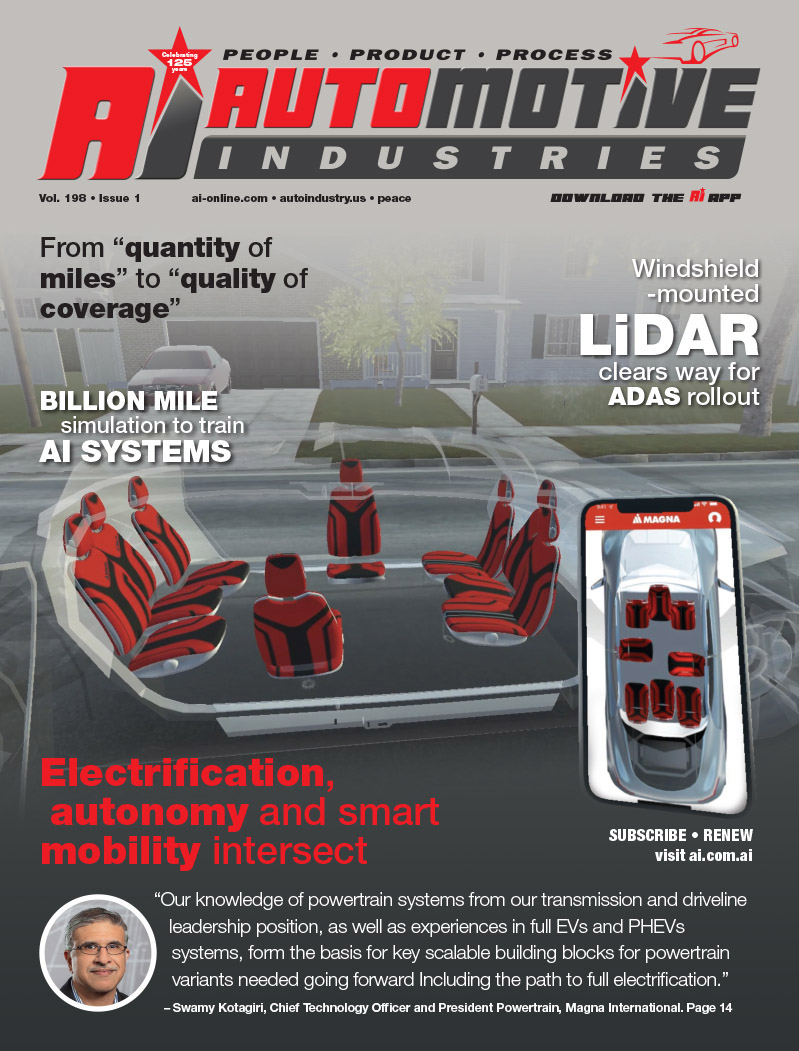
A new range of engineering resins developed by Styron Automotive announced – its PULSE™ GX50 range – set new speed records by securing its first commercial application in the Audi Q3 only a year after introducing it to the market. Styron, is a spin-off from the Dow Chemical Company, is a leading manufacturer of plastics, latex and rubber.
Automotive Industries (AI) asked Dagmar van Heur, Vice President Automotive for Styron, to provide an overview of Styron Automotive’s innovative solutions for automotive interior and exterior components.
Van Heur: Since becoming an independent company, Styron has developed and launched an array of new technologies: PULSE™ GX family; VELVEX™ reinforced elastomers; PULSE™ EXT 200; and a new platable PC/ABS, which are all globally available.
In North America we have developed MAGNUM™ 375HH, a high heat ABS resin, which meets the requirements of the German manufacturers in the US.
New-to-industry applications that significantly decrease weight of the final application in the car include the thermoplastic door panel, the blow molded seat back and hybrid front end carriers.
Styron works with molding equipment manufacturers to develop processes that reduce the amount of material needed for applications like pillars and trim parts. A recent co-development reduced pillar trim material use by 40 %, while having the same performance characteristics as the present unit.
AI: What are some of the competitive advantages in using products such as the PULSE™ range?
Van Heur: The PULSE™ range of engineering resins is tailored towards interior and exterior components. For exterior components, Styron has developed the PULSE™ EXT resins that combine high heat resistance with high impact strength at both room and low temperatures. For the interior, the PULSE™ GX resins address the industry’s demand for lighter materials without compromising quality, performance or cost. The PULSE™ GX line offers resins made of a PC and ABS blend that provide easy flow and are more cost-efficient in comparison to conventional PC/ ABS materials. The series includes: PULSE™ GX50, PULSE™ GX70 and the PULSE™ GX90.
AI: And what of your MAGNUM™ and CALIBRE™ range of resins?
Van Heur: Styron’s MAGNUM™ ABS resins are manufactured with continuous mass polymerization technology, resulting in a very stable process that ensures superior lot-to-lot consistency of properties. Mass polymerization allows for lower levels of process additives, and therefore a purer polymer. As a result MAGNUM™ ABS resins have a highly consistent, white base color, resulting in a combination of excellent processability and aesthetics, which make it suitable for self-coloring. Our MAGNUM™ 3416 SLG (Super Low Gloss) is an ABS product with inherent low gloss appearance, allowing car manufacturers to eliminate a painting step. CALIBRE™ IM (Impact Modified) polycarbonate resins offer superior low temperature impact strength and easy processing with improved impact strength in highly filled formulation.
AI: Why was the VDI conference an ideal platform to launch your PULSE™GX70 and PULSE™ GX90 products?
Van Heur: This year’s conference focused on two major global trends in the automotive industry: weight reduction and quality improvement. Our PULSE™ GX70 and PULSE™ GX90 products address both of these trends. Our PULSE™ GX products have lower densities versus conventional PC/ABS products. Some of these solutions can replace steel components, thereby drastically reducing weight while offering the same safety. We also see the demand for higher quality interiors in the growing small luxury car segment. Several European OEMs are using more styrenics polymers to improve the quality of the vehicle interior.
AI: How important are such events for Styron Automotive?
Van Heur: Styron sees these international trade fairs as an opportunity to enter into dialogue with the industry. Trends come and go, but the people who work in the industry are there for a long time. This contact is important, because it can take about three years to develop solutions with OEMs before commercializing. At the VDI Conference, Styron Automotive had a great experience and the overall response confirmed that our developments are headed in the right direction, particularly in light-weighting and quality improvement.
AI: What is your strategy for expanding the scope of Styron’s brand image in the automotive sector?
Van Heur: We believe that we have to establish a competitive cost position for our products before engaging with car manufacturers, and offering them globally approved products.
OEMs will be able to introduce the same high quality car interiors and exteriors globally. We are continuously working on increasing our global footprint. Today various global Styron PC/ABS products are produced in Taiwan for our (mainly) Chinese customers. The roll out of the supply of PP compounds and LGF PP from production sites in China/Taiwan is ongoing. Increasingly our resins for the automotive industry that have been approved by US and EU car manufacturers are being offered globally.
AI: What expertise does Styron have in terms of R&D?
Van Heur: We have dedicated TS&D and R&D resources in all major geographies (Brazil, US, Europe, China). In addition, there are European engineering resources covering global application development needs. One example is the frequent co-operation between Styron Color Group and Styron Automotive to match OEMs color needs. For the PULSE™ product family, a Color UV package with improved hydrolytical stability has been developed. This is also used in combination with PULSE™ GX50, and can be used for interior unpainted applications.
More Stories
MESSRING completes new crash test facility for Mahindra in India
ROHM Develops an Ultra-Compact MOSFET Featuring Industry-Leading* Low ON-Resistance Ideal for Fast Charging Applications
More than 30 of the top 50 global suppliers have production facilities in Turkey