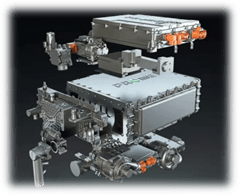

Original equipment manufacturers and Tiers need a new generation of advanced materials as they switch from total reliance on internal combustion engines to electric vehicles.
Research shows it is important that the technology development is informed by consumer preferences.
Automotive Industries (AI) asked Tamim Sidiki, Global Marketing Director Mobility, DSM, to share what trends the company’s research has identified.
Sidiki: There have been multiple in-depth discussions about electric vehicles (EVs) with a number of OEMs, Tiers and consumers. We have identified three key drivers – safety, lightweighting and sustainability.
Specifically, we are looking at EVs from the perspective of the consumer. From a safety perspective an EV must be treated as an unattended appliance product, like a washing machine. Where a washing machine runs on around 220 volts, EVs are charged at 400 volts, with some now at 800 volts. It would be a catastrophe for everyone, including the owner of the vehicle, the OEM and the image of EVs if they spontaneously catch fire while parked in the garage.
Lightweighting is already reducing fuel consumption. It will be more important for EVs which are around ~400 to 500 kilograms heavier than the comparable ICE car, due to the weight of the battery pack. No consumer wants to drive a car which feels like a tank, and everyone wants a long driving range.
Sustainability is driven by legislation, the positioning OEMs and increased consumer pressure.
AI: Would you like to elaborate on lightweighting?
Sidiki: Plastic components are typically about 50% lighter than metal equivalents. They also offer greater design flexibility and a cost saving of some 20%. Our portfolio of bio and recycled plastics for injection molding and composite structures can reduce the carbon footprint vs. metal components and alternative mineral oil-based plastics by up to 80%.
Having replaced many “easy” aluminum parts, the next challenge is to replace magnesium and structural steel components. We are working on plastic and metal/plastic hybrid designs in applications such as the car crossbeams, front end module, engine mounts and air springs. Gas and clutch plastic pedals are already standard. For EVs, we now see the replacement of steel brake pedals with full plastic or metal/plastic hybrid designs. Regenerative braking results in
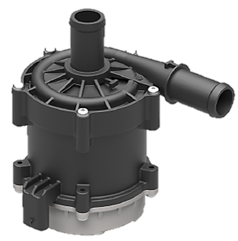
1-pedal driving, reducing the long-term load forces on the pedal.
AI: Please tells us more about your EV applications.
Sidiki: It is all applications linked to the high voltage system, starting from the charging station through the cable and charging plugs to the vehicle socket, and from there to the battery, inverter/converter and ultimately the motor. We have a complete portfolio of flame retardant materials with highest comparative tracking indexes to support this system, all of which have technical approval and are available in the market.
AI: What about fuel cell and hybrid vehicles?
Sidiki: One of our key focus areas is hydrogen and gasoline tanks, for which we developed Akulon® Fuel Lock which offers the industry’s lowest gasoline and hydrogen permeation rates. We support every component in a fuel cell system from the manifold to the auxiliary
components attached to the fuel cell. For the batteries and e-motors we assist with dedicated Xytron PPS thermal management compounds to ensure peak performance and longevity in the e-water pump or cooling valves. Xytron PPS compounds have the lowest ionic leaching amongst various engineering plastics and are at the same time optimized for mechanical strength, especially along the weld line. Various OEMs already have xEVs on the road with Akulon Fuel Lock or Xytron components.
AI: What is special about Akulon® Fuel Lock?
Sidiki: It replaces materials like HDPE for both hydrogen and gasoline tanks. It offers the ability to design tanks with thinner walls. Tanks with 2 mm wall thickness molded from Akulon Fuel Lock perform at an evaporative emission rate of 80% below the U.S. EPA and CARB regulation limits.
AI: What are the trends in high voltage charging?
Sidiki: The first main driver behind high voltage charging is reducing the time taken to recharge. 800 volts can reduce charging time for an 80% battery load from currently 40 to 60 minutes down to only 15 to 30 minutes. Multiple studies have found that consumers find a recharge time of around 15 minutes acceptable.
The second main driver is that higher voltages also simplify the design of electrical components. You can increase power supply through higher current or higher voltages. For higher currents you need thicker c
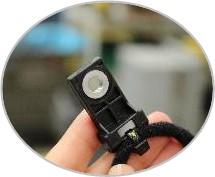
opper cables. If you keep the current low but increase voltage you can use the same or thinner cables, saving on weight and costs. We are the first in the market with PA66 and also PPA materials with a CTI of 750V and 850V to safeguard such high voltage charging.
AI: What does DSM offer designers of semi and fully autonomous cars?
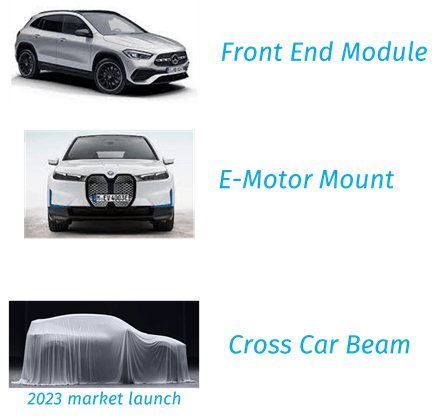
Sidiki: They are all controlled by various electronic control units (ECUs) or by one fusion high-performance computer fed with information from numerous ADAS sensors. We work to replace the metal housings of such components. There are mechanical requirements such as protecting it from dust and moisture, but also functional requirements such as conducting heat away from the sealed box. There also needs to be radiation shielding of the chips in the processor. Dedicated thermally and/or electrically conductive compounds allow effective passive cooling as well as EMI shielding well in the range of 50-60dB protecting application from emitting EMI as well as getting disturbed by EMI.
We also provide a full material portfolio for connectors required to link the processor to the sensors and the rest of the vehicle such as FAKRA, HSD or header connectors.
We have developed a ForTii Ace (PPA) JTX8 compound, the only MSL JEDEC1 polyamide to avoid any blister formation during reflow PCB assembly. It enjoys infinite shelf lifetime for the resin as well as molded connectors and other components. Color consistency and stability is excellent.
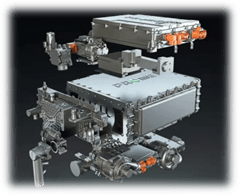
AI: Please tell us more about your fuel cell applications.
Sidiki: Xytron™ G4080HRE, a glass reinforced polyphenylene sulfide (PPS), has the highest weld strength of all PBSs and is also impact modified. DSM’s tailor-made PPS is the purest material solution on the market today and offers the lowest ion leaching up to 120°C. Ion leaching is important for commercial applications such as trucks and buses as it affects performance over time.
AI: What makes automotive companies want to do business with DSM?
Sidiki: All companies in the supply chain have focused on replacing metals with plastics for a number of years, so all the easy applications have been done. For me, what makes DSM pretty special is that we are a very flexible, innovative, agile and fast company. Many clients tell us they see us being fully integrated in their design cycle. We start with a cost analysis using a set of tools we have developed to compare a plastic component against the metal equivalent. The project only continues the total cost is lower using plastic.
We then provide support all the way from part design, CAE simulations through to prototype development, with a focus on reducing costs, weight and carbon footprint. Our goal as a development partner is to make the process as smooth as possible and to reduce delays and costs by getting it right first time.
AI: What is next for DSM?
Sidiki: The Mobility segment will continue to be one of our key focus areas. The market is dynamic, with many exciting new technologies and applications on the horizon. We are extremely well positioned from a material perspective, and from the way we tackle joint application development with customers.
More Stories
Towing Services Explained: 6 Key Facts You Need to Know
Environmental Factors That Influence Ceramic Coating Choices
Best Wheel Size for Off-Road Adventures: What People Get Wrong