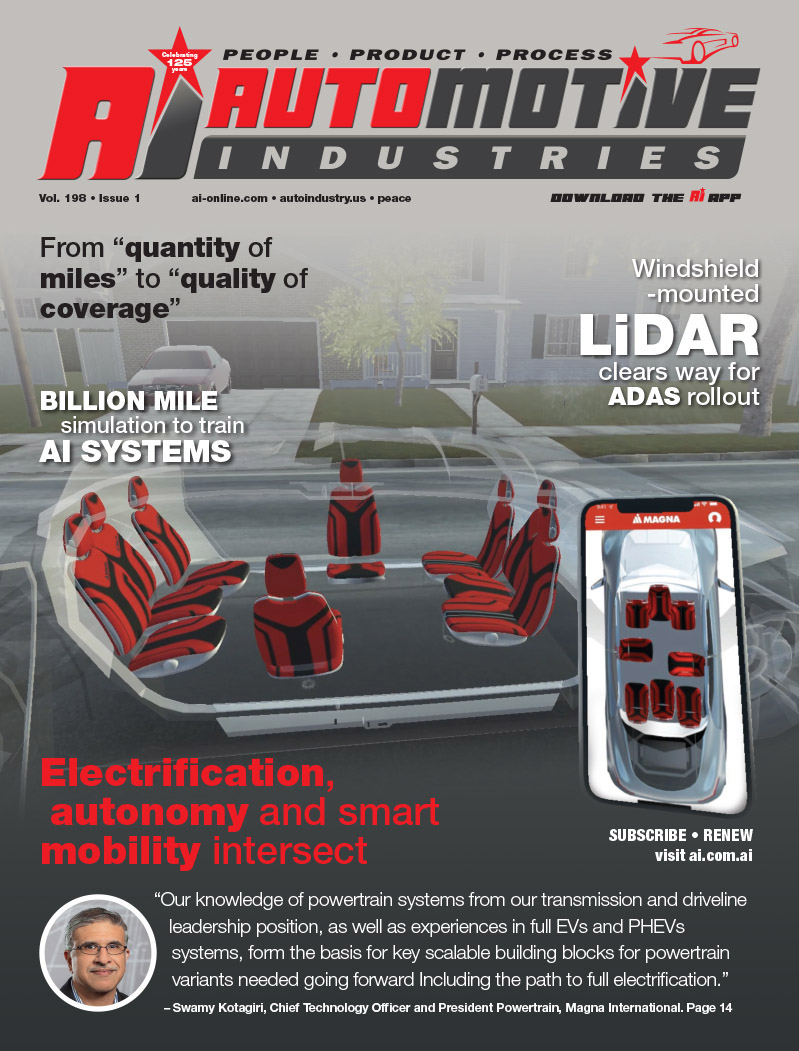
Global technology and specialty materials company the Celanese Corporation is celebrating 50 years of its flagship product, the Celcon®/Hostaform® acetal copolymer (POM) product line by introducing a new Hostaform XGC glass reinforced series for demanding structural applications. Celanese’s new Hostaform XGC POM series which combines improved mechanical properties with a superior anisotropic shrinkage factor compared to other glass fiber reinforced resins, according to the company. It is designed to give customers a competitive edge in innovative structural applications, such as window lift plates, gears and motor housings that are used in a variety of industry segments including the automotive industry.
The Hostaform XGC POM series uses hybrid technology which improves coupling strength of POM to glass fiber reinforcement. The new series includes two core grades: XGC10 and XGC25, 10 and 25% short-glass fiber reinforced, respectively. Mechanical improvements of Hostaform XGC25 POM vs. conventional glass fiber reinforced POM include 10% better tensile stress at break, 130% improvement in Charpy impact strength and 60% increase in Charpy notched impact strength. The improved mechanical properties of Hostaform XGC make it a “best-in-class” for a glass fiber copolymer. More importantly, the series can compete with short-glass fiber reinforced PAs and PBTs. Celanese has also introduced its next-generation GUR® ultra high molecular weight polyethylene (UHMW-PE) – nearly 60 years since the engineered material was first introduced at K 1955. “We believe this new Celanese technology can deliver tremendous value to our customers across a broad range of applications,” says Christopher Davie, Celanese strategy and marketing director – GUR, Industrial, Medical and Composites. “For example, this breakthrough technology can help manufacturers of membranes and separators achieve superior material performance and processing advantages.” This will be particularly applicable to electric vehicle and hybrid vehicle manufacturers. Based on in-house testing vs. grades in the existing product line, the next generation of GUR UHMWPE enhances performance for the separators used in lithiumion batteries, which improves membrane puncture strength and provides greater design freedom. Recently, Celanese underwent a brand restructuring exercise which saw the company simplifying its brand architecture to capture in a single brand the full suite of Celanese technology, resources, products and solutions.
Automotive Industries (AI) asked Mark Rohr, chairman and chief executive officer, Celanese Corporation, what are the reasons behind the Celanese brand restructure.
Rohr: This brand change simplifies how we identify ourselves and provides a cohesive element when we share our product and capability portfolio across the diverse industries in which we participate.
AI: What are some of the changes that come with the brand restructuring?
Rohr: Last year Celanese started on a path to be a first-choice chemistry solution source. We established Global Sales and global Technology & Innovation teams to serve our customers better. Now, we are uniting our businesses under a global brand and identity: Celanese – The chemistry inside innovation. We expect this effort to improve customer understanding of our capabilities and knowledge and, over time, encourage broader discussions on how Celanese can better support them in reaching their goals and aspirations. Only our name has changed. Our products and the brands that customers buy, our manufacturing sites, our quality and our people remain the same.
AI: What are some of the highlights of the new products/ technologies that Celanese is introducing this year?
Rohr: Celanese engineered materials are designed to help automotive OEMs and tier suppliers optimize the balance of functionality, performance, aesthetics and cost via parts consolidation, cost reduction, performance, functionality, appearance, durability and recyclability. This year, at K 2013, Celanese introduced six new engineered materials based on proprietary technology that should be of particular interest to the automotive/transportation industry.
AI: What are the highlights of Celanese’s product offerings at K 2013?
Rohr: Our K 2013 exhibit showcased innovative solutions for automotive powertrain, advanced fuel systems and interior and exterior components. These are really exciting times for the engineered materials business of Celanese and its customers. Our product line of engineered materials now includes the Hostaform PTX POM series, Hostaform XGC glass fiber reinforced POM, Hostaform LPT POM, Hostaform S XT POM, Fortron ICE PPS and a next generation GUR UHMW-PE. In addition, the Celanese exhibit displayed the JEC Innovation Award-winning AgustaWestland helicopter tailplane and the expedition sled, or Pulka, used in “Mission Icefox.” Both examples demonstrate how continuous fiber-reinforced composites used in weight-optimized transportation components are a cost effective alternative to high-end lightweight materials. If you want to really want to think out of the box, these are great examples of how a development in one industry today might be translated into an innovation in the auto industry tomorrow.
AI then asked Phil McDivitt, vice president and general manager of the engineered materials business at Celanese, what are some of the highlights of your company’s new Hostaform XGC glass reinforced series.
McDivitt: Celanese is introducing several new products that will be of interest to our automotive OEMs and Tier customers. Our new Hostaform XGC POM series, which combines improved mechanical properties with a superior anisotropic shrinkage factor vs. other glass fiber reinforced resins, can give customers a competitive edge in innovative structural applications, such as window lift plates, gears and motor housings used in the automotive industry. In addition, Celanese is introducing a Hostaform low permeation and toughened POM, Hostaform extreme toughened XT POM, and Fortron ICE (Improved Crystallization Evolution) PPS. As the leading supplier of POM for automotive fuel systems, Celanese used a proprietary hybrid POM technology to design Hostaform LPT POM as a cost-competitive alternative material solution that can perform in fuel systems -even those that use “advanced fuels.” This Celanese POM hybrid technology also enabled us to create Hostaform XT grades for automotive applications – fasteners, buckles, dampening gears and housings – that require exceptional impact strength and flexibility in demanding environments. And, our Fortron ICE grades provide all the known performance benefits of Fortron PPS plus unmatched processability, which opens up significant and new design spaces in the automotive industry. This next generation Fortron PPS, with improved productivity and properties, can help customers stay competitive by reducing cycle times, scrap rates and overall production costs, as well as improve flatness and enable easier demolding.
AI: What makes the new product so much better than the earlier variants?
McDivitt: Celanese polymer scientists have improved the coupling strength of POM to glass fiber reinforcement for new level of performance in a short-glass filled copolymer. This means our Hostaform XGC POM series can challenge short-glass filled polyamide (PA) and thermoplastic polyester (PBT) products. The new series provides wider design latitude and offers features that clearly differentiate it from other short-glass fiber POM copolymers and homopolymers. Celanese also designed its Hostaform LPT POM injection molding and blow molding grades to deliver an unprecedented balance of impact and durability performance. The Hostaform LPT POM property profile can help customers increase their productivity via faster cycle times, which can save energy and lower per unit costs. The new Hostaform XT 20 and XT 90, which complement and expand the existing Hostaform S series, are designed to compete in application areas previously reserved for highly modified impact modified acetal copolymers and homopolymers, thermoplastic polyurethanes and impact modified polyamide (PA) resins. This is achieved with proprietary Celanese POM hybrid technology that allows lower levels of impact modifiers to be used while enabling significant improvements in mechanical properties and weld-line strength retention vs. competitive impact-modified POM.
AI: Tell us about the improvements in Celanese’s GUR® ultra high molecular weight polyethylene.
McDivitt: Our next generation GUR UHMW-PE is capable of delivering a step change in both material performance and processing efficiencies. Celanese is selecting strategic development customers in realizing the full potential of this exciting technology to receive samples of the next generation GUR UHMW-PE. We look forward to working closely with them in realizing the full potential of this exciting technology.
AI: What are some of the automotive applications of the product?
McDivitt: We believe this new Celanese technology can deliver tremendous value to our customers across a broad range of applications. For example, it can help manufacturers of membranes and separators achieve superior material performance and processing advantages. Based on in-house testing against grades in the existing Celanese product portfolio, our team is seeing enhanced performance for the separators used in lithium-ion batteries, better gelation that is expected to provide fiber and membrane manufacturers clear processing advantages, significantly higher abrasion resistance that can extend the life of machined parts and improved fiber strength and tensile properties for critical applications
More Stories
Professional vs. DIY Tinting: What You Should Know
New updated edition of “PXIMate” reference guide for T&M engineers available from Pickering Interfaces
5 Mistakes That Can Ruin Your Car Accident Claim