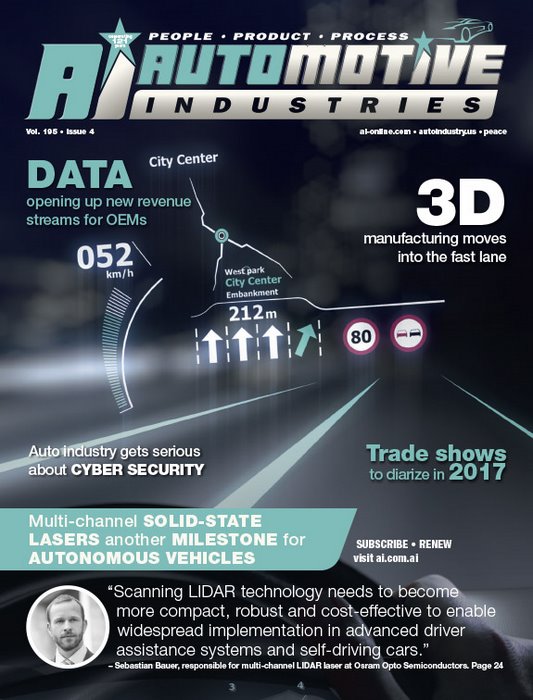
LIDAR (light detection and ranging) technology plays a key role in supporting cameras and radar in the development of advanced driver assistance systems (ADAS), and ultimately semi-autonomous and fully autonomous driving systems.
The introduction of multi-channel solid-state lasers with an exceptional vertical field of vision marks an important advancement for scanning LIDAR sensors. They enable vehicles to generate an accurate, three-dimensional image of their surroundings and use this information to initiate the appropriate driving maneuvers.
LIDAR works on the basis of the time-of-flight measurements (ToF). This involves emitting a laser pulse, which hits an object and reflects back onto a detector. The distance to the object is calculated from the time of flight of the laser beam. LIDAR has already started to feature in some automotive applications, such as emergency brake assist.
The focus is currently on two different technologies: Flash LIDAR systems send out a high-intensity, wide angle laser burst, register the reflected light pixel by pixel using a detector array and create a 3D image of the surrounding area based on the time-of-flight. Scanning LIDAR systems sweep a narrow horizontal beam over a certain segment of the car’s surroundings. For each pixel they record the time of flight of the reflected light and produce a high-resolution 3D map of the environment. In most cases the laser beam is mechanically deflected, making the systems relatively bulky. Some solutions also mount several laser diodes above one another to extend sensing to the vertical field of view.
Automotive Industries (AI) asked Sebastian Bauer, head of multi-channel LIDAR laser at Osram Opto Semiconductors, what role lasers play in the driver assistance systems.
Bauer: Our pulse laser diodes have been in use in cars for 10 to 15 years. They are used to measure distance in adaptive cruise control systems. That is how we have become involved in the development of laser sensors for advanced driver assistance systems and for autonomous and semi-autonomous cars. Scanning LIDAR will play a major role here, but the units need to become smaller, less expensive and more robust. Lasers are a key factor in this equation, not only terms of achievable optical power, but also and as an enabler of innovative sensor designs.
AI: What sets your new laser apart?
Bauer: It is an edge-emitting laser that sends out four perfectly parallel beams, which is a developmental milestone that has not yet been matched. We produce four laser diodes next to one another in a single production step, so they are precisely aligned with one another but can be individually controlled.
At present our customers mount several individual diodes above one another to enlarge the vertical field of view. This new bar means they no longer need to spend time laboriously aligning individual light sources.
The extremely short switching time of less than 5 nanoseconds is a prerequisite for scanning LIDAR using MEMS mirrors. The pulse duration of our laser diodes was previously in the 20 nanosecond region. Short pulse duration is also required The new 4-channel LIDAR laser module from Osram Opto Semiconductors delivers perfectly parallel laser beamsan thus allows for scanning LIDAR systems with a large vertical field of view.
to operate the LIDAR system the high optical output required for long ranges. Our laser delivers peak optical power of 85 watts per channel. The short pulse duration and low duty cycle of 0.01% ensure that, even at such high outputs, we meet eye safety standards.
AI: Could you give us a brief outline of its other technical features?
Bauer: The laser is based on our nanostack laser diodes, which have a wavelength of 905 nanometers and three emission centers
per chip. And since we have increased their optical output from 75 to 85 watts peak power at 30 amps, the 4-channel laser emits four times 85 watts. It is mounted together with a capacitor and control circuit on an 8 x 5 millimeter circuit board. The four laser channels are activated one after the other to avoid overheating. The entire module is surface-mountable, which greatly simplifies assembly in comparison with the through-hole components generally used at present. With an operating voltage of 24 volts, the laser is also automotive-ready.
AI: Osram partnered with Innoluce (recently acquired by Infineon) to demonstrate LIDAR scanning using a microelectromechanical (MEMS) system for the first time. What are the benefits of this technology?
Bauer: Scanning LIDAR technology needs to become more compact, robust and cost-effective to enable widespread implementation in advanced driver assistance systems and self-driving cars. In response many providers are developing MEMS-based solutions that replace mechanical deflection with micro-electromechanical mirrors to direct the laser beam. As well as being more compact and less susceptible to wear and tear, these pave the way for lower-cost solutions. Our partner Innoluce has developed a MEMS mirror with an area of 2.7mm x 2.3 mm, which is large enough to redirect the four parallel beams of our new laser. The result is a system covering a 12° vertical and 30° horizontal field of view. The MEMS chip is operated at up to two kilohertz – another unique feature that enables the system’s high resolution of 0.3° horizontally by 0.5° vertically. In daylight, the range for detecting vehicles is at least 200 meters, and 70 meters for pedestrians.
AI: When will the new laser be on the market?
Bauer: Samples of the new 4-channel LIDAR laser will be available early in summer 2017, with market launch planned for 2018.
More Stories
Professional vs. DIY Tinting: What You Should Know
New updated edition of “PXIMate” reference guide for T&M engineers available from Pickering Interfaces
5 Mistakes That Can Ruin Your Car Accident Claim