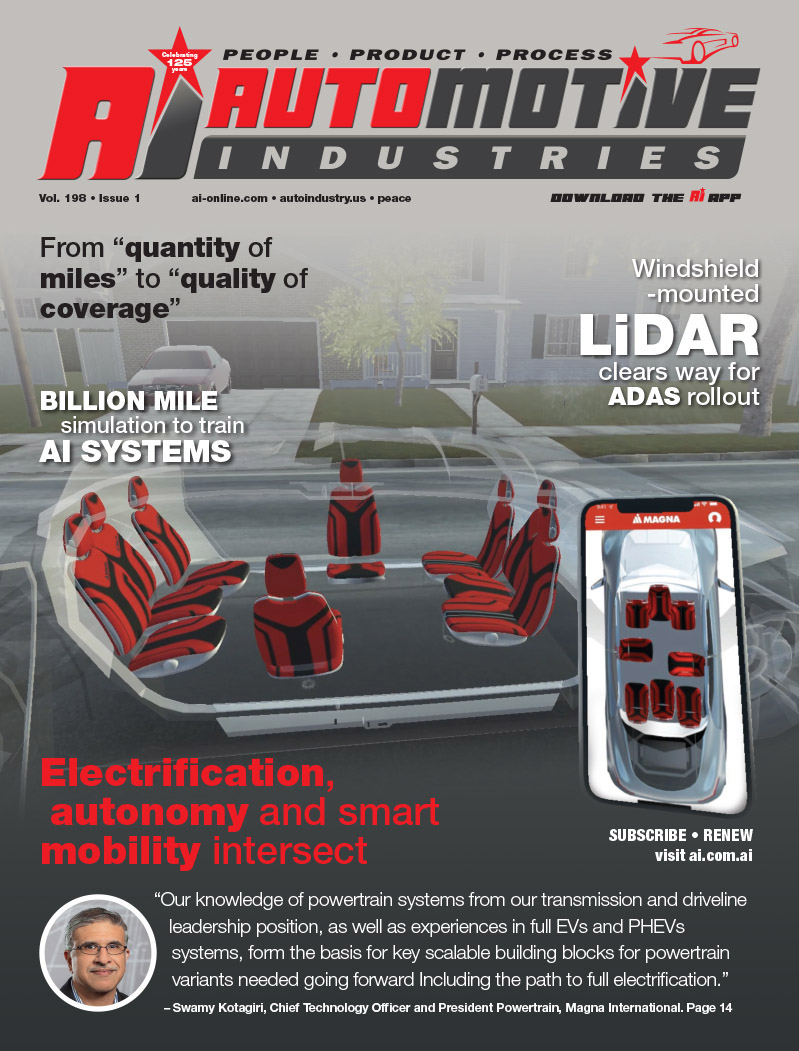
What has transformed graphite from an uninteresting mineral to strategic material is that the anode in Li-ion batteries is made from graphite – and there are no substitutes. Both the European Union and the USA have named graphite a supply critical mineral. In addition, the British Geological Survey recently ranked graphite right behind rare earths and well ahead of lithium in terms of supply criticality. Manufacturing Li-ion batteries takes 20 to 30 times more graphite than lithium.
Most Western graphite producers were put out of business in the early 90s when prices crashed as China dumped product on the market to earn foreign exchange. Exploration and development ceased. Prices did not start to recover until 2005 as it took that long for excess production capacity in China to be used up. Since then, graphite prices have more than tripled due to the continued industrialization of China, India and other emerging economies and resultant strong demand from traditional steel and automotive markets. At present, China produces over 70% of the world’s graphite. The country has introduced a 20% export duty, and licensing requirements on its production. Exports are expected to decline at a time when graphite demand is expected to grow rapidly. New applications such as lithium-ion batteries, and also fuel cells, vanadium redox batteries and nuclear power, represent potentially significant sources of incremental and competing demand growth in the future.
Driving the demand, both President Obama and China have stated that their goal is to have one million electric vehicles (EVs) on the road by 2015. There are two to three kilograms of graphite in the average HEV and 25-50 kilograms in an EV. Even at the low end, a million EVs need 25,000 tons of anode material – which requires 75,000 tons of graphite.
Current annual flake graphite production is about 400,000 tons a year, so even a modest EV adoption rates will put significant pressure on graphite supplies and prices. If EVs gain only 5-10% of the market by 2020 annual world flake graphite production will have to more than double.
This creates a very compelling supply/demand/price dynamic if you happen to be planning a new graphite mine. One such company is Ottawa, Canada based Northern Graphite Corporation (NGC:TSXV). Northern’s Bissett Creek graphite project is located about two and half hours east of the country’s capital, Ottawa, and it is only 15 kilometers (nine miles) from the Trans-Canada highway. It is the first significant new graphite mine to be built in the world in over 20 years. The advanced stage of Northern project and its proximity to infrastructure and markets are two of the reasons it is considered a leading candidate to change that situation.
The Bissett Creek Project will produce almost entirely high purity, large flake graphite – which is the high value, high growth end of the market, with amorphous graphite being the low value, low growth market. Only flake graphite which can be economically micronized, rounded and purified to 99.95%C can be used in Li-ion batteries. Almost all of the company’s production will meet this standard. In addition, Bissett Creek has the potential to be the largest graphite mine in the world as resources which have already been identified through drilling are sufficient to increase projected production by three to five times if the markets grow as expected. The deposit is located right at surface and is very flat lying so expansion can take place by moving laterally rather than deeper.
Automotive Industries (AI) asked Gregory Borden Bowes, Chief Executive Officer of Northern Graphite Corporation, how optimistic he is of starting construction at Bissett Creek this year.
Bowes: We have been working on the feasibility study and permitting for a couple years and are at a very advanced stage so I am quite confident they will completed within a couple months. The next challenge is raising US$80-90 million in capital for construction. It sounds like a lot of money but is actually quite modest in mining terms as most projects are a couple hundred million plus. We have the benefit of good infrastructure, and there are no major engineering or technical challenges. Interest in new graphite projects is quite high in the financial community and among both industrial graphite users and Li-ion battery manufacturers so I feel positive about our ability to get the financing done.
AI: Tell us a little about the impact graphite has and will continue to have on the automotive industry.
Bowes: Graphite is already widely used in gaskets, brake linings, clutch parts and batteries and I think it has the potential for far more use in composite materials where the goal is to reduce weight. Most of these materials are based on carbon fiber, which is essentially expensive synthetic graphite. Natural graphite based composites would be a lot more cost effective. Of course, the big use will be Li-ion batteries in hybrid and electric cars. That is real and it is here now. It is only a question of how quickly they will get greater commercial acceptance and how far that goes.
AI: Since graphite is such an important part of Li-ion batteries, do you see further breakthroughs technologically in terms of how the material is used?
Bowes: Absolutely, “supply creates demand”. There is no incentive to spend money on research and development or design a material into new products if you do not have reliable suppliers of high quality material. Graphite is truly a remarkable material that could be used in a lot more applications, but supply from China has been a problem. We think our Bissett Creek project, and others, will address this situation.
AI: What role do you see Northern Graphite playing the global graphite industry?
Bowes: We not only want to be one of the first new graphite mines built in 20 years, we want to be the biggest and the best. We have done far more metallurgical testing, drilling and engineering than our peers, and I think have verified that the Bissett Creek deposit has the size and product quality to achieve this objective and we envision doubling production very quickly after the mine goes into production..
AI: When your mine starts full commercial production, how much of the global demand will it be able to satisfy?
Bowes: We will start out by producing about 20,000 tons of graphite per year which is 5% of the 400,000 tons annual flake market. This market is reportedly growing at up to 5% per year so in theory, the world needs a new Bissett Creek every year. In addition, the market has to contend with declines in aging mines and declining exports from China so even in the absence of any growth in the Li-ion battery market, the world needs more new graphite mines.
AI: How will your partnership with Panacis add value to Northern Graphite?
Bowes: We don’t want to be just miners. Value added processing will become a big part of our strategy moving forward but it will take some time to investigate these markets and determine where the best opportunities lie. However, we believe there is an opportunity right now for western producers of spherical graphite. This is the product that is used in the anodes of Li-ion batteries. It is made from the concentrate produced by graphite mines in a process that involves, micronization, rounding and purification.
Almost all spherical graphite is currently produced in China and purified using strong acids which results in large volumes of acidic and toxic waste. This method is not environmentally sustainable as the demand for, and production of, Li-ion batteries increases. It is also inconsistent with the green energy objectives of the hybrid and all electric car industry. The high quality and purity of graphite from Bissett Creek has enabled the company to develop a proprietary purification technology that is environmentally friendly and sustainable.
We have already successfully made and tested spherical graphite from the Bissett Creek deposit and want to establish ourselves as a secure, reliable supplier of a high quality, Canadian made spherical graphite that has been produced in an environmentally friendly manner. Panacis has a great deal of knowledge and expertise with respect to the manufacture and testing of Li-ion batteries and has established relationships with most manufacturers. This provides us with a very important window into the Li-ion battery world. Recently we engaged Hazen Research of Golden, Colorado and the National Research Council of Canada to continue testing and optimizing its process for manufacturing spherical graphite which is used to make the anodes in Lithium ion batteries
AI: Tell us a little about graphene and what impact you see the material having on industries such as the automotive industry?
Bowes: Graphene is a material that will truly transform the way we live, work and build things. It is a very sexy topic that brings a lot of attention to our industry because it will likely be made from natural graphite for many high volume applications. However, it is still very much a research stage material and there are no processes to produce it economically on a commercial scale. You will probably see it creep into lower-end applications over the next five years, but I think the real changes it will bring about in the automotive or any other industry are at least five to ten years away.
More Stories
Automotive Industries (AI) Newsletter April 2025
Bangkok International Motor Show 2025 – The Talk of Sensuous Automotive
Earn GHG reduction values through MOL Pure Car Carrier “Book and Claim (B&C)” service