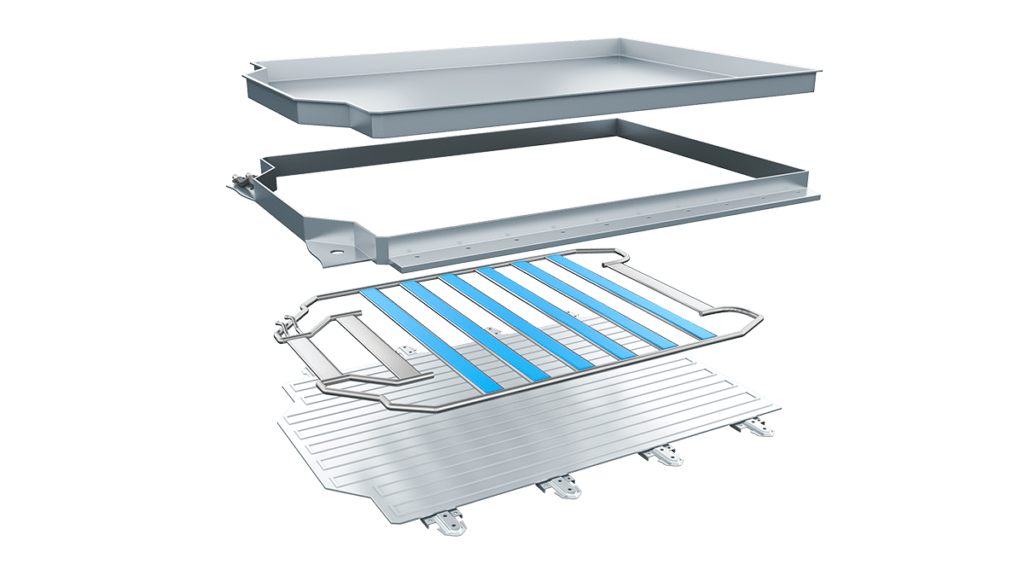
The formulations of DuPont thermally conductive adhesive solutions can be modified to meet the requirements of the customer.
New or improved adhesive technology allows OEMs to improve crash durability, thermal management performance and safety while reducing weight.
Companies like DuPont also optimize the use of their products during the manufacturing process, with a focus on sustainability. New adhesive formulations allow for the reduction or elimination of solvents and hazardous plasticizers through primer-free and phthalate-free technologies.
Automotive Industries (AI) discussed some of the latest developments with Christophe van Herreweghe, Global Strategy & Marketing Director and Dr. Andreas Lutz, Global Technology Director, both at DuPont.
AI: What are the main designs and trends in EV battery pack design?
Van Herreweghe: Cell-to-pack has become a key design trend as the industry moves to reduce the number of components in the battery pack. But, when you remove components, you potentially compromise the structural integrity of your battery pack.
So, one of the key challenges the industry faces is how to ensure that we still have 15 years plus durability of the battery pack / vehicle after removing some of the components.
Our adhesive solutions address the challenge by allowing multiple substrates to be bonded together, retaining the structural integrity of the battery pack while reducing weight. In addition to providing the material, we deliver the
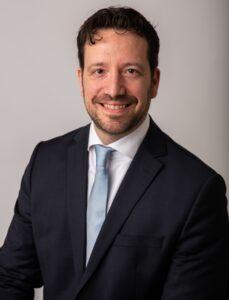
necessary application development knowledge. For example, our engineering teams work closely with our customers to find solutions to their challenges.
AI: How are you helping to make battery modules more durable and able to go longer between charges?
Lutz: The answer lies in the chemical structure of our adhesive formulations. The new designs require more structural adhesive solutions combined with thermal conductivity. This means the performance of the battery relies on the qualities of the adhesives. That is why our focus is not only on formulating adhesives, but also on developing polymers, curing catalysts and filler packages which enable higher load strength and durability combined with efficient filament conductivity.
Van Herreweghe: If you completely remove one level of packaging, you have a lot more energy density in your battery pack. We help the industry to improve the range and time between charges by providing the technology needed for new battery designs.
AI: What about the space between the battery cells and the cooling plate?
Lutz: Our thermally conductive adhesive solutions are specially formulated to bond with the battery cells and cooling plate. They offer thermal conductivity levels which allow an efficient heat transfer into the cooling blades. The formulations can be modified to meet the thermal conductivity and durability levels defined by the customer.
AI: How does BETATECH™ Thermal Interface Material help to control battery heat?
Van Herreweghe: BETATECH™ is able to transfer heat from the cells into the cooling plates, and also to transfer heat from the cooler to the cells in winter.
The conductivity level is adjusted according to the design of our customer. We work together to determine the optimal level of thermal conductivity. It is important for it to be spread homogene
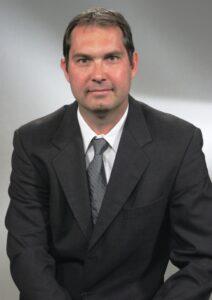
ously because you do not want to have hotspots within your battery pack.
Lutz: The material can easily be applied to any required layer thickness. Adjusting the layer thickness together with the thermal conductivity properties of the material offers the most efficient heat transfer.
AI: Have you developed special formulations for EVs?
Lutz: Our solutions are available in a variety of formats — from bulk and non-silicone adhesives to dispensable gap fillers. DuPont products are differentiated from the competition with higher thermal conductivity, higher electric resistance, improved handleability and improved thermal stability during continuous operation. DuPont’s portfolio not only focuses on adhesives, but we also supply specialty lubricants for battery applications, as well as thermoplastic solutions.
Van Herreweghe: We are very well known for our structural adhesives. Every third car produced globally is bonded using our BETAMATE™ solutions. So, we have leveraged our historical expertise in structural adhesives into our battery pack designs in order to deflect the energy in case of a crash.
AI: How can manufacturers of luxury EVs achieve a balance between stiffness and elongation to achieve the structural strength?
Lutz: Our solutions are based on different chemistries using our epoxy or structural polyurethane adhesive technology or our acrylic technology. In addition to our adhesives we have polyurethane solutions, which can be tailored to meet the requirements of the customer.
Van Herreweghe: For elongation between multiple substrates or carbon, steel or aluminum, you need to make sure that you are marginally stiff enough in order to provide a comfortab
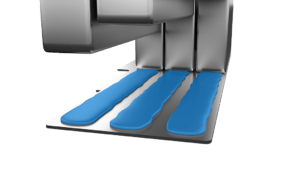
le drive, safety, and durability. You also need to allow for certain variations between the substrates. So, we have a complete portfolio with high modulus to low modulus and higher elongation to lower elongation. Customers can tailor make specific substrate combinations to meet their needs.
AI: What about the balance between weight reduction, acoustic performance, and lean manufacturing processes?
Van Herreweghe: We need to start by asking ourselves why reducing battery weight is so important. What we find is that weight reduction is very important for the performance of the vehicle, but also for its durability and cost of ownership, such as the need to replace tires more frequently.
From a manufacturing point of view, batteries are very heavy. Surfaces and equipment in the manufacturing plant have to be reinforced to cater to them. To reduce weight, we also have to make our adhesives lighter, including thermal interface materials, such as potting materials and foams. Lightweighting is still important to the industry.
Lutz: Our adhesives enable lightweighting because we offer superior adhesion for any kind of substrate, which is why it is an enabler for lightweight substrates.
AI: What about lean manufacturing?
Lutz: We developed a catalytic system which is included in our two-component offering. It allows us to tailor open time and temperature accelerated curing in the manufacturing process. You can include accelerants to speed up the curing process. In addition, we tailor the viscosity of the material to make it easy to dispense.
AI: What steps have you taken on your journey to carbon neutrality?
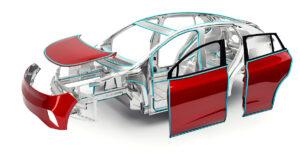
Lutz: It starts with the raw materials, by engaging with suppliers to select the raw materials with the lowest carbon footprint, and those which are bio-based. We use a cradle-to-gate Life Cycle Assessment (LCA) tool to analyze our suppliers.
Van Herreweghe: Sustainability informs our choice of suppliers and materials in order to reach DuPont’s target of being carbon neutral by 2050. In the automotive sector we are going to do it sooner, because our customers require that we be carbon neutral as quickly as possible. We are working together with leading industry companies in order to meet their targets.
AI: What is next for DuPont?
Van Herreweghe: We collaborate very closely with our customers, in order to understand their needs. There is a lot of technology which will be coming to market in two to three years from now, which is being developed in partnership with our automotive customers. As a company we are working on developing the advanced technologies that we believe our customers will need in the future. You will find more DuPont content in the vehicles of the future.
More Stories
DuPont materials science advances next generation of EV batteries at The Battery Show
How a Truck Driver Can Avoid Mistakes That Lead to Truck Accidents
Car Crash Types Explained: From Rear-End to Head-On Collisions