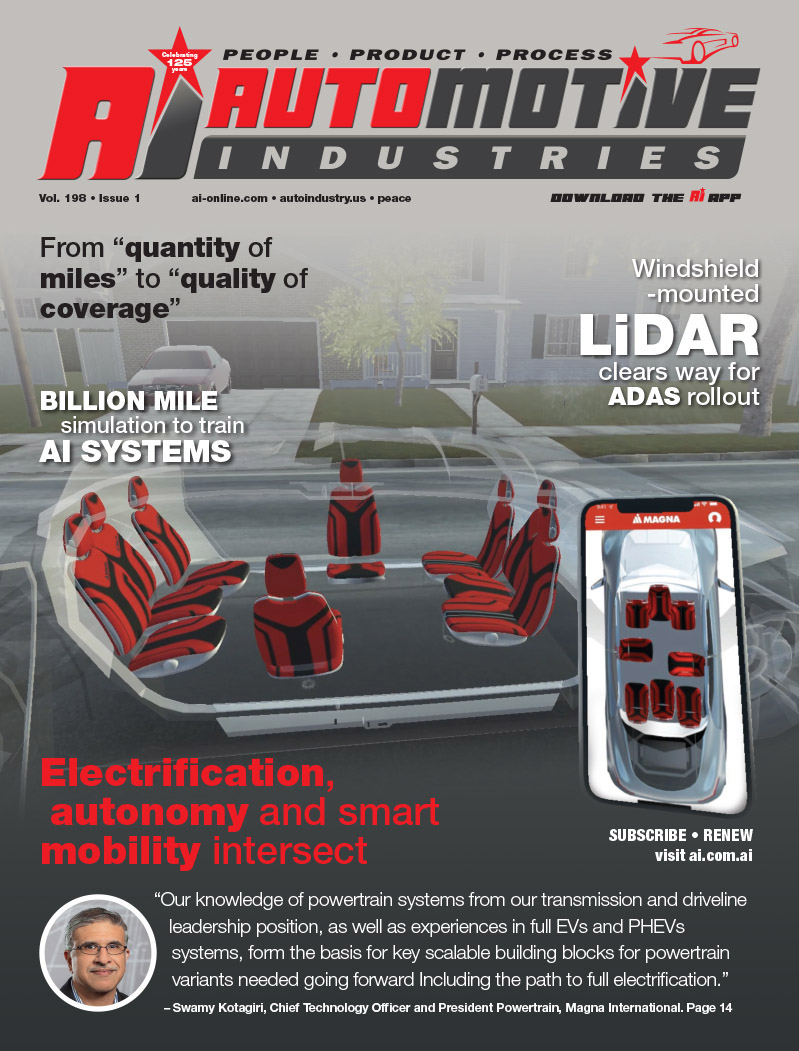
NORMA Group, a global market leader in Engineered Joining Technology, and one of the pioneers of plastic connecting technology, has developed the next generation of quick connectors for charged air and cooling water systems.
Automotive Industries (AI) asked Thomas Kraus, Vice President Business Development Europe, Middle East and Africa, to provide some background into the group’s product portfolio.
Kraus: Besides the standard clamping and connecting technology of approximately 35,000 articles for all types of industry, trades and private applications, our Engineered Joining Technology (EJT) business unit develops both individual and standardized solutions for Emission Control, Cooling, Air Intake & Induction, Ancillary Systems and Industrial Fluid Connectors. We offer individually designed clamps, couplers, connector solutions, as well as fluid transporting pipe systems from our modular system of components. Our engineers work in our technology centers across EMEA, the Americas, and Asia. Their broad knowledge creates a basis for design-tocost solutions, while at the same time supporting our customers´ requirements to downsize their internal combustion engines or implementing alternative drives like hybrids or electrical motors.
AI: Why a new generation of quick connectors?
Kraus: It is the logical consequence of our tag line: “Customer Value through Innovation”. During the lifetime of the existing NORMAQUICK® TWIST line we gained valuable experience about the performance of the current connecting technology for charged air and cooling systems in passenger vehicles and trucks. Based on this information, the know-how we had from the other seven NORMAQUICK® Connector product lines and drawing upon the discussions with our customers about future requirement for interfaces in the charged air and cooling application on future turbo charged engines and vehicles, we started the development of a new connecting technology.
AI: What are the main advantages of this system?
Kraus: Existing plastic or metal quick connectors which comply with SAE or VDA have the disadvantage that they need to be actively locked after assembly, or need to be prepared for another assembly operation after being disassembled. The range of sizes is also limited by performance, design and manufacturing constraints. Because we focused on the design of the complete interface rather than just the connector, our engineers developed a new, size-optimized mating spigot design that can easily be integrated in the design and the manufacturing tools of every charged air or cooling system component part. The TWIST III Connector sets a new level of performance in terms of extremely tough requirements in packing, mechanical load, chemical and temperature resistance, as well as emission standards. The TWIST III generation has already been successfully tested against several OEM specifications, like the GMW 15803. It is made up of as few as four components, which are assembled on our fully automated lines. The materials are fully recyclable. TWIST III is available in three standard versions. The NQ TW III SP is for applications in which the connector will be welded on other injection or blow molded plastic components or flexible TPE ducts. The NQ TW III V0 is a straight connector with a hose barb for the assembly of an elastomer hose, while the NQ TW III V90 is the equivalent 90° bend version with a hose barb.
AI: What are the advantages of the new generation of NORMAQUICK® TWIST III connectors?
Kraus: First, this new connector generation improves the quality of assembly because the operator only has to carry out a push-pull action due to the self locking mechanism. The disassembly operation is as easy as the assembly operation because the so-called spider ring only needs to be turned and the connector can be pulled from the spigot. After disassembly, the spider ring returns automatically to the assembly position.
Warranty issues which occur in service actions with the actual available quick connector versions will be eliminated completely.
The second advantage is the very low assembly forces required for big sizes, due to the optimized axial to radial size relation. The symmetric design allows the connector to be opened from any angle. This makes them perfect for tight environments and suitable for spin welded applications. Since the optional anti-rotation feature, which guides the connector into a specific position, can be integrated into the mating spigot, no additional knobs or cut outs are needed.
This means that the mating spigot dimensions are the same as those of the standard spigot. The modular design of the connector and the tools gives a maximum of flexibility for customized solutions, and allows for an easy integration of additional functions with sensors or actuators.
AI: What were the biggest challenges?
Kraus: As the axial length of the TWIST III Connectors compared with other quick connectors on the market is very short, the forces during mechanical load in combination with vibration and temperature need to be compensated in a very small area of the connector. To find the right dimension of the components by taking into consideration the different materials for the different applications was the biggest challenge for our engineering team. However an optimal solution was found.
AI: What are the next steps?
Kraus: The NORMAQUICK® TWIST III generation has already been successfully launched in series production with some international OEMs in the range of 45mm to 80 mm. Based on this success and our customers´ wish to use this Quick Connector generation in further applications, the next step is to tool the sizes below (down to 10 mm) and above (up to 100 mm). With that product portfolio we are prepared to start the next projects and realize solutions for Charged Air and Cooling applications with our customers in the EMEA, Americas and APAC region.
More Stories
MESSRING completes new crash test facility for Mahindra in India
ROHM Develops an Ultra-Compact MOSFET Featuring Industry-Leading* Low ON-Resistance Ideal for Fast Charging Applications
More than 30 of the top 50 global suppliers have production facilities in Turkey