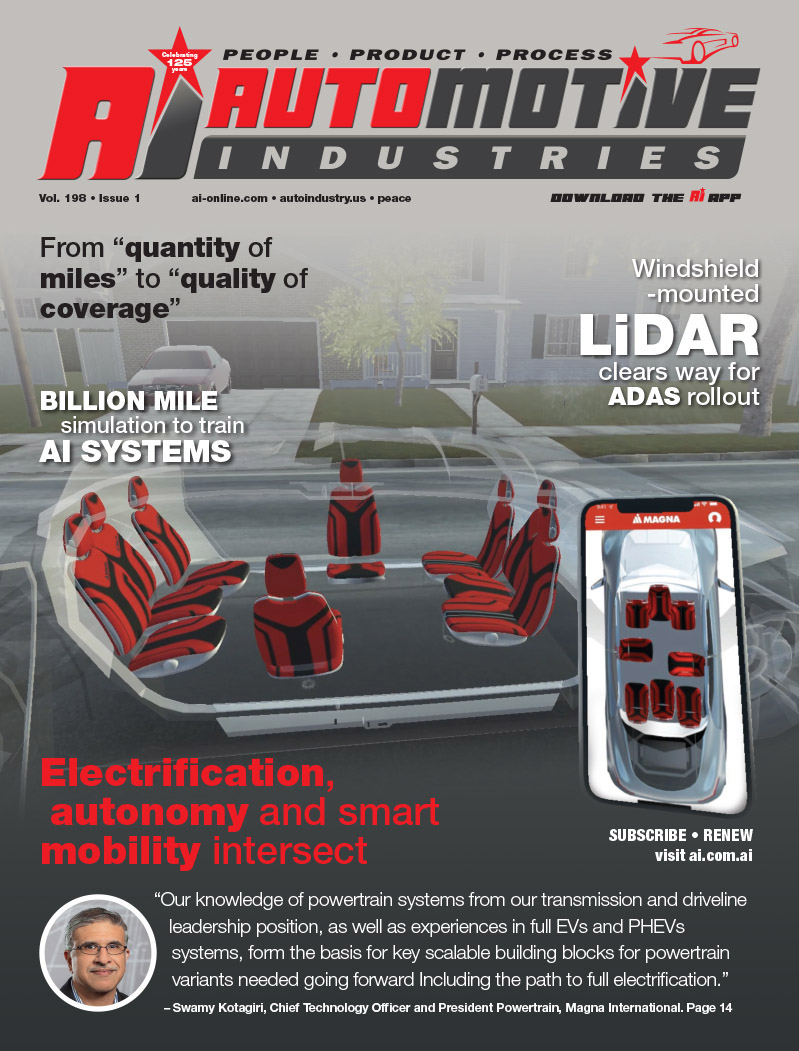
Since 2012 the Rolls-Royce Phantom Series II has been assembled using components from 3D printers in series production. In total over 10,000 plastic components were produced for serial vehicles using additive manufacturing technology. The company says its Additive Manufacturing Centre at the BMW Group’s Research and Innovation Centre (FIZ) has been using 3D printers to produce parts for the new Rolls-Royce Dawn since the start of 2016.
“Additive technologies will be one of the main production methods of the future for the BMW Group – with promising potential,” says Udo Hänle, Head of Production Strategy, Technical Integration. “The integration of additively-manufactured components into Rolls-Royce series production is another important milestone for us on the road to using this method on a large-scale. By utilising new technologies, we will be able to shorten production times further in the future and increasingly exploit the potential of tool-less manufacturing methods,” he says.
Components produced using additive manufacturing include high-visibility plastic holders for hazard-warning lights, centre lock buttons, electronic parking brakes and sockets for the Rolls-Royce Phantom. Mounting brackets for fibre-optic cables are the main use case in the Rolls-Royce Dawn and the company will install several thousand of these clips throughout the model lifecycle. The BMW Group says additive manufacturing has been proven to manufacture components with complex designs faster than conventional methods, and without any compromise on quality or aesthetics.
New and upcoming planar printing technologies enable considerably faster production times than conventional point-to-point 3D printing methods. Beamers or infrared sources are used to expose the full surface, rather than point-to-point, high-priced light sources, such as CO2- or UV-lasers as used in Selective Laser Sintering. Thus the potential of Additive Manufacturing is constantly growing as the printing of bigger parts or larger quantities of a serial component becomes more and more cost-effective.
Automotive Industries (AI) asked Dr Jens Ertel, head of the BMW Group’s Additive Manufacturing Centre, what results the company is obtaining from the trials of planar printing.
Ertel: The new planar technologies can produce more components without increasing the production time. Thus, they are faster and more flexible than conventional, selective 3D printing. How long it takes to produce a component depends on its size and geometry, so it’s difficult to generalise. But as a rule, planar technologies are five to ten times faster than current options because they work by exposing a larger area to the light source. Depending on the geometry of a part, it can take minutes rather than hours to produce. Demand is steadily rising, and material costs are falling as a result.
AI: Is the technology ready for series production?
Ertel: Across the automotive industry, there’s a growing trend towards shorter production times and lower technology and material costs. Planar technologies are a key factor in the use of additive manufacturing in series production. To begin with, we’re using them in prototype construction, but over the longer term, we are looking at introducing them into series production. We expect the number of parts that can be economically produced by planar printing to rise steadily over time. The new technology won’t be in operation in high-volume series production until at least the next decade.
AI: What about tooling – is it reducing the cost of tooling?
Ertel: 3D printing is a tool-less production method, so parts can be manufactured with no additional production tools. Instead, components are created by building up and hardening them layer by layer. So, making fully functional components directly by planar 3D printing means we no longer need to factor extra tooling costs into the overall cost of production.
Printed polymer injection moulding tools are already used today to produce spare parts. They are cost-efficient, and make parts available more quickly.
Additive manufacturing can also be used to make series tools. The technology-specific design results in better surface cooling with shorter cycle times, which reduces costs and improves the part quality. The BMW Group, for example, operates injection-moulding tools for making plastic parts for vehicles.
AI: When will we see additive manufacturing used in mass-produced models?
Ertel: We first used additive manufacturing in small-series production back in 2010 to make water pump wheels for our motorsport models. These are still working successfully today, in the German Touring Car Masters (DTM). Later, in 2012 and 2016, we used it again in small-series manufacturing at Rolls-Royce Motor Cars. So we’ve already achieved a number of major milestones towards implementing additive manufacturing in large-series production. Moving into the future, we will continue to leverage the potential of this new technology to shorten production times even further. We are constantly exploring other opportunities for using them in large-scale production, where we expect to introduce them at the earliest next decade. Additive manufacturing won’t replace existing technologies completely but will be a useful addition to them.
AI: Will we see a fully printed engine and gearbox?
Ertel: A number of printed prototype engine parts are already in use today, and individual printed components will make their way into series production in the future. But given the costs involved and the specifications that apply to materials and components, printing entire engines is not really a viable option.
AI: What will the impact be on the supply chain?
Ertel: We’re working with our suppliers to establish a supplier market for additive manufacturing. On the one hand, we’re developing our current prototyping suppliers so they can meet the requirements of the automotive industry. On the other, we’re encouraging our Tier 1 suppliers to explore additive manufacturing more closely
More Stories
Professional vs. DIY Tinting: What You Should Know
New updated edition of “PXIMate” reference guide for T&M engineers available from Pickering Interfaces
5 Mistakes That Can Ruin Your Car Accident Claim