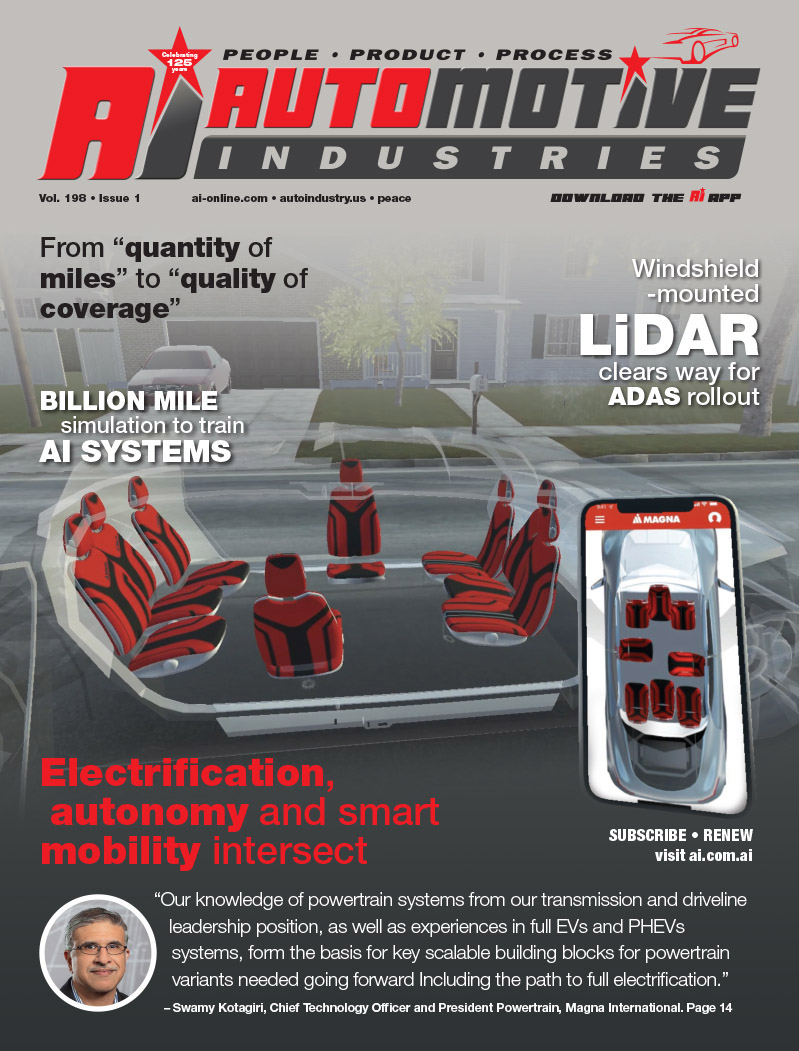
Choosing an interface for the interior of the vehicle plays a major role in helping a brand to distinguish itself from its competitors through the look and feel and innovations in functionality.
Automotive HMI (human machined interface) design has become a significant tool for brand differentiation for all automotive segments. The arrival of the connected car and the development of automated driving are main drivers. Information technology and software that enables the next generation of multimodal, multi-touch and multi-zone HMI design is the key for OEMs going into the future, according to Preh, the 95-year-old business which has focused on the automotive industry exclusively as an electronics supplier since 1988.
In July 2014, Preh won first place for “Innovative HMI Technology” in the first CAR HMi Awards held in Berlin. Preh’s Head of Advanced Development Dr. Matthias Lust said, “We are pleased that our center console concept was chosen by an independent jury of experts as the first-place winner. More and more, smartphones and tablets are influencing the HMI concepts of future vehicle generations. This award shows that we at Preh have addressed the right issues in our product development, and that ease of operation, as well as driving safety, are not incompatible.”
The company recently announced that is producing three control systems for the new BMW X5. They were developed at Preh’s global headquarters in Bad Neustadt, Germany. Technical solutions that have already proven themselves in other BMW models include the iDrive Touch Controller and the Driving Experience Control.
Preh is guided by the belief that the ultimate goal for HMI experts is the creation of an interface that is both engaging, functional and easy to reach and use, thus avoiding driver distraction. This has become even more important in the automotive cockpit, where the number of instruments and functions directly accessible to the driver has kept rising steadily over the years.
Preh’s functionality philosophy is also represented by the climate controls for the new Audi TT. The Audi design integrates the controls into each of the five air vents in the TT interior. Preh designs both the interfaces and the control electronics and software. Preh has developed the battery management ECUs for the fully electric BMW i3 and i8. In addition, it is supplying the iDrive controller for the vehicles’ interiors.
Preh has also developed ECUs for BMW’s Battery Management System (BMS). The ECUs are designed to extend battery life through intelligent control that includes the charge and discharge cycles. “The continuous and effective investment in R&D is the key success factor of our strategy. It not only includes product development, but also improves manufacturing technological levels, competitiveness and innovation,” says Preh President Nick Lontscharitsch.
With ever more stringent emissions targets being introduced and a corresponding surge in EV and HEV production globally, an in-depth understanding and maximum utilization of the battery management system is more important than ever. In the race to optimize performance and reduce costs, an intelligent battery management system is necessary to lengthen battery life, thereby reducing vehicle cost over its entire lifetime
For reliability, performance and longevity of battery packs being engineered into HEV, PHEV and EV drive-trains, a key factor is the electronics employed in the BMS. This year, Preh announced that it had developed the battery management ECUs for the fully electric BMW i3 and i8. In addition, it was supplying the iDrive controller for the vehicles’ interiors.
In 2014 Preh was singled out by the BMW Group in the categories of quality and productivity for the annual BMW Supplier Innovation awards. Klaus Draeger, member of the Board of Management of BMW responsible for Purchasing and Supplier Network, explained “innovation is a decisive factor in a vehicle’s market success. Many customers ultimately opt for the car with the most impressive innovations. In fact, innovations are a key driver in our role as a pioneer in shaping the mobility of tomorrow.”
Preh was nominated for the iDrive Controller building block, as well as for a 3-D test station for control surfaces. “As a development partner and series supplier to BMW, we have worked with our customer to bring numerous innovations to the road since the 1980s.”
Automotive Industries (AI) asked Lontscharitsch to describe what role the company played in developing the BMW iDrive control system.
Lontscharitsch: This product family shows what great potential a building block design represents. The basic structure of the control panels and of the central rotary/push controller knob could be implemented consistently, while the surface panels relevant to the brand-specific design were varied. Without this similar parts concept clearly more effort and cost would have been required.
Proportions vary between the different carlines and designs. Based on the components developed for the BMW brand, the percentage is higher for the Rolls Royce versions, and lower for the Mini brand versions. The advantages of an equal parts strategy is seen in the development costs and project investment. It was possible to integrate all variants in the existing installation and testing lines—with appropriate extensions. The equal parts concept saves costs, especially for variants that run in small quantities. For this achievement of improved economy our customer BMW nominated us for their Supplier Innovation Award 2014.
AI: Tell us a little about the HMI Award Preh recently won.
Lontscharitsch: Our center console concepts are always about new ways to minimize driver distraction while operating the controls. In the sense of intuitive controls, the latest technologies developed at Preh are applied in combination with high-quality materials for a modern, elegant design. One of the innovative technologies of the HMI award-winning center console concept will already be seen in a further development in series production in 2015. Further series start-ups are imminent. The main differentiators are genuine glass surfaces, displays with optical bonding technology and touch applications with haptic feedback.
AI: What role do you see Preh playing in connected cars and highly automated driving?
Lontscharitsch: The currently existing control system trends will be strengthened. We see a trend towards larger, high-quality displays and black panel technology. This means that only information which is relevant to the current driving situation is shown to the driver. New operating scenarios and HMI designs will be developed for partially automated driving.
AI: How have you overcome the challenge of getting the balance right between safety/driver distraction and new features?
Lontscharitsch: The challenge for new HMI concepts is for the operation and display to be designed like smartphone and tablet PC interfaces. At the same time the driver should not be distracted. Over the past few years we have looked intensely into several projects with this task in mind, and can already offer proven concepts. There is, for example acoustic and haptic feedback for touchpads and touchscreens to reduce distraction during operation. Preh currently has controls with touch applications with various OEMs in series production. Our wide range of available in-house technologies and special know-how for high-quality surfaces and haptics are prerequisites for the development and production of innovative HMI concepts. This enables us to rapidly prototype new approaches, and to evaluate their suitability for series production. AI: A new kind of component design is that the climate controls are integrated into the air vents of the new Audi TT. What were the challenges for this design and may it be seen in other cars soon?
Lontscharitsch: The integration of controls with visual display in the air vents was a project with challenges, mainly because of the very limited packaging space. Each of the five individual knobs has a very compact design and the climate control functionality is distributed between these knobs. Also, the corresponding assembly processes were a challenge. In order to ensure a similar high-quality feel for each individual module, all individual part-manufacturing tolerances in the product review and development process were repeatedly and critically scrutinized. These findings flowed back into the construction and assembly process. This is a good example of what can change when the center console is conceived as a unit and the individual components are closely coordinated. With the air vent skills of our stakeholder Joyson, we will be able to offer complete systems in the future.
AI: Any other new developments that the industry should stay tuned-in to?
Lontscharitsch: In the near future touchscreens with haptic feedback will help alleviate the driver distraction issues associated with this type of control interface. Series production readiness of such improved touch screens is in the works at Preh advance development.
More Stories
Cybord warns of dangers of the stability illusion
Automotive Industries interviews Bahar Sadeghi, Technical Director, Car Connectivity Consortium (CCC)
Hexagon’s MAESTRO reinvents CMM systems through digitization