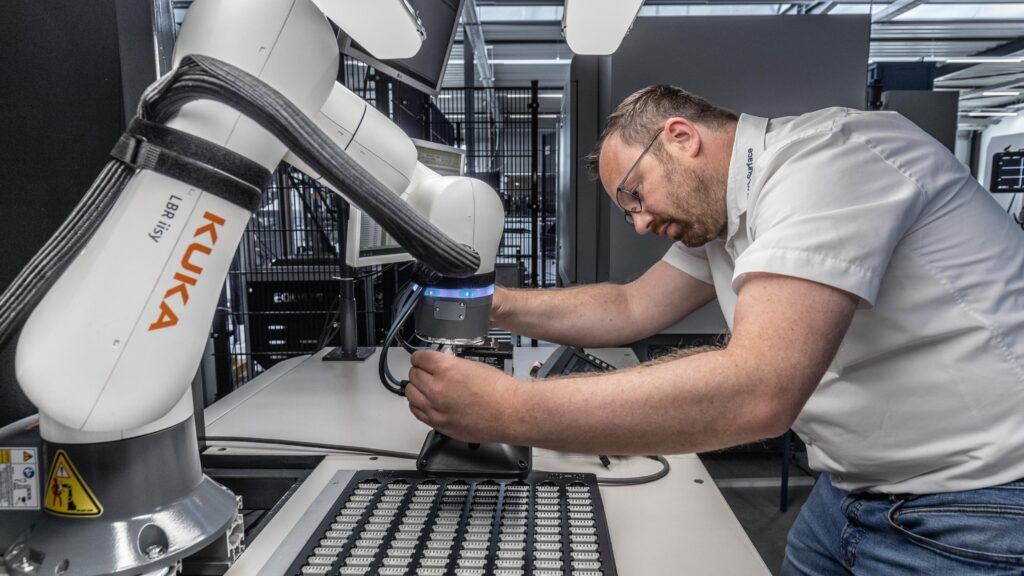
Debuting what it terms Sensitive Cobotics, KUKA Robotics will show IMTS attendees the future of automation in the form of its new LBR iisy cobot. As ready-to-use automation, the LBR iisy quickly and easily integrates into any manufacturing application from pre-defined production processes to open, unstructured work environments with unpredictable conditions from one job to the next. For show attendees in the automotive, e-mobility, aerospace, electronics and related industries, the company will also demonstrate advanced automated friction stir welding (FSW), a process that fulfills the growing need for fast, clean, reliable and cost-effective joining for non-ferrous metals and mixed metal combinations frequently encountered in fabricating such components as electric vehicle (EV) battery housings and trays.
With six axes, a 3-kg payload, 600-mm maximum reach and 18.8-kg overall weight, the LBR iisy is well suited for overcoming the challenges posed by confined workspaces. Whether loading/unloading machines, assembling components or packaging, the cobot provides increased versatility and can be immediately operated by anyone from an automation expert to a cobotics newcomer. Featuring various operator levels, the user-friendly system adapts to the corresponding level of user knowledge.
The LBR iisy is fully embedded into the KUKA Industry 4.0 ecosystem. In addition to the availability of downloadable software apps, the company’s KUKA Connect cloud solution allows users to access and analyze the cobot’s data at any time.
Despite its low procurement costs, the LBR iisy is equipped with high-grade joint torque sensors integrated in all its axes. These sensors respond to the slightest of external forces and provide certified collision protection.
As part of a live demonstration, IMTS attendees will also see KUKA’s robotic FSW process welding aluminum parts to manufacture an assembly. The cell will consist of multiple robots. One robot will pick parts from bins and place them into a fixture and a second robot will perform FSW using both Roboception and SICK PLB 3D vision technologies.
For EV battery tray production, KUKA has engineered its cost-effective KUKA cell4_FSW modules to provide up to 95% more process efficiency and maximize the available configuration options for manufacturers. Used for both 2D and 3D welding tasks, the modules are scalable and accommodate either one or two 6-axis robots. Shops can arrange several workpiece clamping tools in the working area of the cell so that robots can work simultaneously on larger components if needed.
KUKA
KUKA is a global automation corporation with sales of around 3.3 billion euro and roughly 14,000 employees. The company is headquartered in Augsburg, Germany. As one of the world’s leading suppliers of intelligent automation solutions, KUKA offers customers everything they need from a single source: from robots and cells to fully automated systems and their networking in markets such as automotive, electronics, metal & plastic, consumer goods, e-commerce/retail and healthcare. 12/ 31/2021
More Stories
DuPont materials science advances next generation of EV batteries at The Battery Show
How a Truck Driver Can Avoid Mistakes That Lead to Truck Accidents
Car Crash Types Explained: From Rear-End to Head-On Collisions