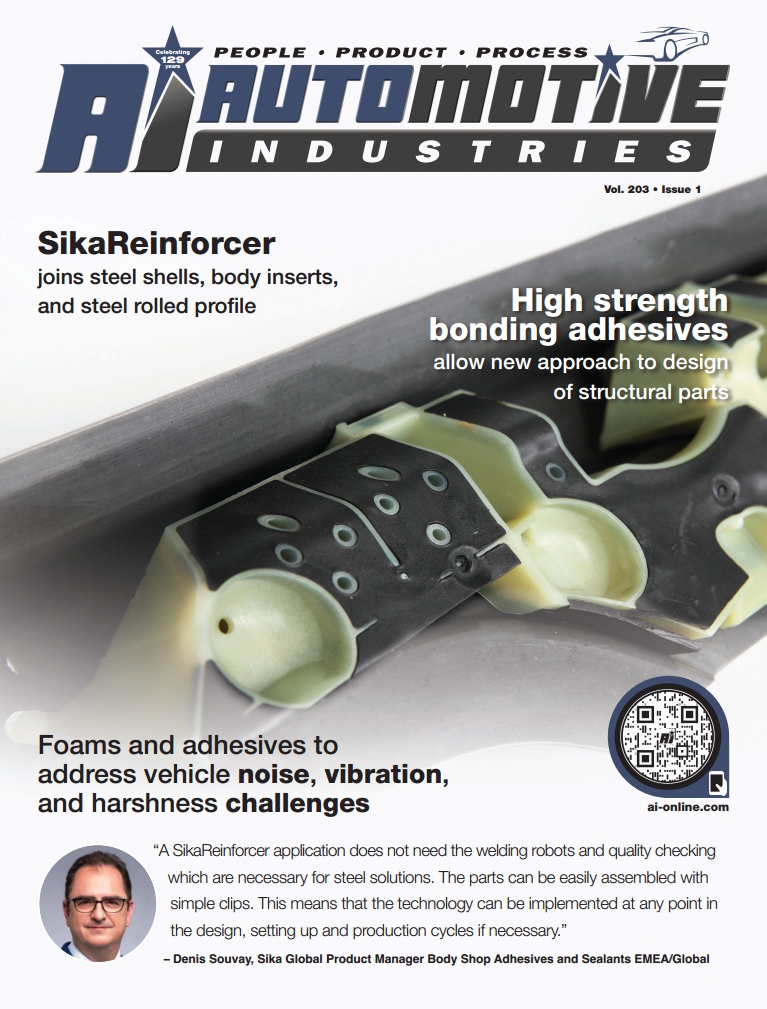
Sika structural foam enhances the crash performance of automotive steel structures
Thanks to its smart design, the incorporation of structural foam and 3D fiber-reinforced polymeric body inserts in SikaReinforcer technology enables it to not only match the crash performance of aluminum and steel inserts but also to deliver significant reductions in weight and assembly complexity.
The parts fit vehicle cavity geometry like a glove thanks to their highly engineered design utilizing vehicle CAD data.
The expandable structural foam component of SikaReinforcer joins steel shells, body components, and steel rolled profile.
It is also suitable for other sill constituents, such as aluminum sheets, fiber reinforced composite shells or organic sheets and other internal reinforcement profile constituents including aluminum extrusion profiles or polymeric extruded and pultruded profiles.
Simple SikaReinforcer profiles (tapes) can fill small gaps and add structural integrity in tight joints during the design process, or post design, as add-in solutions.
Automotive Industries (AI) asked Denis Souvay, Sika Global Product Manager Reinforcers about the advantages of structural foam over metal reinforcing.

Souvay: The use of heat expanding structural epoxy foam, or alternatively, high strength bonding (HSB) using SmartFlow liquid epoxy adhesives enables design flexibility and allows designers to approach load transfer and impact absorption in structural parts differently during a crash event.
The advantages of three-dimensional plastic part technology include the expansion and curing of components in the body-in-white assembly process, and additionally, the bonding of materials which cannot be joined using conventional welding techniques.
AI: What are some key trends driving the increased use of insert/reinforcement solutions?
Souvay: There are significant savings in capital outlay and production line complexity. A SikaReinforcer application eliminated the need for welding robots and quality checking which are necessary for steel solutions.
The parts can be easily assembled with simple clips or small welding tabs.
This means that the technology can be implemented at any point in the pre-development, design, production equipment setting and production phases, if necessary.
Weight savings, an important factor, also is driving the reduction of metals and thinner metals, combinations of metals, and even the addition of composites. Sika Reinforcer enables all three while also maintaining structural integrity of the vehicle.
Considering also new requirements in terms of technical solutions LCA assessment, the SikaReinforcer technology provides more than 50% lower emissions than an aluminum profile solution, which provides our customers with an advantageous solution in this regard.
AI: Please explain the technology in a bit more detail.

Souvay: SikaReinforcer technologies combine a three-dimensional customized fiber-reinforced thermoplastic carrier with a high performance engineered epoxy heat-activated structural foam material. During assembly, the structural inserts are placed inside the cavities of the body-in-white of the car. When the car body moves through the E-coat oven, the heat activates the SikaReinforcer structural foam or SikaPower adhesive material, which then expands and cures.
Due to superior adhesion to the surrounding metal structure and the insert, the result is a hybrid composite structure with excellent performance.
This technology enables designers to tailor reinforcement solutions that improve the performance in stiffness or crash protection in specific areas of a car body structure, or in contributing to the overall structural integrity of a vehicle.
In addition, SikaReinforcer parts are used to help address vehicle noise, vibration, and harshness (NVH) challenges.
Additionally, they contribute towards improved vehicle dynamics by increasing the stiffness of the BIW.
AI: What are the benefits?
Souvay: SikaReinforcer structural inserts enable lightweight body structures without compromising the overall performance of the application. In general, the SikaReinforcer applications enable our customers to enhance the performance of a 100% metal design by reducing the complexity of an application and at the same time saving weight and material at equivalent performance versus a 100% metal design.
Additionally, cost savings can be achieved compared to a metal solution due to a reduced need for stamping dies for metallic parts and reduced metal usage.
AI: How is the performance of a structural insert or reinforcement solution being validated?
Souvay: The Sika product development team uses its expertise with advanced computer aided engineering (CAE) simulation tools to design a two-component engineered part. The simulation will always be confirmed on the complete CAE model of the OEM. When necessary, part designs can be modified and optimized based on analysis prior to prototyping, introducing cost savings.
CAE simulation is used to anticipate problems before physical tests of stiffness or crash protection are performed on the complete car or a sub-model assembly. The CAE simulation methodology continuously shows excellent levels of correlation between CAE simulation and real tests.
AI: Is the technology being used in production?
Souvay: The technology is well accepted in the market. It is being used by a number of OEMs.
While in use, the technology has proven to perform to specification and to age well, based on teardowns and follow up studies of production vehicles. Customer feedback is further used to guide future design, using technology to enhance the driving experience.
AI: Are there different requirements for electric vehicles (EVs)?
Souvay: Sika supplies heat-conductive adhesives and materials for encapsulating and insulating electrical systems. These help ensure that the

vehicles of the future will be safer, longer-lived, and more efficient. These products are dedicated to the battery systems.
In EVs, the battery must be protected from intrusion on all sides during a crash, and this must be done either in the structure of the car body, or in the structure of the battery enclosure.
The SikaReinforcer technology is one of the potential alternatives to the commonly used aluminum extruded profiles or steel cold rolled housings. SikaReinforcer inserts can be added as protectants to common crash zones.
As an example, Sika partnered and worked extensively with the Automotive Center Südwestfalen in the ECoS (Electric vehicle: Crash-optimized Sidefloor structures) project.
The target of the project was the virtual development of innovative sill reinforcement concepts for underfloor battery protection in crash cases.
Placement of EV batteries in the underbody fundamentally changes the requirements for crash structures. There is a basic conflict between optimizing the size of the battery for range and ensuring there is sufficient crumple zone protection.
The battery array and enclosure also increase the total weight of the vehicle thereby changing the center of
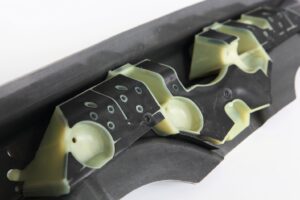
gravity.
Simulation models were used to analyze the changed load paths and deformation behavior compared to internal combustion engine-driven cars and to develop different solution concepts in principle.
Analysis of a broad range of vehicles brought to light changes in requirements, especially in comparison to combustion vehicles, crash physics, and deformation behavior.
OEM responses to these challenges were then analyzed, revealing significant differences in the vehicle architecture and the load path design, which consist of structures in the underbody and sill.
The most common approach was found to be the use of a high-strength sill with internal aluminum extrusion profiles. This design leads to various challenges, such as profile connection, the compensation of thermal expansion and the avoidance of contact corrosion.
SikaReinforcer is able to successfully overcome the main challenges.
Advantages include lower weight, simplified body assembly and better absorption of thermal dilatation differences between materials – leading to cost savings compared to legacy technologies.
The ECoS study can be found at: https://acs-innovations.de/leistungen/verbundprojekte/ecos2021
AI: Where is the development focus for SikaReinforcer?
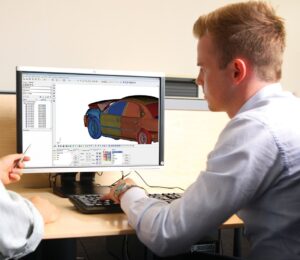
Souvay: The current focus is on sustainability, including lower activation temperatures for our products: use less energy to produce and assemble the parts in the car body (e.g., Low bake E-coat ovens), source raw materials with zero emissions, and work on the circular design of the components.
AI: What differentiates Sika solutions from others in the market?
Souvay: Sika has a global footprint in development and production to serve all regions of the world with industry leading solutions.
R&D and CAE engineers are specifically important for this technology.
Sika has proven expertise in material development, and we are able to adapt quickly to any evolution in specification, such as sustainability, low bake or no bake requirements.
Additionally, we have a long history with SikaReinforcer products and the applications of structural inserts in general.
AI: What can we expect in the Innovation pipeline for OEMs?
Souvay: In order to provide an alternative to SikaReinforcer parts with structural foam, Sika has developed a unique solution using a pumpable structural adhesive instead of epoxy structural foam to further enhance the crash performance of steel structures.
This unique HSB (High Strength Bonding) technology, which uses SikaPower structural adhesives instead of structural foams, is also able to improve the performance of press hardened steel components.
Our unique SikaPower SmartFlow technology allows the structural adhesive to be injected at the end of the body-in-white assembly process in sections which have been fitted with plastic parts. This futuristic technology enables Sika to consistently provide solutions in the car body industry moving forward, involving an increased utilization of extruded aluminum and castings.
More Stories
Professional vs. DIY Tinting: What You Should Know
New updated edition of “PXIMate” reference guide for T&M engineers available from Pickering Interfaces
5 Mistakes That Can Ruin Your Car Accident Claim