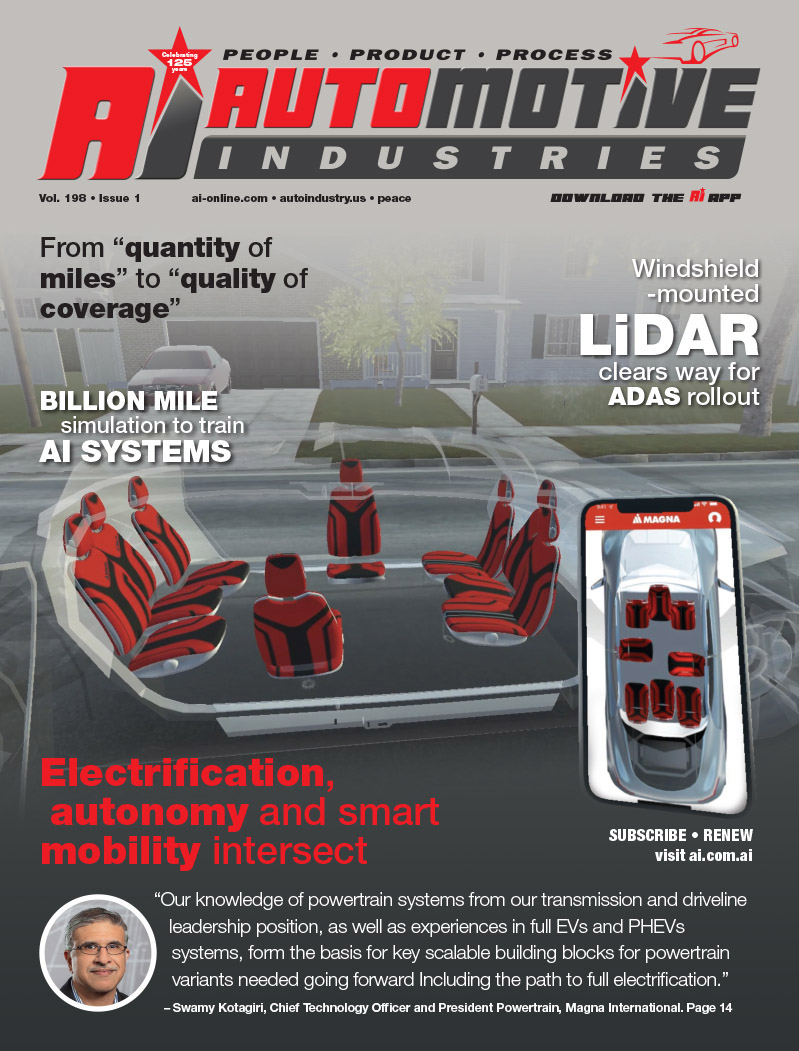
A new high-tech production capacity at the assembly facility for the Mitsubishi Motors Corporation (MMC) Catalão, Brazil is putting the company in the fast lane in the race for market share in the region.
The investment is through the company’s exclusive distributor and assembler MMC Automotores do Brasil. (MMCB). Mitsubishi’s current cycle of investment started in 2011 with the announcement that the company would invest US$638 million in the country. By 2012 Brazil had become the fourth largest automobile market in 2012 with annual sales of 3.6 million units. The MMC plant in Catalão (Goias) covers 11,000 m2, and can produce 25 vehicles per hour.
MMC first commenced assembly through MMCB in September 1998, with production centred on three SUV models in the recent years. In 2013 the plant started assembling the ASX, which is a global strategic vehicle and a core model for MMC Production of the ASX started in Japan, with lines opening in the United States, Indonesia, and China prior to Brazil. One of the technology suppliers to the plant is Geico of Italy, which was responsible for the paint plant.
Automotive Industries (AI) asked Rubens Juquiram, Mitsubishi’s Director of Supplies, what the brief from Mitsubishi had been in the design of the new facility.
Juquiram: The objectives were to improve quality through the use of new technologies, to reduce energy consumption, and to minimize maintenance. We were also looking for simplicity in design and operation. The curing paints and other materials is one of the main contributors to the quality of car coating. In this way the curing process is optimized to meet the requirements of different paints, products and product material types. Environmental protection is provided by using both recuperative and regenerative thermal oxidizers, which are integrated with a heat recovery circuit. Forced air cooling zones combine simplicity and effectiveness to meet the specified results.
AI: Why did Mitsubishi choose Geico for the project?
Juquiram: We have established a good relationship with Geico as we have worked together to find solutions to challenges. Together we have developed new technologies for energy saving and advances in the design of paint application systems, such as the compact Amir aluminum booth. The Amir booth is built with aluminim framework and partly or fully glazed walls. The patented profiles which were developed together with the unit structural principle make its design modern and ergonomic.
AI: What Geico technology has been installed in the Brazilian plant?
Juquiram: A number. To start with Geico uses advanced software to simulate the automotive body flow in a paint shop. The simulation includes cycle times, working sequence timing of the various system sections and the most critical points of the production flow, so as to determine the simplest, most economical and efficient layout solutions. Using the simulation software we are able to optimize the design.
Equipment in the plant includes:
Hydrospin Plus, which is recognized by OEMs as one of the best scrubbers for the paint application booths. It is the most modern and efficient air washing system on the market. The technology was developed from the first system developed by the Drysys company some 50 years ago. The design was improved on over the years first by Haden, and then by Geico. This system is based on the concurrent washing principle of mixing exhaust air extraction with water in order to remove paint overspray particles left over from the painting process from the atmosphere.
The J-Jump 4C conveyor system is designed to keep the paint shop compact. This process is easily adaptable for different vehicle models, thus allowing a flexible response to market needs.
Robots: Paint is applied by robots installed on the walls of the paint booth. Thanks to a close cooperation with its main partners of robots and application equipment, Geico is able to offer solutions for the automatic application of paint in a very short time. All the solutions proposed make use of the latest products and technology.
In addition, Geico is a leader in the fields of application systems for paint, putty, soundproofing sprays and various protection materials. In partnership with the major paint producers, Geico develops new application technologies through which it improves the quality performance of coating processes.
VFD, to avoid electrical energy surpluses: There is wide use of VFD (inverters) on electric power utilities which have a variable load, are oversized for maintenance purposes or for performance back-up and this allows a significant reduction in power consumption.
A Regenerative Thermal Oxidizer (RTO) exhaust system to recover energy, RTO is an energy-saving process that oxidises and decomposes VOC´s (volatile organic compounds) at 850º and higher.
AI: What are the advantages of the new paint shop technology in terms of energy consumption?
Juquiram: The new MMCB paint shop is one of the few paint shops in the world where the design is focused on energy saving. This has helped “green” the MMCB plant as vehicles are painted using lower levels of energy than with older systems.
AI: Are you proud of your plant?
Juquiram: Yes, the new plant meets the all the requirements of MMCB. We have a flexible and sustainable manufacturing system in place.
More Stories
Professional vs. DIY Tinting: What You Should Know
New updated edition of “PXIMate” reference guide for T&M engineers available from Pickering Interfaces
5 Mistakes That Can Ruin Your Car Accident Claim