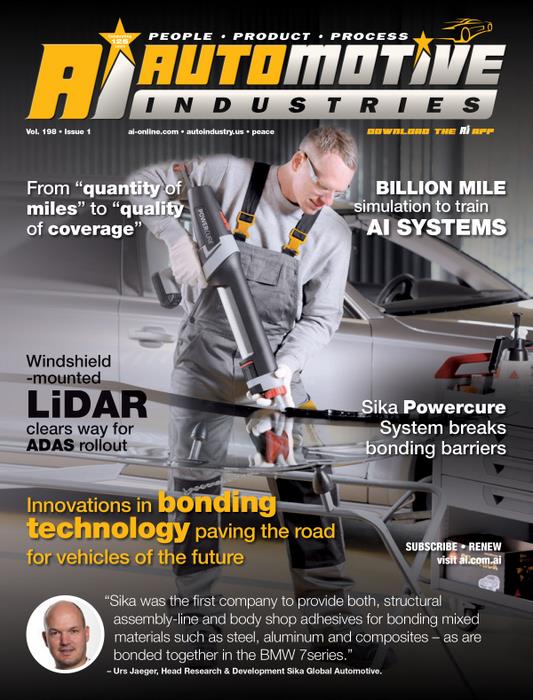
New bonding technology is needed for the next generations of IC, hybrid, electric and autonomous cars. Lightweight bodies, the growing use of mixed materials, E-vehicle modules such as battery and drive systems and increasing proportions of electronics components require new generations of bonding tools.
Automotive Industries (AI) asked Urs Jaeger, Head Research & Development Sika Global Automotive, for insight into what is driving some of the underlying design trends.
Jaeger: The need for fuel efficiency and EV range extension lead to lightweighting concepts which involve the bonding of mixed materials. Lightweighting technologies are now also being carried to and deployed in the mid-range and small car markets. An important topic gaining momentum and affecting the specialty chemicals sector is the trend towards lower emissions and reduced odor, driven on the one hand by stronger regulations, but also by consumer sentiment towards the different perception of odors in different cultures, leading to demand for “smell-free” cars.
There are further trends to mention: ongoing globalization, scarcity of resources, energy and waste reduction, increased individualization of cars and the market preference for SUVs over sedans, which all impact our business to a certain extent.
AI: How is Sika Automotive innovating for the “cars” of the future?
Jaeger: Our research programs address identified needs in order to develop solutions which enable future car concepts. We actively monitor soft trends and mobilize as they gain momentum. We started to investigate structural bonding solutions for mixed material bonding, both for body shop as well as for assembly line applications more than a decade ago – before it was requested by our customers. One of these programs yielded our Sikaflex® Ultra-High Modulus Polyurethane Adhesive technology which enabled structural bonding of the CFRP car body to the aluminum chassis of the BMW i3. A second pillar for our innovations is close cooperation with our development partners; customers, suppliers, peers and industry institutes. Understanding our customers plans and future needs are key to developing value-adding solutions.
AI: How different are the materials required for electric and hybrid car manufacturers from those already in use?
Jaeger: Electric cars offer many new applications for sealing and bonding when you consider the elimination of traditional powertrain components, and in design and assembly as both native or non-native BIW configurations. Unique materials are required not only to bond the battery boxes and other electrical components, but also components within them. In batteries, heat management is of utmost importance. Therefore, thermal conductive sealants and potting adhesives are needed to manage heat transfer. Further, batteries need to be protected against mechanical impact as well as against heat in case of an accident. Here is where our unique reinforcing solutions and intumescent fire rated coatings can make a big difference.
For comfort, the missing sound of the combustion engine allows road and wind noise to become dominant to vehicle occupants. In this NVH area our acoustic expertise contributes to achieve high levels of sound comfort through placement of our reinforcers, airborne noise blocking baffles and structure borne vibration damping solutions at the right spot.
AI: What technological breakthroughs has your company made in developing materials that make vehicles better? Jaeger: Examples run far and wide. Sika was the first company to provide both, structural assembly line and body shop adhesives for bonding mixed materials such as steel, aluminum and composites – as are bonded together in the BMW 7series. Our Sikaflex® UHM assembly line adhesive technology was honored with an Automotive News Pace award, our SikaPower® MBX body shop adhesive technology was a finalist for the Altair enlighten award, and our UltraLite damper was an Altair Enlighten award winner.
Sika has developed many other innovations and industry leading products, such as dampers with the best sound performance to weight ratio and our high strength bonded (HSB) Polyamide reinforcers for maximizing improvement of the crash performance of steel structures. We also play a leading role in Monomer or VOC reduced adhesive systems and were the first to introduce a VOC free direct glazing system, through deployment of water based pretreatments. We lead the industry in repair solutions with our Sika PowerCure system, enabling windshield replacement in less than 30 minutes and our unique 2C-Epoxy adhesive for car body repair, which combines the highest modulus (stiffness) and impact peel (crash resistance). We are soon introducing a new generation of proprietary 2C-PUR adhesives branded Cure-on-demand technology where we are able to manage open time and curing speed separately, and of course the entire innovation pipeline remains full.
AI: Tell us a little about the role Sika’s adhesive products have had in car manufacture/assembly.
Jaeger: Sika solutions are developed to meet real industry needs, and not just to offer me-too products. Sika was the first company to introduce black primer-free direct glazing adhesives, followed later on by Sika HydroPrep® water-based systems. We enabled the successful combination of antenna suitability combined with direct fixation of windscreens, structural bonding of mixed substrates and classification-free hotmelt lamination adhesives, just to name some.
Introducing innovations requires a close co-operation with the customers, since innovation means change and not just replacement. The customer must be involved in the whole development process in order to understand the benefits and risks of the new systems very well in order to change. We call this Courage for Innovation because it requires commitment, we call our results Value Added Solutions.
AI: Similarly, how have your acoustic applications been impacted by the changing demands of the automotive sector?
Jaeger: There are several dozen baffle and damper parts in the modern car which contribute to noise reduction. Sikacontinues to bring innovations to the market such as lighter weight baffles with highest sealing performance and new ultra-lightweight constrained layer dampers, which enables weight savings up to several kilograms per car compared to standard systems. Our acoustics innovation is not only in our materials but also in core competencies of acoustic engineering and parts design. Sika experts in our modern acoustic technical centers can help our customers through extensive full body testing to exact placement of the parts to achieve maximum noise reduction while our engineers create best possible optimized parts designs, many of which are now and remain patent protected.
AI: What technologies are in the early stages at Sika’s R&D division?
Jaeger: Usually we do not talk about our chickens before they are hatched, but I can assure you that we are continuously creating future technologies. We spend over 25% of our development time on future technologies, many of them years away. Based on the identified megatrends we are working on further solutions for e-vehicles, and a range of products curing at lower e-coat oven temperatures or over shorter oven duration times. We also are pushing hard to develop a new platform of polyurethane adhesives with a new set of properties, having a big impact on assembly bonding applications. AI: How are your R&D programs affected by regional requirements?
Jaeger: Requirements differ between customers and sometimes even at the same customer between the regions.
There are both different regional government regulations, and customer expectations. What is also important to consider is global availability of raw materials as we formulate the future. Customer requirements also differ in EHS related issues (which and how much VOC, emissions, odor, etc. are allowed). Assembly process related differences also can present a challenge. Fully automated and climate-controlled environments have different needs compared to a manually applied processes in a hot and humid region without climatic control.
A key Sika differentiator is proximity to customers. We have strong development teams established in every region who collaborate regularly within our networks. So, even if a big part of our business is global, regional or local adaptations and interfaces are readily enabled. We maintain close and good collaboration between these development teams, which is crucial to roll out our technical innovations fast and successfully.
More Stories
Sonatus – The industry is shifting gears to software
Cybord warns of dangers of the stability illusion
HERE building trust in ADAS systems