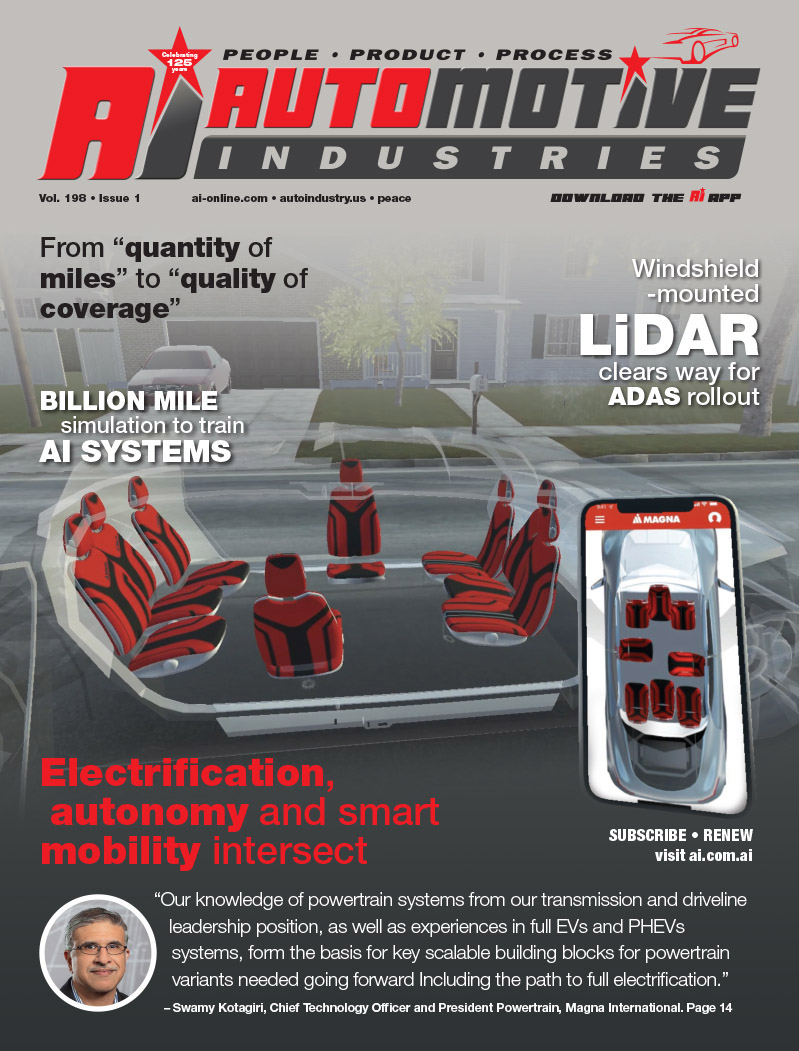
Adding strength and durability to polymers
By adding more polymers to vehicles in order to save weight and increase the green credentials of their vehicles OEMs are potentially building in a new set of challenges. Polypropylene-based materials and other plastics need to be stronger, more environmentally sustainable, lighter and more durable than ever before One of the leaders in the field of polymer stabilizer developments is Songwon of Korea, while Sabo is a key player from Italy in the area of light stabilizers.
Automotive Industries (AI) asked Thomas Schmutz, Director Global Technical Service at Songwon and Arnim Helmboldt, Marketing Director from Sabo what they see as the main trends in the auto industry.
Schmutz: There are a number of convergent trends which have a direct impact on the demand for polymers. The pressure on OEMs to reduce costs is higher than ever after the 2008 financial crisis. Together with being able to meet the demands of mass production comes the need to reduce development time. OEMs want to unify platforms – which allows for the faster development of new cars – while at the same time having maximum flexibility when it comes to design. The purchase of a car remains an emotional experience. Environmental pressures keep OEMs focused on weight savings in order to reduce CO2 emissions, and to increase the use of recycled materials. We see more and more recycled resins being used in vehicle manufacturing. Our challenge is to develop products which leave no deposit on the windshield, do not smell, do not degrade throughout the life cycle, and are more cost-effective. There is a trend to replace the more expensive polymers such as styrenes or engineering polymers with polypropylene, and to substitute polypropylene with polyethylene because the availability of shale gas is widening the cost gap between these two polymers. There is also a move from the heavier polymers such as PVC or styrenes to lighter weight polymers such as polyolefins.
AI: What are the key trends in the automotive industry where Songwon additives can have an impact?
Schmutz: Weight savings – 100 Kg weight reduction yields up to 10 g/Km reduction of CO2 emissions. We have solutions to help OEMs reduce weight further by making a solid wall thinner. A reduction in thickness decreases intrinsic stability, and this can be counterbalanced by the use of more (or better) stabilizers. Factors that need to be taken into account include reaction between the stabilizer and blowing agents, and the absorption of additives by the fillers, which means that the additives are as a result not available in the polymer matrix to protect the polymer. Our additives also ensure that there is no degradation throughout the life-cycle. Thermoplastic polymers such as PP, TPO, PE, PUR, PVC, and styrenes would not be suitable for automotive applications without stabilizers. Stabilizers allow the OEM to guarantee components under the hood, as well as molded exterior components for the life-time of the vehicle. The durability of plastics can be significantly improved with the right choice of stabilizers. This allows reduction of CO2 emissions and the use of fossil resources because fewer articles are manufactured. The key point here is that stabilizers allow extension of life time (durability), reduce the amount of plastic required, and so decrease the emission of CO2 and the consumption of fossil resources. When it comes to recyclability, downcycling can be delayed or avoided with early top-up stabilization. Typically, stabilizer levels present in the polymer are not sufficient for the recycling process, and “top-up†stabilization is needed. New standards require new solutions. The industry standards on VOC, FOG and total carbon emission are changing drastically. State-of-the-art stabilization systems are not able to meet these new standards.
AI: How can you replace engineering polymers with polypropylene for under the hood applications?
Schmutz: Songwon’s Global Application Center development facility in South Korea is in the process of developing a new stabilization system, which we call “Concept Alphaâ€. This concept will almost double the lifetime of PP at aging testing temperatures of 150° C. PP is very sensitive to thermo-oxidative degradation. There is severe degradation during melt conversion in the absence of stabilizers. Classical state-of-the art stabilizer systems reach only a certain performance level, because additives exceed solubility level in PP, and a further addition has only a marginal effect on the long-term thermal stability of PP. Our “Concept Alpha†is able to overcome these limitations.
AI: What is the right strategy to reduce volatiles and odor for car interior applications?
Schmutz: Classic stabilization systems typically meet most of the long-term thermal stability criteria of the automotive industry. However, they have a number of limitations related to extraction resistance, interaction with filler materials, interaction with carbon black, resistance to external chemicals (e.g. chlorine) , compatibility with selected UV additives, and indirect food contact (low SML of DSTDP). Songwon is offering three strategies to overcome the performance limitations of the classic systems. 1. SONGXTENDâ„¢ 2121 stabilizer is able to meet the long-term thermal stability level of classic additive systems, while reducing the sulfur content by 60%. 2. SONGXTENDâ„¢ 2122 stabilizer equals the long-term thermal stability level of classic additive systems. The reduction of the sulfur content is 30%, and the system offers better cost performance. 3. SONGXTENDâ„¢ 2123 stabilizer is a completely sulfur -free system, which means it is odorless. The system cannot meet the long-term thermal stability performance level of the classic sulfur-based system, but is better than the next-best alternative.
AI: How can an additive supplier make a car bumper formulation – automotive exterior application – more cost efficient?
Helmboldt: Light stabilization formulations for car bumper systems based on TPO were established many years back. However the requirements for increased light stability combined with ancillary properties such as no blooming of the additives and excellent paint adhesion persist. Sabo has grown to become the second biggest supplier of monomeric and polymeric HALS (hindered amine light stabilizers) over the last years. We operate at two fully backward integrated manufacturing sites in Italy. We support our customers through security of supply and economy of scale. Sabo has invested substantially into the form giving abilities in order to provide safe, low dust and free flowing granular materials. SABO®STAB UV 70 and SABO®STAB UV 91 50PP light stabilizers are two of the products largely used in automotive applications. Sabo entered into a distribution partnership with Songwon for its light stabilizers last year. The product ranges of Sabo and Songwon complement each other to form the second largest supplier of polymer additives. Our partnership extends to joining resources in research and development. The outcome of the joint development resulted in a new solutions for automotive applications. These products are being promoted to selected customers under the trade names SABO®STAB UV 210 light stabilizer and SABO®STAB UV 228 50PP light stabilizer. They represent synergistic blends with SABO®STAB UV 228 50PP dedicated for interior applications and SABO®STAB UV 210 outperforming standard UV stabilizers in automotive exterior applications like TPO bumpers, when criteria like surface and color protection and gloss are key quality requirements. AI: What is the right light stabilizer solution for an automotive interior application meeting the more stringent requirements of the automotive industry on VOC / FOG and total carbon emission?
Schmutz: The automotive industry recently changed the requirements of FOG. One of the reasons for this change is that nowadays new cars are stored outdoor for couple of months in case the market slows down and the off-take of the car dealers is reduced. Volatiles coming from additives in the polymer settle as a deposit (FOG) on the interior windscreen. This needs to be removed manually before the car gets sold, which adds to the costs. The other reason for reducing volatiles in the car interior is the reduction of odor. Again, in most cases low molecular weight components of the polymer or additives are the major contributors.
Helmboldt: The Songwon / SABO partnership understands the needs of the automotive industry very well and in addition to SABO®STAB UV 228 50PP light stabilizer further solutions for interior applications are under development. Our light stabilizers and new solutions offer excellent light stability for applications such as dashboard, door panels, rear shelf and others. They are also able to meet the new requirements of the automotive industry in terms of low VOG, FOG and total carbon emission
More Stories
Automotive Industries (AI) Newsletter April 2025
How to Create the Ultimate Off-Road Vehicle Garage: A Practical Guide
GlobalLogic Pioneering Software-Defined Vehicles, AI Innovation, and Sustainable Solutions for the Future of Automotive Mobility