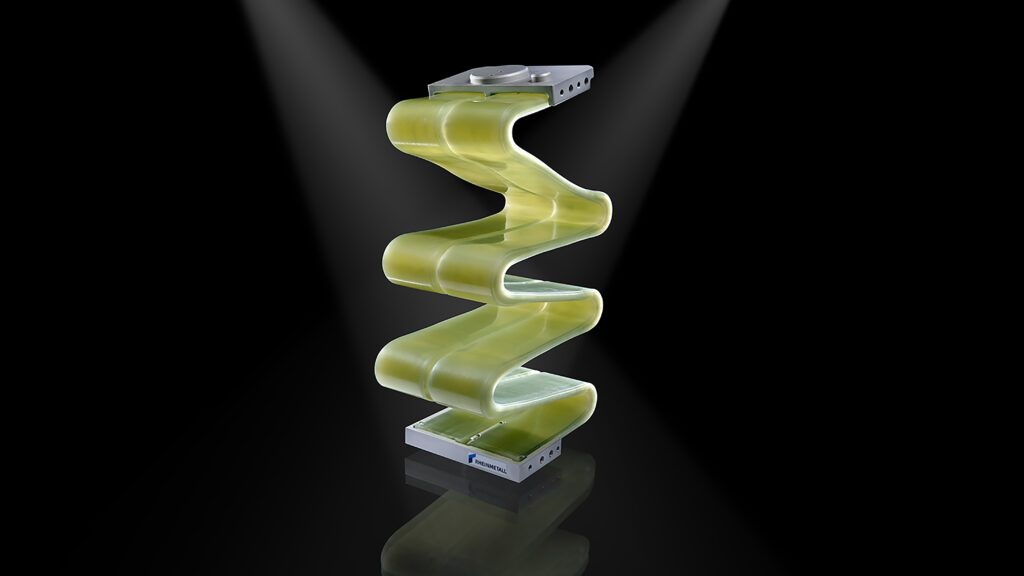
Rheinmetall has developed a globally unique new glass fiber suspension spring. In cooperation with a premium OEM, the Düsseldorf-based technology group has now presented this product to the public in a prototype testbed vehicle. Featuring a patented design, the new spring won over the automaker thanks primarily to its significant weight advantage in the unsprung mass as well as its compelling performance.
In winning this order, Rheinmetall continues to expand its position as a leading parts supplier to the automotive industry – including solutions for applications beyond conventional combustion engines. A proven partner of the automotive sector, Rheinmetall has been applying its special expertise in innovative materials for many years to make valuable contributions in weight optimization, helping in turn to reduce fuel consumption and promote e-mobility.
The current project follows an initial order placed by the automaker in early 2021. Following the development phase at Rheinmetall’s Neckarsulm plant in southwest Germany, the glass fiber springs were recently installed in the test vehicle at the cooperation partner’s location under conditions of strict secrecy. There, the springs had to pass an intensive testing programme involving actual trials prior to being successfully accepted.
Further development work with other leading automobile manufacturers is already underway.
In developing this innovative spring system, Rheinmetall has not only scored a technological breakthrough, but has also entered a market with strong future growth potential. The INVENT unit of Rheinmetall’s Materials and Trade division engages in research and development of various chassis-related components – with series production the goal.
Because they connect the wheels to the chassis, suspension springs play a vital role in influencing a vehicle’s safety and how it handles. The new glass fiber-reinforced plastic springs result in a weight advantage in the unsprung mass of up to 75% compared with conventional steel coil springs, making them particularly suitable for range-optimized electric vehicles.
In addition to lower weight, the development team attached central importance to maximum pitch and roll stability, high inherent damping of the material, and assuring optimum noise, vibration and harshness characteristics. Another advantage of the glass fiber-reinforced springs compared with conventional steel springs is their resistance to corrosion, as plastic can only be corroded by certain chemicals, not by oxygen and water. The springs fit into the same installation space as standard springs and feature outstanding fatigue strength, including very good emergency operating characteristics that enable the vehicle to continue driving.
The newly developed suspension springs are based on long decades of technical know-how amassed by Rheinmetall in the fields of mobility and security, coupled with tremendous innovative drive oriented to future trends and developments.
The company has longstanding expertise in lightweight automotive engineering; its Castings business unit make it a leading producer of lightweight aluminium components. The product portfolio encompasses structural and chassis parts as well as special e-mobility components such as e-motor housings and battery trays. Moreover, since 2019, Rheinmetall has held a 25% stake Carbon Truck & Trailer GmbH of Stade, Germany, a company that produces carbon fibre-reinforced plastics. The focus here is on low-cost serial production of lightweight commercial vehicles.
More information on this product can be found at: rheinmetall.com/fibersuspensio
More Stories
Professional vs. DIY Tinting: What You Should Know
New updated edition of “PXIMate” reference guide for T&M engineers available from Pickering Interfaces
5 Mistakes That Can Ruin Your Car Accident Claim