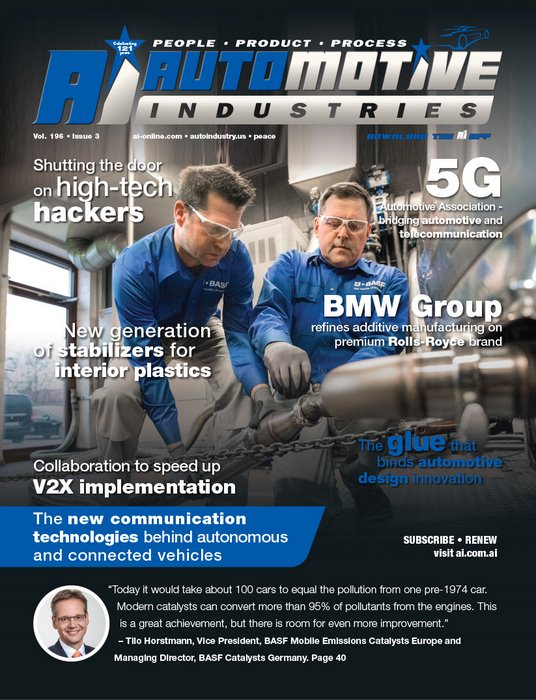
City air has steadily become cleaner year by year since the invention of the automotive catalytic converter in 1976.
Increasingly stringent emission controls are the spark behind ongoing innovation at companies such as BASF, which is at the forefront of developing innovative solutions to increase the effectiveness of this critical technology. The automotive industry is one of BASF’s key customer industries. In 2016, BASF’s automotive driven sales represented approximately 17% of the group’s sales. BASF’s extensive portfolio for the automotive industry includes catalysts, coatings, plastics, automotive fluids and battery materials, which makes it the world’s leading chemical supplier to the automotive industry.
Automotive Industries (AI) asked Tilo Horstmann, Vice President BASF Mobile Emissions Catalysts Europe and Managing Director of BASF Catalysts Germany, what measurable contribution catalysts are making to reducing pollution.
Horstmann: Last year the emissions control catalyst celebrated its 60th birthday. Today it would take about 100 cars to equal the pollution from one pre-1974 car. Modern catalysts can convert more than 95% of pollutants from the engines. This is a great achievement, but there is room for even more improvement.
AI: What is EMPRO™ Emissions Control Catalysts and how does it work?
Horstmann: New engine technologies, tightening emission regulations and fluctuating precious metals prices create emissions control challenges. We help make automotive manufacturers more successful with innovative, cost-effective solutions to meet the toughest emissions control regulations. The combination of multiple benefits into one catalyst substrate is a key part of EMPRO.
AI: Is the EMPRO Catalysts solutions suitable for gasoline and diesel engines?
Horstmann: Yes, we develop and market emissions control catalysts and filters for gasoline- and diesel-powered cars, trucks, buses, motorcycles, construction equipment and other vehicles.
AI: What is new in the EMPRO Four- Way Conversion catalyst?
Horstmann: Our single component EMPRO Four-Way Conversion catalyst (FWC™) combines the functionally of a Three-Way Conversion catalyst with a filter to remove all four pollutants – namely particulate matter, carbon monoxide, hydrocarbons and nitrogen oxides – from gasoline-engine exhaust with just one component. This helps automotive manufacturers meet strict emissions regulations, including Euro 6 with “Real World Driving Emissions” (RDE) limits, while minimizing negative effects on the engine’s performance and fuel consumption. Our customers can benefit from the reduction in system complexity, tooling and overall system cost. We are very proud that the series production of the FWC starts this year at our production site in Nienburg, Germany.
AI: What solutions does your EMPRO SCR System offer for the diesel engine?
Horstmann: In addition to putting together separate components to create exhaust emission reduction systems, we have also developed solutions that combine multiple technologies on one component. As an example, the EMPROTM SCR.2F (SCR on Filter) is a patented technology combining SCR with a diesel particulate filter to control NOx (nitrogen oxides) and PM (particulate matter) emissions from diesel engines on a single substrate. This can save space and weight.
AI: What are the benefits of your next generation Direct Ozone Reduction (DOR) technology?
Horstmann: EMPRO PremAir® NXT is the next generation Direct Ozone Reduction (DOR) technology. When applied to automotive radiators, the solution converts harmful ground-level ozone, which is the main component of smog, into oxygen. This process capitalizes on the large volume of air that passes through a vehicle’s radiator.
AI: In terms of Research & Development what are you working on at present?
Horstmann: Over 1,100 catalyst experts drive innovation in our global Research & Development and Engineering network. They are supported by over 10,000 scientists in the global BASF R&D Verbund with a history of recognized innovation, including the UN Award of the Decade and the National Medal of Technology for the invention of the automotive catalytic converter. Without innovation, the tightening regulations and durability requirements would mean larger, heavier emission control systems. Our experts are working intensely to meet these challenges and develop even more advanced technologies for catalytic exhaust conversion, to optimize the performance of emissions control catalysts for gasoline- and diesel-powered vehicles and to test new raw materials to enable clean air.
AI: Why do you think there is a rather negative perception of diesel technology in the public right now?
Horstmann: It is right that there is currently a rather negative perception of diesel technology in the public. From our point of view global CO2 reduction targets are necessary to tackle challenges like global warming. These are the reasons for CO2 reduction targets for automotive manufacturers. Amongst global targets, Europe has the most stringent CO2 targets with 95g CO2/ km starting 2020.
In our opinion diesel technology is crucial in the engine mix to achieve the CO2 targets because of the advantages of diesel technology due to up to 15% lower CO2 emissions compared to their gasoline counterpart. Of course, CO2 reduction can and must be achieved while reducing other pollutants. The widely-discussed diesel NOx emissions will be addressed through the RDE regulations that will be introduced as of September this year.
Those cover more than 90% of all driving conditions and behaviors in Europe. The new state of the art Euro 6 technology makes diesel the cleanest technology it has ever been. It allows automotive manufacturers to achieve their CO2 targets as well as significantly reduce real world emissions of diesel NOx that comply with all current and future regulations. The introduction of RDE regulation based limits has shown that needed air quality improvements will occur.
AI: How is your production network positioned globally in order to meet the demand?
Horstmann: With our production network for BASF Mobile Emissions Catalysts in the EMEA region we are very well equipped to supply automotive manufacturers with our catalysts solutions. We operate production sites in Nienburg, Germany; Ṥroda Ṥląska, Poland; and Port Elizabeth, South Africa. In total, about 1,500 employees work with us in the region. Our headquarters with R&D, sales, marketing and other strategic functions is based in Hanover, Germany. Products and technologies are tested on engine test beds here and we also operate a Hanover Catalysis Lab. We continue to invest heavily in our sites across the EMEA region but also in our sites around the world.
More Stories
Cybord warns of dangers of the stability illusion
Automotive Industries interviews Bahar Sadeghi, Technical Director, Car Connectivity Consortium (CCC)
Hexagon’s MAESTRO reinvents CMM systems through digitization