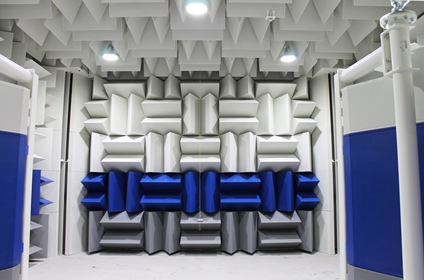
Saint-Gobain has installed an anechoic chamber at its facility in Bristol in the UK.
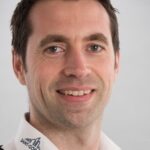
Better understanding of the role of bearings in the reduction of noise and weight is leading to a number of technical innovations suitable for both electric and internal combustion powertrains.
An example is the NORGLIDE® range developed and manufactured by Saint-Gobain in its Willich, Germany factory. Instead of balls or rollers they comprise two concentric rings of material – an inner ring of polytetrafluoroethylene (PTFE) polymer and an outer metal ring made from steel, stainless steel or aluminum. There can be an intermediate mesh of aluminum, bronze or other metal.
Automotive Industries (AI) asked Tom Francis, Segment Lead for Chassis and Powertrain at Saint-Gobain Bearings, what challenges technology shifts are bringing to powertrain design.
Francis: There are huge challenges coming and they all stem from the uncertainty of what’s happening in the marketplace. Governments down to city level keep changing their minds about what technology they want to support. Companies are therefore reluctant to fully commit to a particular technology. That uncertainty is rippling down to Tier 2. We often find that projects we are working on are suddenly stopped.
This means that as an industry we have to be more agile. The automotive industry is still very conservative and quite slow moving. A big mindset shift is needed so that we can adapt quickly to the changing needs. Instead of the platform-type approach, I think we should adopt use case type thinking. Here you have a particular use case for an identified size and type of driving, and you develop the appropriate technology for it.
AI: Which Saint-Gobain products help to reduce CO2 emissions?
Francis: Our RENCOL® tolerance rings allow designers and engineers to use lighter components. For example, there are challenges when you combine different materials such as steel with aluminum or plastic. You have to allow for the different thermal properties of each material. And that causes engineers big headaches, particularly when using adhesives. Differences in thermal expansion can cause gaps to appear, and noise and vibration issues. A tolerance ring acts like a spring which maintains the integrity of the multi-material component through the total thermal cycle.
AI: How does the NORGLIDE® bearing technology help reduce weight?
Francis: When you compare something like a roller bearing to a NORGLIDE® bearing, there is a significant reduction in weight. For example, by replacing the big roller bearings on the top of suspension struts in the chassis you can immediately save between 350 – 700 grams per vehicle.
AI: Do RENCOL® Tolerance Rings contribute to saving space and reducing cost?
Francis: RENCOL® is very clever technology in two main ways. Firstly, it allows you to combine materials with different thermal properties. Mechanical tolerances can also be higher and the finishes on the mating components to not have to be as precise due to the flexibility of the ring material.
The second is our precision torque offering, which is like a slipclutch to protect components from shock forces. Our tolerance ring can replace a mechanical slip clutch through an elegant, inline solution. You take your normal shaft and housing and connect them using tolerance ring to provide the slip clutch functionality.
This saves on space, weight and costs.
AI: How do you ensure the best possible fit between mating components?
Francis: Our approach is to work with our customers. Traditionally, tolerance rings tend to be off-the-shelf items. Very, very often that does not give you the optimum solution. We design bespoke tolerance rings using our FEA capability, design tools and a couple of hundred years’ worth of collective experience!
AI: How can you help reduce noise and vibration?
Francis: We have three products. With our RENCOL® products we can tune the performance of the system by designing the stiffness of tolerance ring to adjust the point at which natural frequency occurs. A great example of this is computer hard disk drives, where the tolerance ring is used to join the bearing cartridge with the reading heads, and part of its function is to make sure the natural frequency point is outside the working range.
With our NORGLIDE® range we are talking damping through a thick layer of PTFE. A pure plastic bearing is up to 10 dB louder than a NORGLIDE® bearing because our soft PTFE layer absorbs and dampens the sound, and also changes the quality of it. For humans, annoyance level created by a sound is due to a combination of factors including loudness, frequency and pitch. NORGLIDE® bearings often produce sounds that are more
pleasant to the ear than those produced by plastic or metal bearings, and can add to a quality feel of the product.
And then we have our SRINGLIDE™ products which are a combination of the two. Spring steel is used together with our NORGLIDE® technology. With SRINGLIDE™ you can adjust the frequency and provide some damping in the system.
AI: What about consistent function and perform over time?
Francis: NORGLIDE® products use a very thick PTFE layer which provides you with a consistent surface over the lifetime of the component. That is an inherent part of how we form our products. As it wears the functional layer remains constant, which means there is also no change in the friction performance over time.
With the RENCOL® products there are probably two things. One is the clutch overload mechanism, which protects components from damaging input forces or torques like an overload protection device. The other side of it is maintaining a good fit over thermal and wear cycles to prevent any rattling that might result from wear.
AI: Can the RENCOL® tolerance ring for e-motors save assembly time and cost?
Francis: What we see here is a value proposition which has more to do with the manufacturing cost savings. There are two main competing solutions in the e-motor assembly. There is heat shrink pressing, which is where you heat the components up press them together.
Then you have adhesives, which process engineers dislike intensely. It’s messy, it requires lots of maintenance for the equipment especially in e-motors because they tend to use very specialist and highly abrasive glues.
During assembly you have to control the atmosphere and the temperature of the adhesive, and then you have to cure it. There is a lot of energy in that process. Heat shrink pressing is easier, but there is still lots of energy required. You have to heat it up very quickly, which is very energyintensive and then you have to cool it either through energyhungry air conditioning or you need lots of space to allow the motor to cool down naturally.
With the RENCOL® solution the assembly is done in 3-4 seconds at ambient temperature and it can be moved to the next station immediately. That’s really where you can save the time on the assembly and the cost of the product.
AI: Can you get the required friction and damping performance in BISG (Belt Integrated Starter Generators) using NORGLIDE®?
Francis: BISG-type alternators are very different to the normal belt tensioners. The product is a lot bigger and provide
s decoupling as well as optimizing the belt angle over the rollers for the drive and recovery phases. Our design philosophy is to follow a collaborative approach with the customer in order to understand their needs, select the right material, the right shape and then provide the overall requirements of friction, damping and wear.
Different compounds provide a balance between friction, wear and damping properties. We also take into consideration things like corrosion or if they are being assembled in an aluminum housing.
AI: What’s next for Saint-Gobain Bearings?
Francis: We will be focusing on the rollout of the hybrid NORGLIDE® and RENCOL® product, SPRINGLIDE™. It is a fantastic product that gets you the best of both worlds. In terms of powertrain, for us the emphasis is about making sure that we are developing solutions for electrification, and making sure that our R&D is focused on developing solutions for eMobility.
More Stories
DuPont materials science advances next generation of EV batteries at The Battery Show
How a Truck Driver Can Avoid Mistakes That Lead to Truck Accidents
Car Crash Types Explained: From Rear-End to Head-On Collisions