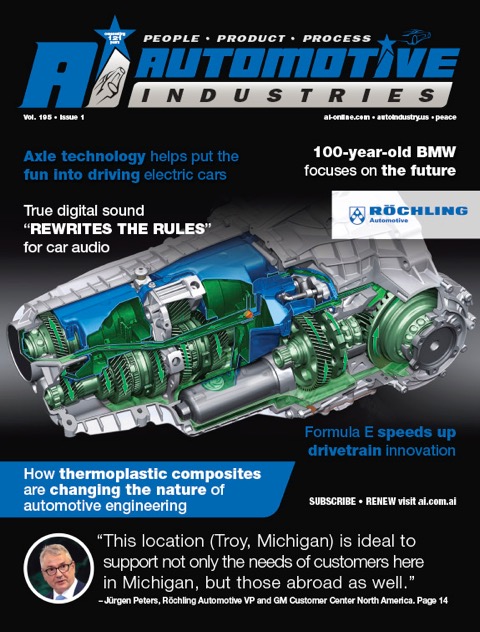
Ongoing breakthroughs in the development of thermoplastic composites are changing the nature of automotive engineering.
One of the companies at the head of the field in the development of thermoplastics is Röchling Automotive. Automotive Industries follows the evolution of thermoplastics through this overview of the Röchling product portfolio.
Body elements
In the new field of complete car body elements made of composites, Röchling has utilized both its Stratura™ material and its Softlofting™ technology to create a lightweight car-body floor sandwich structure, which combines acoustic and thermal insulating layers. More recently the company has added Stratura Hybrid™, further lifting the structural performance by integrating aluminum elements. By replacing conventional floor systems with composites OEMs can save up to 15 kg (33 lb) of weight, according to Röchling.
The integrated sandwich floor (ISF) solutions of Röchling Automotive are produced in a one-shot process and accelerate the evolution of thermoplastic composites in automotive engineering.
In addition to Syntralite™, a self-extinguishing, lightweight material, Röchling offers Seralite™, a lightweight construction material that does not burn, even when contaminated with highly flammable fluids. Additionally, the company offers Peralite™, a cost-effective underbody version that provides superior aerodynamic functionality. It indirectly supports the trend toward an increasing degree of underbody closure in the small car segment.
Reducing noise
Loud ambient noise considerably reduces driving comfort. Knowing that air intake systems offer great potential for acoustic optimization, Röchling has developed a new central air distribution manifold for air conditioning systems. This lightweight solution has a sandwich structure, allowing the air noise at maximum air flow to be reduced by up to 10dB (A) in certain frequency ranges.
For the upper part of the air conditioning duct, Röchling engineers utilize Seeberlite™, a noise-reducing material made of LWRT. Its 80% porosity in the open core layer allows for excellent acoustic characteristics due to improved sound absorption.
Reducing gearbox friction
Röchling has developed a transmission oil delivery system that allows a direct gravitational lubrication, instead of the individual gears rotating through the oil in the sump. Unlike traditional oil delivery systems where gears lose kinetic energy when rotating through the oil sump, Röchling’s solution systematically lubricates and allows gears to rotate more freely. Less resistance results in a saving of two grams of CO2 per kilometer. This system is currently in series production with Audi.
Röchling has been presented with a 2016 Automotive News PACE Innovation Partnership Award, in conjunction with Audi and FTE Automotive, for this oil delivery system. Röchling also was named a PACE award finalist in the product innovation category for the same technology.
Optimized tank solutions
According to forecasts, approximately 90% of all diesel-powered vehicles will have a SCR (selective catalytic reduction) tank system in 2017. In response to the growing demand for smaller SCR tanks designed to fit into tight spaces, Röchling has developed an acoustically optimized model. As one of several contributions to the field of SCR tank systems, Röchling has designed anti-slosh measures to improve driving comfort. Röchling Automotive was honored at the 16th SPE (Society of Plastics Engineers) Automotive Innovation Awards in the powertrain parts and components category for its SCR filling system, which eliminates odor.
Clean air
The use of composites has eliminated many of the constraints in the design and manufacturing of air filter and induction housings. In response to the growing need to simplify the air filter and air induction design process, Röchling has developed software that identifies optimum air filter design, as well as predicting service life and performance in a matter of hours and at lower cost.
Röchling’s program utilizes manufacturer information such as vehicle and engine data; the driving profile; the filter’s service life; dust capacity targets; and specific packaging data, including pleat height and distance between pleats.
Röchling strives to optimize manufacturing processes through its alternate assembly techniques. It uses clean manufacturing technologies that are particle-free alternatives to vibration welding. They include JectBonding™ for charge-air tubes, and Sealbonding™ to connect intake manifolds.
Sealbonding™ supports flexible design shapes and joins complex, multi-part components in a single step without any unwanted particles or weld flash. The solution is proven to provide an exceptionally durable joint, with the mechanical resistance of the seals being up to five times higher than that of traditional welds. This process ensures the component shape is optimized for the injection molding process, eliminating the need for a two-dimensional parting line consistent with vibration or spin welding. As a result, Röchling’s solution overcomes the technical production hurdles previously faced by automotive designers.
Optimizing charge-air tubes
Improved decoupling movements between the engine and chassis are increasingly necessary as automakers continue to downsize engines. Röchling’s developers optimized this process by creating an integrated soft blow-molded solution that is 68% more heat-resistant than comparable products, replacing the previously used mounted rubber elements.
Active Speed Lips
Designed for the SUV segment, Röchling’s Active Speed Lips control the air flow around the tires. What was previously a passive component can now be controlled electronically through compact actuators and be individually adjusted and retracted.
Optimized air flow leads to improved fuel consumption and decreased drag, resulting in improved aerodynamic function overall.
Active Air Dam
The Active Air Dam enhances air flow along the lower side of the front of the vehicle. Measurements in wind tunnels have proven that fuel consumption and emissions can be significantly optimized using Active Speed Lips or the Active Air Dam. To avoid damage caused by obstacles, the Active Speed Lips and Active Air Dam are retracted when a vehicle drives slower than 43 miles per hour (approximately 70 km per hour).
Front grilles
For most automotive manufacturers, using distinctive front-end grille designs in vehicle development is part of a brand strategy. Conversely, these grille designs may limit functionality of the vehicle due to reduced airflow. To address this, Röchling utilized its expertise in actuating elements and kinematics to develop the vertical active grille shutter (AGS), which uses vertically arranged vanes. This allows for a high degree of integration into the vehicle design while maintaining functionality. With this concept, the vane system is installed directly behind the radiator grille, even in tight packaging geometries, to achieve optimum air flow.
A full integration of the AGS directly into the design grille blends styling with maximum aerodynamic efficiency. This Röchling solution is called Evolution II Style.
More Stories
DuPont materials science advances next generation of EV batteries at The Battery Show
How a Truck Driver Can Avoid Mistakes That Lead to Truck Accidents
Car Crash Types Explained: From Rear-End to Head-On Collisions