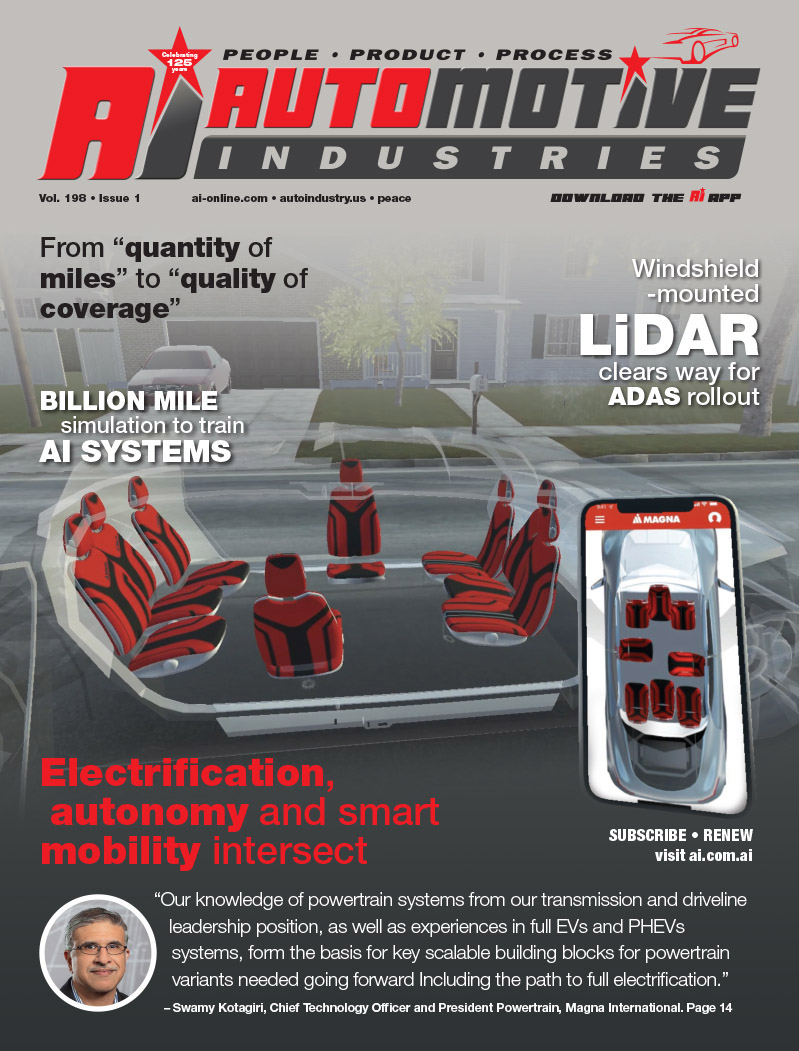
Battery management for both hybrids and fully electric vehicles is focusing on the individual cells. By balancing the cells, it is possible to halt a battery’s capacity decline, increase operating time, and improve the overall system run-time. One of the leaders in the development of battery management is Austrian company ams (formerly austriamicrosystems), which develops and manufactures high performance analog semiconductors.
Automotive Industries (AI) asked Bernd Gessner, Exect. VP & General Manager, ams Automotive Business Unit, why cell monitoring and balancing are such important functions in battery management.
Gessner: Without the balancing of a cell stack which accumulates differences in state of charge for the individual cells over time, the cell with lowest or highest state of charge (SOC) is a weak point. It can be easily overcharged or over-discharged, while other cells only undergo a partial cycle. This has a very negative effect on the ability of the battery to store energy. It leads, for instance, to reduced run-time for battery-driven power tools or limits the range of electric vehicles. The architecture developed by ams is not a direct response to car manufacturers’ specifications, but rather a response to the difficulties that battery manufacturers and BMS electronic system integrators are faced with. ams developed the AS8506 ASSP with funding support from EU research projects E3Car and Estrelia, where European wide experts come together. Today battery management systems capture individual cell voltages in a more or less time-deterministic way and communicate them to a powerful host controller.
Comprehensive data logging and software functions are needed to perform the required computations for cell diagnosis, functional safety, state of charge (SOC), state of health (SOH) data capture and balancing decisions. This approach is quite complex and costly. It requires robust communication architecture across voltage domains, many highly accurate measurement systems, a powerful host controller, the development and qualification of complex software in a safety critical system and the provision of redundant components to support functional safety. As the electric vehicle automotive community reported severe difficulties in fulfilling the requirements with existing products on the market, ams decided to rethink the entire subject.
AI: What makes the product unique?
Gessner: The AS8506 is the first cell monitoring and balancing IC on the market that is able to overcome the obstacle of the communication load. It does this by shifting the majority of the monitoring and balancing functions from software to hardware using an autonomous, highly integrated balancing solution which allows simultaneous measuring with reduced communication. The AS8506 is also a small form factor solution, having the balancing switches integrated and using sequential balancing.
Just one external discharge resistor is needed per seven cells. An even more efficient active cell balancing mode can be configured together with the passive solution. In this mode cells below the reference voltage will be charged in preference to the others through a small fly-back converter and the integrated switches. The autonomous approach enables communication without the need for fast data management by a central controller. This drastically reduces the amount of data to be processed, meaning that a smaller, down-sized battery controller can be used with much less software effort in a safety-critical BMS system.
AI: Where do you see this being used?
Gessner: Generally, this IC covers all lithium-based cell packs, as well as EDLCs (Electrical double-layer capacitors “supercapacitors”), in applications such as:
• Mobility: 12V and 48V automotive applications, e-mobility, motorcycles, e-scooters, e-Bicycles
• Consumer electronics
• Power tools
• Off-grid energy storage
• As well as many more applications
AI: Tell us about the dual voltage onboard power supply and why it is important?
Gessner: The implementation of the 48V power voltage system in passenger cars will certainly help to reduce power losses and CO2 emissions. The 48V power supply enables a much more efficient way of supplying power-consuming components in the vehicle, while reducing the wiring costs and weight. The standard operational voltage level is below 60V, meaning that no additional safety measures for human beings are required.
In order for this implementation to be successful, however, the entire supply chain for electronic components – including semiconductor suppliers, manufacturers of electronic control units and component and system suppliers – will need to examine the impact on their products carefully. For the semiconductor industry a significant and costly investment is needed to be ready for the technical specifications of the 48V power supply. As each semiconductor fabrication process is designed to support one narrowly-defined voltage domain, the automotive industry’s 48V domain, with its demand for a minimum 70V break-through voltage introduces a new process requirement. The effects of this, including the trade-off between figure of merit and voltage capability, are the subject of much debate in the industry. There is not much experience among car manufacturers and suppliers with the new 48V power supply. Devices connected to the battery voltage and the communication wiring will require even higher break-through voltage than 70V, most likely 90V. This means that process technologies need to be developed by the semiconductor companies, and be implemented in their production lines with stringent automotive qualification.
AI: What in your mind is the role of semiconductor manufacturers as far as automotive OEMs are concerned?
Gessner: Semiconductor companies will be the enabler for the dual-voltage supply in vehicles. With the first ICs now designed for the 48V grid, the implementation costs for OEMs are known. Reliability, safety functions and cost efficiency are the key for this new technology, and semiconductor suppliers play a major role in achieving these goals.
AI: Is there a connection between battery management solution and the dual-voltage supply?
Gessner: Unlike the existing 12V vehicle battery, the 48V battery will be Li-ion-based which requires a battery management system. This includes the ability to measure current and cell voltage, functional safety features, cell balancing, a driver for the battery disconnect switch, a BMS controller and communication with the in-vehicle CAN bus. In the dual-voltage supply, the 12V and the 48V net are typically linked together through a bi-directional DC-DC converter. The dual-voltage supply system requires 48V energy storage, typically a Li-Ion-based 48V battery (LFP, LFP/LTO chemistry). As mentioned, Individual cells need to be monitored at all times to stay within the safe operating area. The 48V battery has high energy content and therefore makes a battery disconnect switch mandatory. ams offers its flexible battery management standard products which perfectly fit the application for a 48V BMS. Battery pack current is measured through a shunt synchronous unit with battery voltage by the AS8510. Cell voltage monitoring, measurement and balancing is handled by the new AS8506.
Communication to the vehicle’s CAN bus and power supply may be accomplished with the AS8601, a supply IC with high-speed CAN interface AS8506 launch ams released a cell monitor and cell balancer IC – the AS8506 during the October VDI Congress “Elektronik im Kraftfahrzeug in Baden-Baden, Germany”. The conference, held on the 16th and 17th of October 2013, was the launch pad for the AS8506. It is the first cell balancing product which can be operated completely without micro and serial communication thus reducing software complexity while offering high accuracy. It allows for simultaneous cell capture across the entire cell stack which improves noise margin for balancing decisions. It can balance currents as low as 100 mA to ensure maximum battery life, says ams
More Stories
Professional vs. DIY Tinting: What You Should Know
New updated edition of “PXIMate” reference guide for T&M engineers available from Pickering Interfaces
5 Mistakes That Can Ruin Your Car Accident Claim