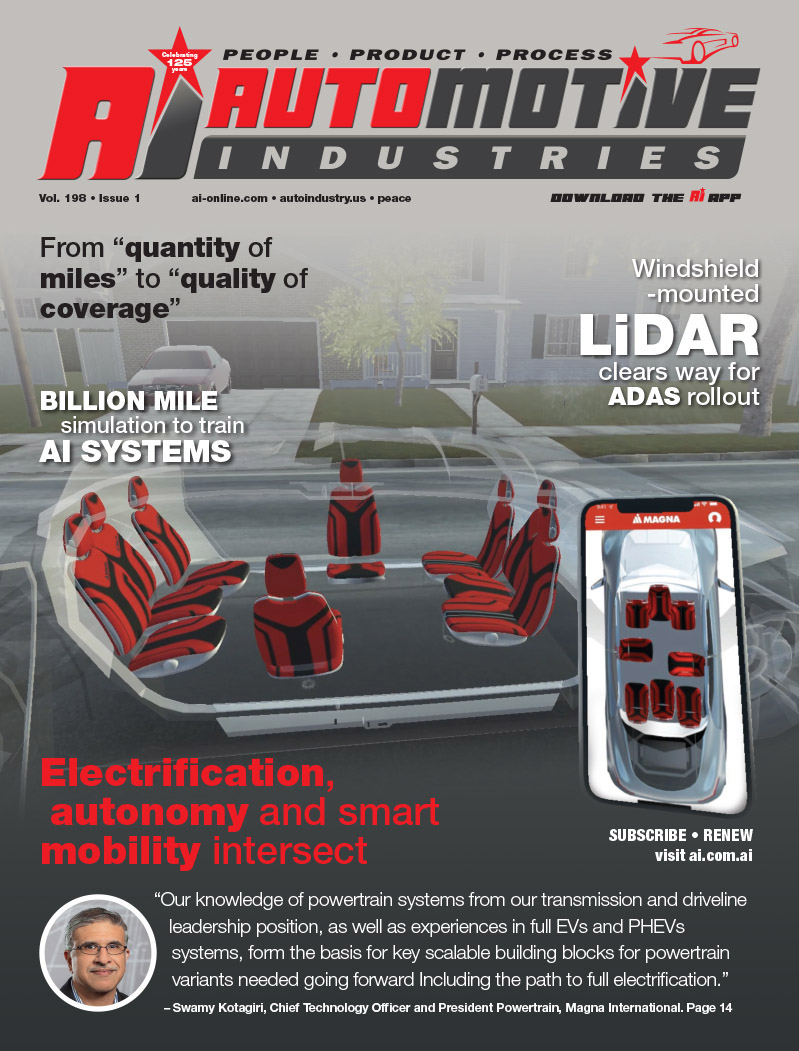
Increasingly stringent emission regulations are forcing OEMs to redesign DPF and catalyst technology in the middle of a model life, and also for after-market support of their vehicles already on the road.
One of the specialists in the fast-track development of DPFs and oxidation catalysts is Danish firm Liqtech International (formerly CoMeTas). It develops, manufactures and markets catalysts and diesel particulate filters for engine emission control for both the OEM and after markets.
Liqtech has developed a portfolio of catalyzed DPFs (cDPF) based on its proprietary washcoat technology and metal oxide composition. The coating can be optimized for low soot combustion temperature, catering for low and high NO2 levels. High NO2 ratios are required for optimal function in an SCR system. In the retrofit segment, Liqtech recommends zone coatings which make it possible to balance regeneration and NO2 performance according to the specific requirements of the region in which the vehicle is being sold and used. “It is our philosophy that for all our customers we verify whether or not our standard coatings are the right choice. We are happy to make the necessary modifications to the formulation to secure it fits the system perfectly,” says the company.
“The Liqtech International portfolio includes SiC DPFs, and we are very proud to present our new asymmetric design. From a back-pressure, durability and soot load capacity point of view this product will be attractive in many applications,” it says. The extra storage capacity of the filter secures a lower back-pressure over time, increases the time between service intervals and thereby the lifetime of the filter.
Liqtech supplies oxidation catalyst for both automotive and non-automotive applications. For the automotive segment, the company offers a range of pre-catalysts for DPF systems. The portfolio includes pre-catalysts for CRT, cCRT, FBC and post-injection system, as well as conventional oxidation catalysts for HC and CO removal in systems where PM reductions is not the focus,” it says. “Our current focus is on metal pre-catalyst for HC-injection systems for OEM use. Generally, our binder technology for metal substrates can be applied to all oxidation catalysts, including hydrolysis catalysts for SCR. In 2012, our SCR catalyst will also be commercially available,” says the company.
For larger stationary engines, as well as gensets, marine and locomotives Liqtech provides catalysts for both rich- and lean-burn engines. The catalyzed metal substrates can be supplied in diameters up to 1200 mm or modular catalysts in square blocks.
It has built up extensive expertise and knowledge in designing 3-way catalysts for the aftermarket in Europe and South America. All catalysts are based on the company’s wash-coating formulation and production. Liqtech makes recommendations based on emission requirements, engine specifications and exhaust system design. We aim to provide recommendations and quotes within 48 hours and general lead time on parts after receiving substrates is less than one week,” says the company.
“For regions with high-sulfur levels, we have developed a DOC Survivor coating with very high sulfur tolerance. The DOC Survivor
Dina Mathiasen, Head of Emission Catalyst Division, Liqtech International.
is a plug and forget solution for simple reduction of odor and smoke in applications where a DPF can not be applied because of high sulfur levels,” says the company.
Automotive Industries spoke to Dina Mathiasen, Head of Emission Catalyst Division Liqtech International, and asked what makes the company’s ceramic membranes and catalytic coating solutions innovative.
Mathiasen: Liqtech International differentiates itself to its larger competitors through a very flexible product development approach, which enables us to customize products very fast. That goes for both the diesel particulate filters, which can be specifically dimensioned and produced for a particular application, and also for the catalysts which can be modified to meet exact customer requirements.
AI: Tell us about the work Liqtech is doing developing ceramics and catalysts.
Mathiasen: Our Innovation and Technology group is really the heart of our business and the most important key to our past, present and future growth. There is a large demand in the market for fast, flexible and reliable development, that allows customers to bring a unique product to the market based on their specific needs in terms of dimensioning and formulations. We are currently working on a variety of different products that we are looking forward to presenting to the market.
AI: How would you describe Liqtech’s automotive capabilities and future objectives?
Mathiasen: Our core competency is definitely within smaller, specialized applications.
AI: What are Liqtec’s plans for further global growth?
Mathiasen: The current plans include a catalyst production facility in North America early in 2012, and hopefully in East Asia for both diesel particulate filters and catalysts by the end of the same year. Besides that, we are expanding our sales activities to provide local presence in all our strategic markets. However, for the catalyst part of the business, we also respect that for some applications, situations and places, it is not feasible to do the production in-house and we also license our washcoat and production technology.
More Stories
DuPont materials science advances next generation of EV batteries at The Battery Show
Cybord warns of dangers of the stability illusion
How Modern Power Management Enhances Connected Fleet Tech